【DX事例紹介】製造業で設備稼働率をモニタリング(見える化)することのメリットとは?
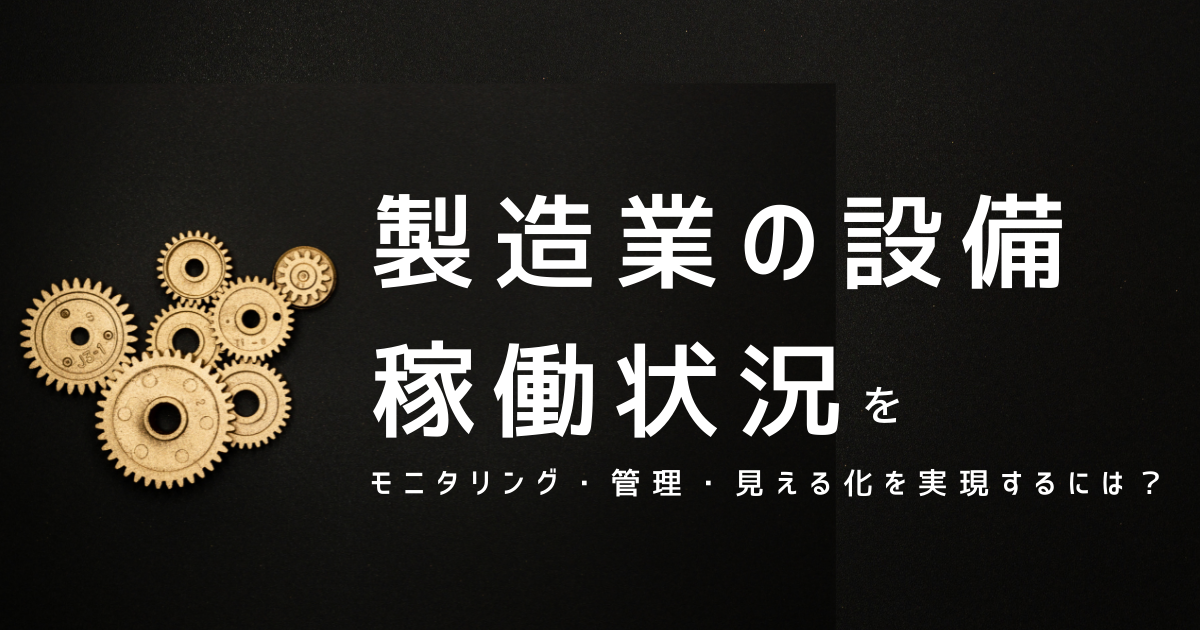
今回は、製造業における設備稼働について解説します。
設備稼働率を悪化させる要因、設備稼働状況をモニタリング・見える化することによるメリットや製造業の設備稼働状況をモニタリング、管理、見える化を実現するためのノウハウをお伝えします。
1.製造業における設備稼働(設備可動)とは
製造業において設備稼働は欠かせません。ここからは設備稼働(率)やその計算方法などについて説明していきます。
1.1設備稼働とは
設備稼働というのは、モノを生産する能力に対する実際の生産量のことです。
製品への需要が高まるとそれを作るための可動率も高まりますが、企業は当然ながらその生産能力を強め、設備投資を行おうとすることから、設備可動率は設備投資の先行指標とされています。また、世界各国で発表されており、先進国では一般的に設備稼働率が80%以上になると設備投資が活発化するといわれています。
つまり、設備稼働率が分からないと、企業としては自社の顧客がどういった製品を必要としているのかがわかりませんので、主観でのみ製品を作っていくことしかできません。
言わば、ゴールのないマラソンコースをひたすら走っている、もしくは、1人相撲をしているというような感じでしょうか。そう考えれば「指標」と言われているのも頷けます。
それほど大切なものであるからこそ、しっかりと設備稼働あるいは設備稼働率を把握しておくことが必要不可欠です。
1.2稼働率と可動率の違い
はじめに、「稼働率」とは、生産能力に対して需要から来る生産の負荷(生産実績)の割合のことで、生産ラインの能力に対してどれくらいの仕事が入っているかの操業率を指します。つまり、現状の設備の実力ではなく、忙しさを示すものであるということです。
例えば、定時までに最大2,000個を作れる設備があると仮定した場合に、注文が最大生産能力の半分1,000個しかなかったとすると、稼働率は1,000台/2,000台で50%となります。
一方、仮に注文数が最大生産能力を超える2,500であれば、稼働率は2,500台/2,000台で125%になります。
この場合、定時までに作れる上限を超えているため、次の日に持ちこしたり、残業や休日操業したりなどの対応をしなければなりません。
次に可動率ですが、可動率とは、機械設備を動かした時に正常に動いた時間の割合を指し、読み方は稼働率との混同を避けるため「べきどうりつ」ともいいます。
例えば、ある設備が通常8時間運転し続けるところ、設備メンテナンスで1時間停止していた場合の可動率は、7時間(8時間-1時間)÷8時間×100=87.5% となります。
このように、可動率とは設備機械の運転効率を表すものであるため、現場が責任を持って向上させるべき指標です。
1.3稼働率・可動率の計算方法
まずは、稼働率の計算方法についてです。
その計算法には、「生産基準」と「時間基準」の2種類があります。
生産基準
生産基準はある意味その名称通り、製品・商品の生産個数を基準に稼働率を計算する方法で、実際に生産した個数(生産実績と言います)を、本来生産できる個数(生産能力と言います)で割るという計算法です。
(例)
・勤務時間8時間/日での生産能力は1,000、その日の生産実績700の場合、
生産能力:1,000
生産実績:700
稼働率 = 700/1,000 = 0.7 = 70%
比較的簡単な方法ですが、それだけに自身が目標をしっかりと達成できたかどうかということが数字ではっきりとわかるというメリットがあります。
それだけに、「前回より生産実績が上がっている、頑張って良かった」「前回より下がっている、次回はもっと頑張らなければ」など、仕事に対するモチベーションを上げたり、今現在の自身の実力を知るのに最適な計算法です。
時間基準
時間基準もその名称通り、時間を基準に稼働率を計算する方法で、実際に稼働した時間を稼働すべき時間で割ることで計算します。
上記の生産基準のように例を出すと、1日に稼働すべき労働時間を8時間とした場合、実際に稼働した時間が6時間だとすれば、6時間/8時間=75%になります。
