【DX事例紹介】予防保全とは?予防保全からみる製造業のDX事例
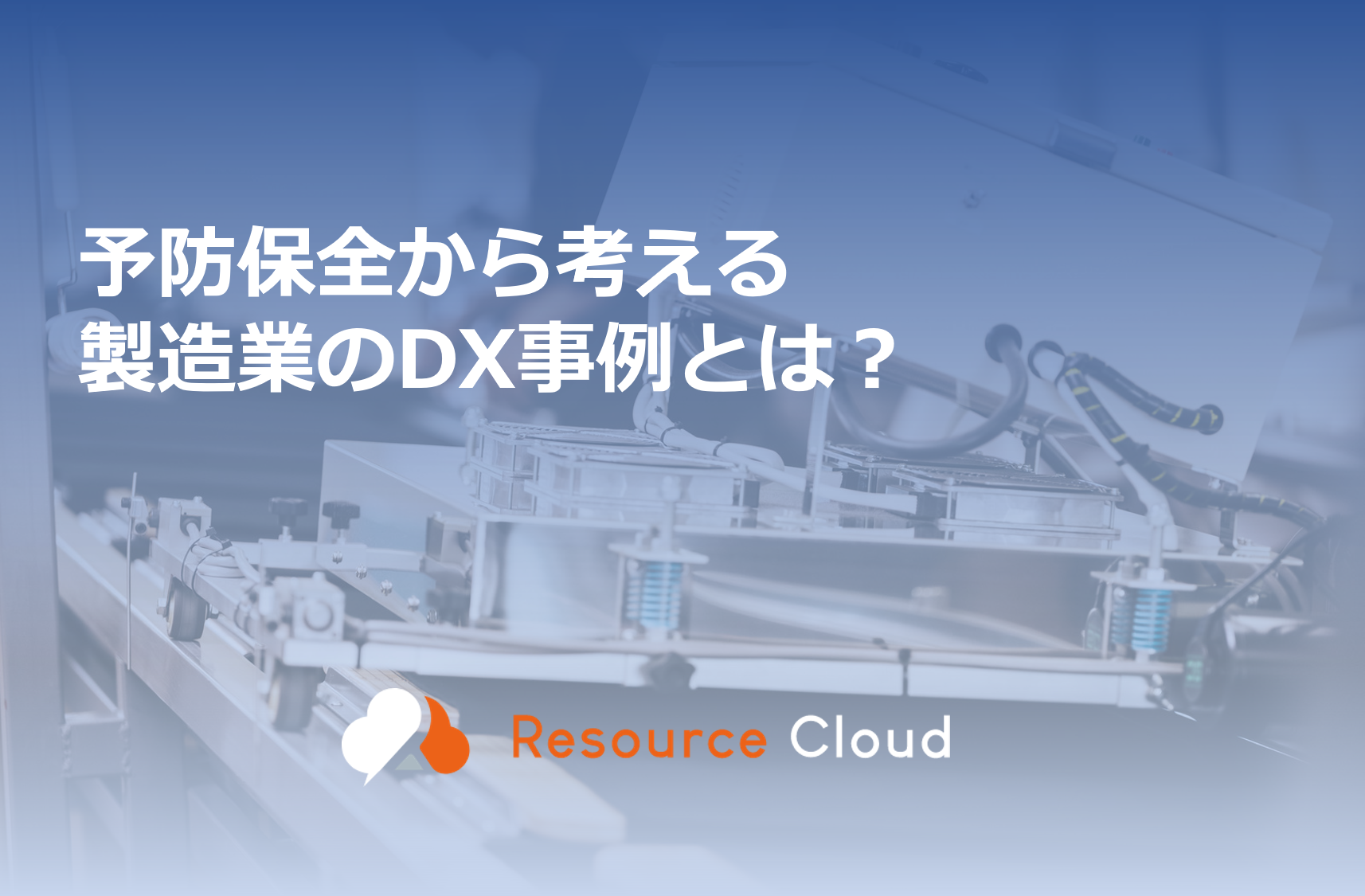
製造業の現場において、機器のメンテナンスは重要な作業でありながらタイミングが非常に難しい作業です。
何故なら、メンテナンスは製造ラインの停止を伴うため、言ってしまえば機会損失を生むこととほぼ同意です。それに加え、メンテナンスの方法によっては復旧までのリードタイムが大幅に伸びてしまい、更に生産性を下げるリスクもあります。 だからこそ、製造業の現場においてメンテナンスは常に試行錯誤していかなければならない課題と言えるのです。
では、メンテナンスにおける具体的なデジタルトランスフォーメーション(以下、DX)の事例はどのようなものになるのでしょうか?
