【DX事例紹介】事後保全とは? PoCと事後保全で成功する製造業のDX事例を紹介

前回、製造業におけるデジタルトランスフォーメーション(以下、DX)の事例として、メンテナンスの「予防保全」をテーマにご紹介しました。
先述した通り、メンテナンスは「予防保全」「事後保全」「予知保全」の3つに分類されるため、本記事では「事後保全」をテーマに製造業におけるDX事例をみていきます。
事後保全のメリットとデメリットは?予防保全・予知保全との違いとは?
まず初めに、事後保全とは「故障や性能低下したら直ぐに交換する」というメンテナンス手法です。他のメンテナンス手法との違いは「故障する前に」行うのが予防保全・予知保全であり、「故障してから」行うのが事後保全です。
そのため、事後保全のメリットは通常必要になるメンテナンスコスト(人員、部品などを抱えるリソース費用)が抑えられることにあります。逆に、デメリットで言えば機器の故障によっては製造ラインの停止リスクなどがあるため、大きな損失が発生する可能性があるということです。
損失の内容としては以下2つのケースが挙げられます。
1. 設備異常が発生している状態では、作業者や製品に対しリスクがあること
故障している最中の設備ですが、故障していても稼働可能な機器が多いため、実際に保全作業を行うまでの期間は使用出来てしまいます。その結果として、製品の破損や、作業者への災害などといったリスクに繋がってしまいます。
2. 製造ラインの突発的な停止は、事業継続にリスクがあること
製造業で事業計画を引く際、基本的には設備が正常稼働していることを前提に行います。しかし、一度設備が故障してしまうと緊急メンテナンスが必要になるため、計画が大幅に遅れてしまいます。その結果、需要と供給のバランスが崩れ、機会損失を生み、最悪のケースでは事業継続に大きなリスクがあります。
以上のことから、事後保全する対象は「安全上、生産上に問題がなく、かつ補修工数が短い」ケースに向いているため、まだPoCの段階であれば事後保全を最優先に考えましょう。