時間基準も上でご紹介した生産基準と同様、目標が達成できたかどうかが数字ではっきりとわかるため、モチベーションを保つためにはもってこいの方法です。
2.製造業において設備稼働率を悪化させる要因
では次に、その設備稼働率を悪化させる要因となるものは何なのかについて解説していきます。
2.1機械故障・不具合
機械の故障や不具合による可動率悪化は、別名「ドカ停」といい、ロボット軸の異常・ポンプ回転不良・電装機器の不良など、設備の突発的な故障を指します。
突発的なだけに、その原因を探ったり、故障や不具合を起こしている部品を交換するための準備をしなければいけないことから、長時間の故障停止を余儀なくされます。
機械を動かすという時に動きが悪い、まったく動かないとなれば、業務を進められませんし、原因究明や部品の交換・修理依頼などで本来の業務どころではなくなってしまいます。
つまり、業務を根こそぎストップさせてしまう可能性があるものだからこそ、これらは設備稼働率を悪化させてしまう要因のひとつといえるでしょう。
こういった事態を避けるためにも、日頃から機械をはじめとした数々の設備のメンテナンスを欠かさず行うようにしましょう。
2.2部品ロス
部品ロスは、製造に必要な部品が物流トラブルなどで予定通り入荷されないことが原因で引き起こされます。
原料・材料・部品といった製品が入荷されないと何も作業ができません。従来の部品で作業できるかどうかという判断や部品自体の選別もしなければいけないことから、その分時間ロスにもなってしまいます。
当初計画していたものに反することになるため、可動率が悪化してしまう原因となります。
こういったことにならないためにも、万が一に備えて日頃から材料や部品の在庫チェックを欠かさないようにすることが必要だと言えるでしょう。
2.3作業スピード低下
設備の動作スピードやその作業に携わる人員の作業速度が遅くなることで稼働率の悪化に繋がります。
例えば、使用している機械や設備が古いことから動きが鈍いというのは想定内だとしても、その作業を行うのが初めての人や、まだ慣れていない人であれば使い方がわからないということも考えられるため、どうしてもスピードが落ちてしまいます。
これを防ぐためには、経験が浅い人に対してリーダーの方がしっかりとOJT(新人や未経験者に対して、実務を体験させながら仕事を覚えてもらう手法)を含めたレクチャーを行うことが必須となります。
このことから、作業について未経験、または慣れていない従業員がいれば、OJT以外でもできる限りのレクチャーを行い、その方自身のスキルアップを図ることで貴社の重要な戦力にしましょう。
2.4段取り替え
段取り替えとは、生産ラインの製品に合わせて部品の品種や工程などを変更する作業のことをいいます。
段取り替えを行うと、プレスの金型、成形やドリル等の取り替え、精密切削加工や化学装置の基準調整・変更、組立部品や部材の切り替えなど、様々な変更が行われることで稼働率が悪化する可能性があります。
多少の変更であっても作業スピードが落ちるため、段取り替えの工数を見越した準備をしておくとよいでしょう。
3.設備稼働をモニタリング・見える化するメリット
このように、設備稼働率を悪化させる要因は多岐にわたりますが、悪化を防ぐためには、設備稼働をモニタリング・見える化(可視化)することが重要です。
モニタリングをすることで、どのようなメリットがあるのかをご紹介していきます。
3.1故障・不具合を未然に防止
設備稼働をモニタリング・見える化することによって、機械やその部品の故障や不具合を未然に防止することが可能です。これにより、上でご紹介したような設備稼働率を悪化させる要因を作らずに済みます。
日頃からモニタリングを行っていると、「この機械は、ここのボタンの効きが悪い」ということがひと目でわかるため、前もって何かしらの対策ができます。
消費者の方の手にわたってからも、貴社の製品は壊れにくくて使いやすいという評価をいただけるのはほぼ間違いありません。
3.2故障・不具合の要因分析ができる