メンテナンス手法を大きく分類すると「予防保全」「事後保全」「予知保全」の3つに分けることが出来ますが、今回は古くから行われている「予防保全」をテーマに製造業のDX事例をみていきます。
製造業のDXにおける予防保全とは?予知保全との違いとは?
「予防保全」とは、機械を安定稼働させるための検査や修理、部品の交換などを計画的にメンテナンスしていくことです。「予知保全」も同じように検査や修理、部品の交換などを計画的に行いますが、大きな違いはメンテナンスするタイミングが異なります。
前提として、機械はある程度使用回数(または使用期間)が増えれば何らかの不具合が発生するものです。
だからこそ、予防保全のメンテナンスするタイミングは「設備の製造元や作業従事者の経験から、壊れる可能性がある使用時間、回数などをきっかけ」に行います。これに対し予知保全のメンテナンスするタイミングは「センサーから数値を定期的に読み取りデータ化しておくことで、正常に動作しているようでも何らかの差分が発生したのをきっかけ」に行います。
これだけを聞くと、予防保全よりも予知保全が優れていると思う方も多いでしょう。何故なら、予防保全はまだ使える機械を交換してしまうリスクがあるため、予知保全と比較してコスト的なデメリットが発生し得ること。また、予防保全は経験に基づくことから業務が属人化するリスクもあるため、事業がスケールする上で障害になり得ると言えるからです。
では、予防保全は予知保全の劣化手法になってしまうのでしょうか?その答えは「No」です。予知保全よりも予防保全の方が優れた場面はもちろんあります。
例えば、「交換部品が比較的安価かつ作業コストも安価であるもの」は「メンテナンスコスト < 故障時のリスク」が成立するため、予防保全のコストパフォーマンスが圧倒的に高くなります。