事後保全はPoCに最適! 事業をスケールさせるために必要なメンテナンスの考え方
先ほどご紹介した「PoC」についてより具体的にみていきましょう。
そもそも、PoCとは「Proof of Concept」の略で、直訳すると「概念実証」です。近年、IT業界では広く使われている言葉で、テストマーケティングや試験的に導入しているサービスなどを指します。
では、製造業におけるPoCとはどのようなものを指すのでしょうか?異なる観点で見れば2つの意味があります。
【製造工程を観点】
- 「製造後=製品」・・・サンプル製品を作り購入者の反応を得ること
- 「製造中=生産」・・・新たな機器やシステムの導入を試験的に行うこと
どちらの観点でも同様ですが、製造業は他の業界と比較して設備・人員リソースなどの事業投資金額が高額になりがちなため、PoCをする際には必要最低限のコストに抑えることが重要だからこそ、固定維持費がかからない事後保全はPoCに向いていると言えます。
しかし、事後保全がPoCに向いているからと言ってPoCの段階で全ての設備を事後保全にして良い訳ではありません。
その際、必ずケアしなければならないのが、”人体”および”建物”の「安全面」です。いくらPoCの段階とは言え、人体や建物の安全が保障されていなければ、最悪の場合企業活動に大きな支障が出るため、そういった場面ではこれまで通り「予防保全」や「予知保全」を採用するなどの判断が必要になります。
そして、事業がスケールしていった際には、「事後保全」から「予防保全」や「予知保全」にシフトしていけばいいでしょう。
大まかな考え方としては以上になりますが、製造業でPoCを導入し成功している企業がある一方、「PoCから先に進めない」または「そもそもPoCを開始出来ない」などの悩みを抱えている企業が数多くあるのも事実です。
しかし、PoCの考え方を上手に取り入れることで、生産過程の変化のみならず、製品の品質サイクルの改善や新規事業着手など、これこそが「ただのデジタル化ではないあるべきDXの形」と言えるのではないでしょうか?
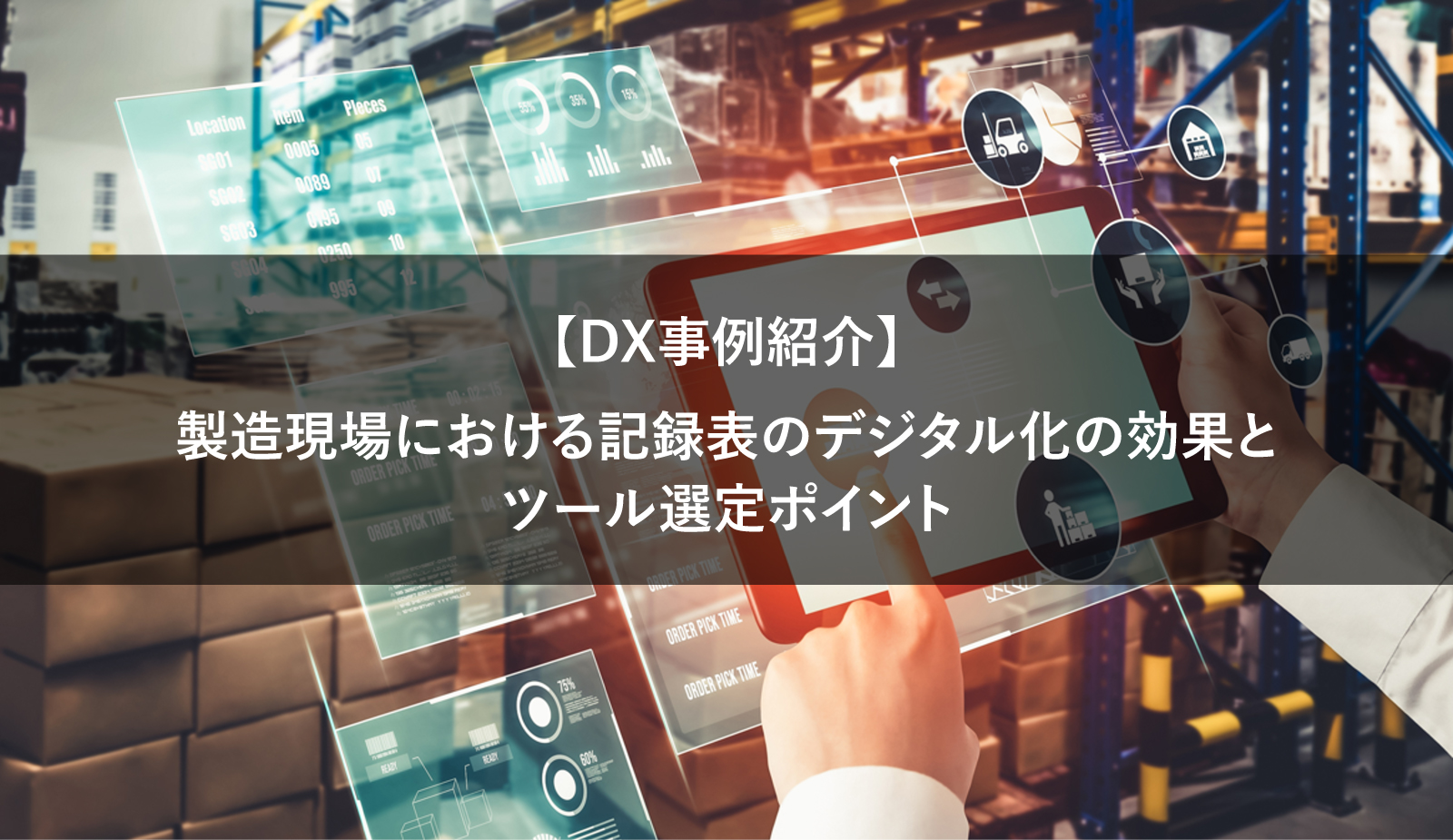
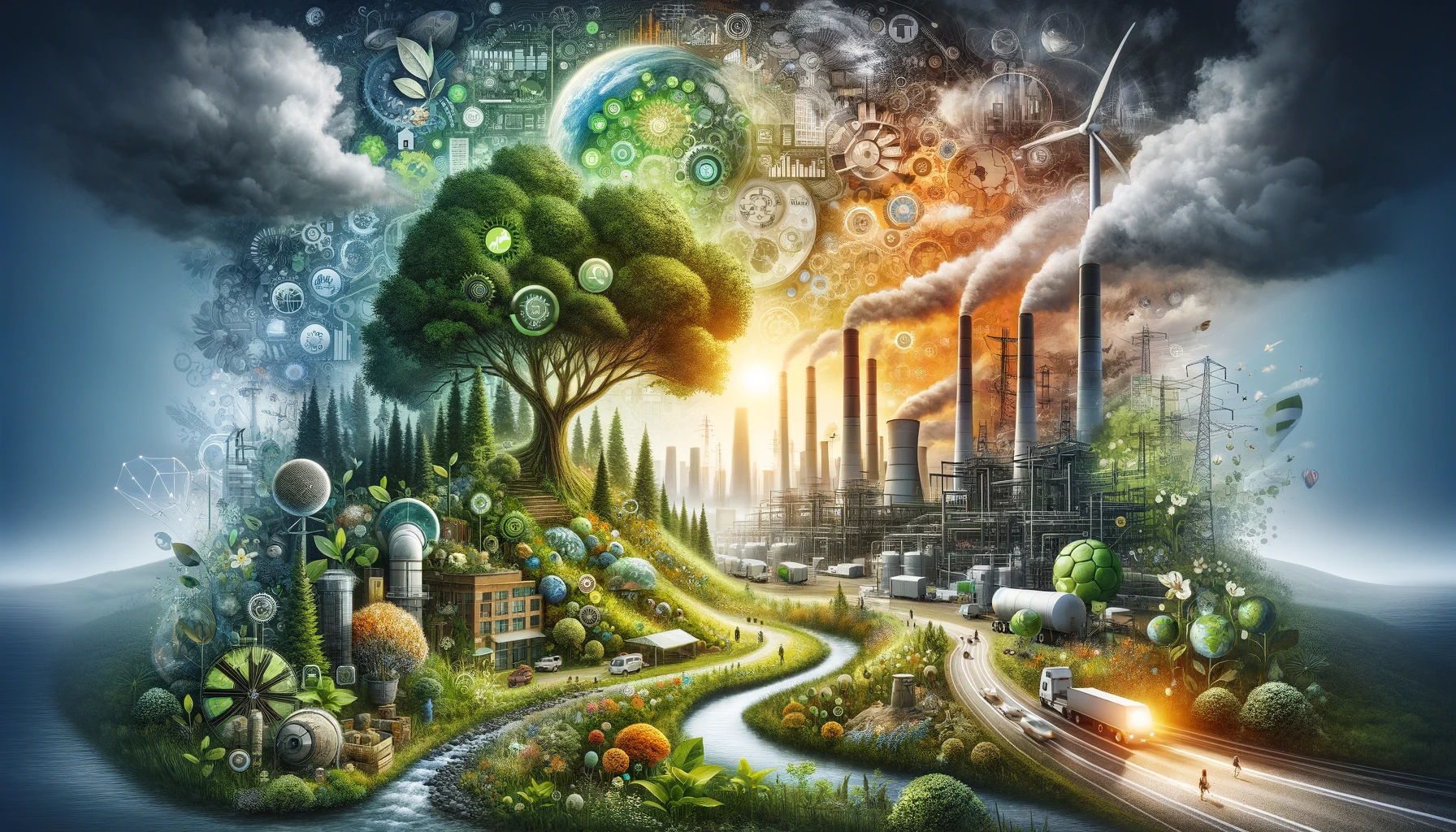
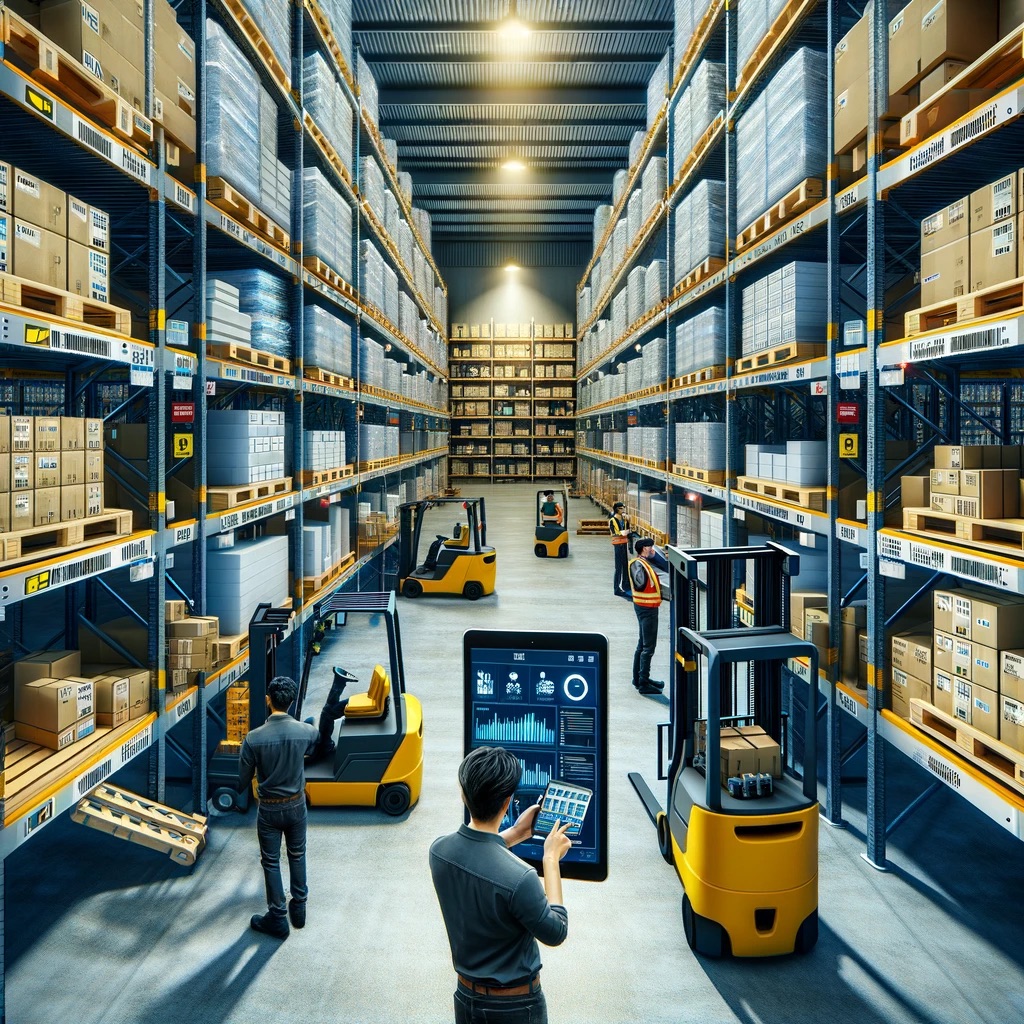
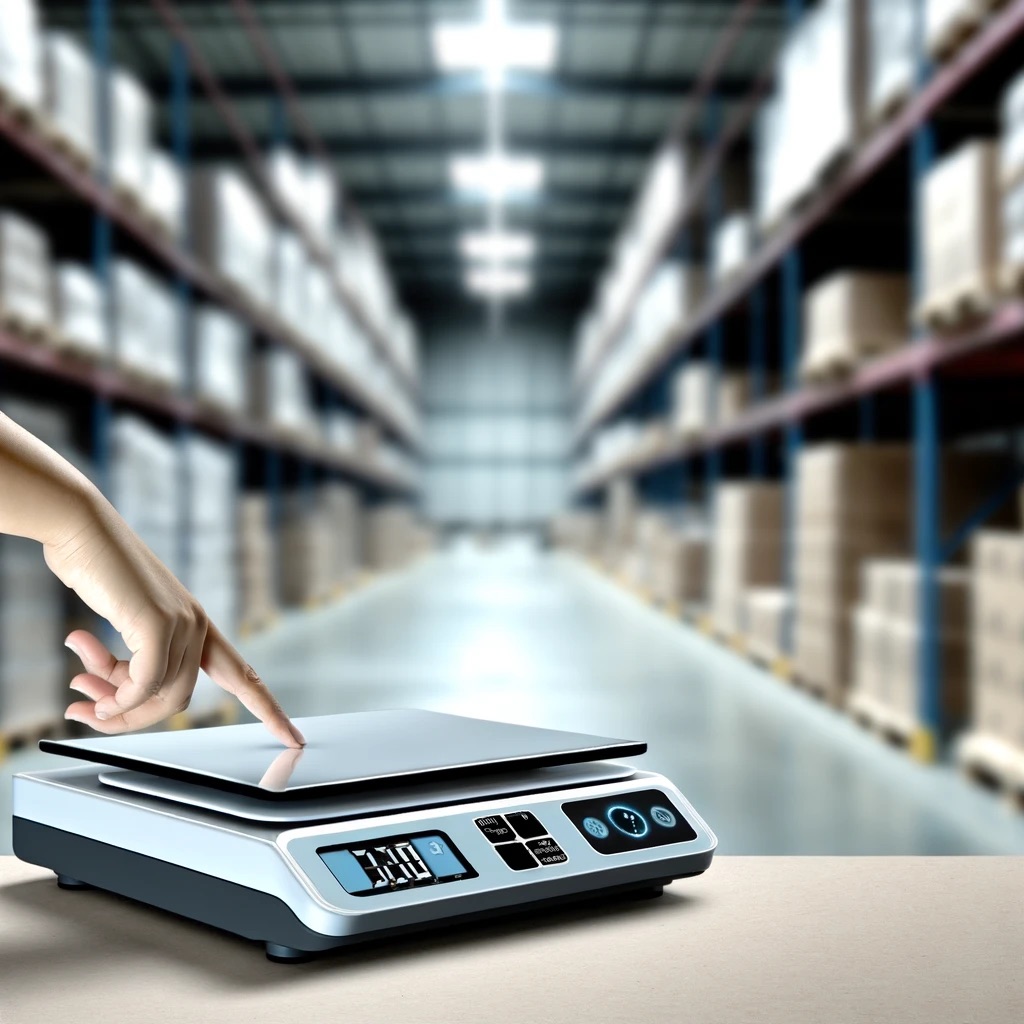
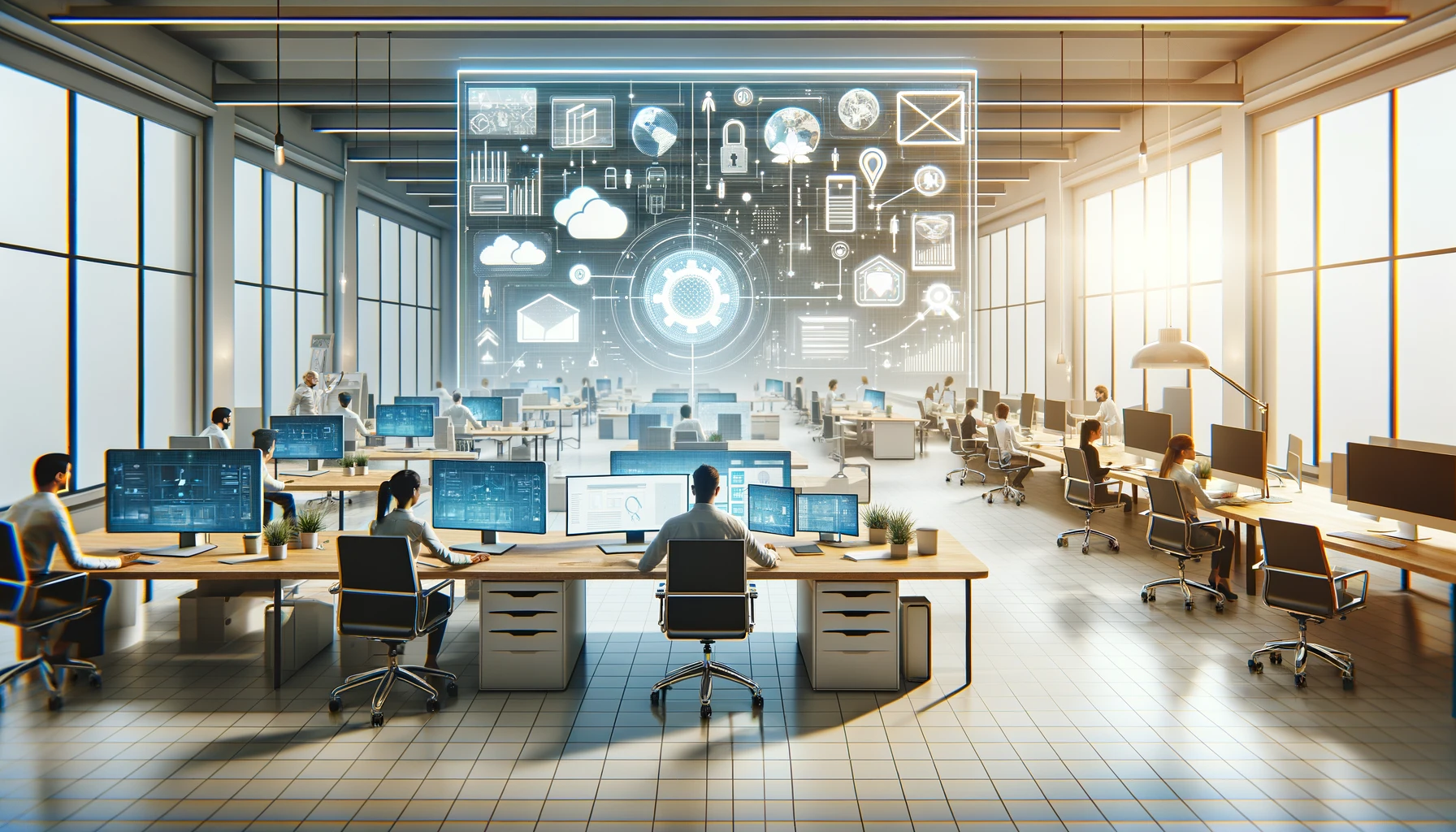
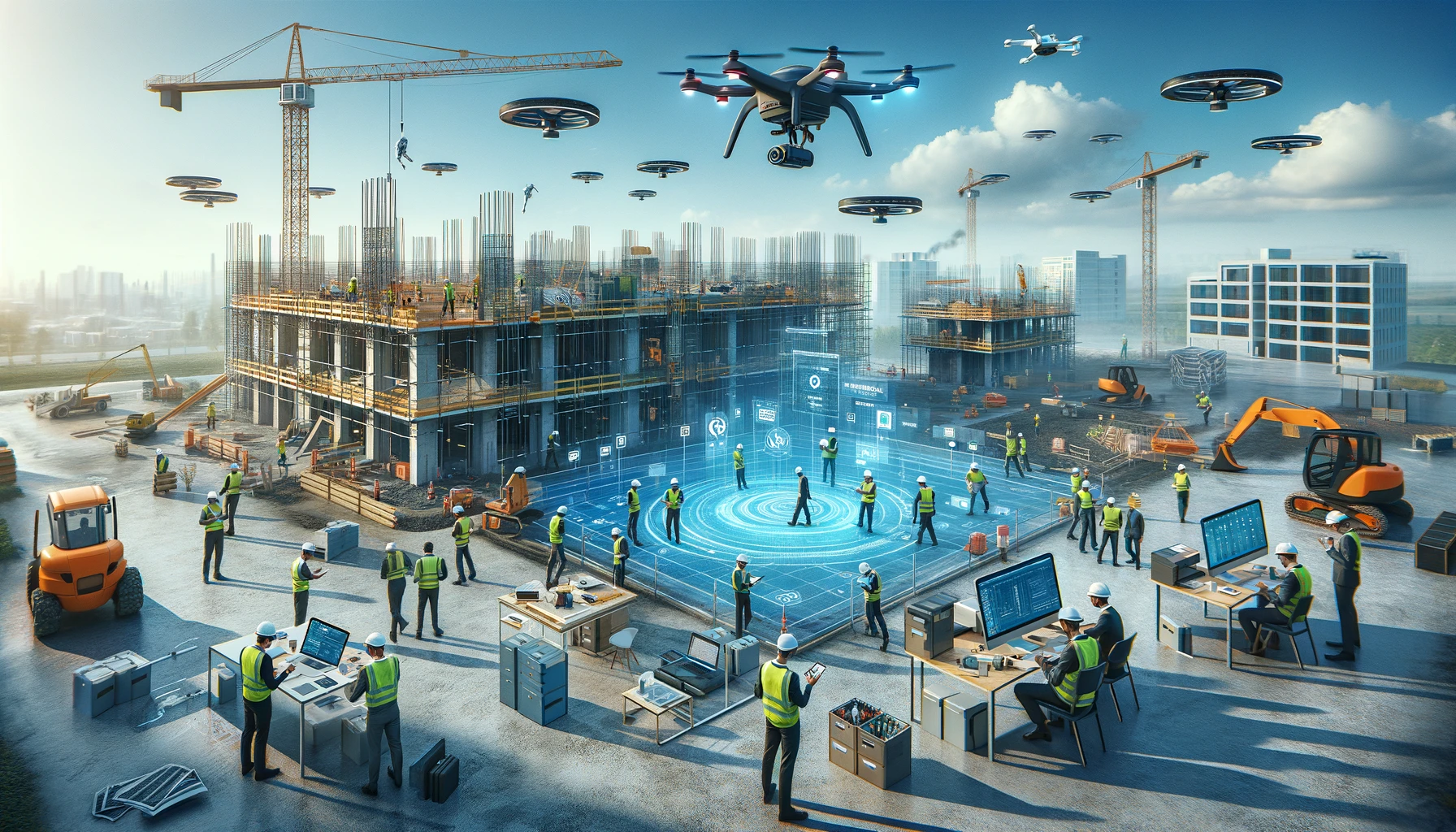
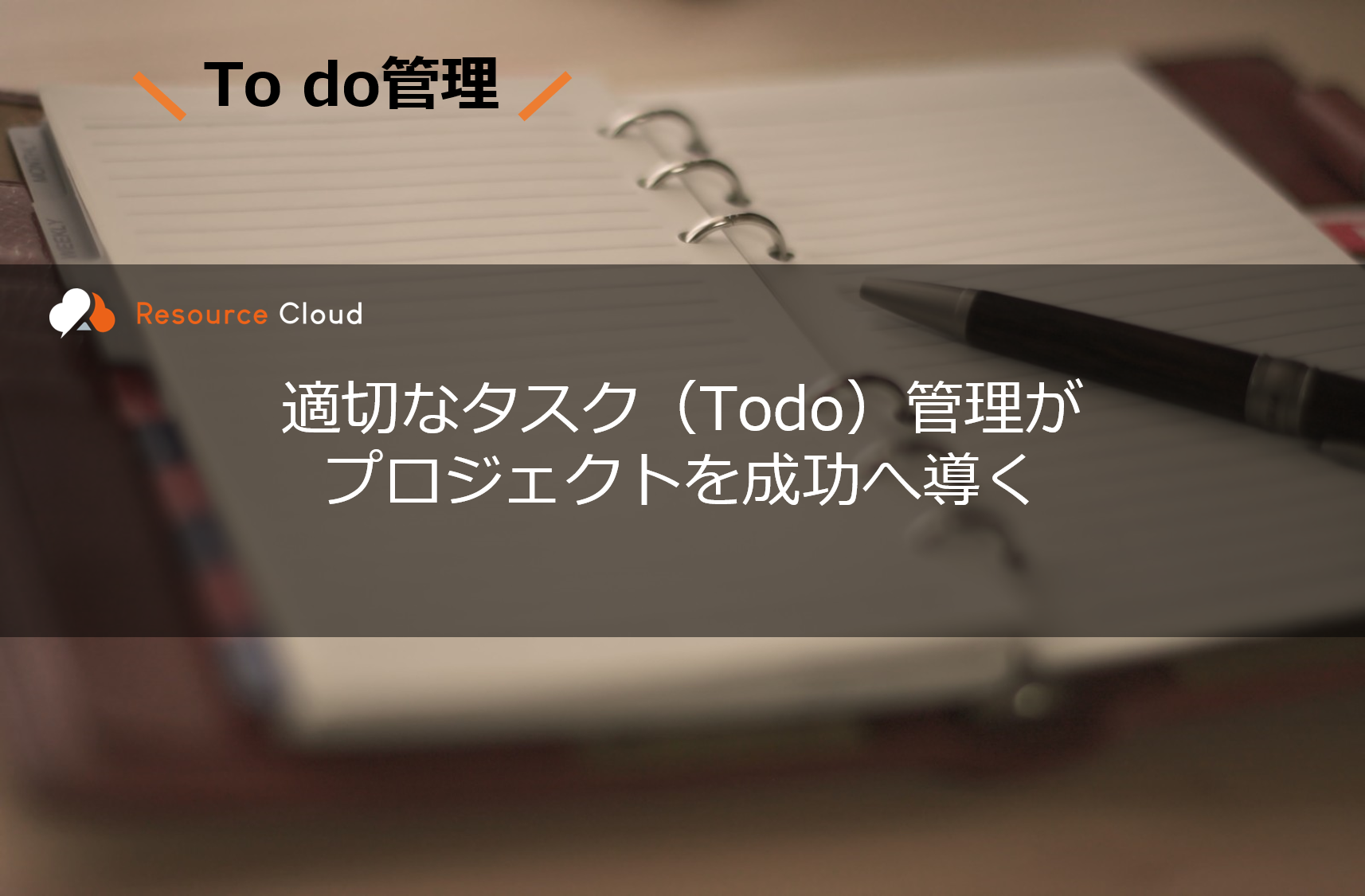
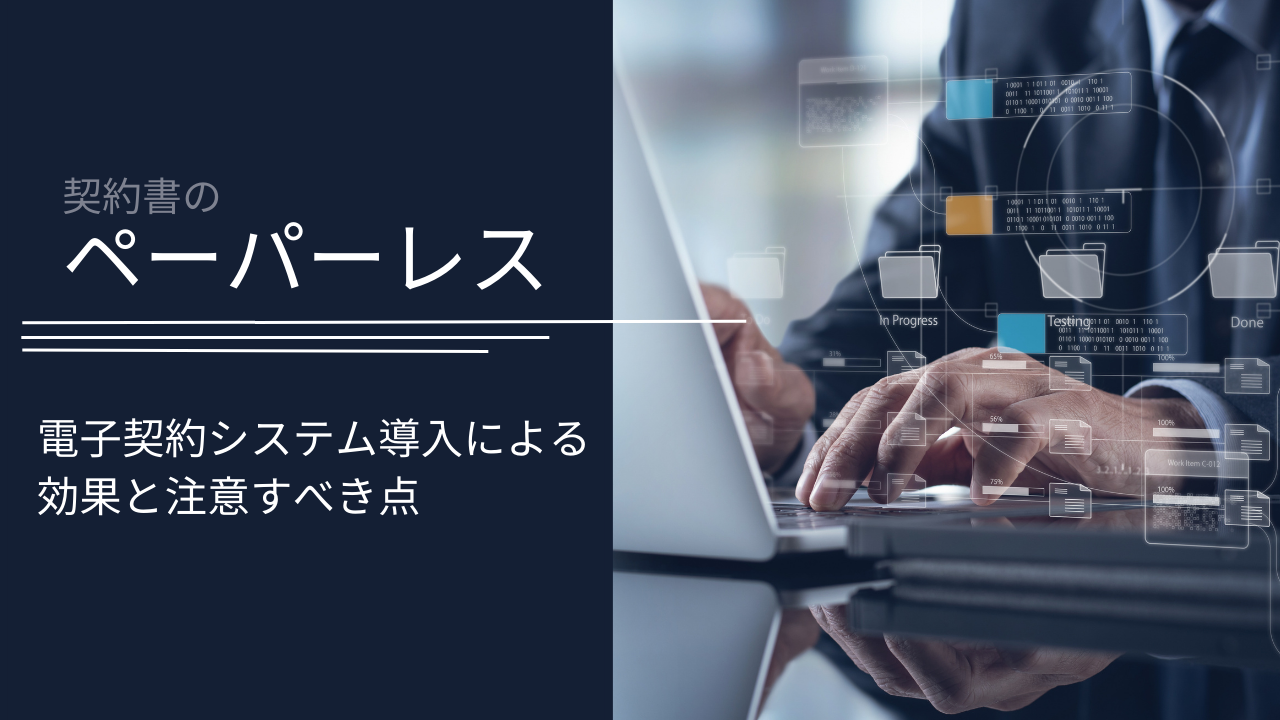
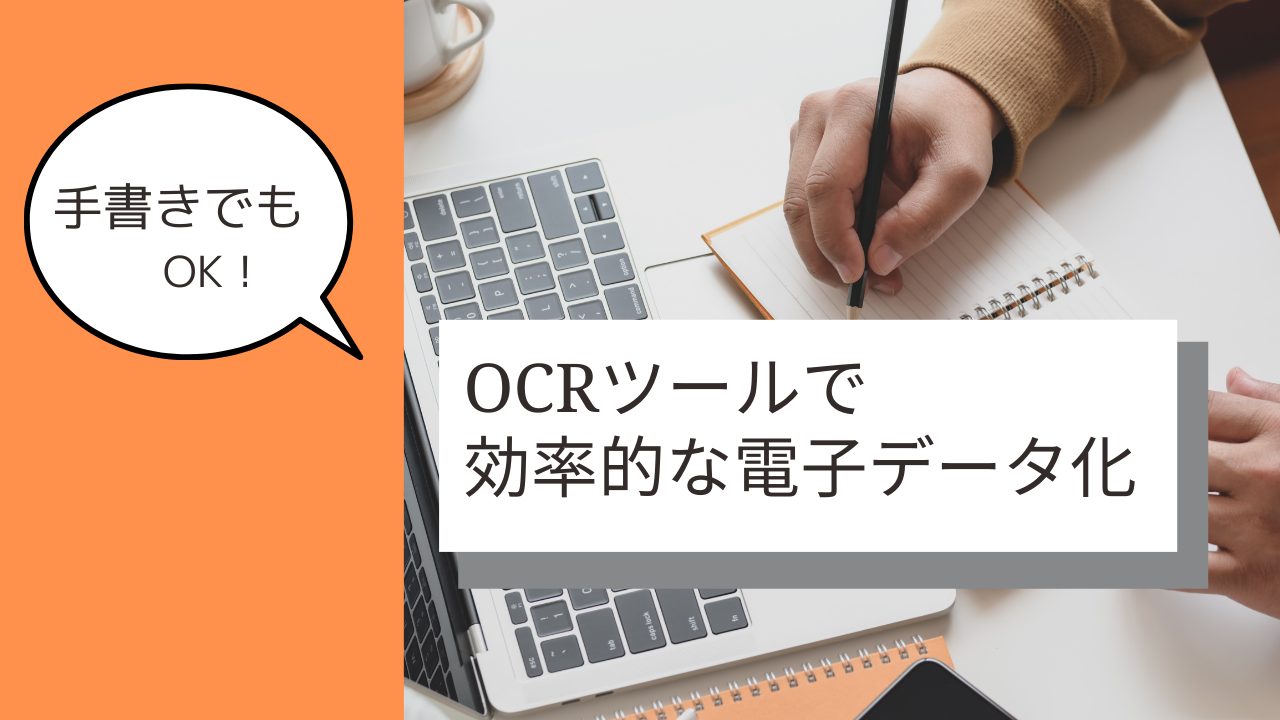
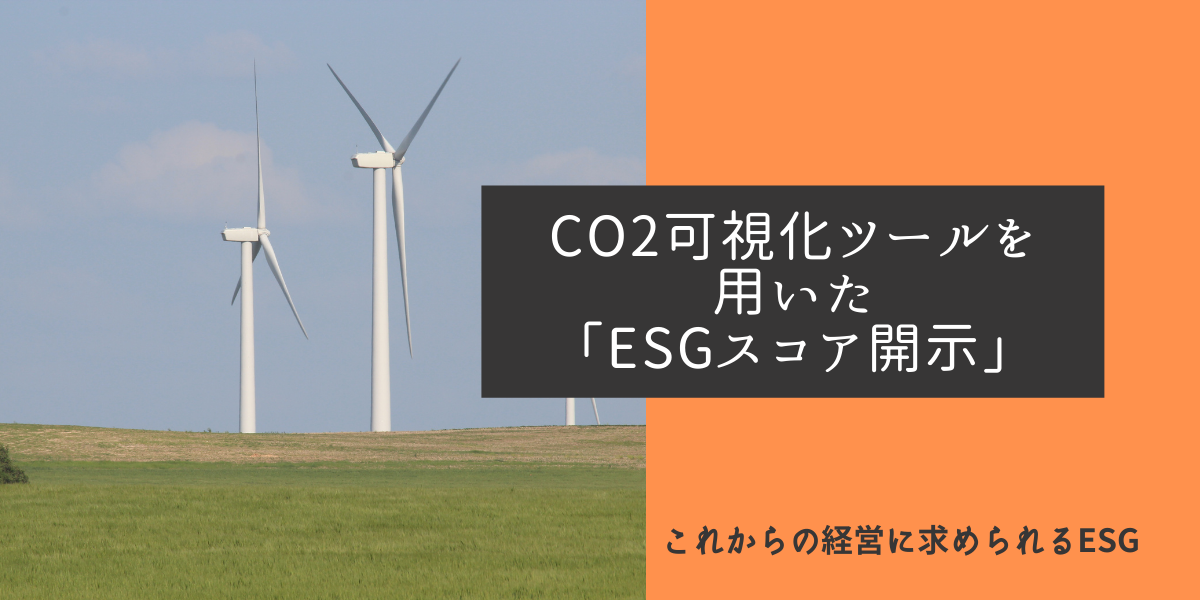