他にも、「データが取得できる状態ではない」場面や「閾値を決めることが出来ない」などの場面はそもそも予防保全しかすることが出来ないからです。
だからこそ、製造業の現場では今回のテーマである「予防保全」以外にも、「事後保全」や「予知保全」をバランス良く使い分けることが重要になります。
予防保全から予知保全への切り替えを進めるにはIoT機器の利用が必要
先述した通り、予防保全・予知保全はどちらも重要な手法と言えますが、事業をスケールさせる上では、業務の属人化を防ぎ、コストメリットのある予知保全にシフトしていくことが理想です。
そのために、まず必要なことはIoT(Internet of Things:モノのインターネット)機器を利用しデータ収集することです。故障予測の精度を上げるために、これまではセンサーやメータの状態を目視確認していましたが、近年ではIoT機器により自動化することで製造業の現場に多くの変化が生まれています。
更に、最近ではこの蓄積されたデータを活用してAIによる機械学習を行う事でより精度の高い閾値を設定する方法も出てきました。各種センサーやPLCからのデータを蓄積した膨大な学習データから人間が様々な統計手法や計算式で計算するより遙かに高精度な閾値を算出できるため、製品の公差の範囲内で異常を検知することも可能になっています。
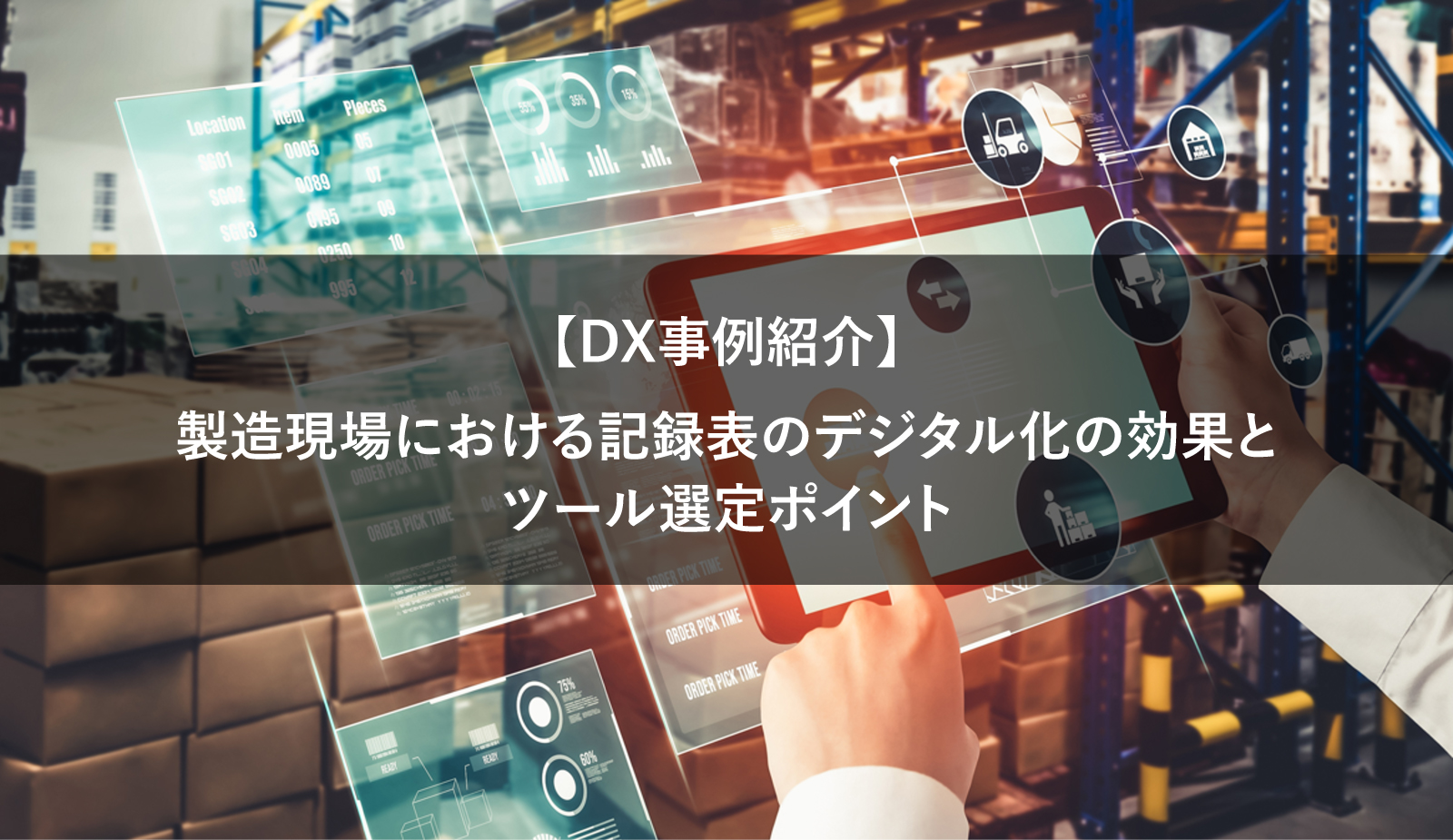
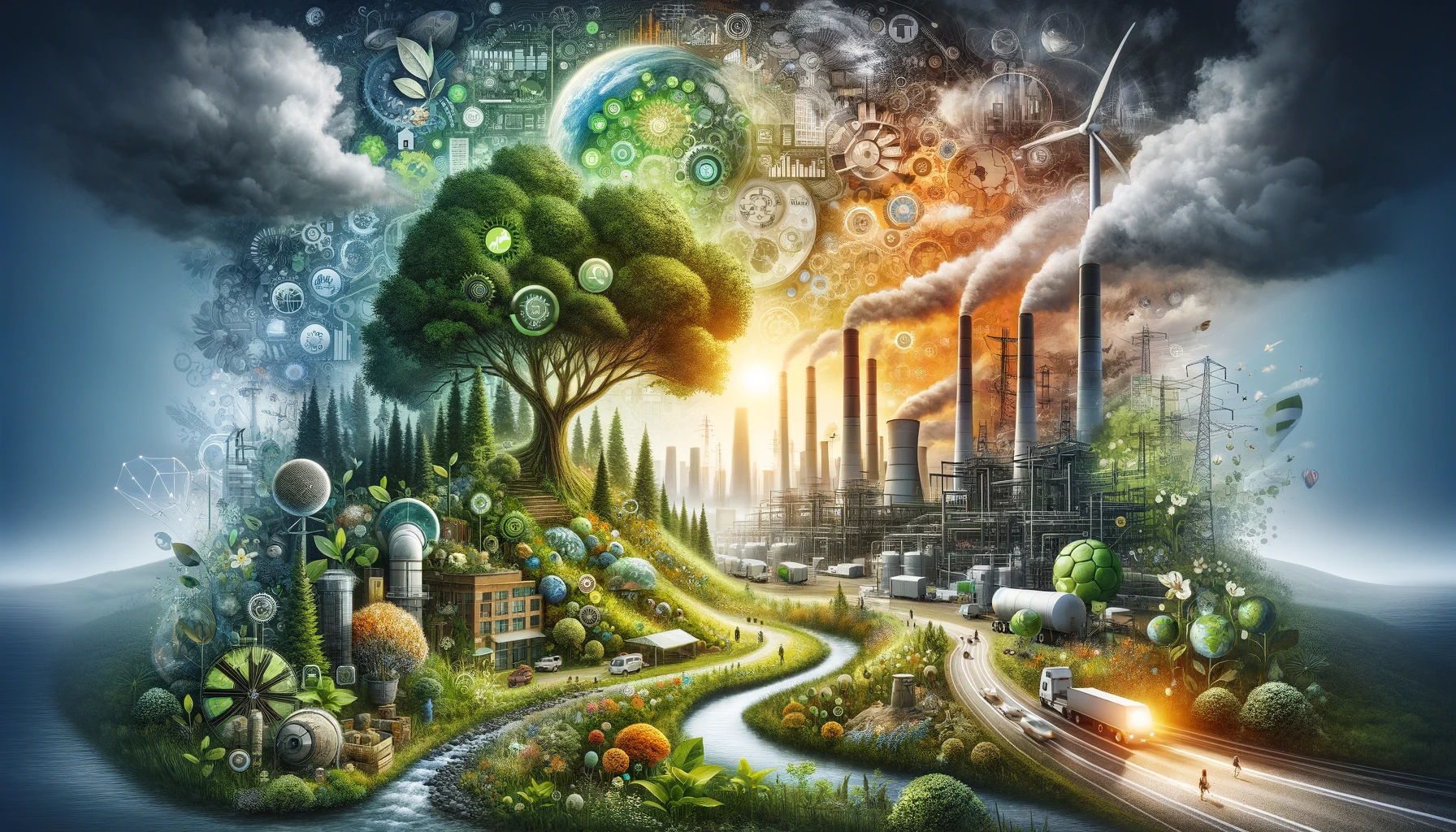
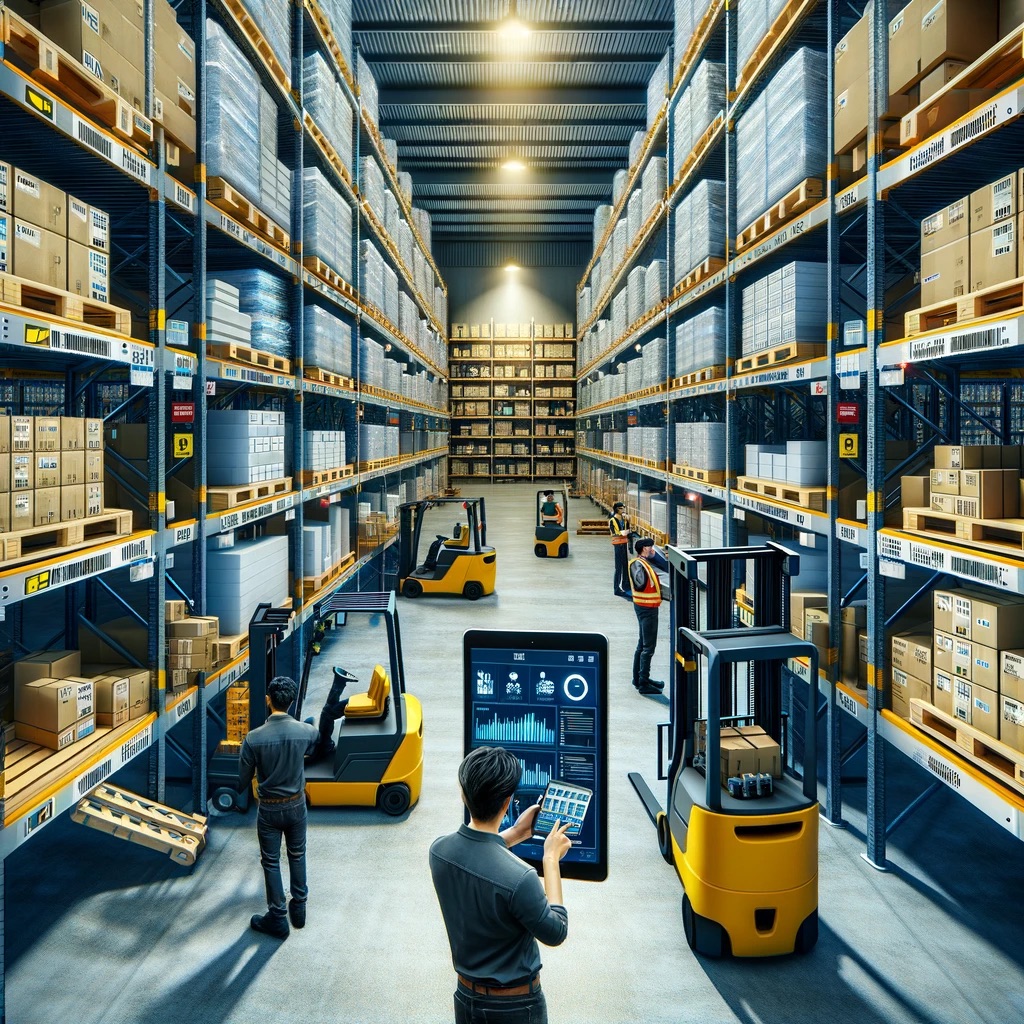
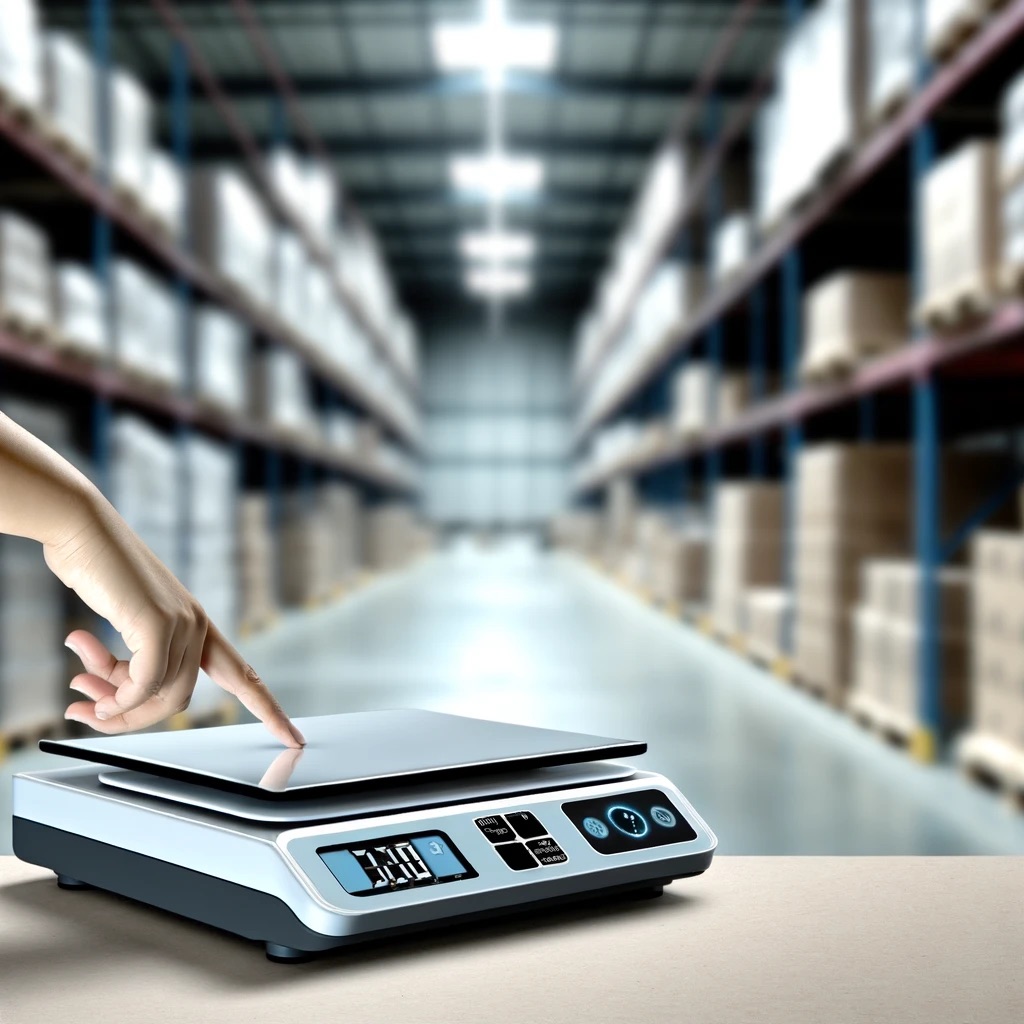