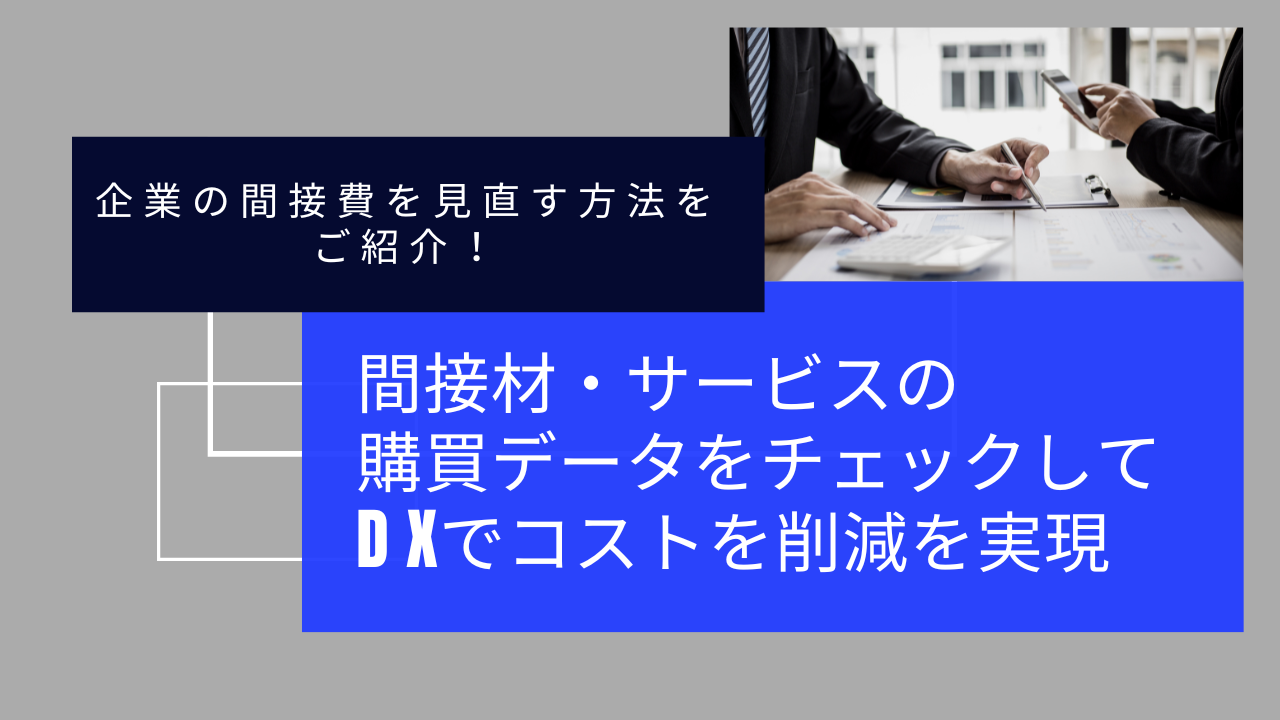
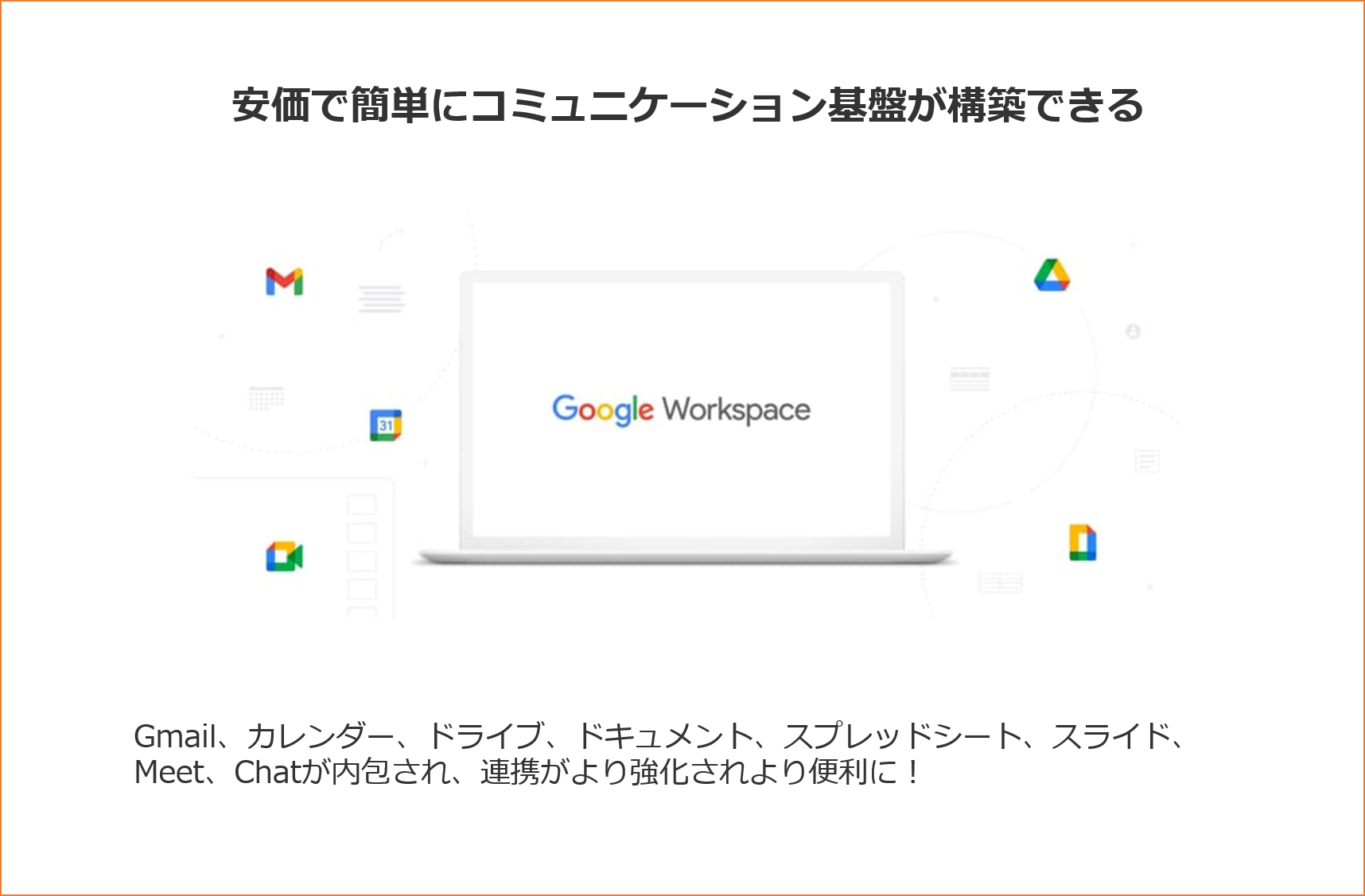
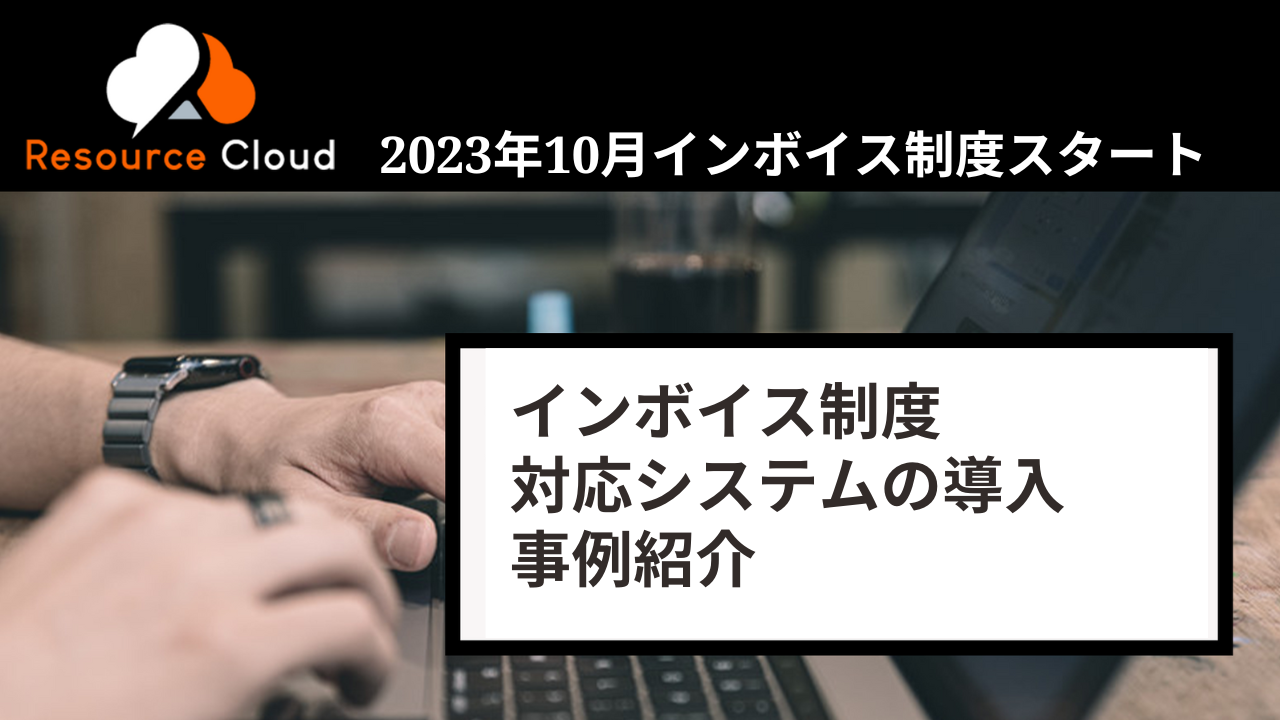
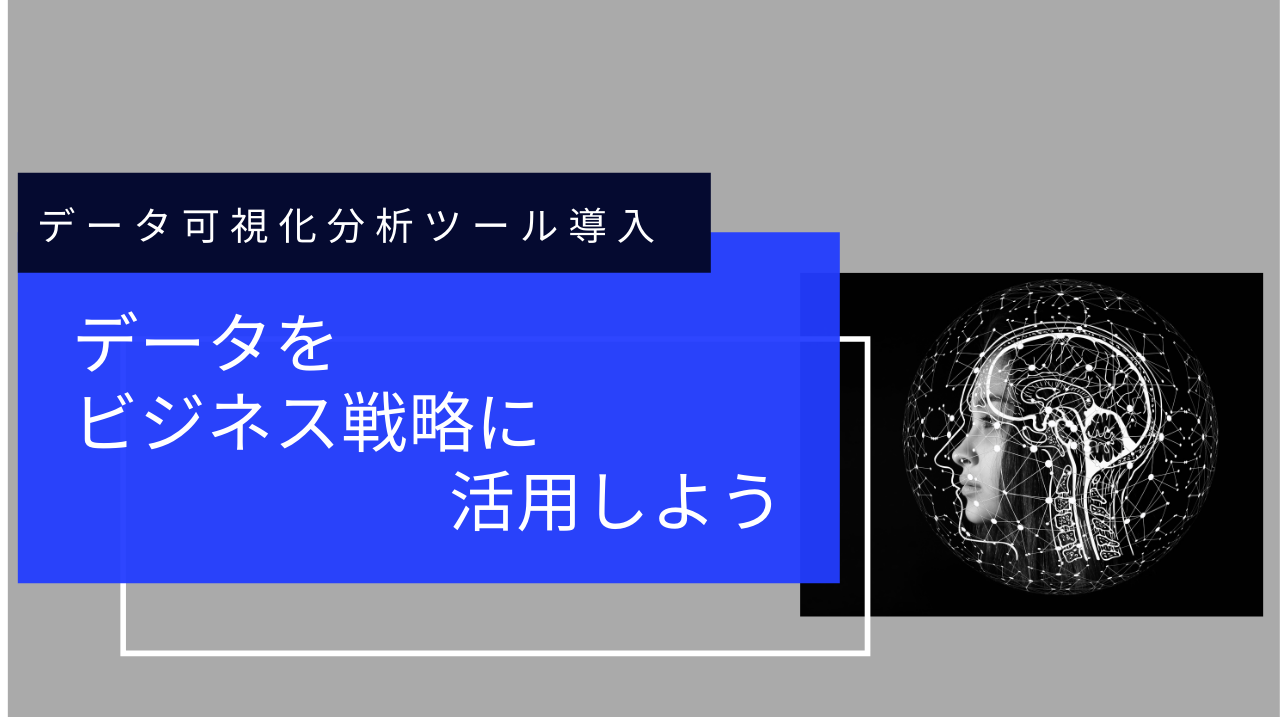
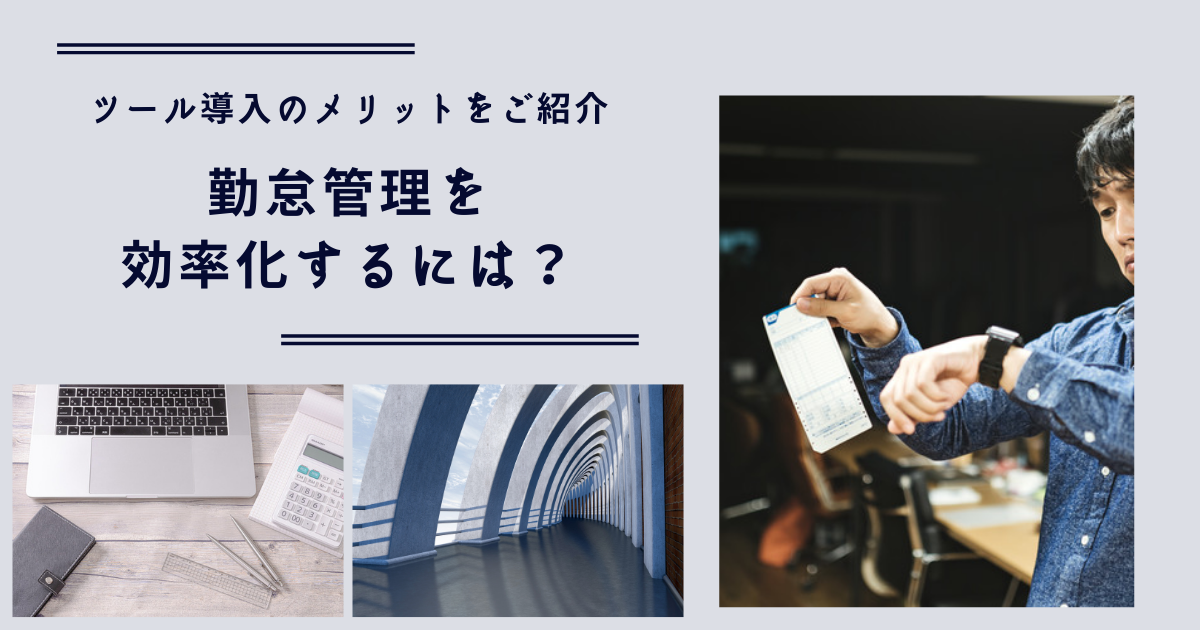
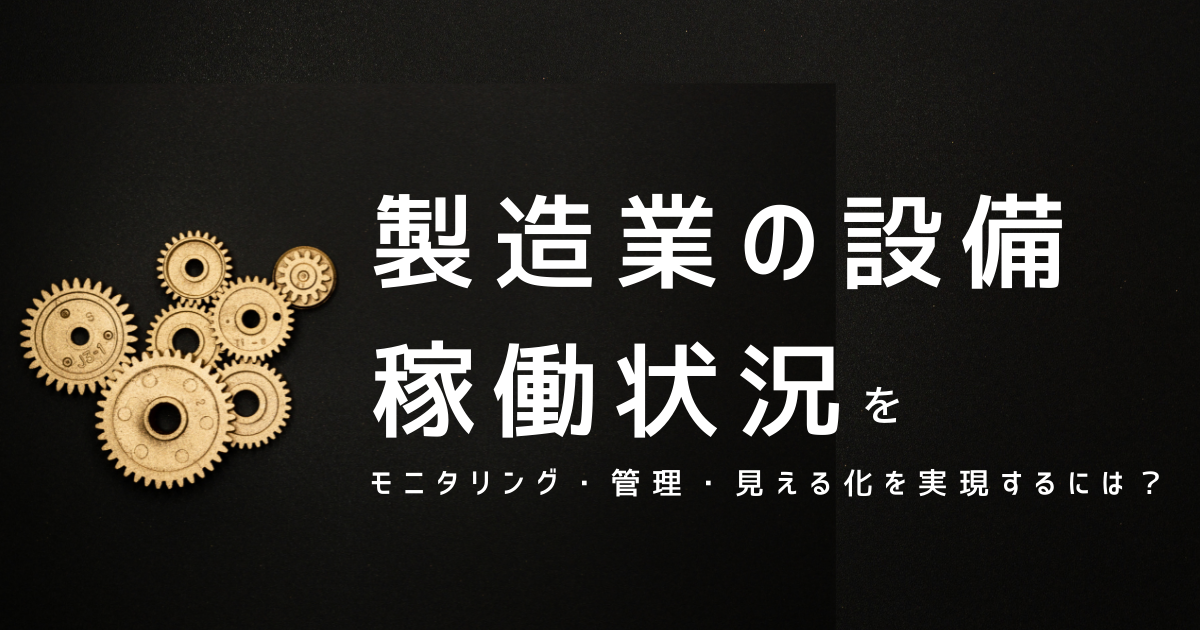
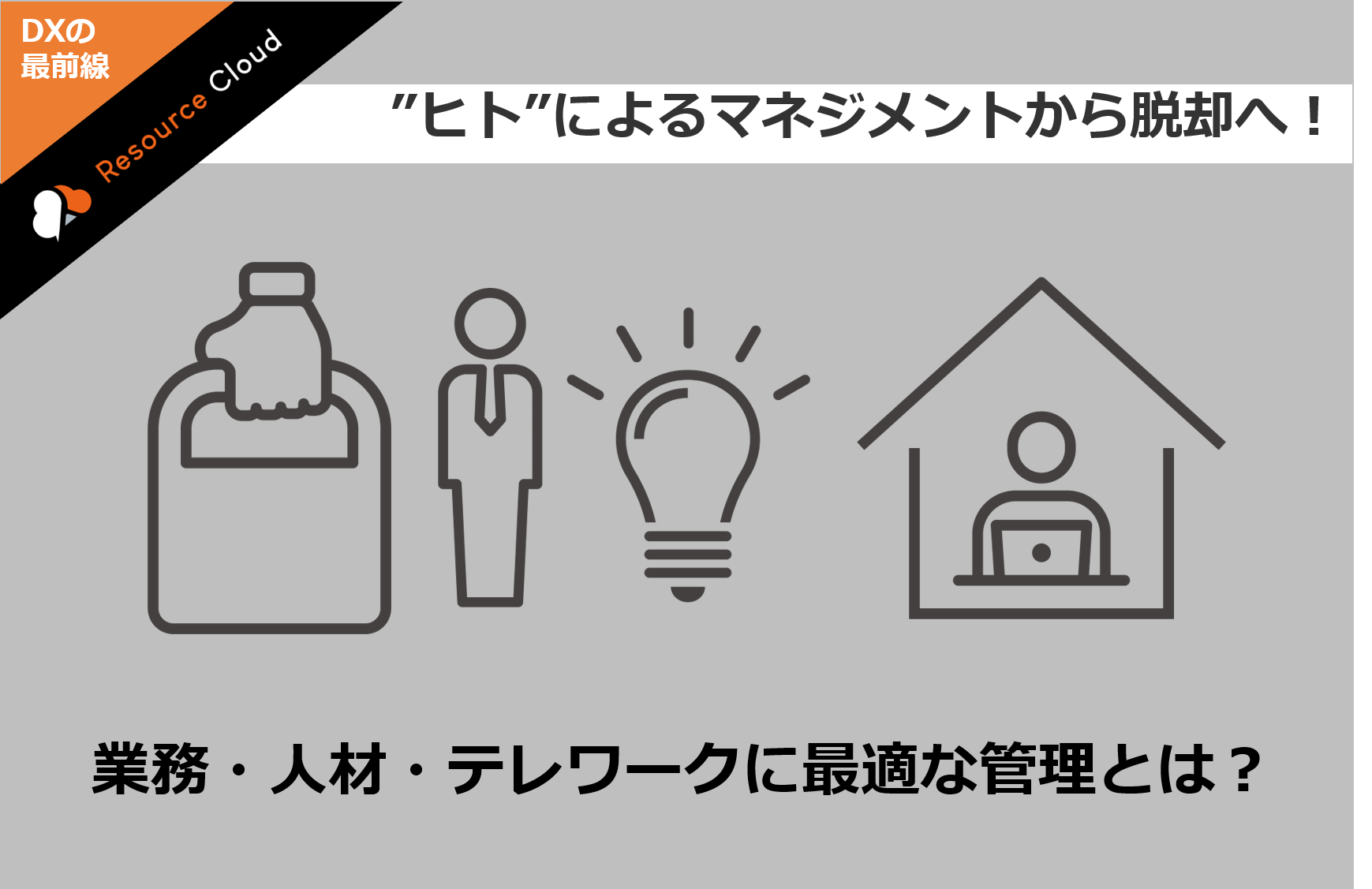
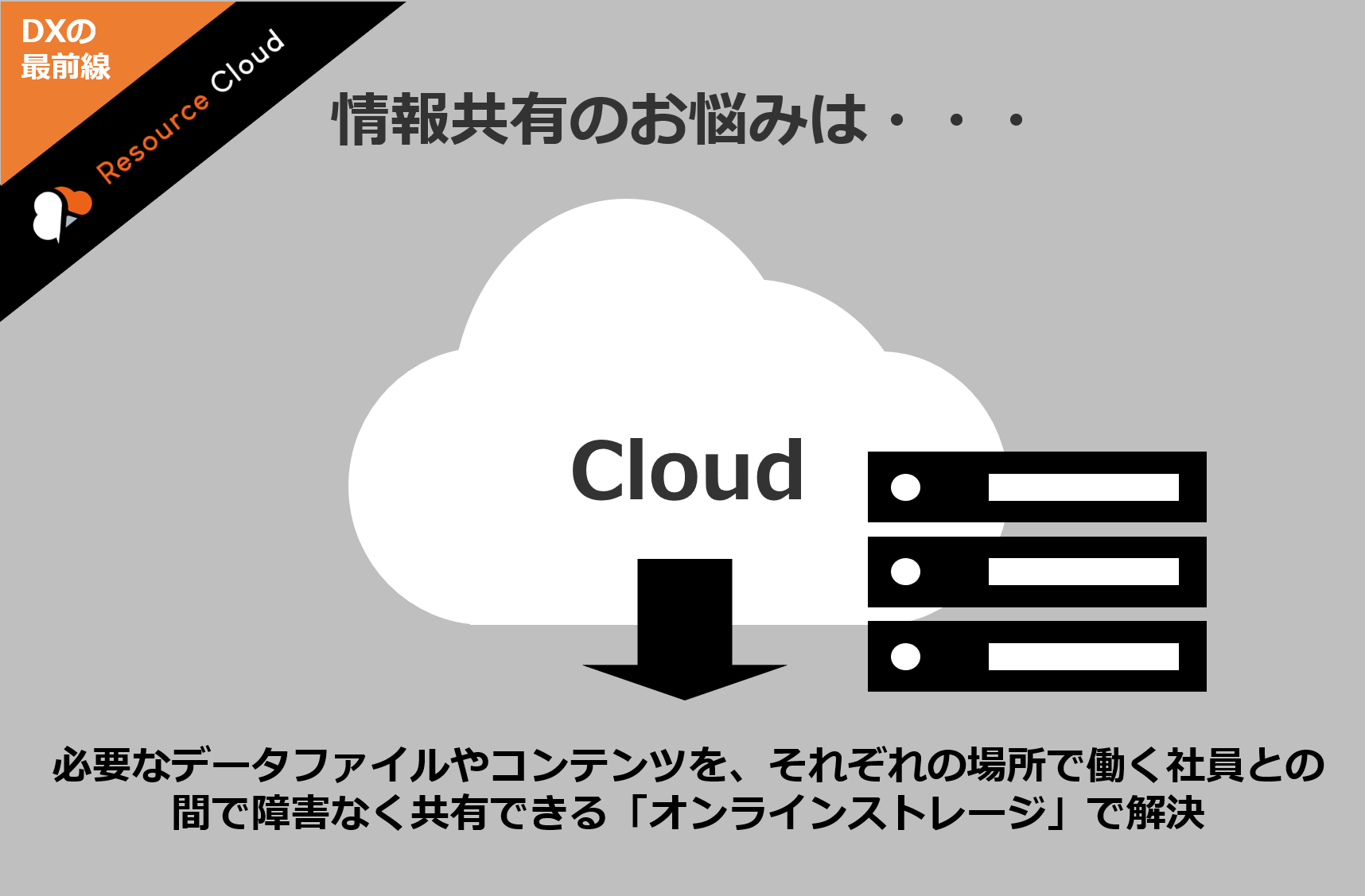
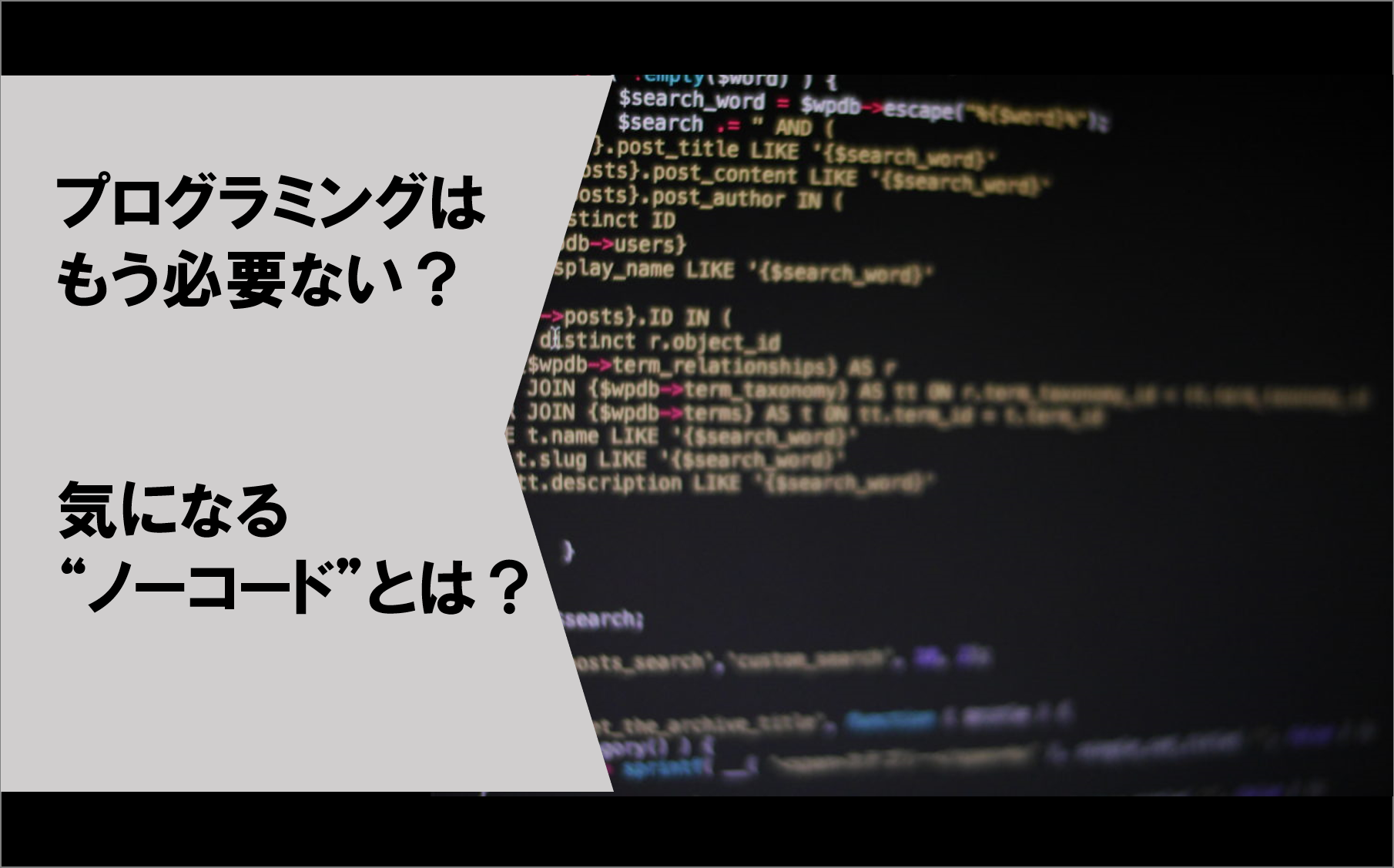
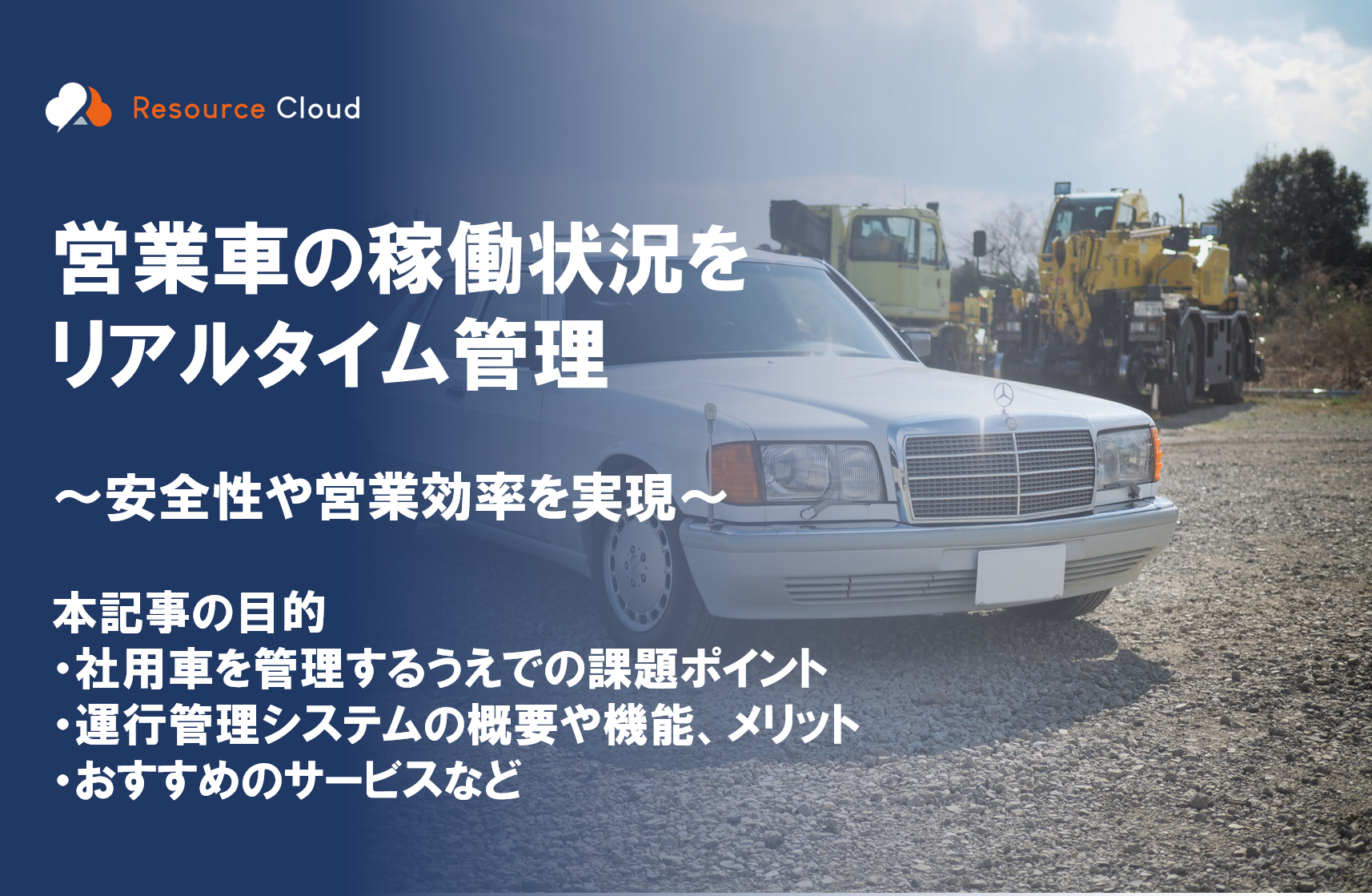
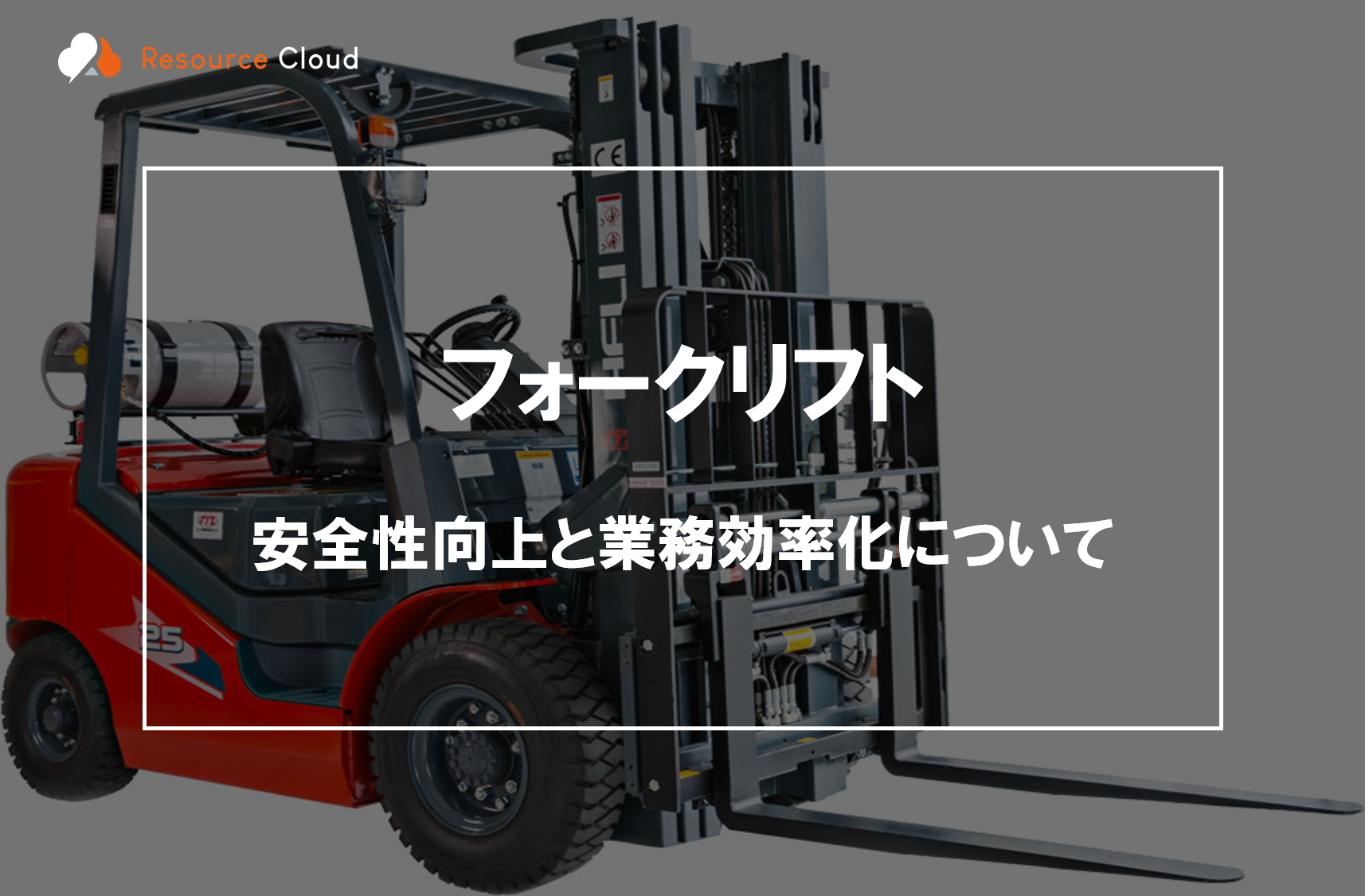