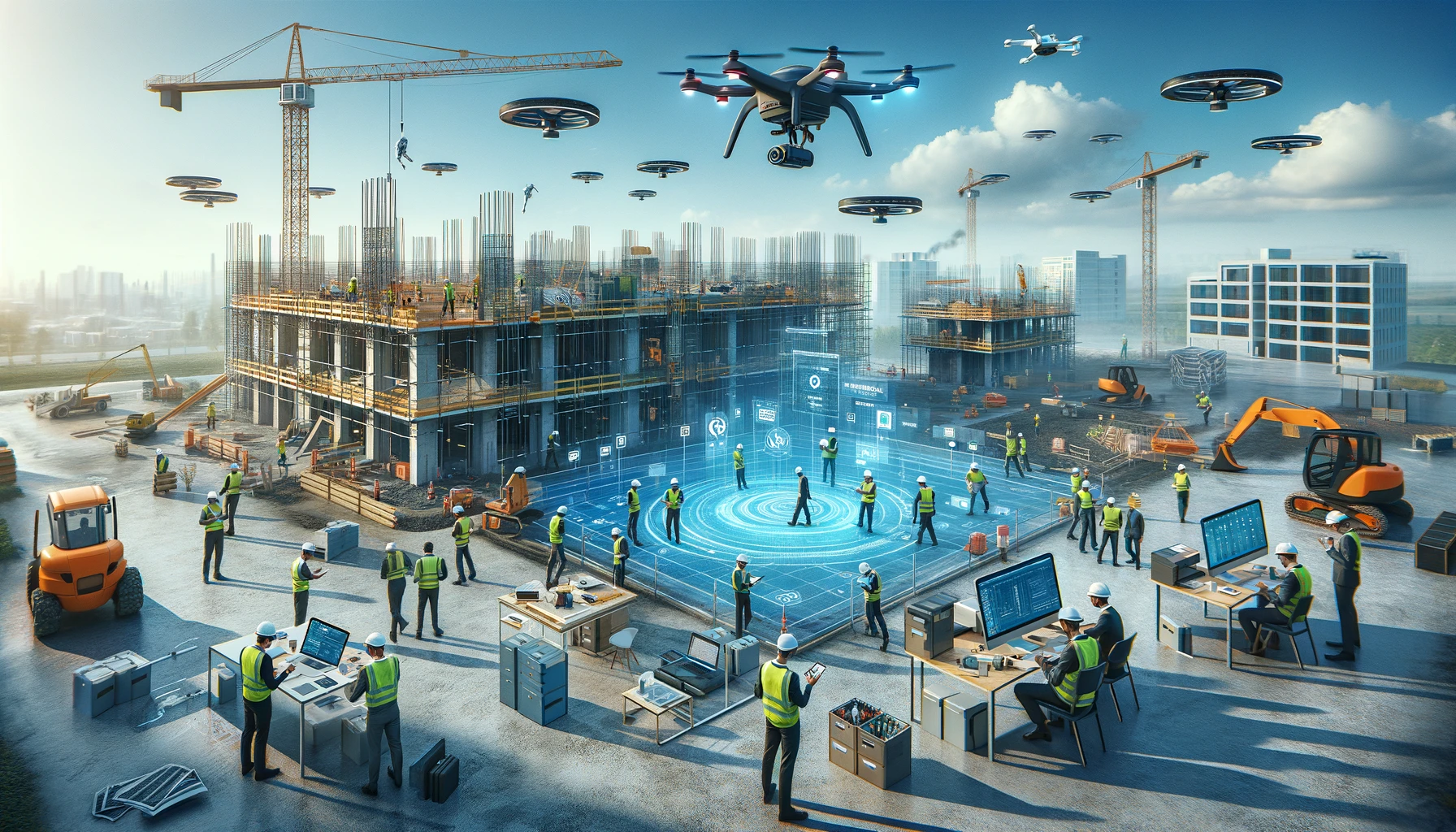
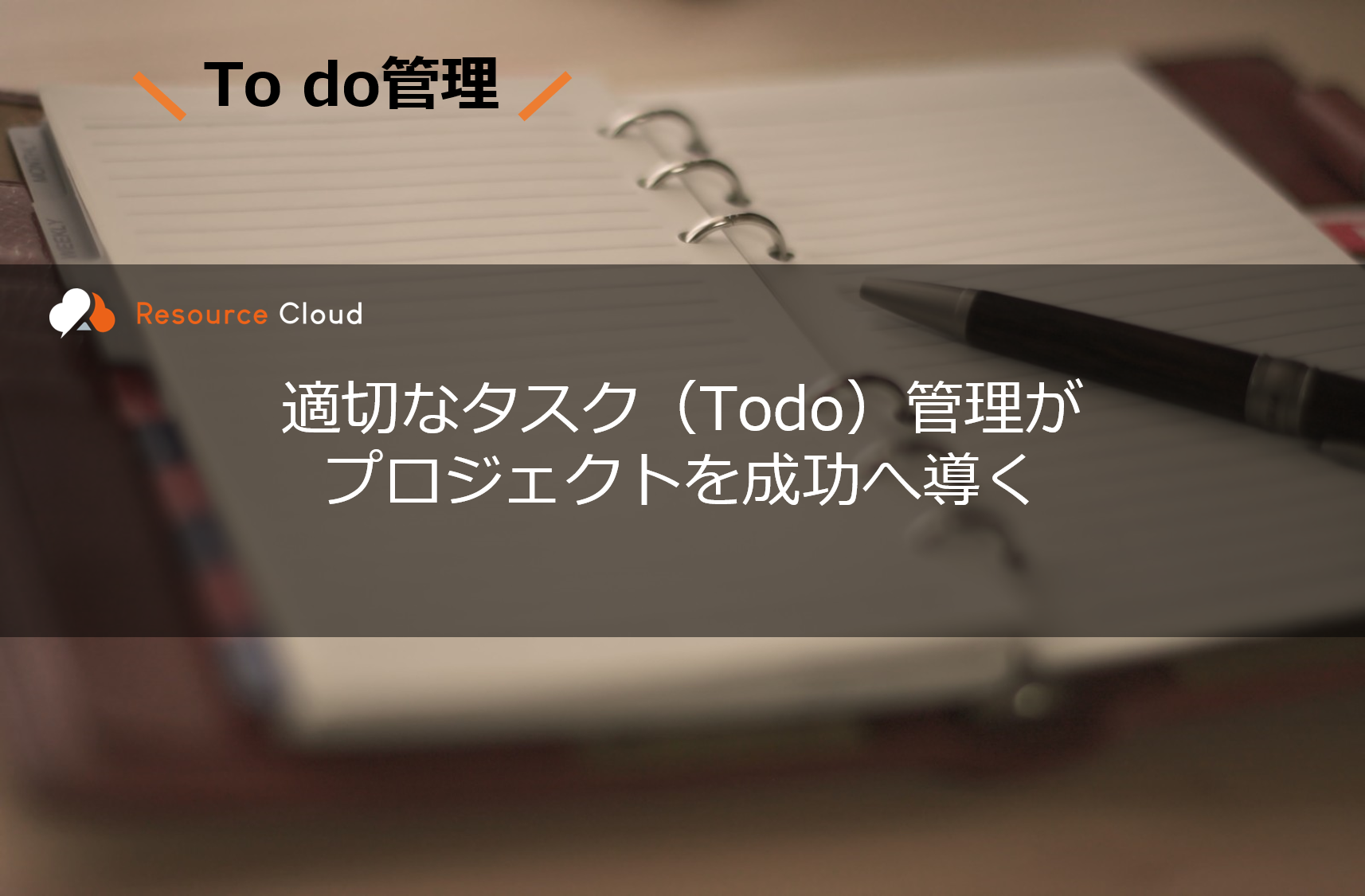

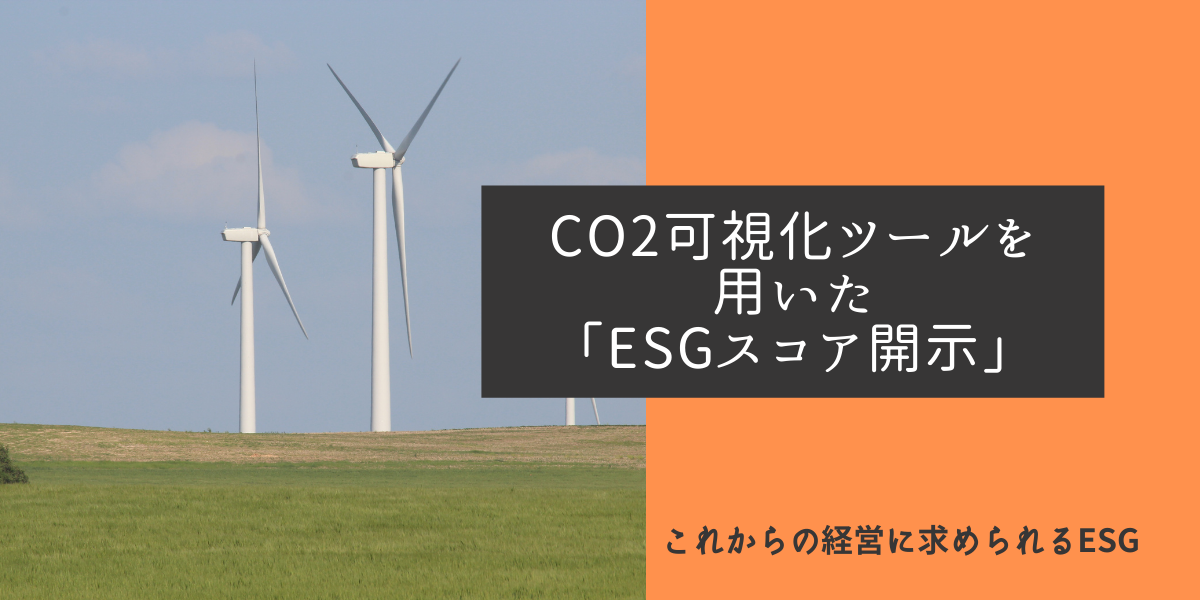
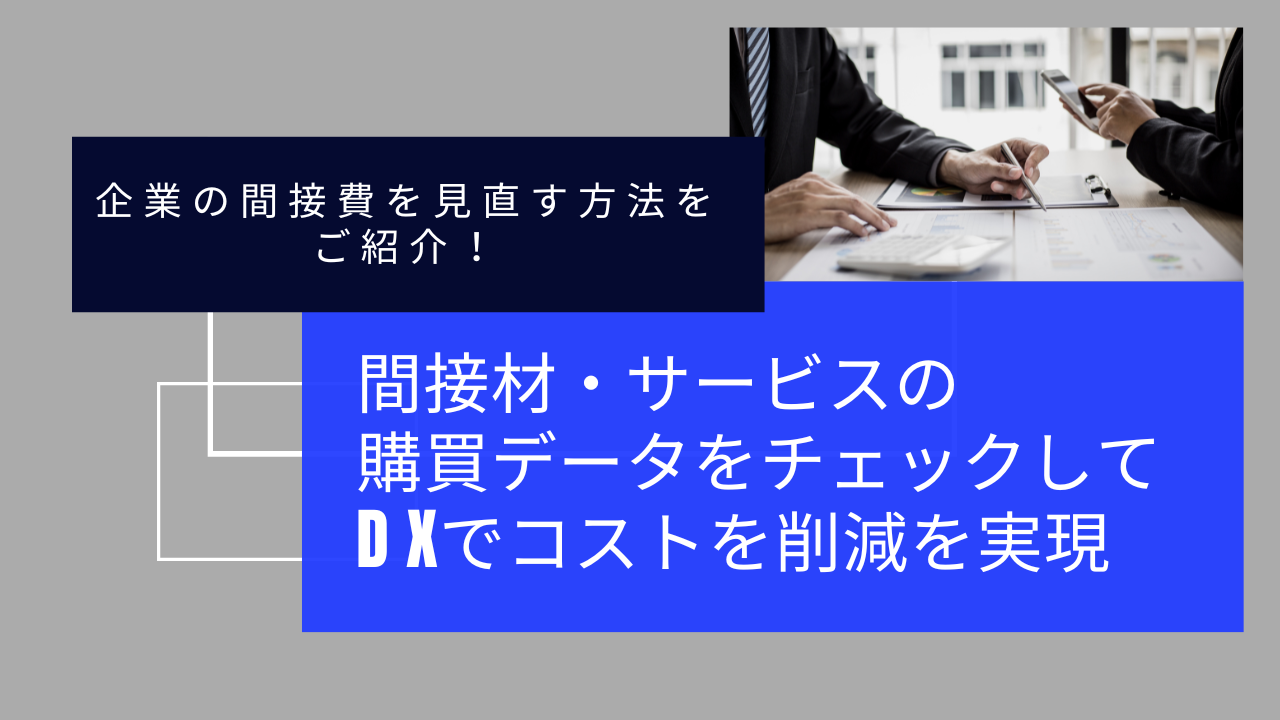
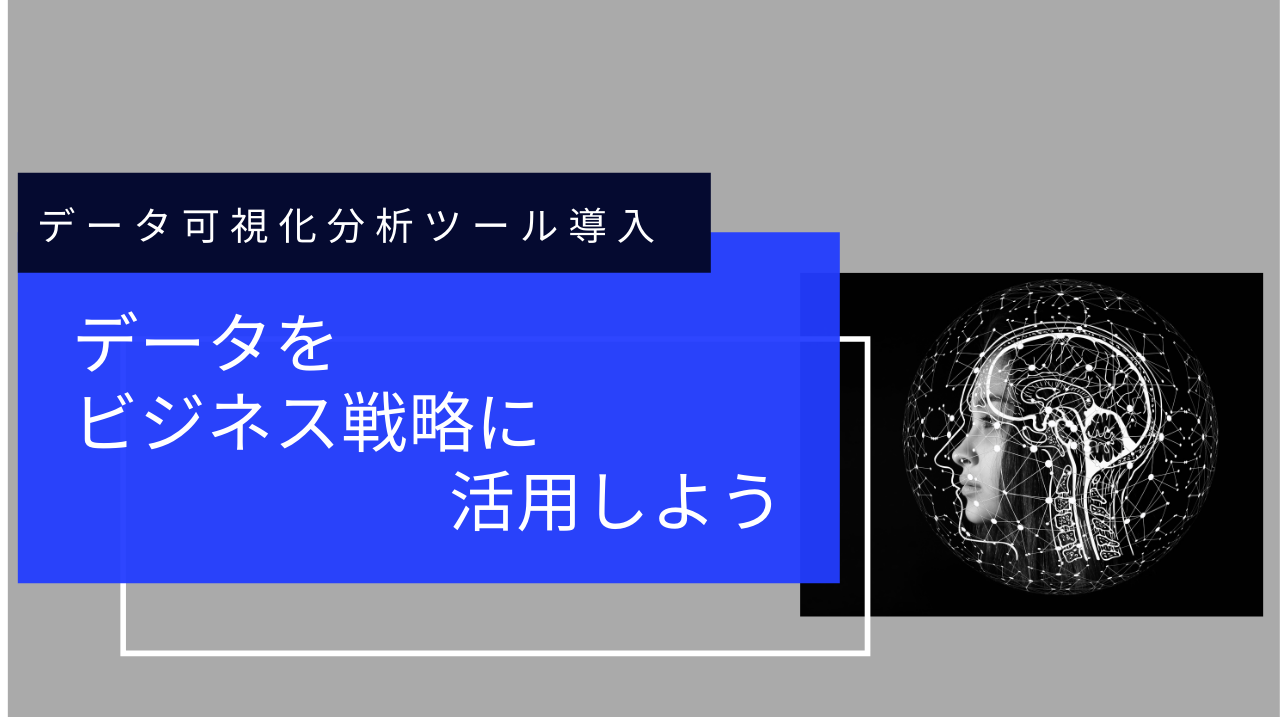
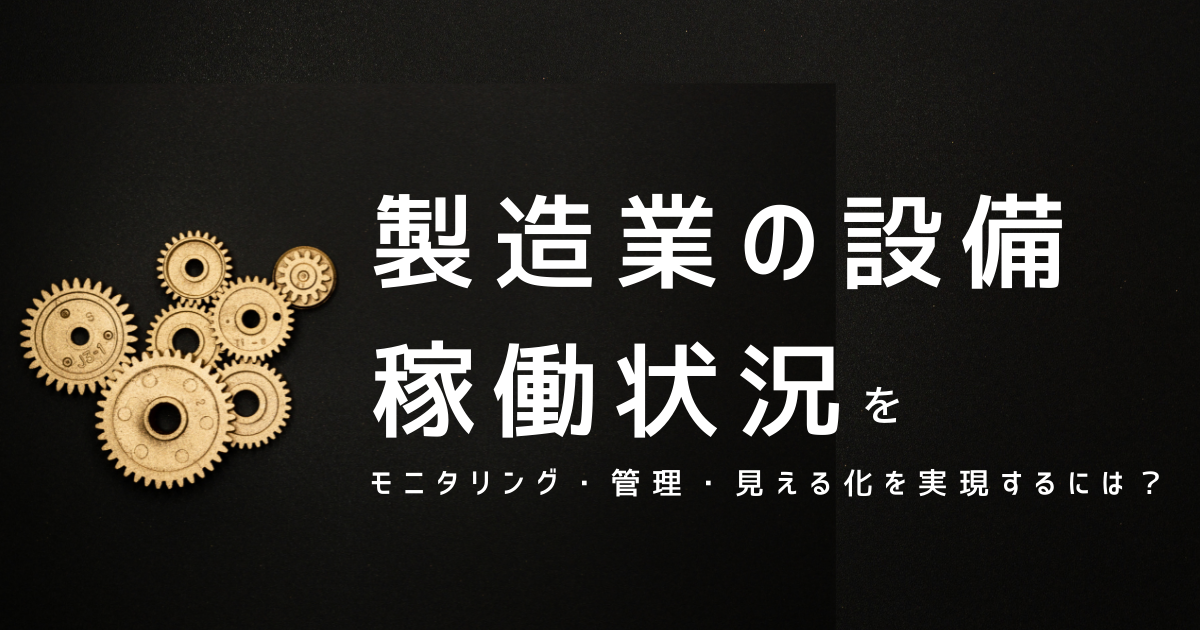
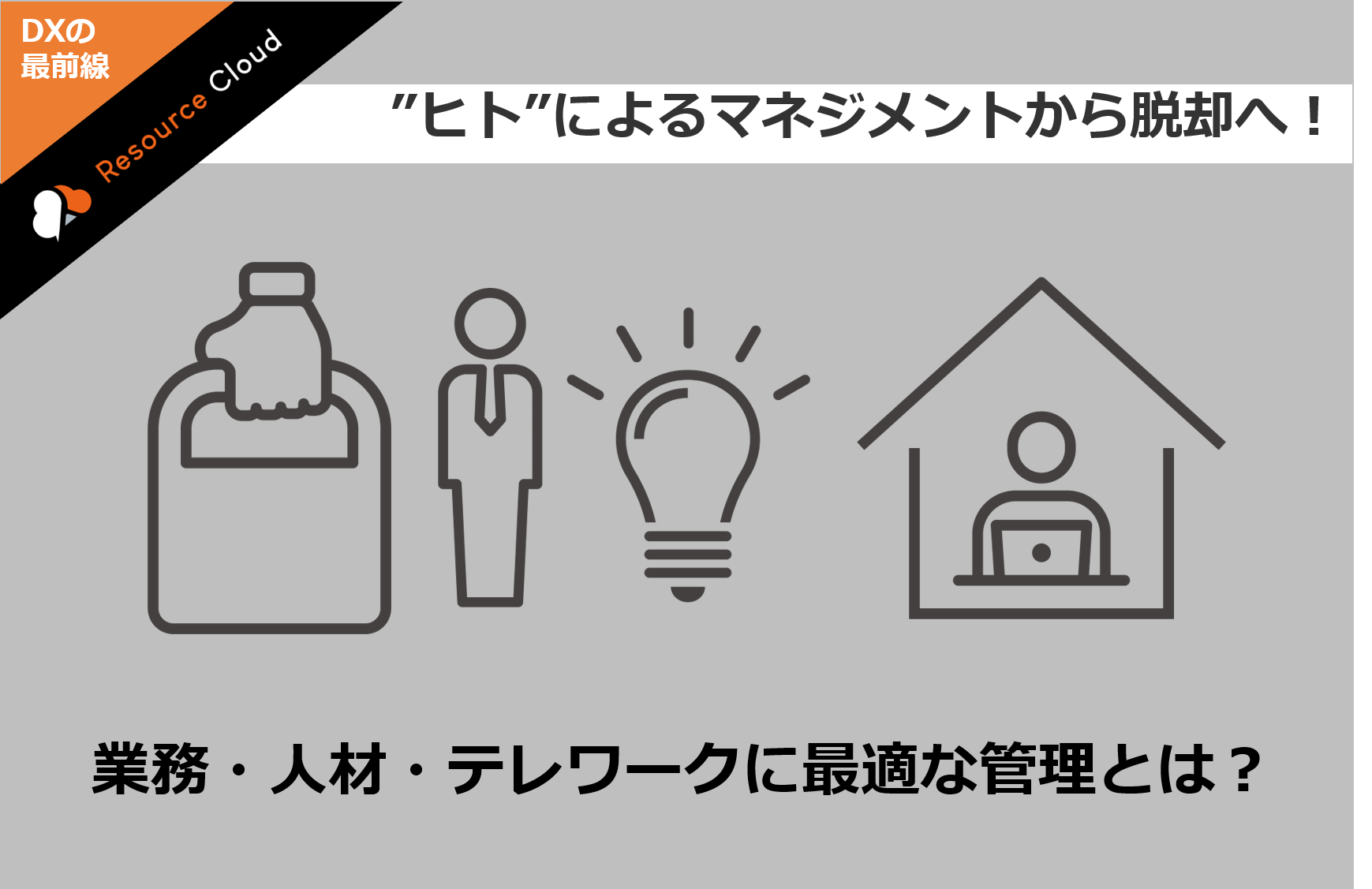
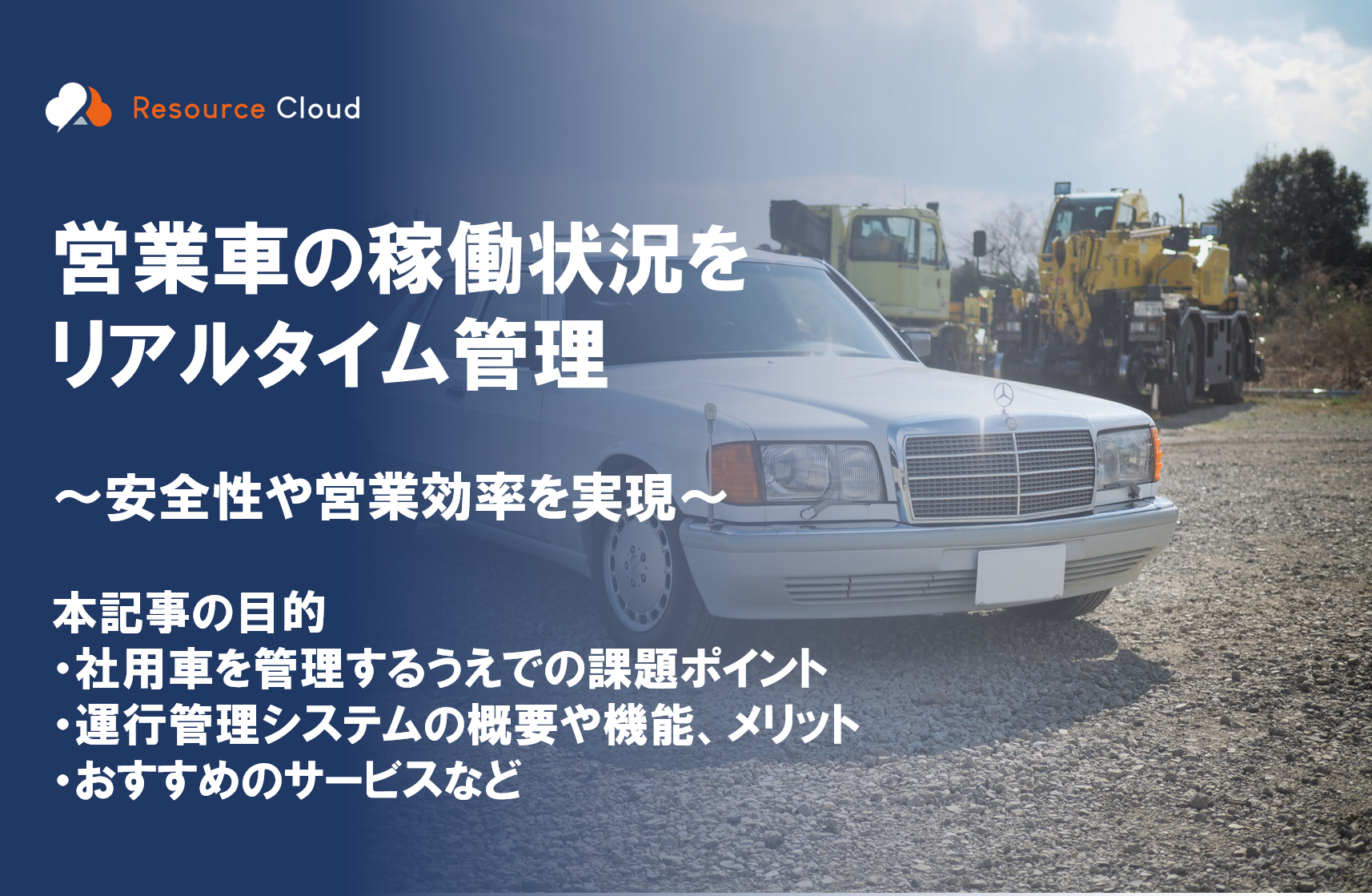
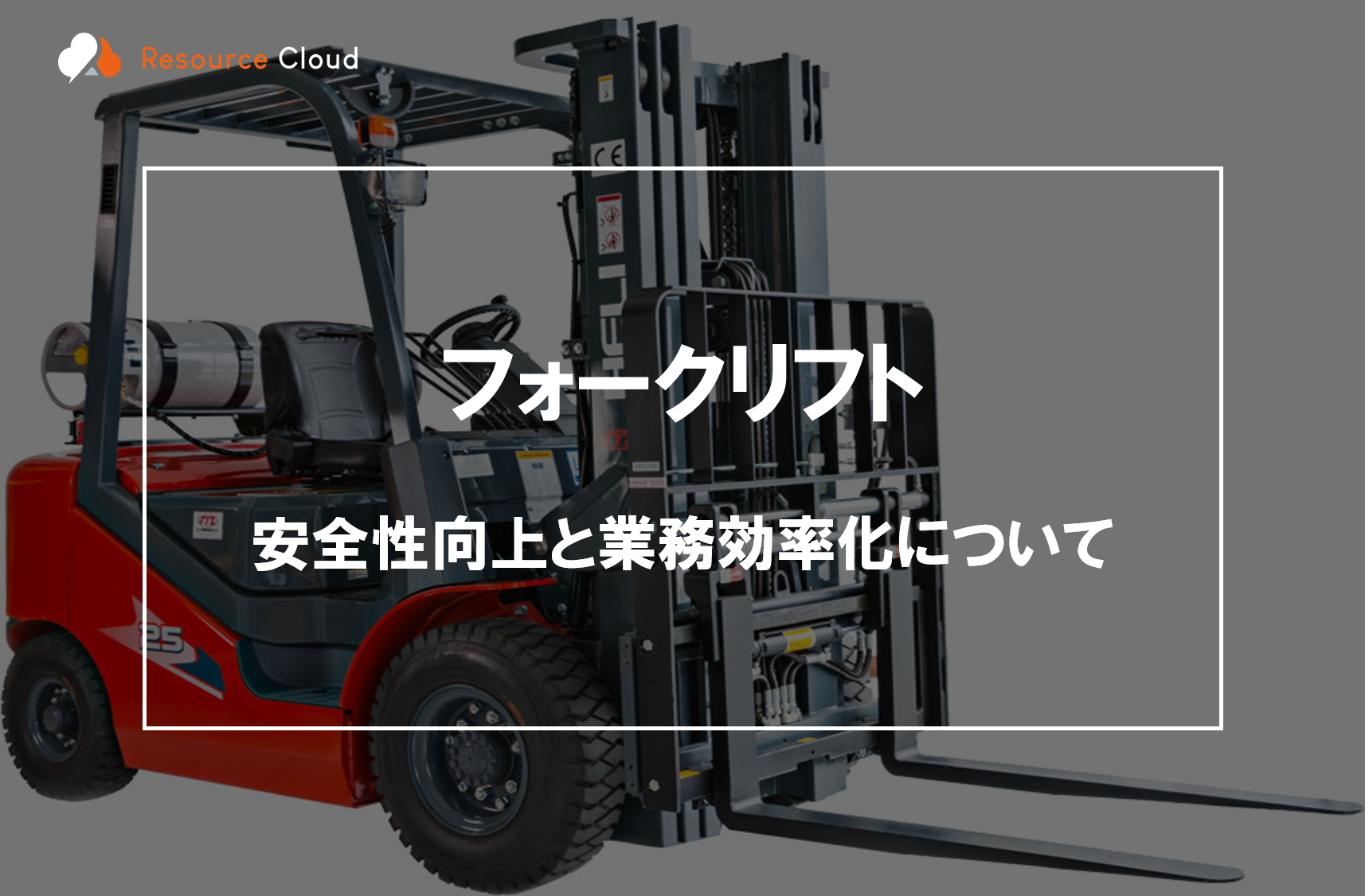