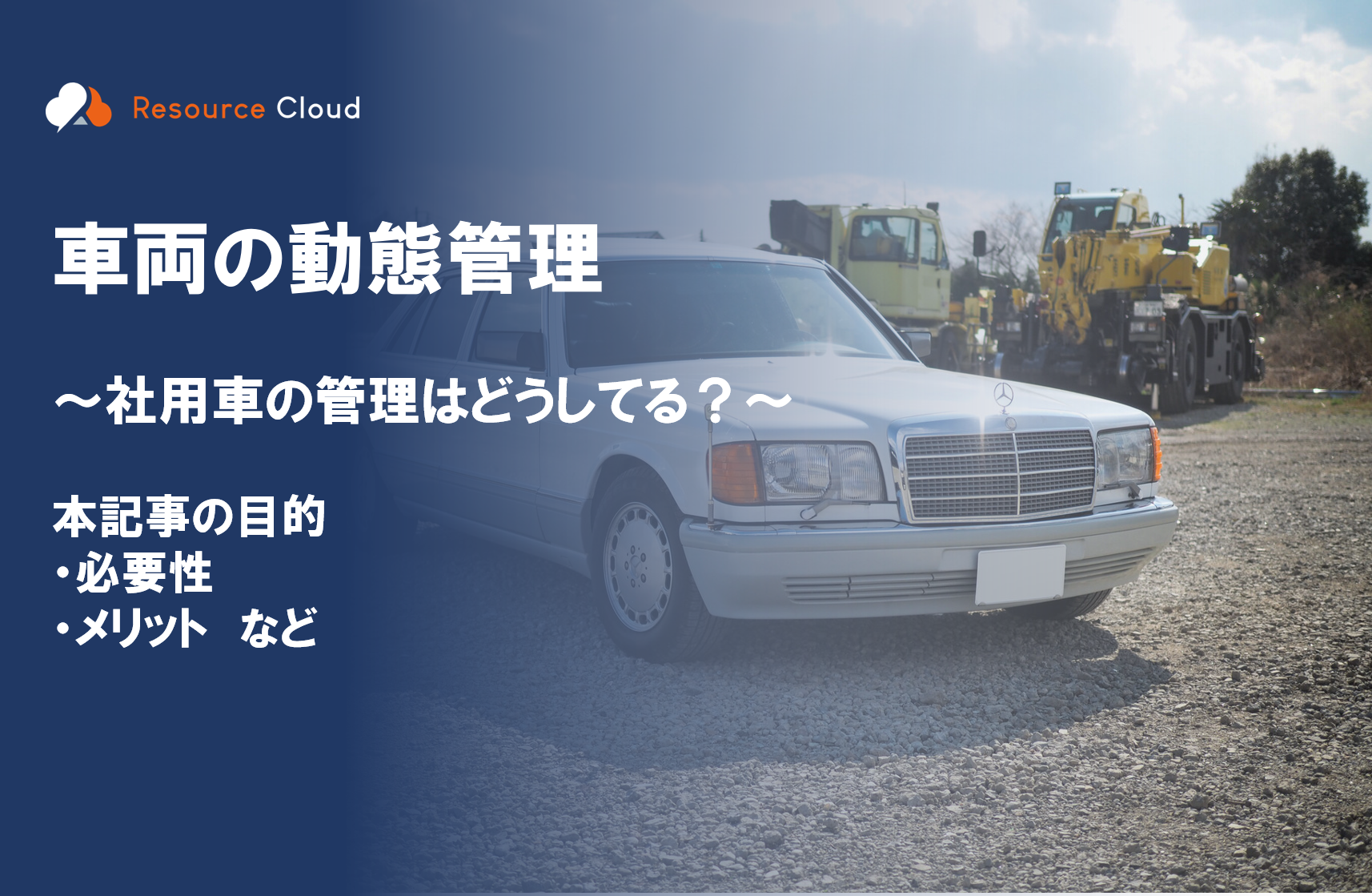
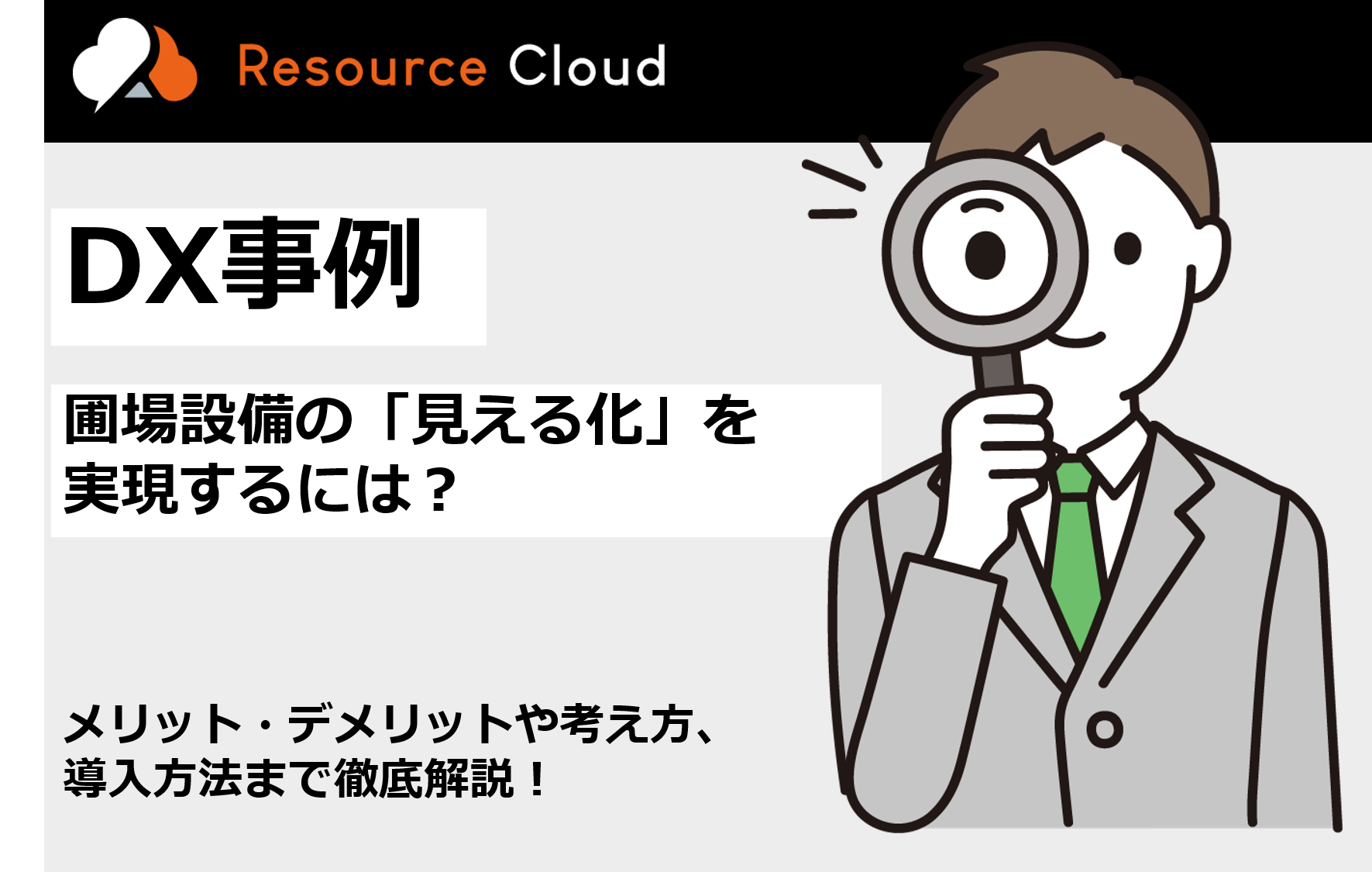
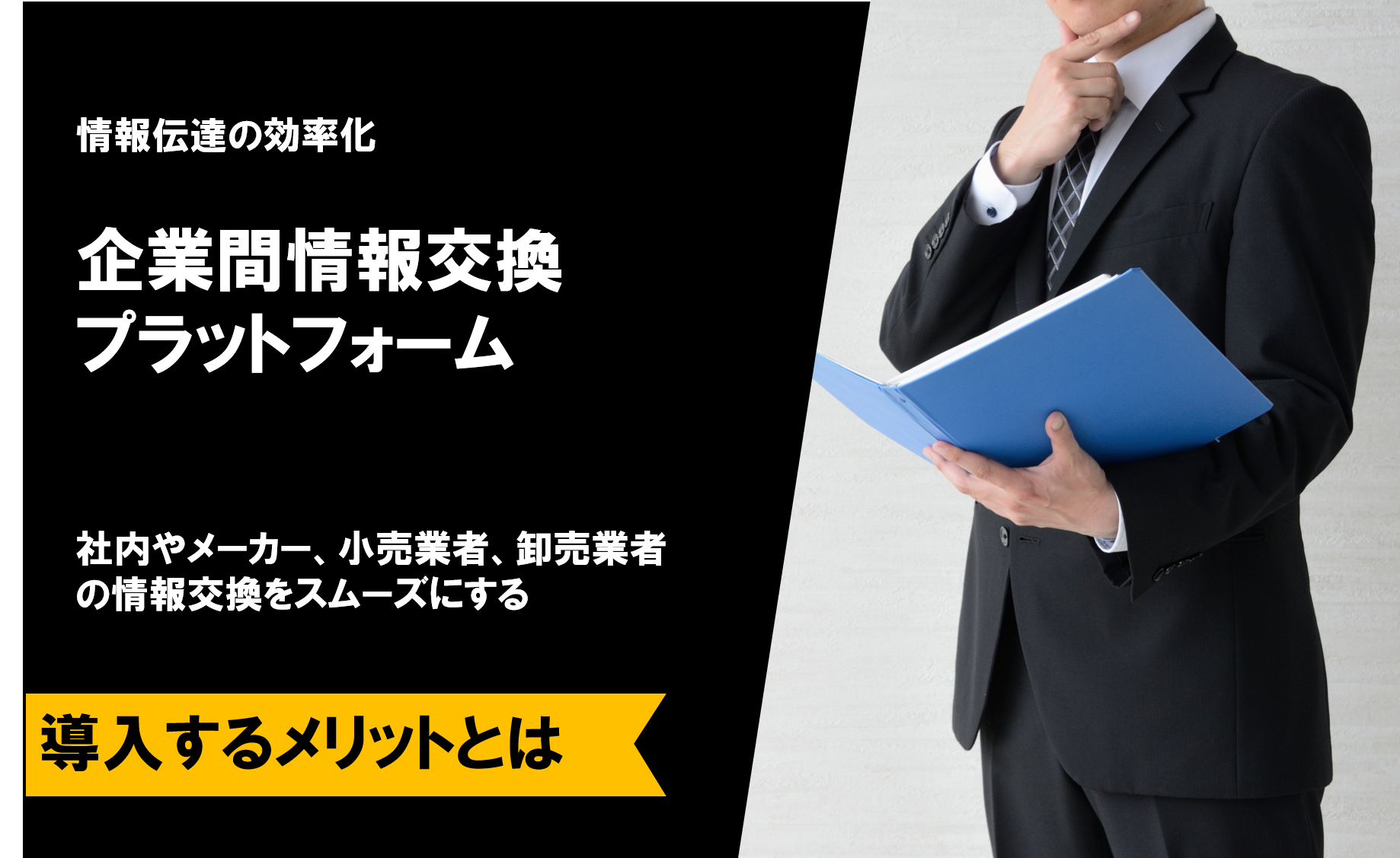
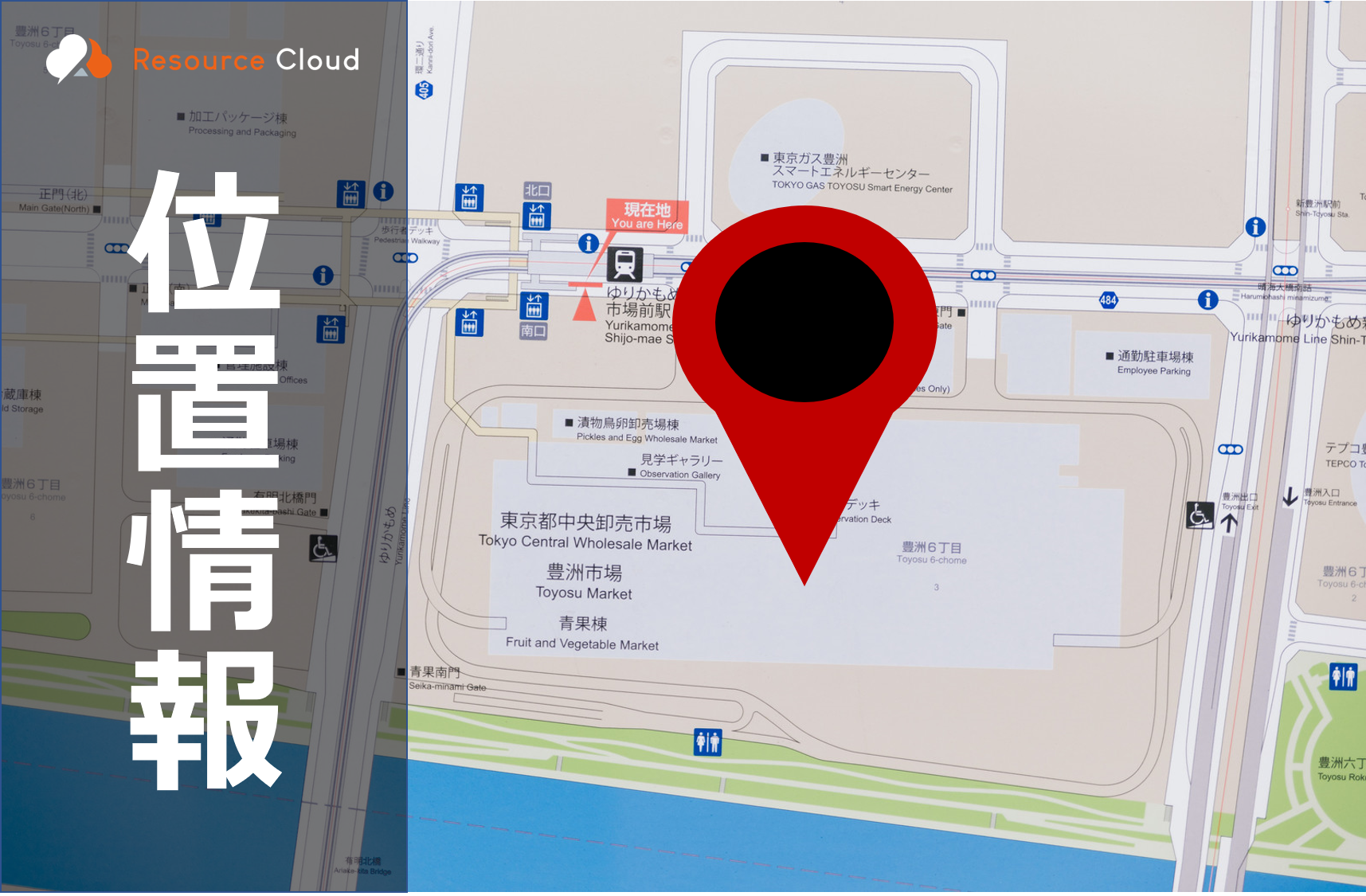
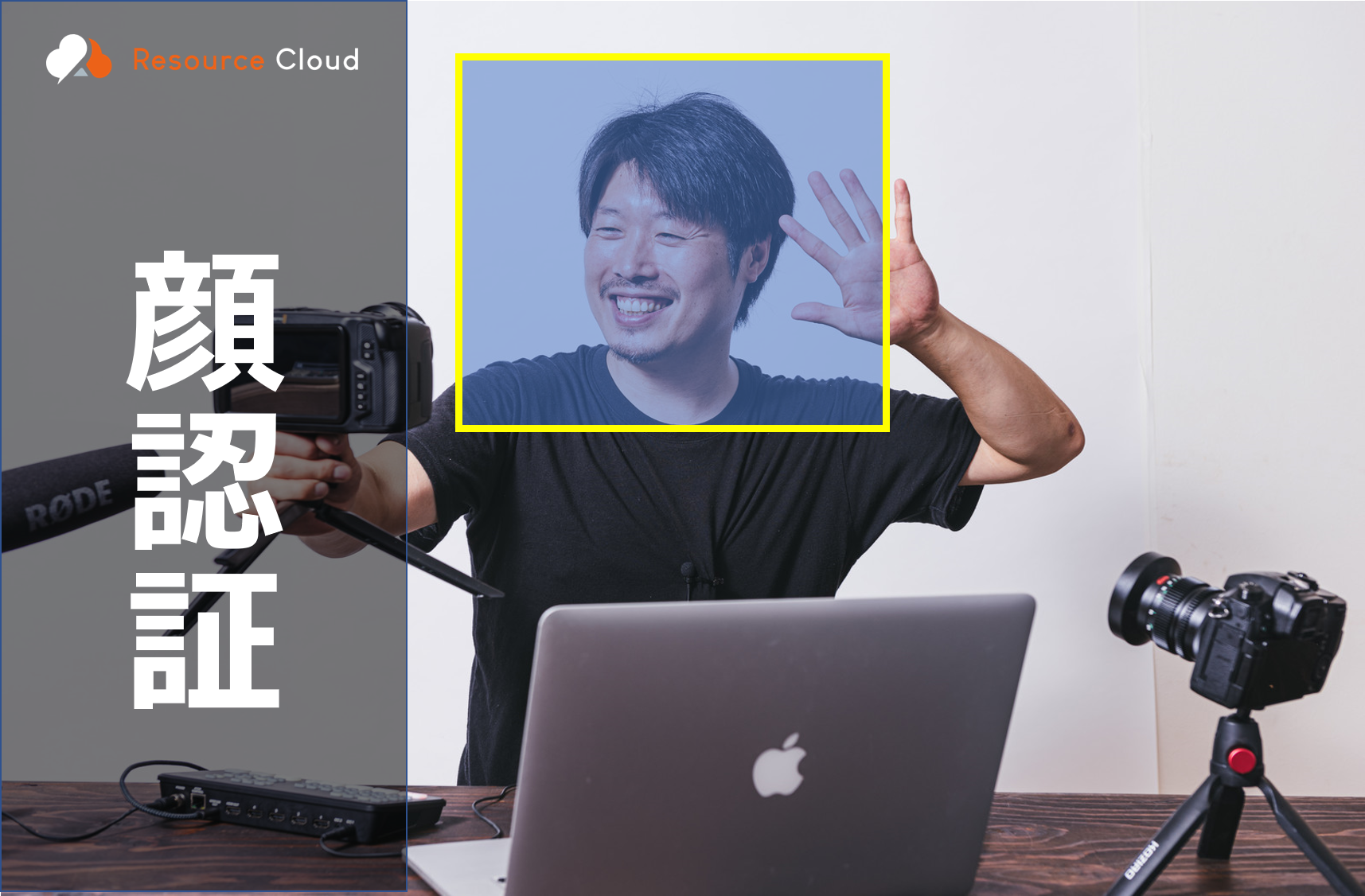
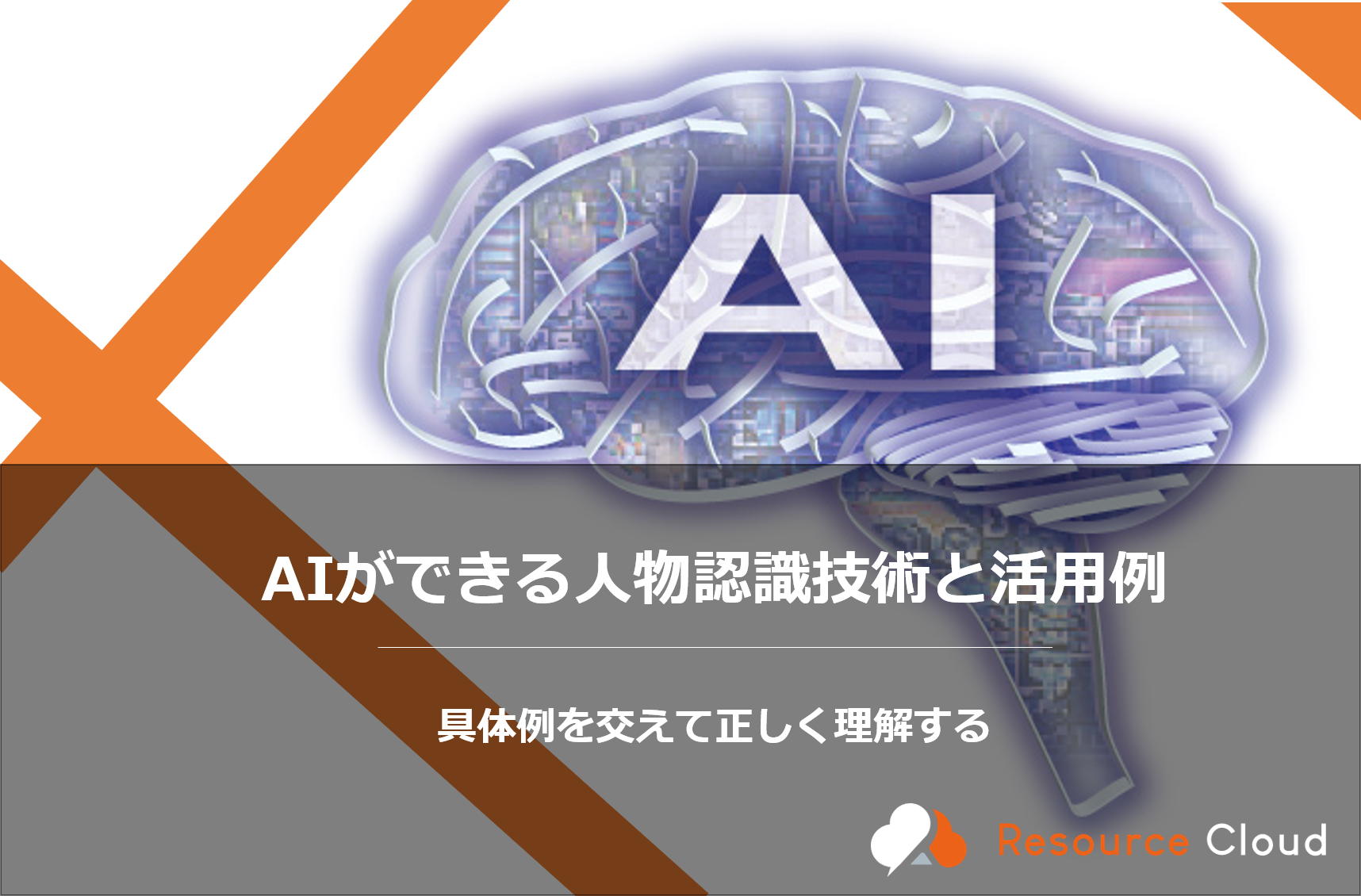
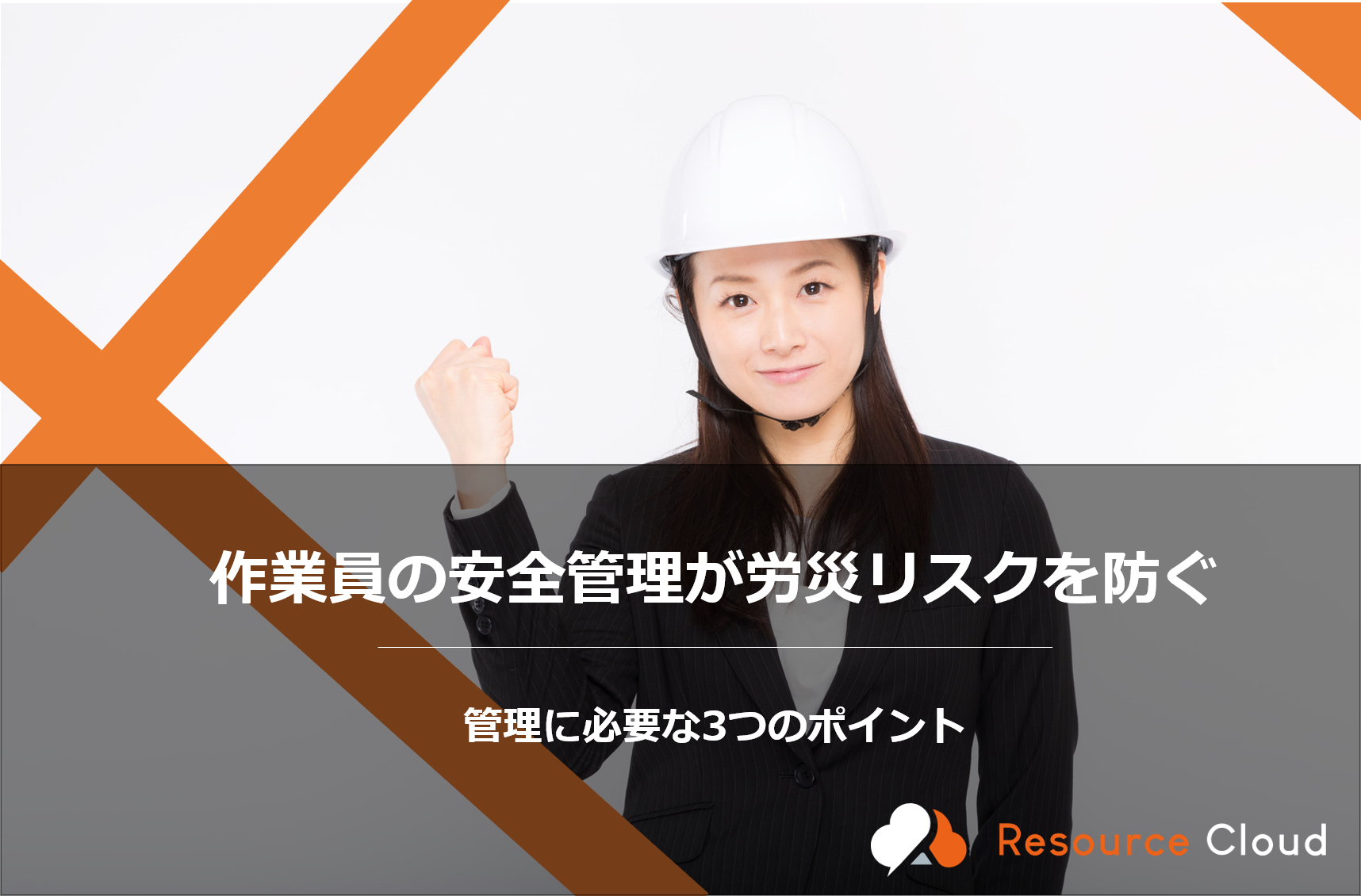
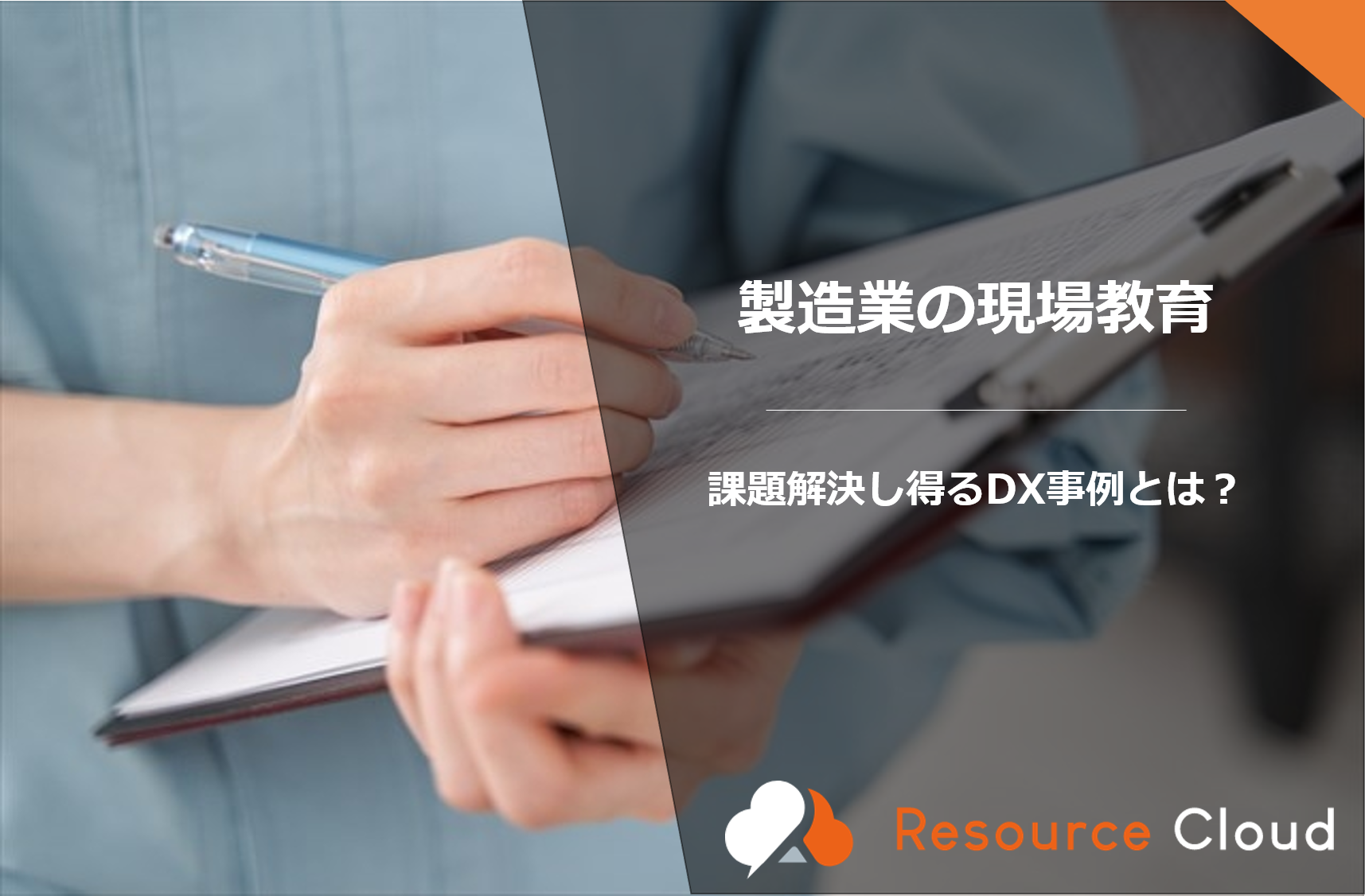
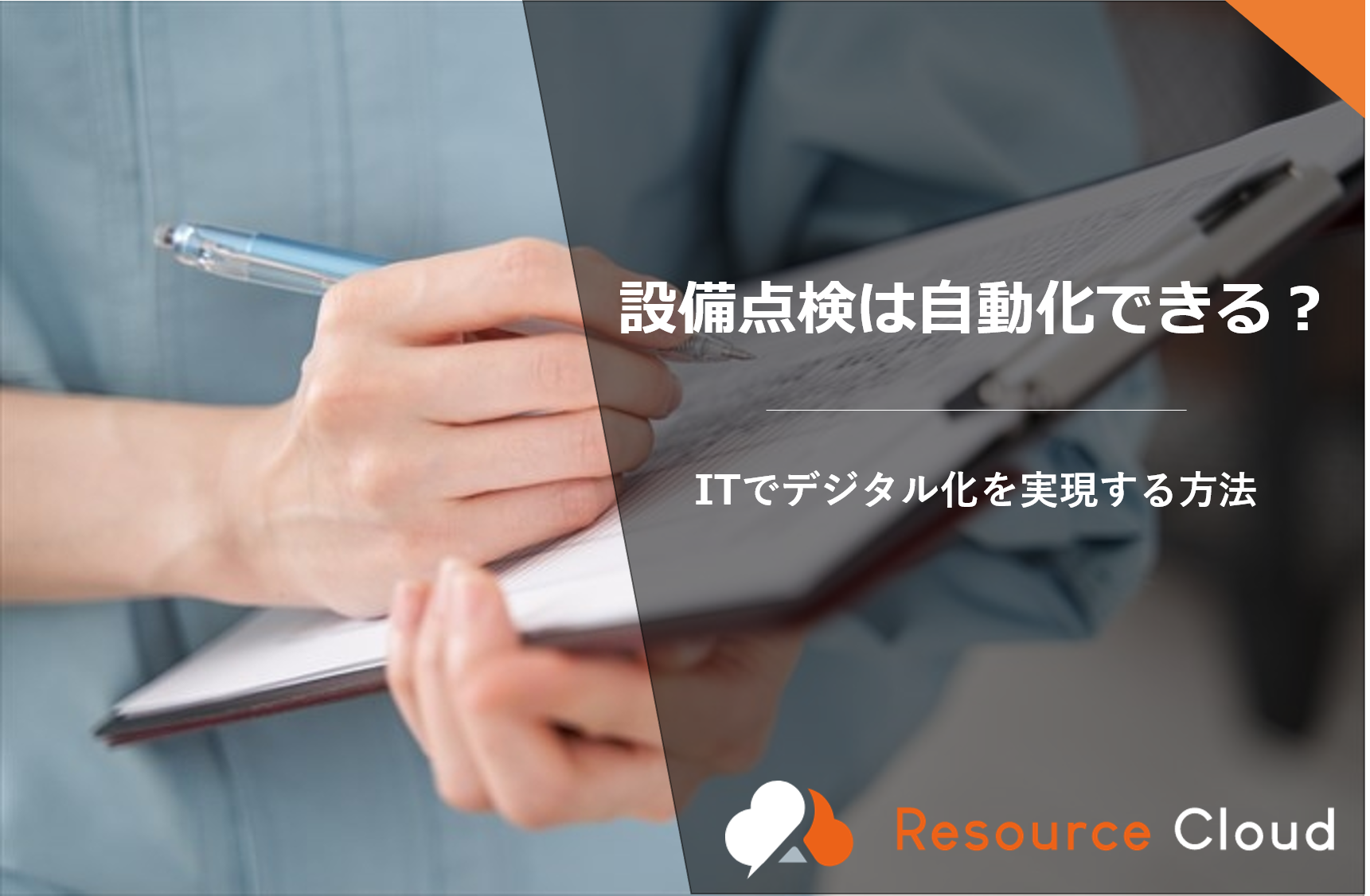
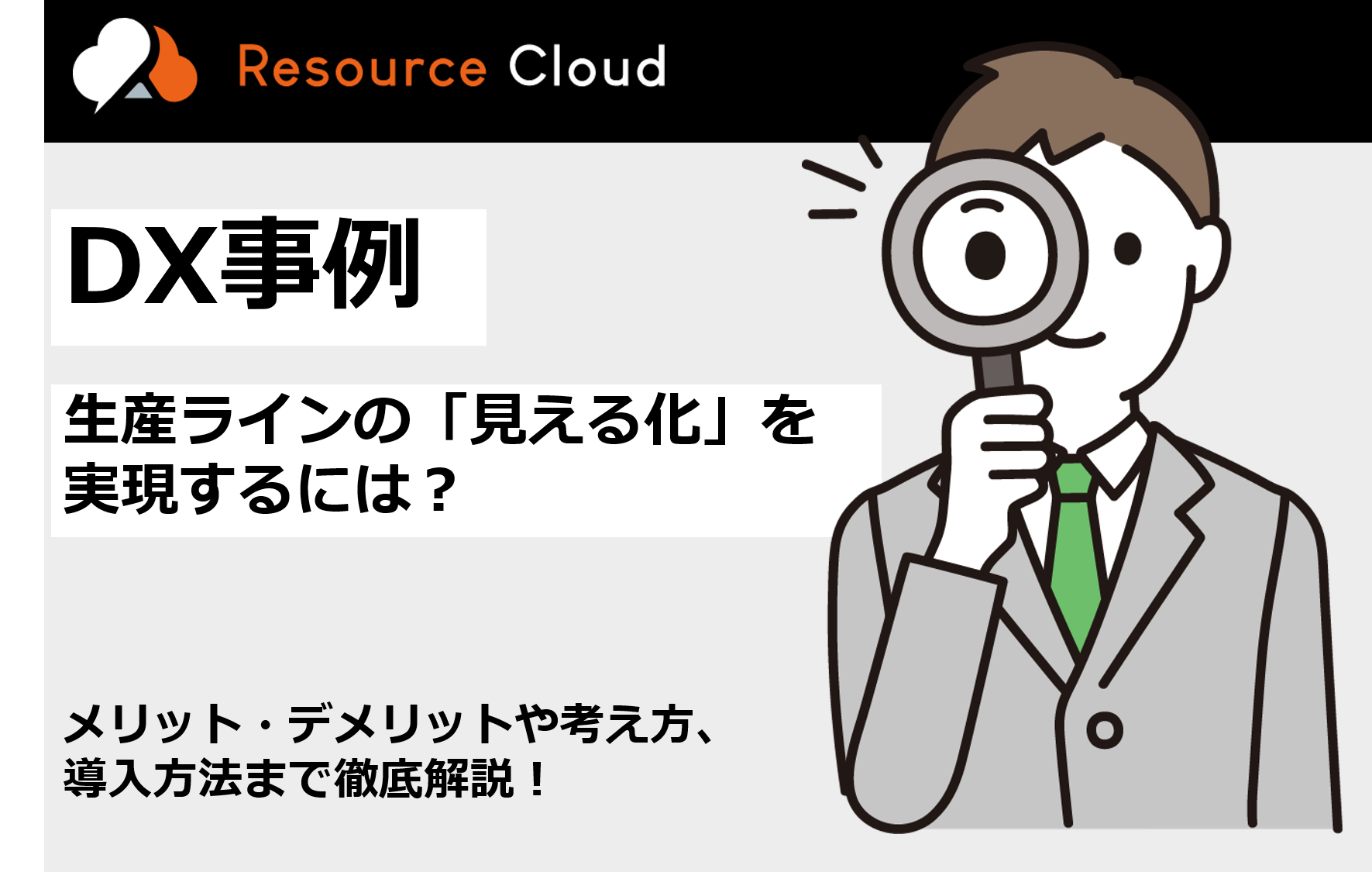