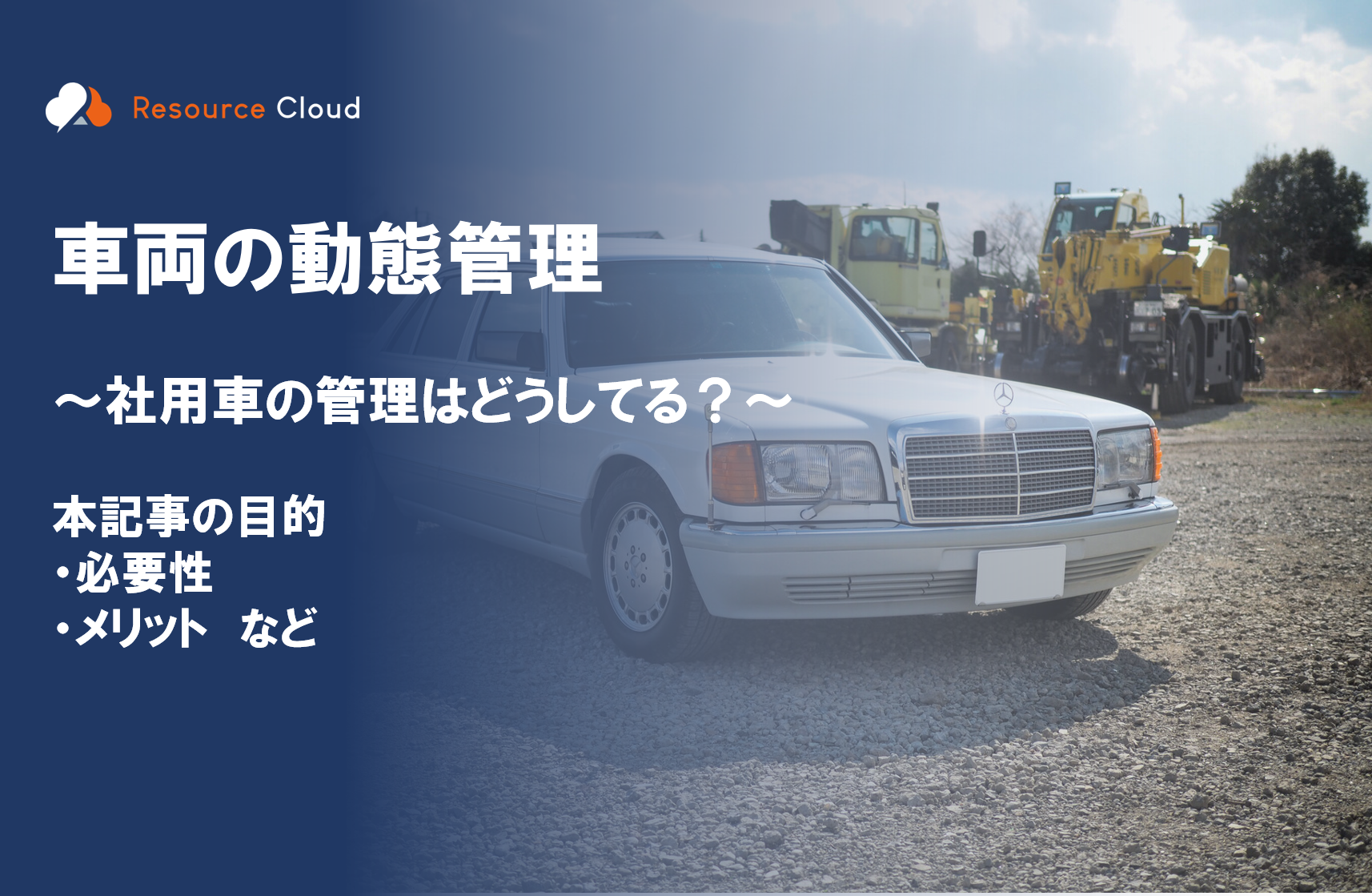
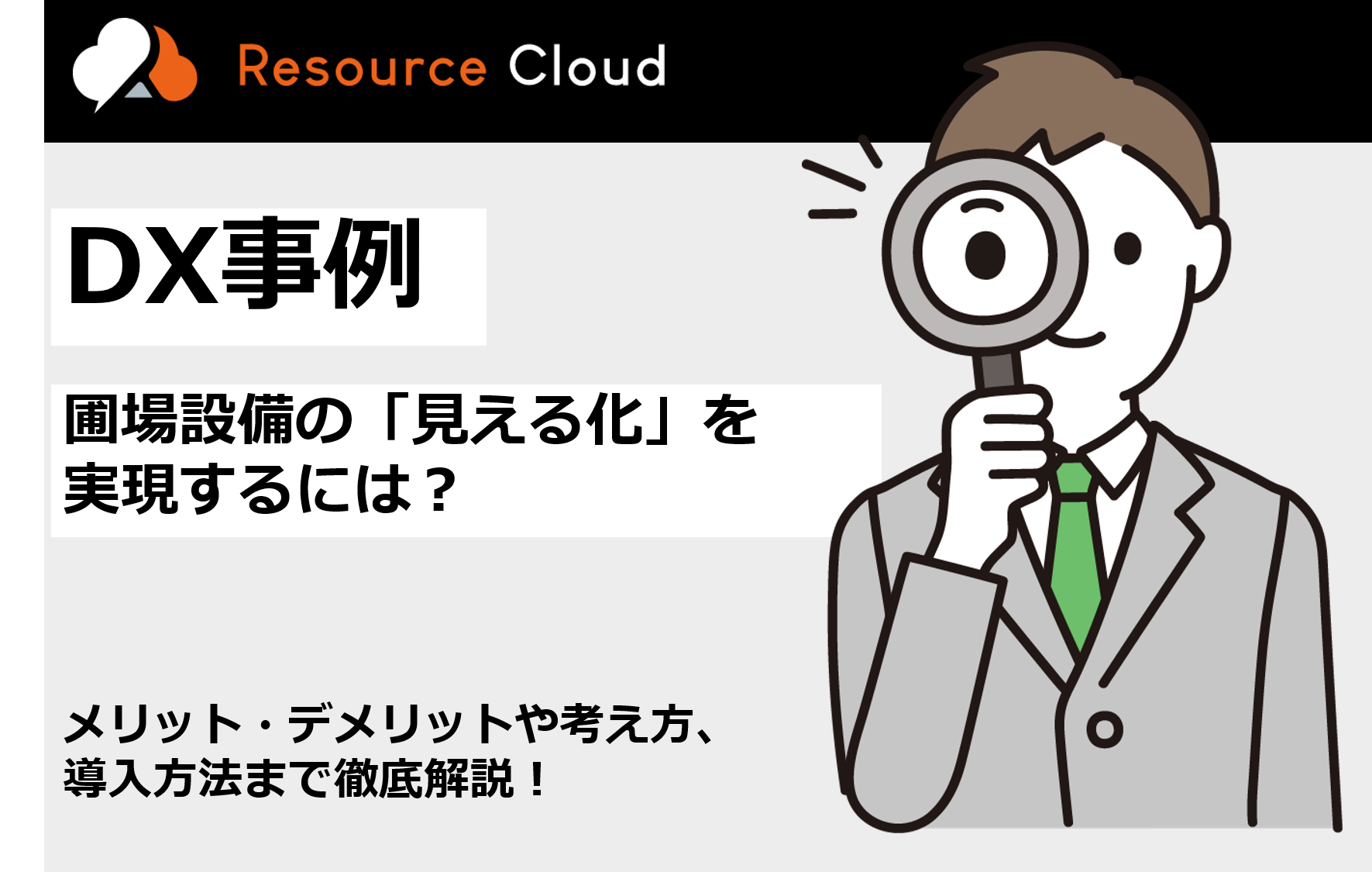
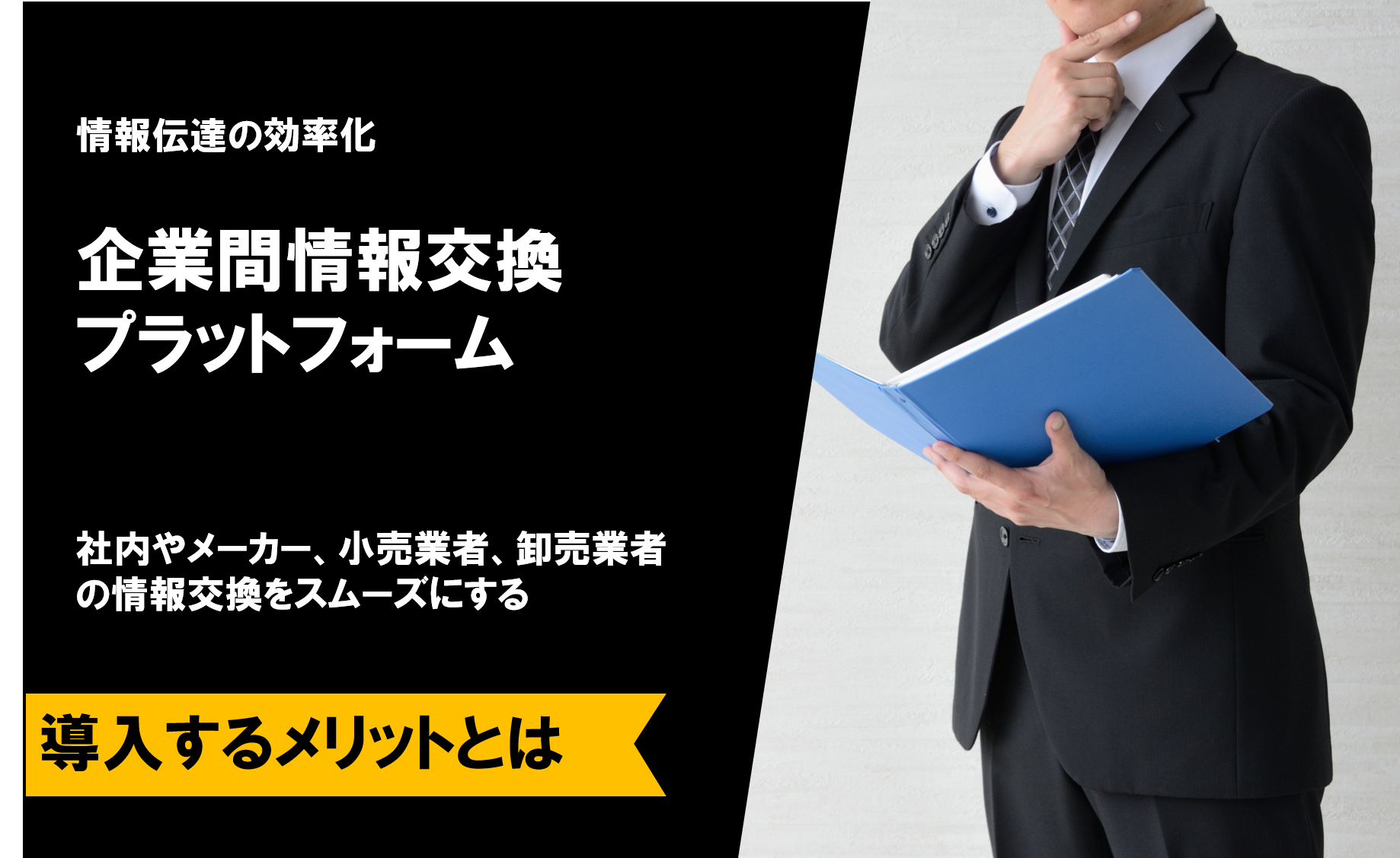
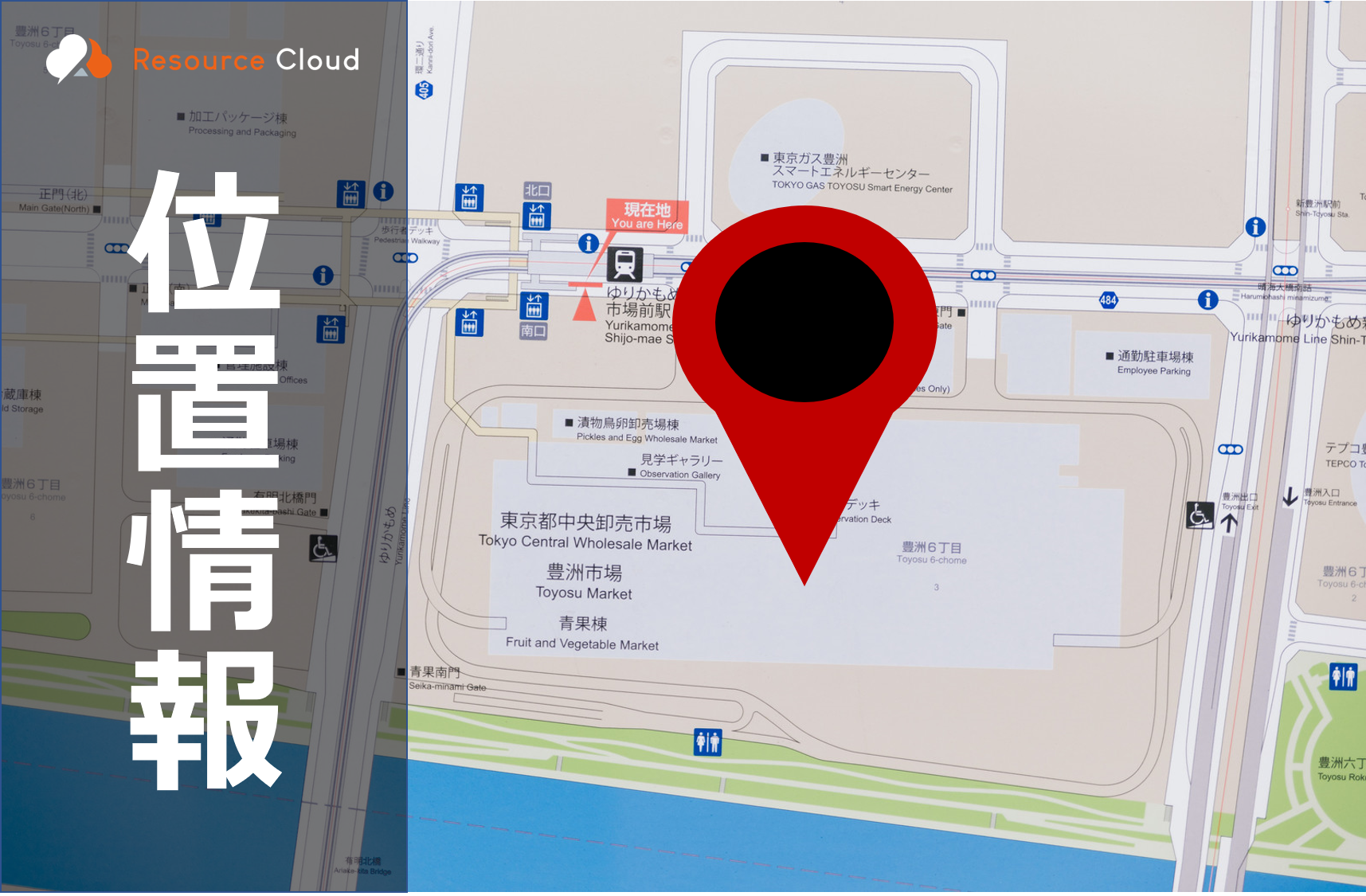
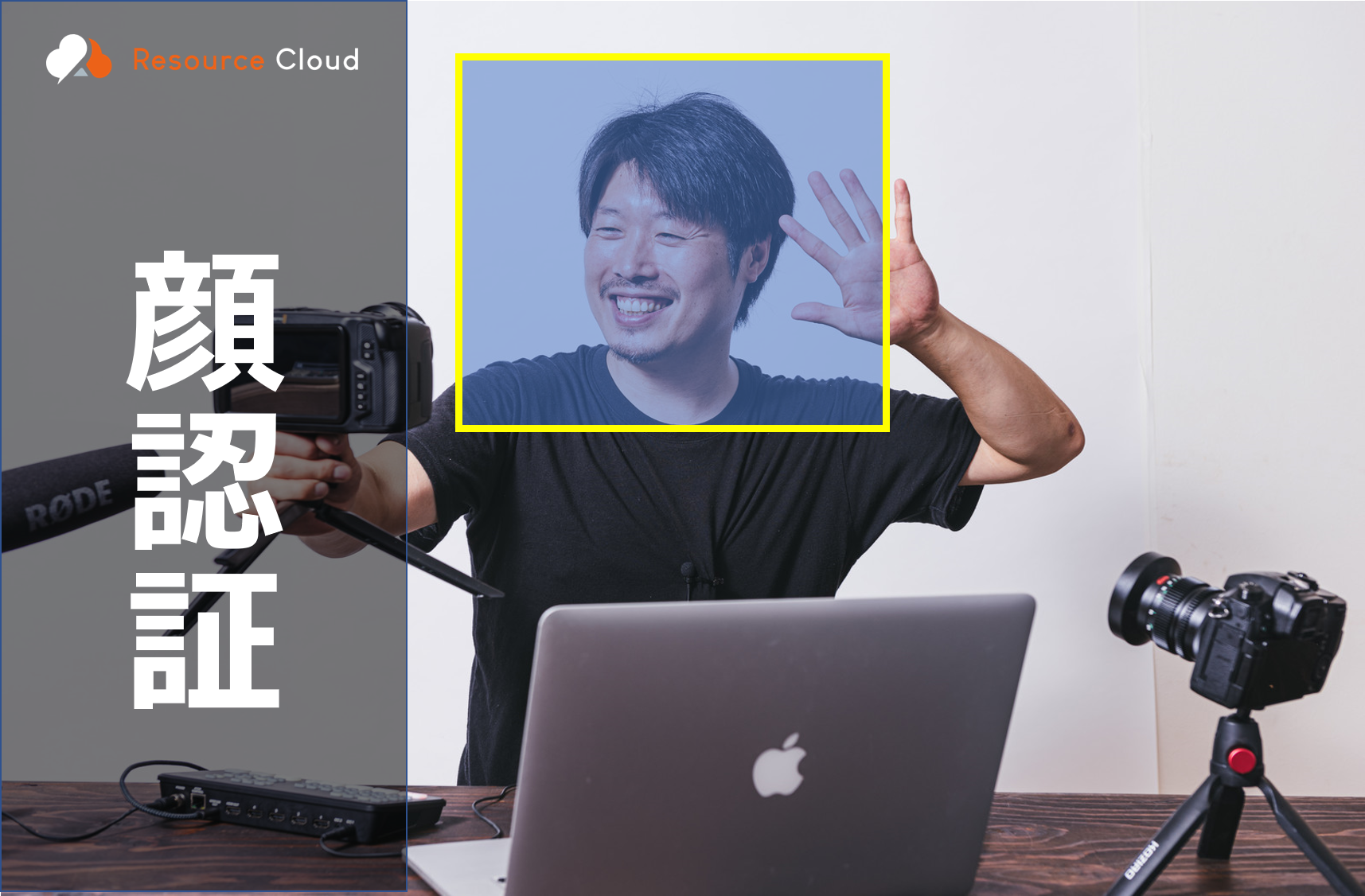
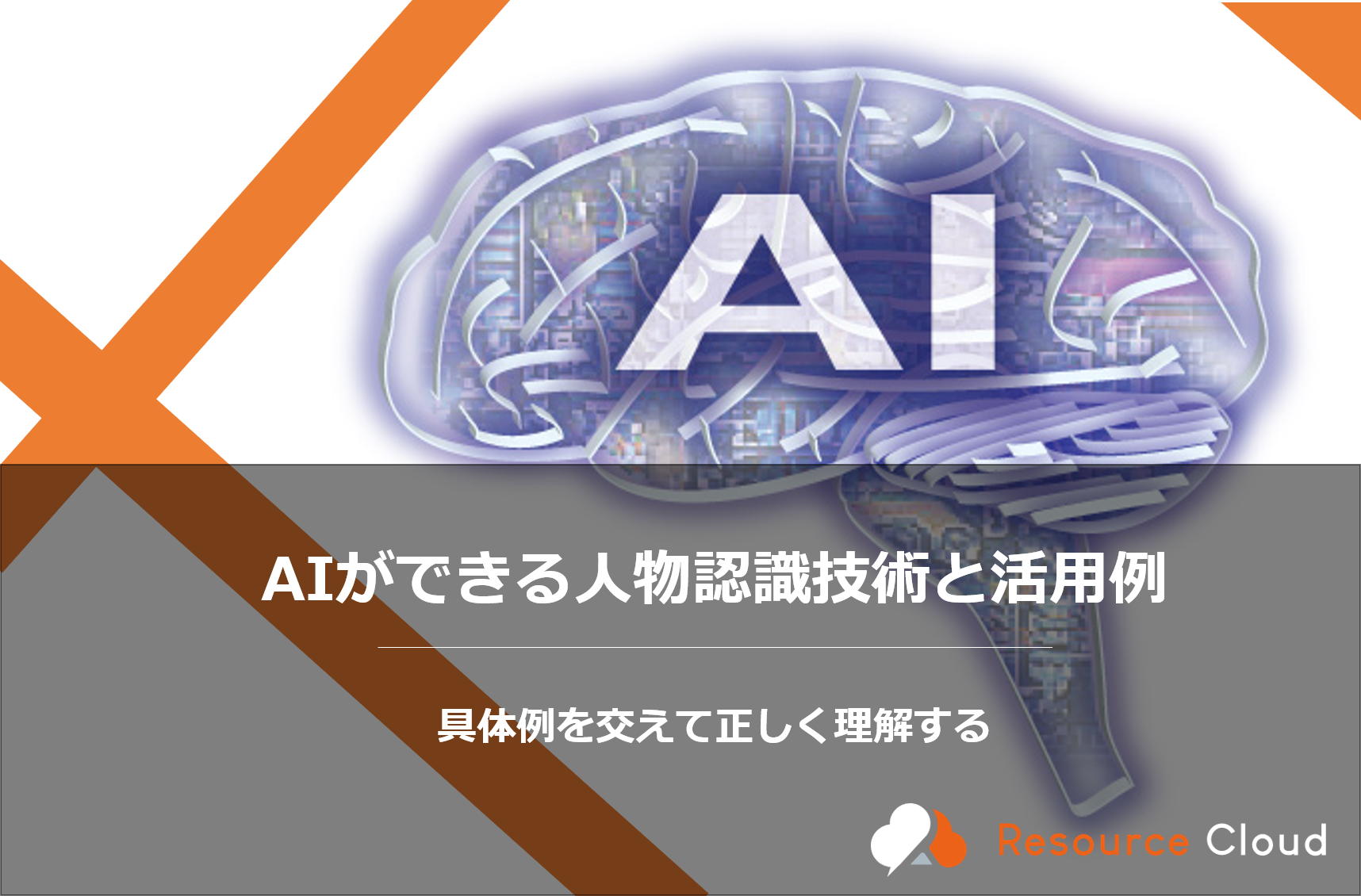
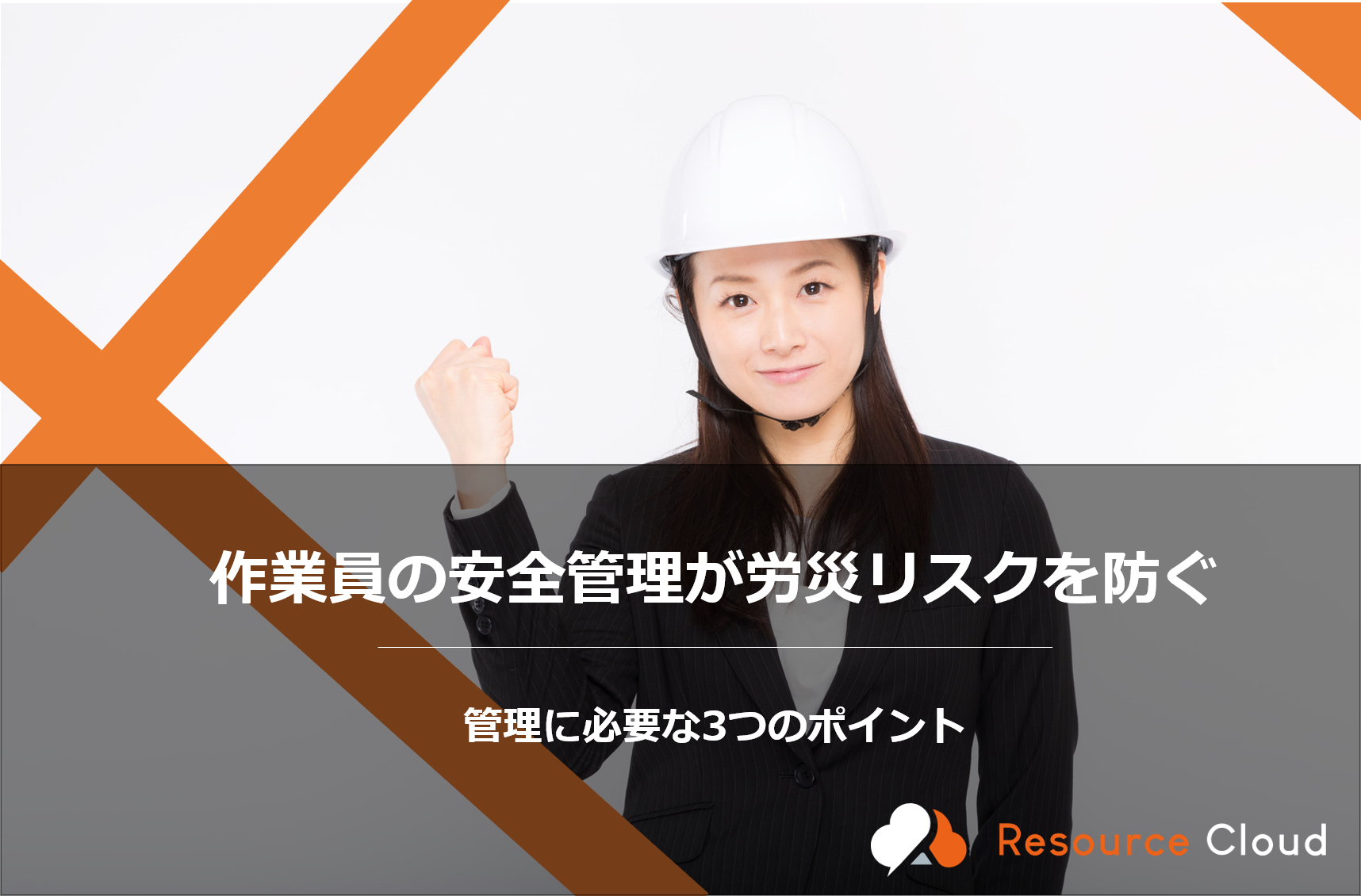
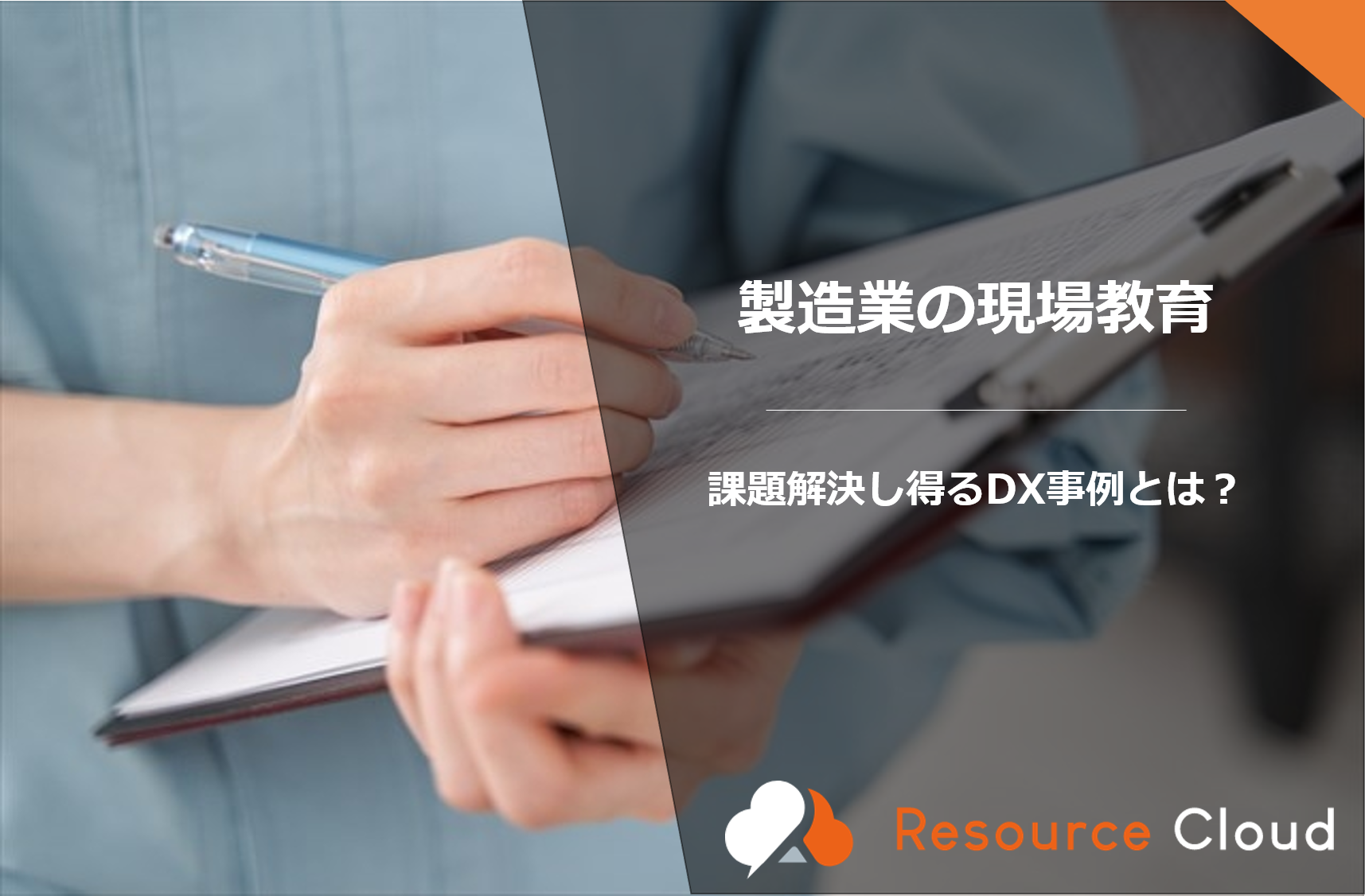
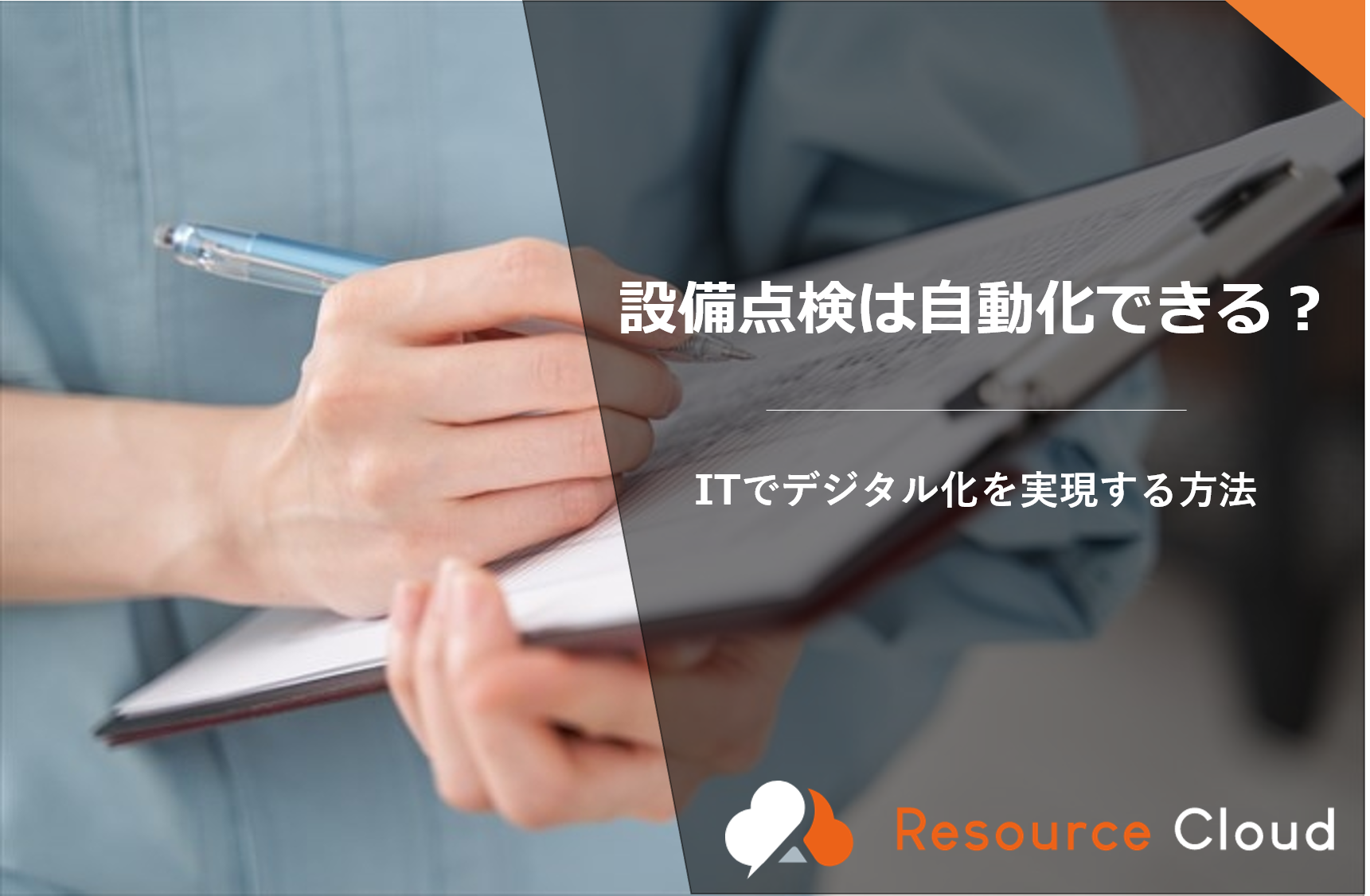
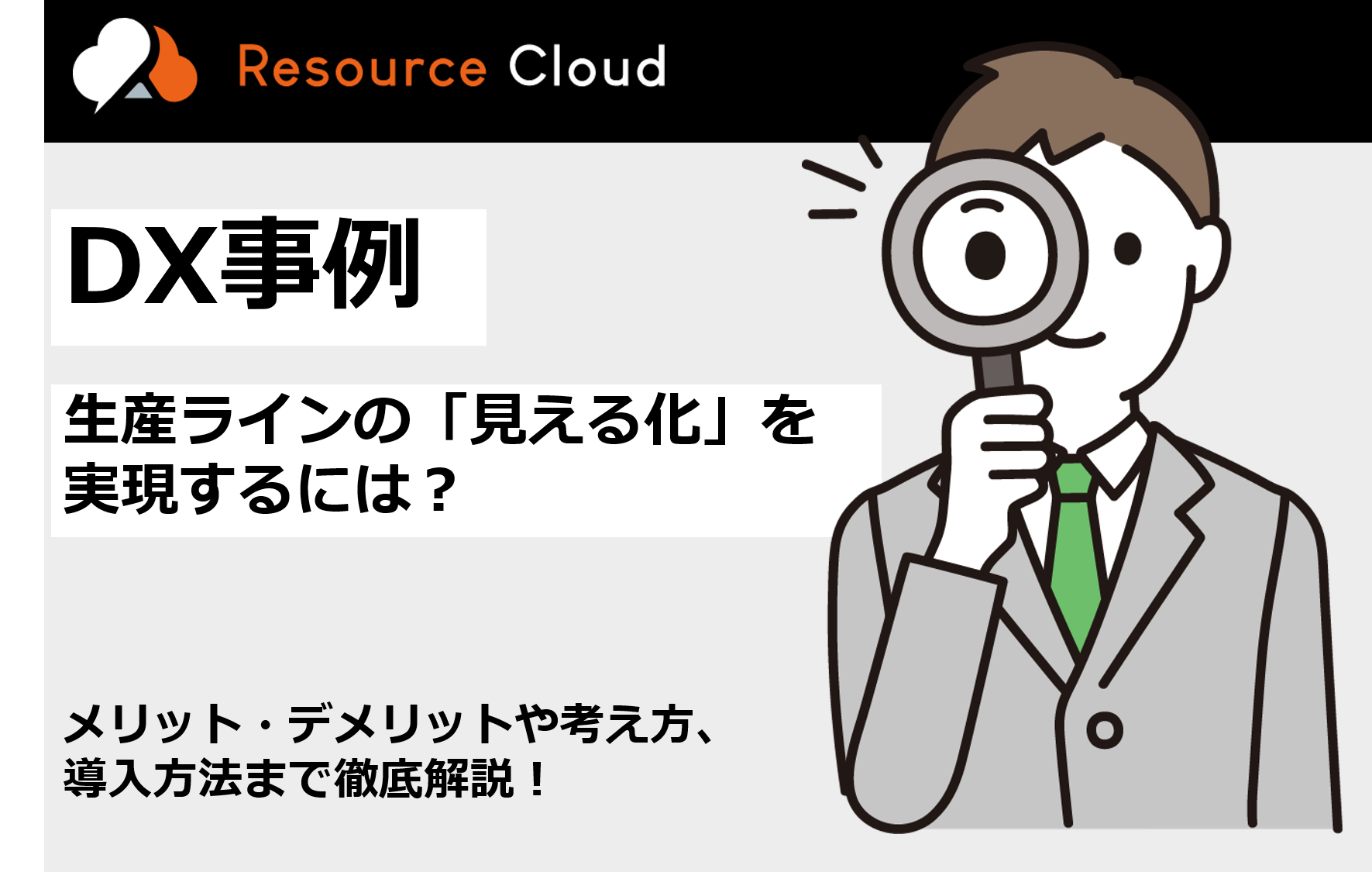
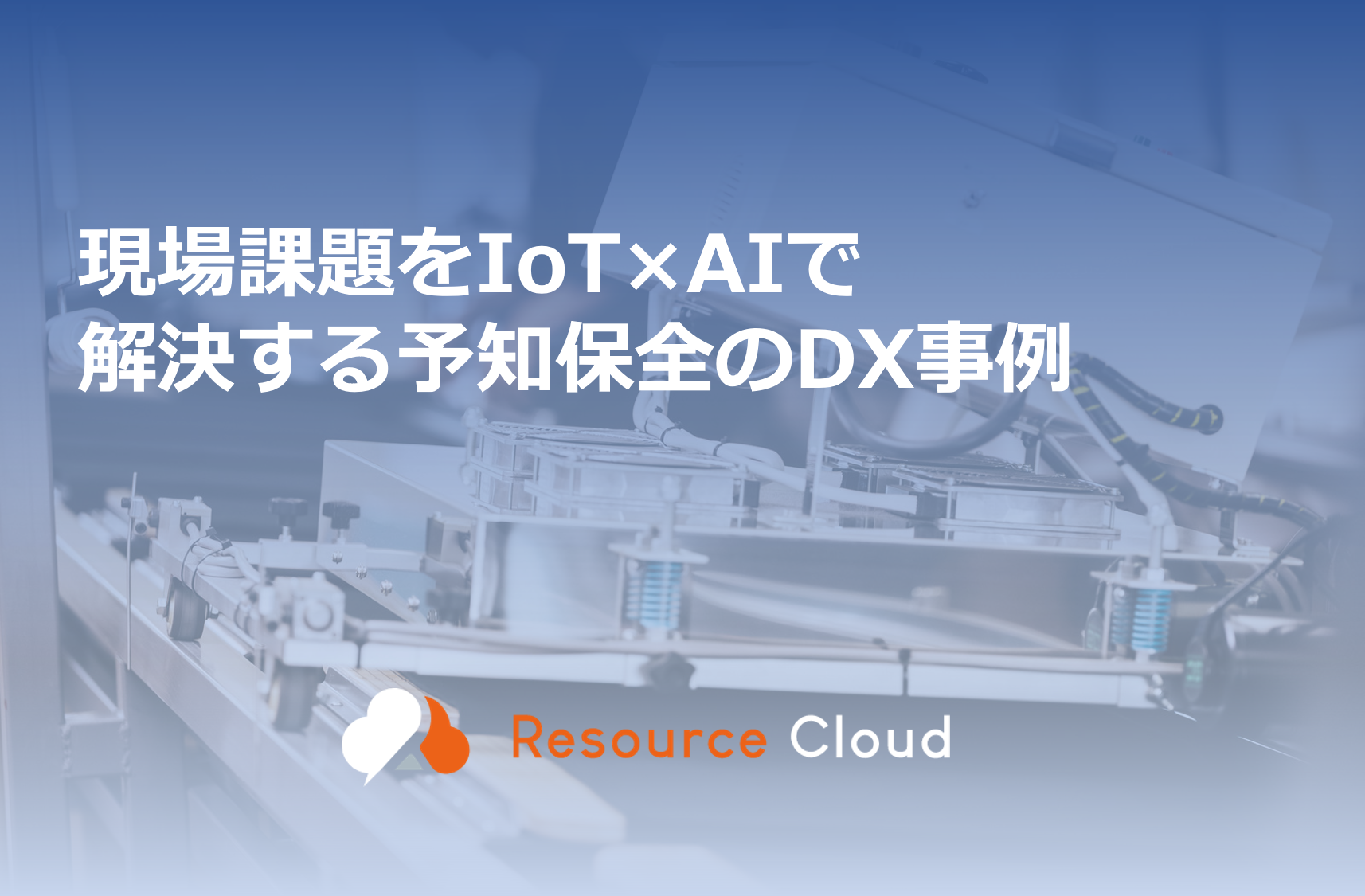
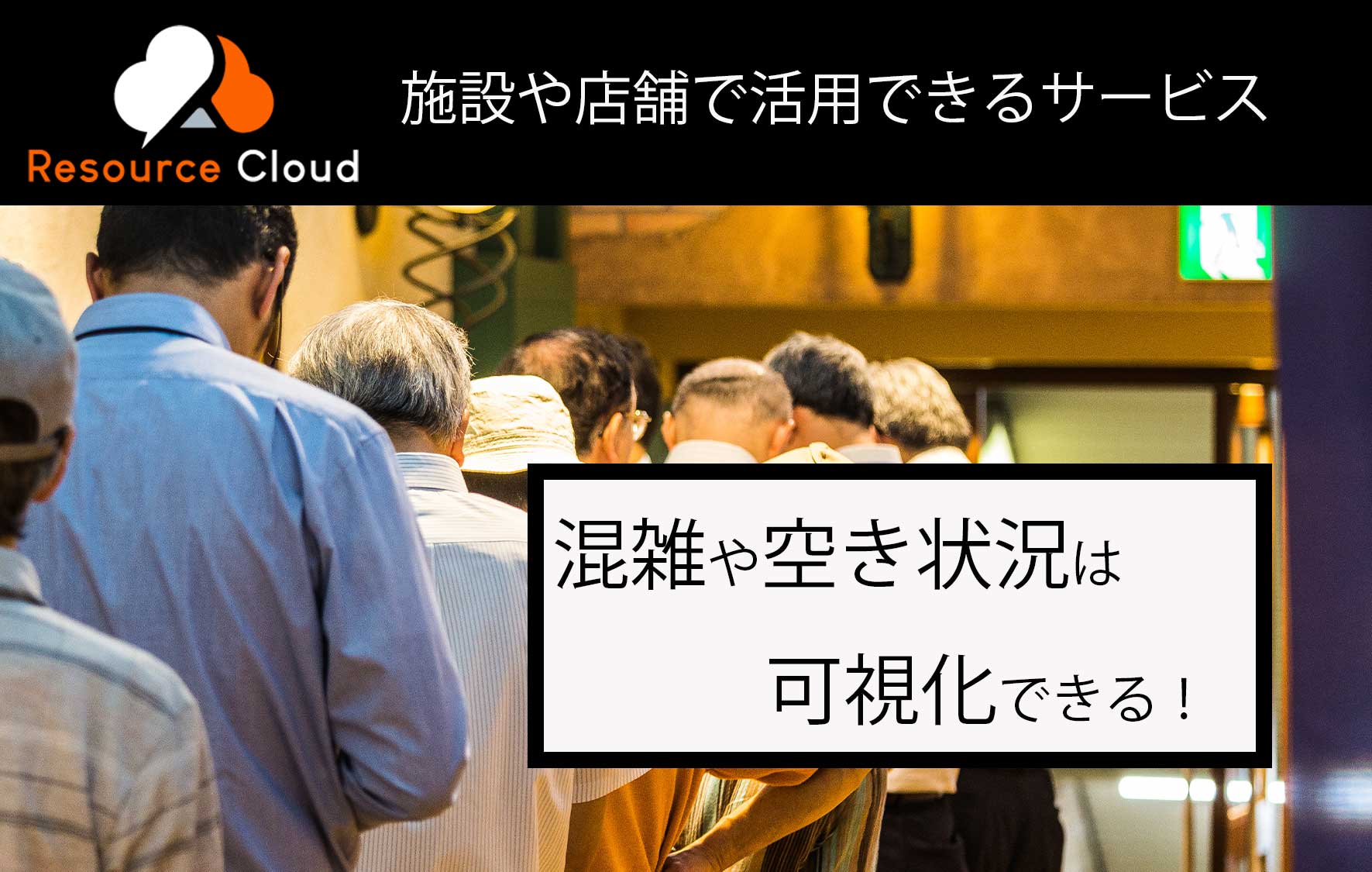
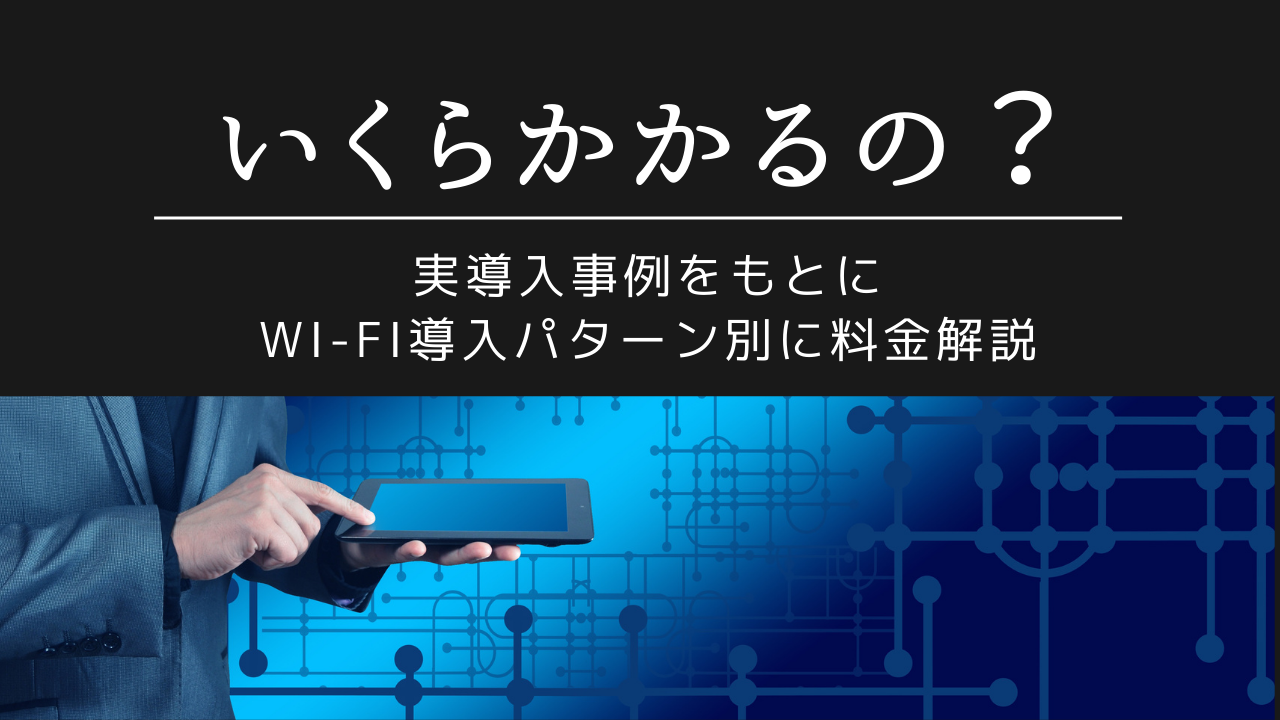
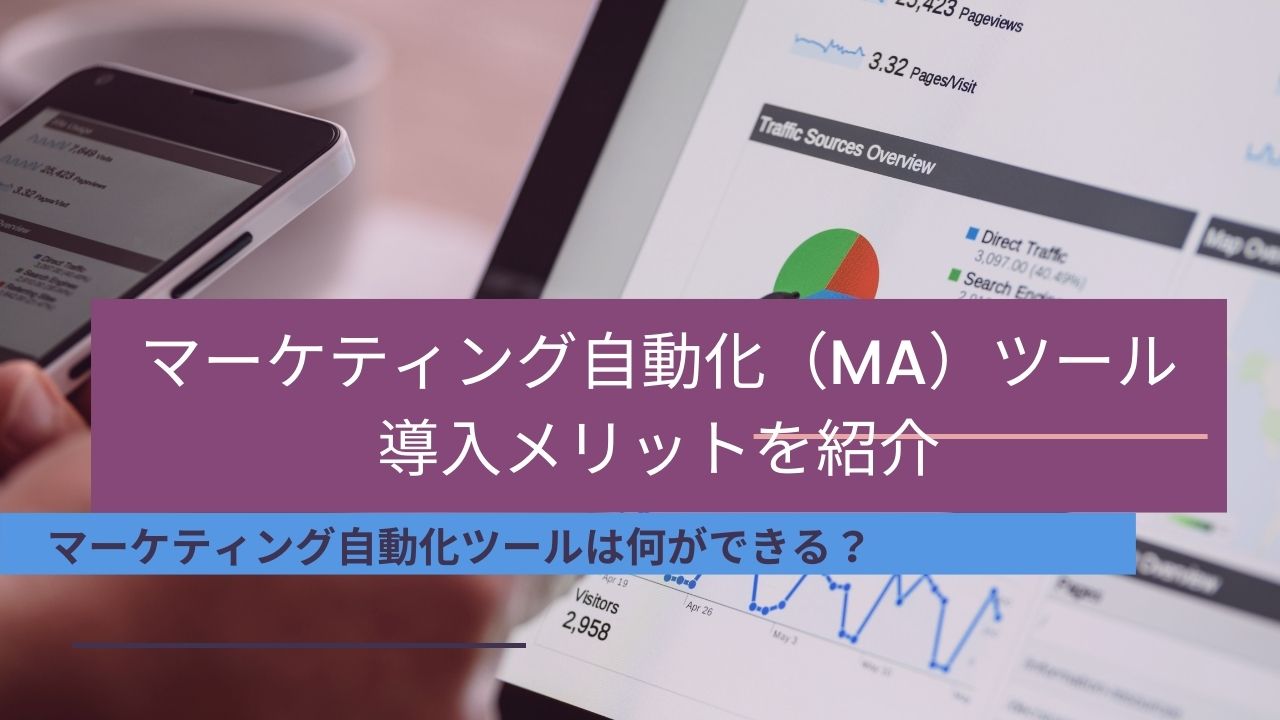
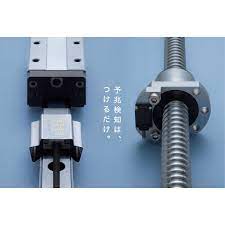
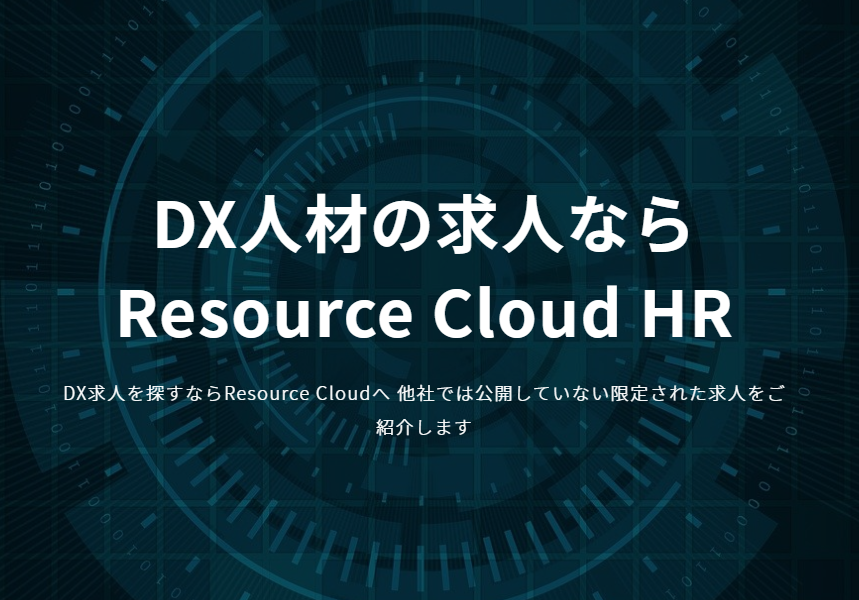
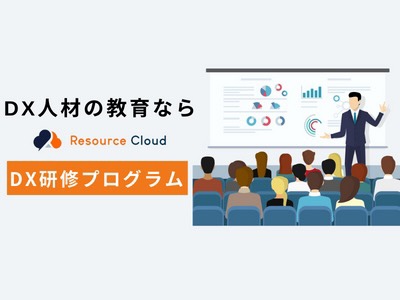
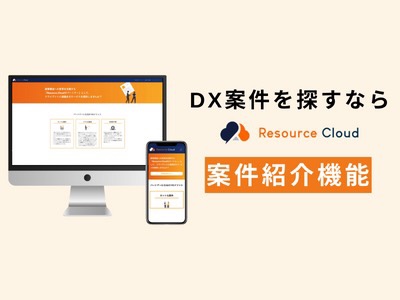