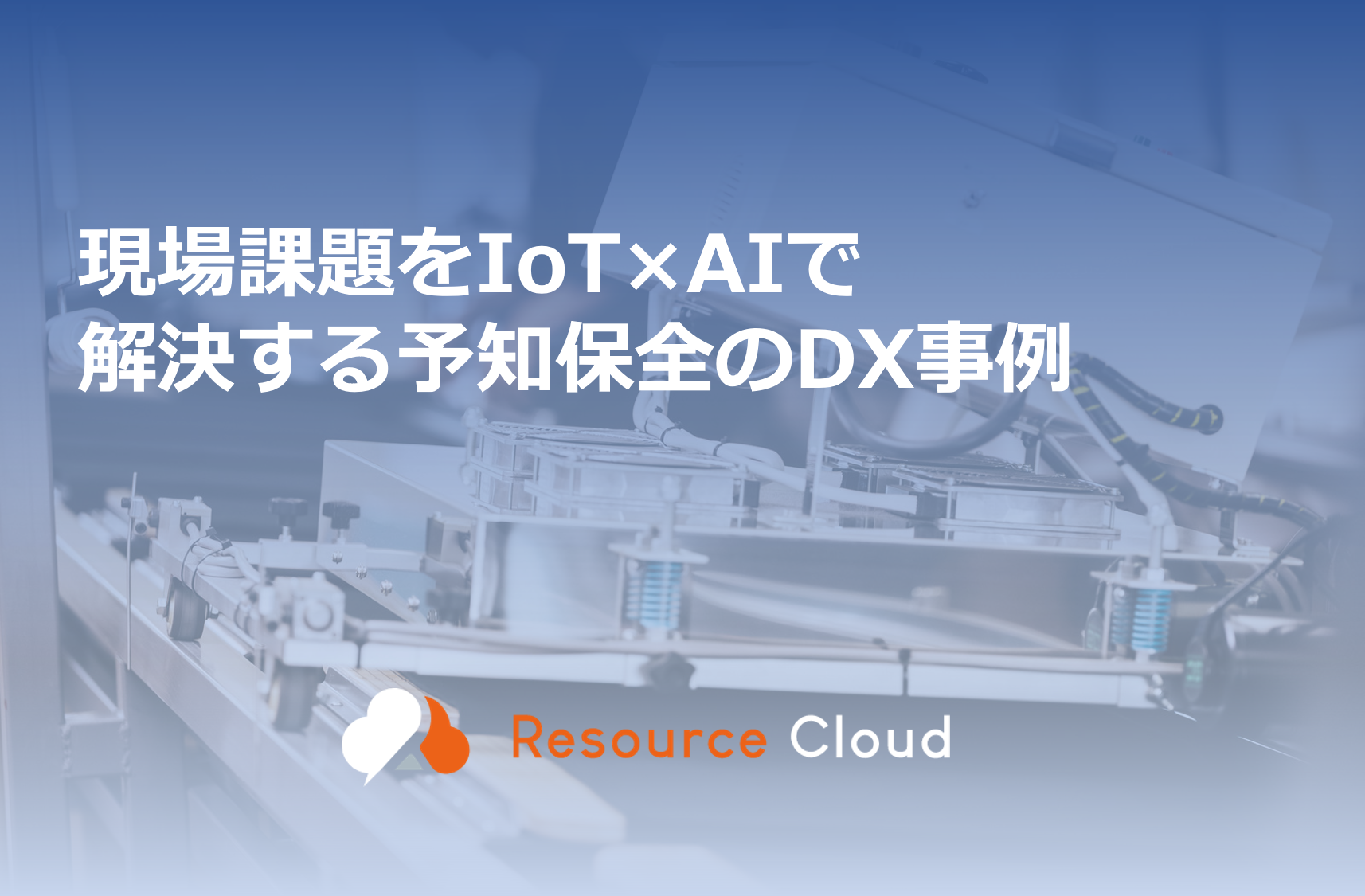
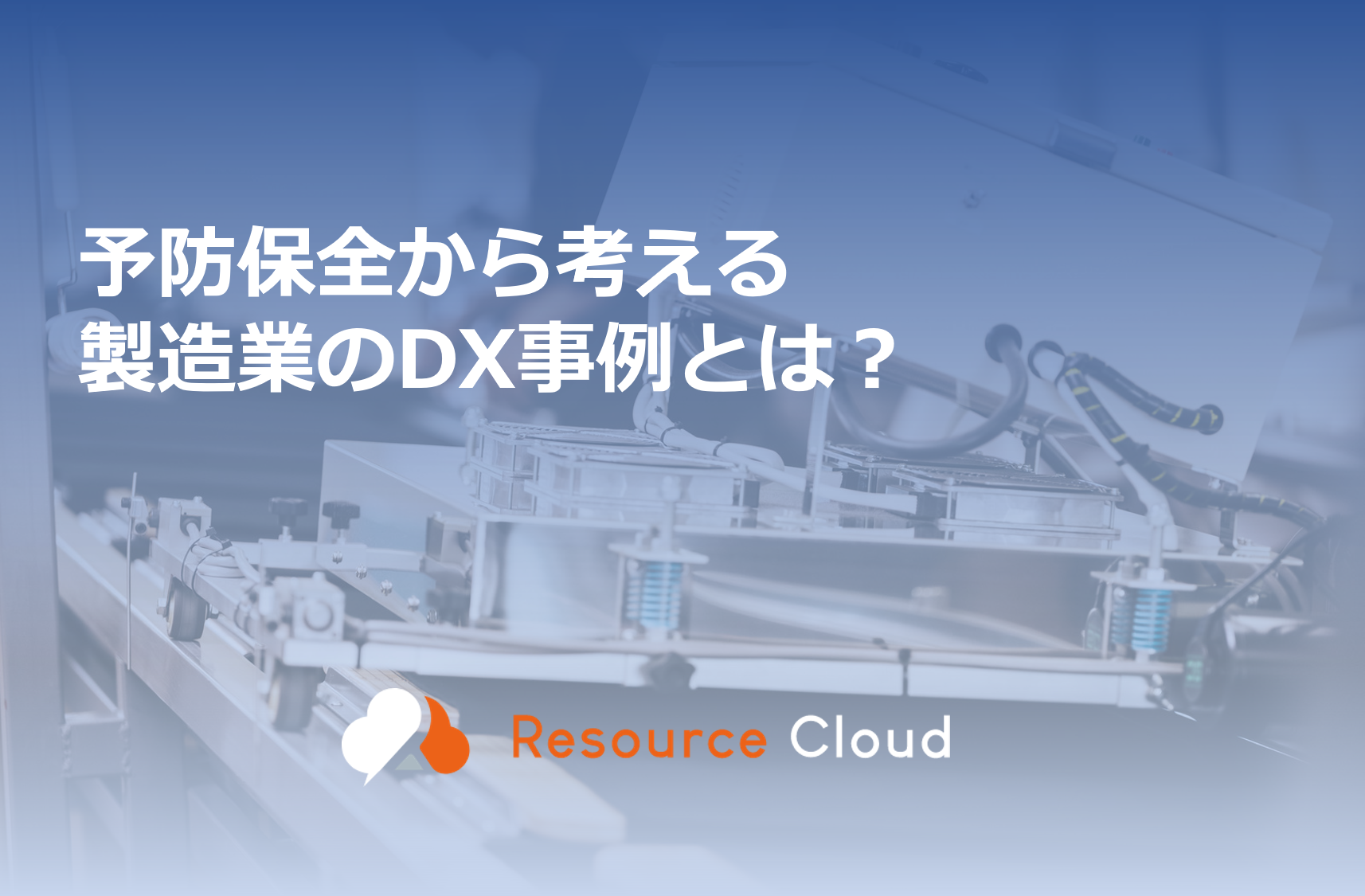
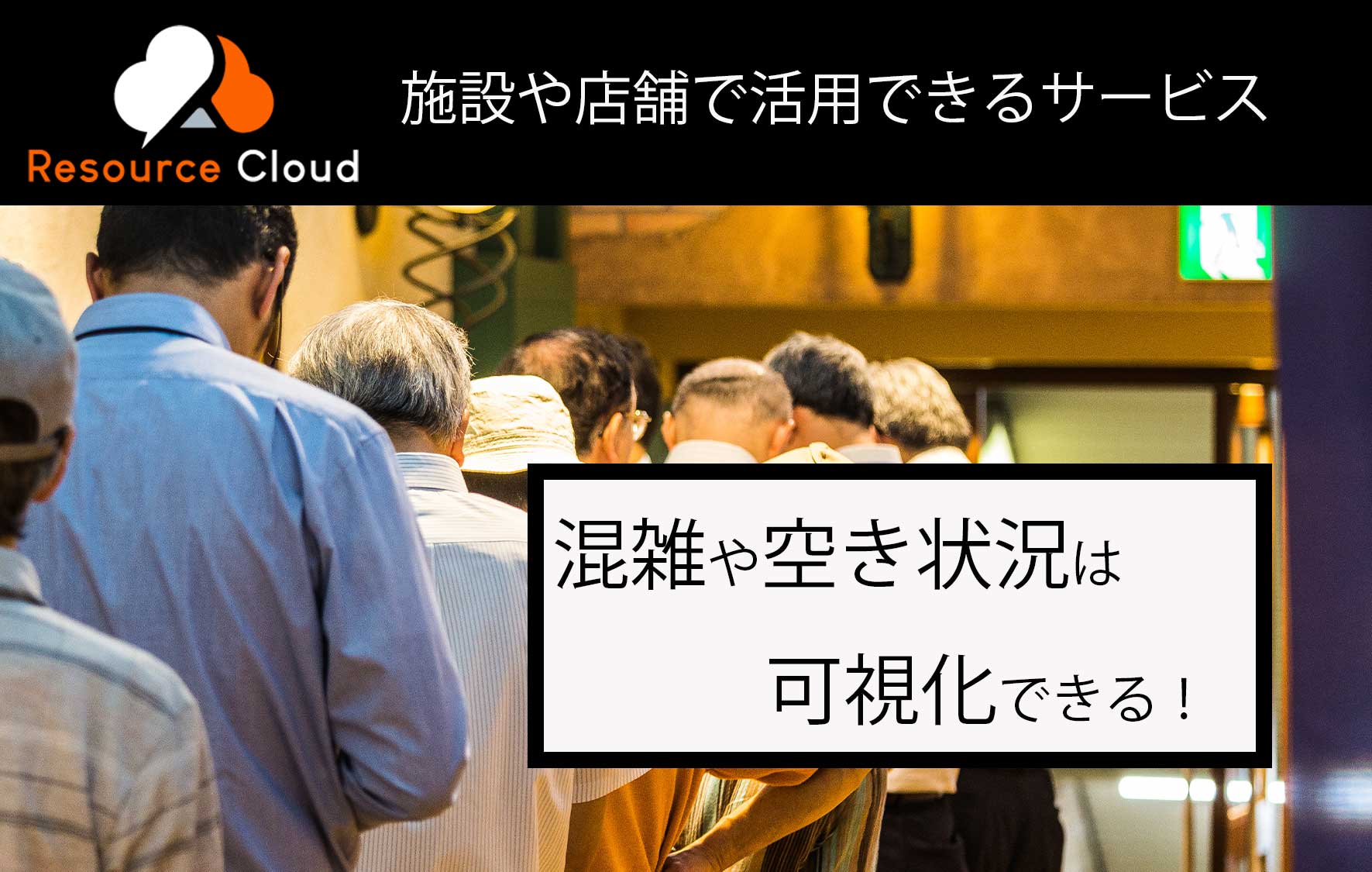
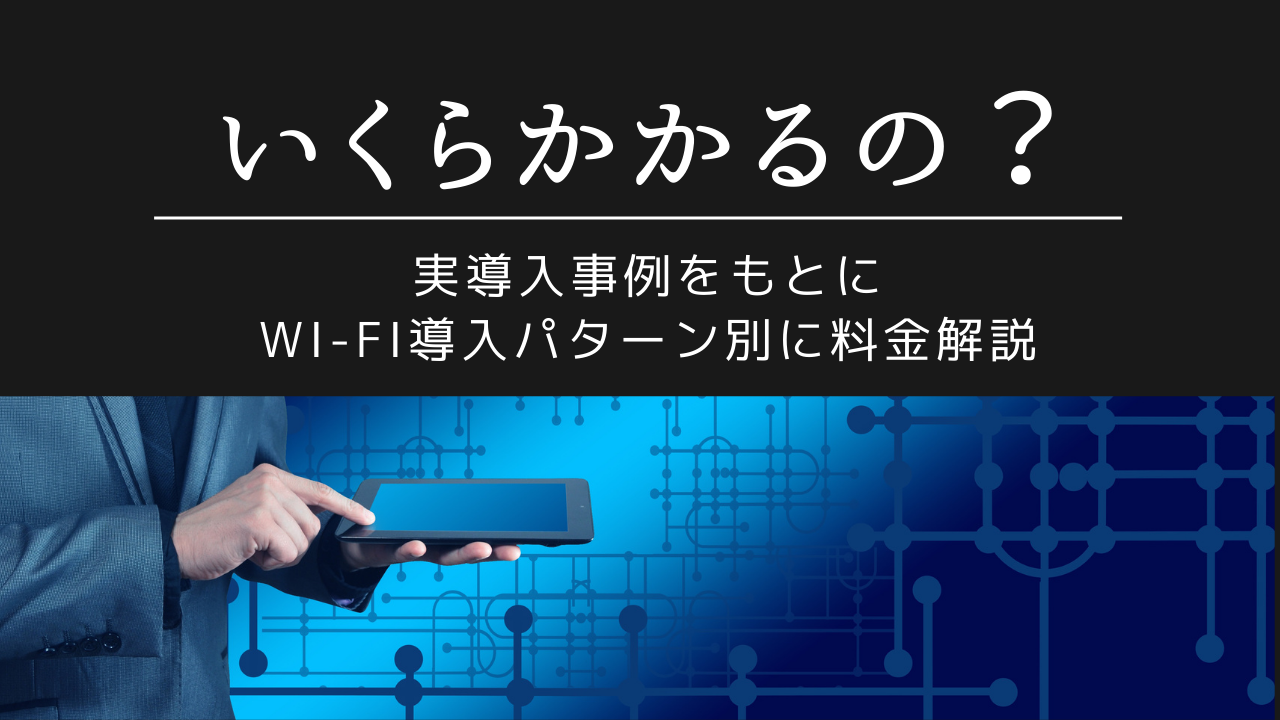
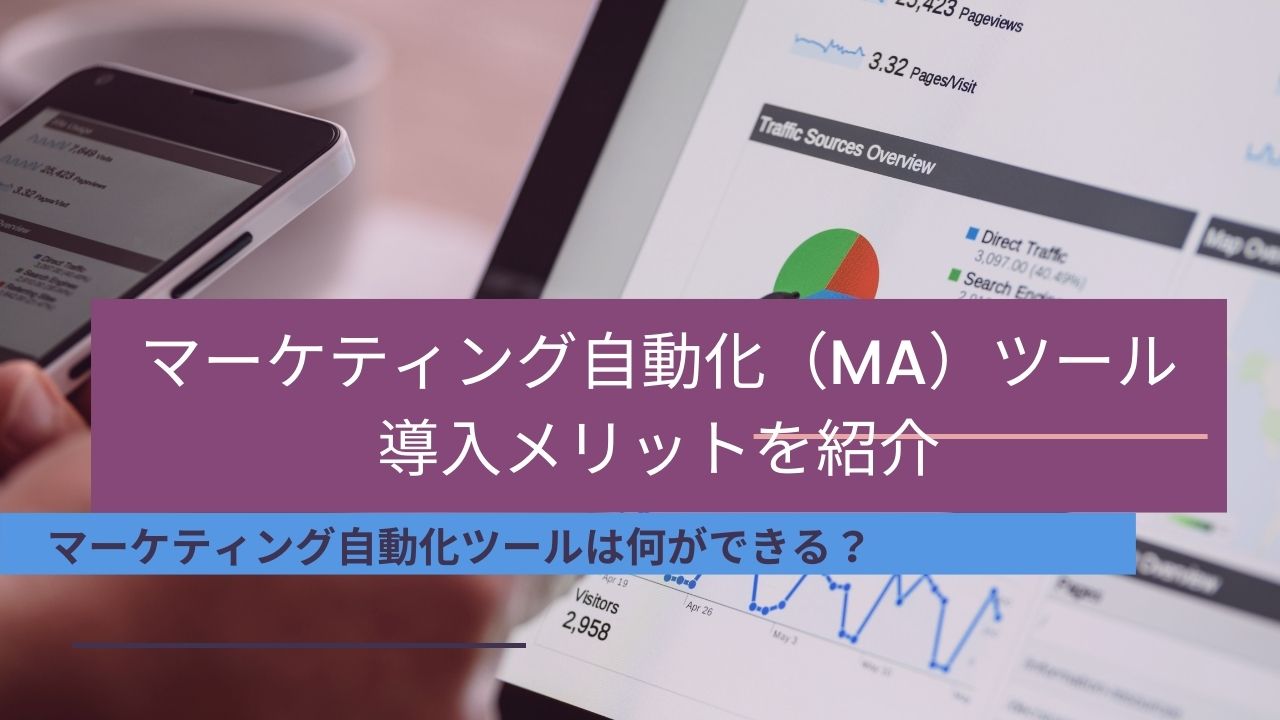
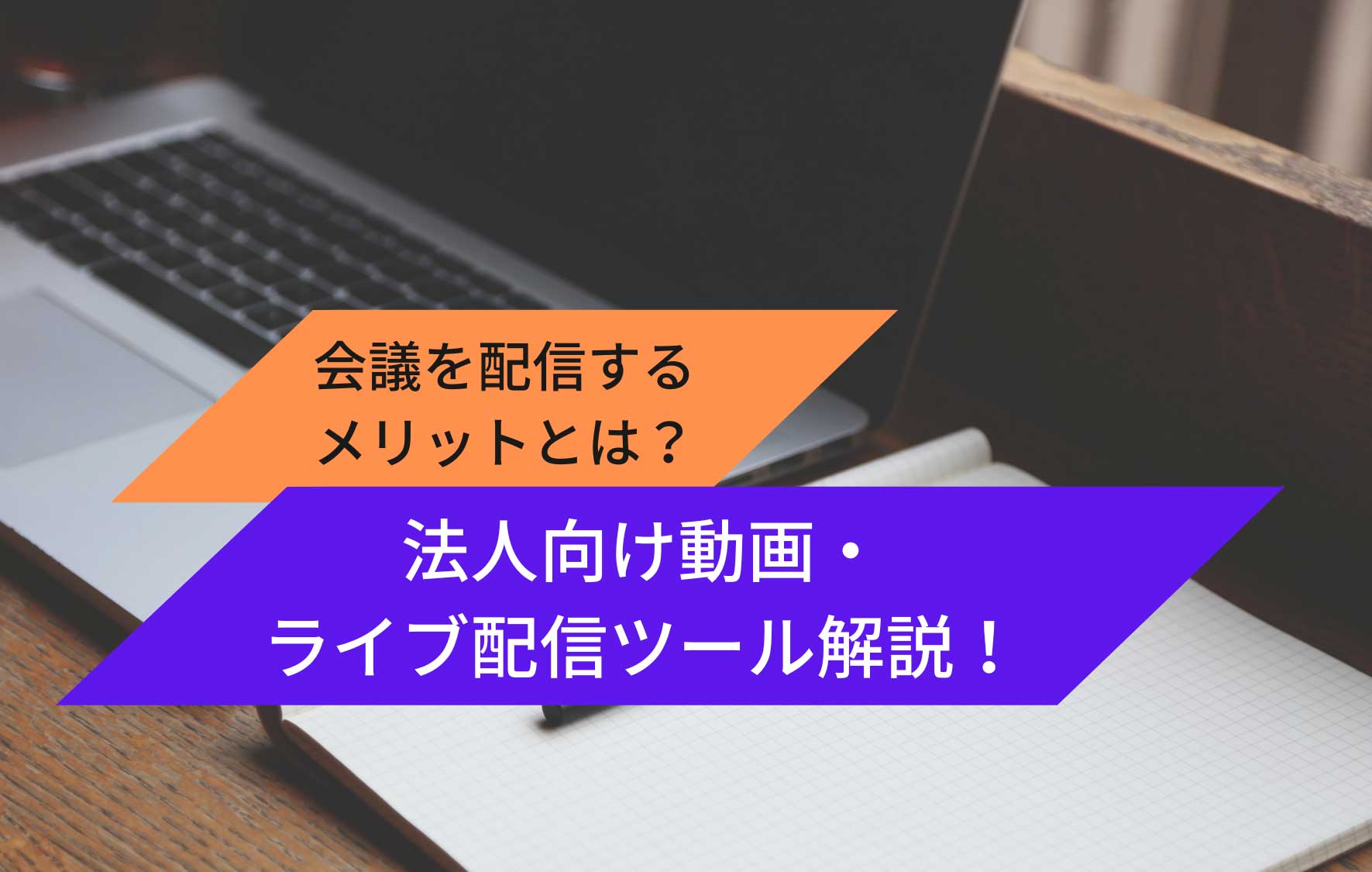
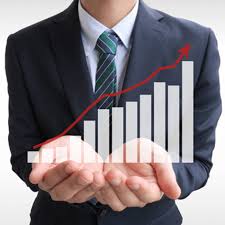
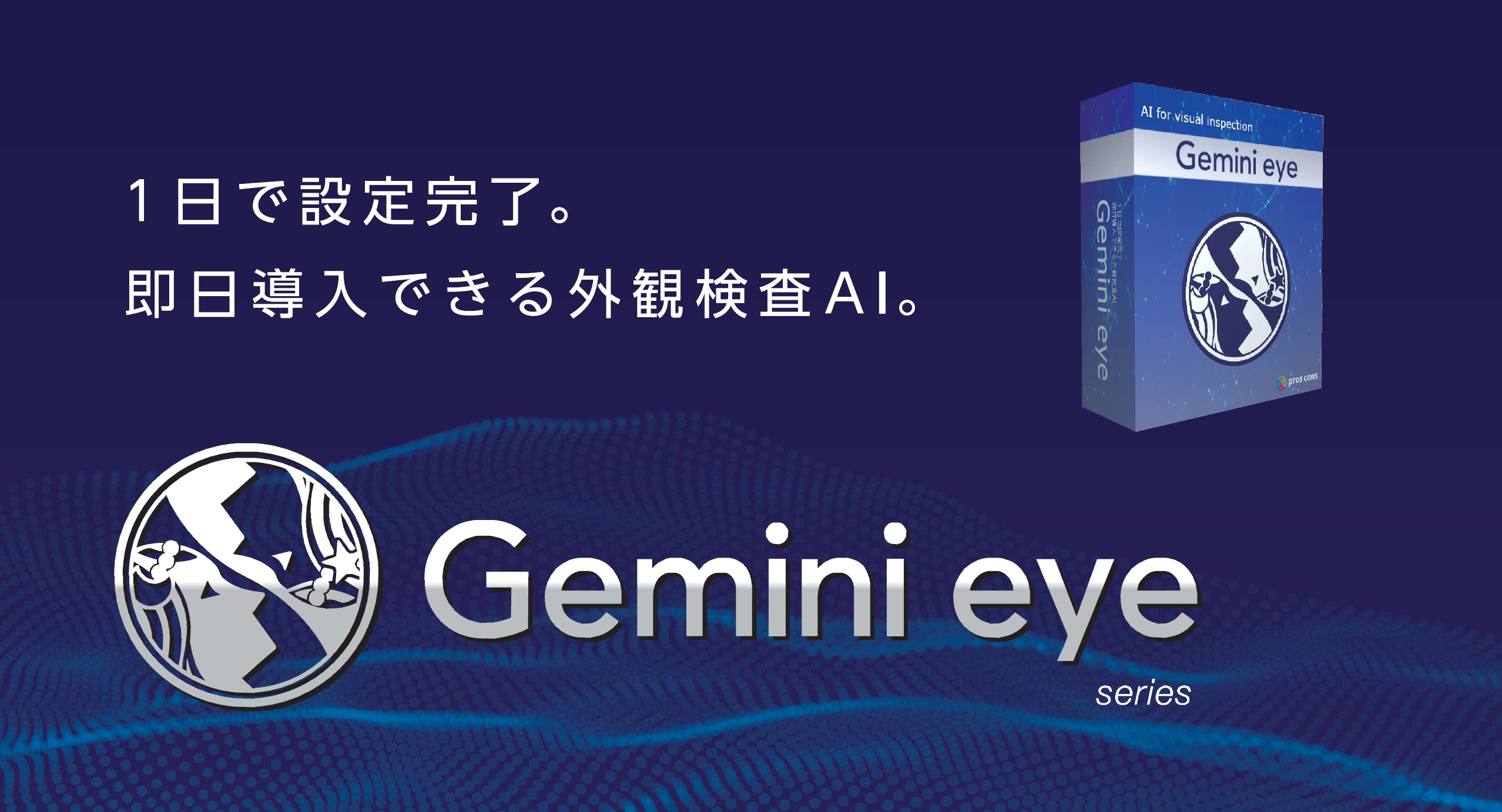
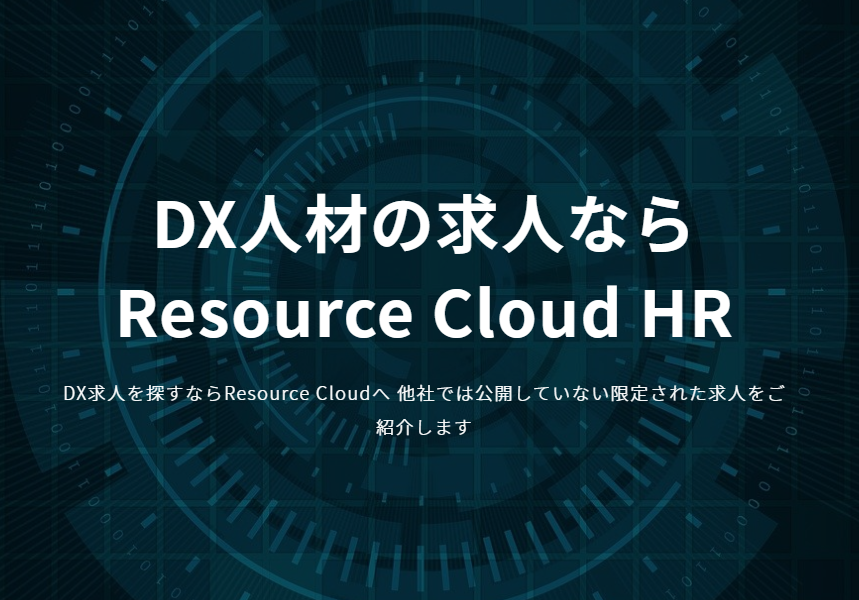
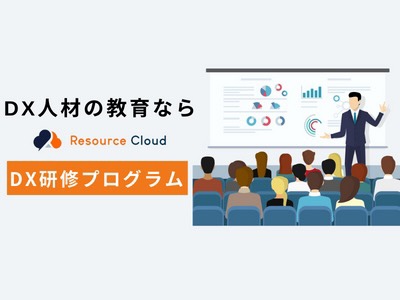
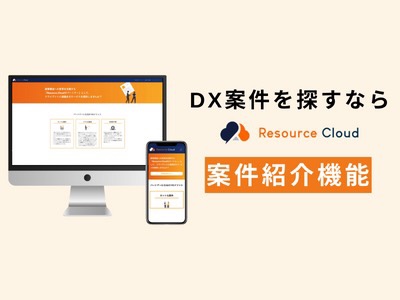