設備稼働をモニタリング・見える化することで故障や不具合の未然防止はもちろんのこと、それについての要因分析も容易にできるようになります。
例えば、「この機械はここが悪くて故障した、不具合を起こした」というようにわかります。モニタリング・見える化がしっかりとできていなければ、故障や不具合といったアクシデントが起こった場合に、どうしたらよいのか判らず「どうなっているのか」と右往左往するだけになってしまいます。
そうならないためにも、設備稼働をモニタリング・見える化することが大切です。
こうすることによって、万が一消費者の方から「貴社で購入した〇〇が壊れてしまったのですが」という問い合わせがあった場合でも、変に慌てることなく速やかに要因究明をすることが可能となります。
消費者の方からの信用・信頼のためにも、モニタリング・見える化は必須です。
3.3生産プロセスの効率化
設備稼働をモニタリング・見える化すると、当然ながら生産プロセスの効率が格段に上がります。また、それによって従業員の方はもちろん、工場全体のモチベーション向上にもなるため一石二鳥です。
人間というのはとても単純な生き物なため、物事がなかなかうまくいかない時にはイライラしてしますが、逆にうまく進んでいる時はその勢いに任せて猪突猛進してしまうものなので、そういう意味では、このメリットは人間のそういった心理をうまくついているということになります。
もちろんそれだけではなく、これにより従業員の方々の気持ちが十二分に込められたより良い製品が作られることにもつながるため、常にモチベーションが高く仕事に取り組めるようモニタリング・見える化をぜひ実施してみてください。
4.IoT、稼働管理システムで製造業の設備稼働率を効率化
IoTという技術を使うことで、設備稼働率を管理でき、製造の効率化を図ることができますが、IoTのことを知らない・もしくは「知ってはいるものの、あまり詳しくない」という方にも納得していただけるように解説をしていきます。
4.1IoTと製造業
IoTというのは「Internet of Things」の略で、モノに通信機能を搭載してインターネットに接続・連携させる技術のことです。
その一例をご紹介すると、パソコンやスマートフォンをはじめ、プリンター、据え置き型ゲーム機など、これまでインターネットに接続されていたIT機器以外にも、テレビや冷蔵庫、エアコン、時計、自動車などのアナログ機器もデジタル化し、インターネットに接続することでデータの連携が可能となっています。
流れを説明すると、まずモノからセンサーでデータを取得し、インターネットで送信→集めたデータをビッグデータとしてクラウド上のサーバストレージに蓄積→そのデータをAIで分析し、必要な情報としてデジタル化を行います。
Iotを製造業に活用することで、当然ながら生産性や品質の向上はもちろん、コストの削減、社員の質の向上などさまざまなメリットや効果が見込めます。さらに、活用時のポイントとして、
・苦手意識を持たない
・取り入れることで解決したい問題は何かを見極める
・社員全員がIoTを使えるような仕組みを作る
上記3点を特に意識して導入していきましょう。
これらの対策を行った上で活用することで、貴社の生産性や品質は現在よりもさらに良くなり、飛躍的に向上することでしょう。
5.おすすめの設備稼働管理システムを紹介
設備稼働状況をモニタリング・見える化することで、それまでとは比較にならないほど向上する効率と状況の把握が可能です。
品質を上げるためにも、ぜひ取り入れることをおすすめします。
その一例として、製造ライン監視IoTキットがあります。
5.1製造ライン監視IoTキット
株式会社インフォコーパスが提供する「My First IoT シリーズ ~製造ライン監視IoTキット~」は、機械の古い・新しいを問わず、簡単かつ素早く接続できる(センサー取り付けから稼働開始まで30分ほど)ほか、価格も25,000円~とコストパフォーマンスも抜群のキットです。
取得したデータはクラウド上のプラットフォームへ保存され、稼働状況を把握するだけでなく、管理、分析を効率化することができます。また、クラウドシステムであるため、ネット環境があればどこでもデータを確認することができます。
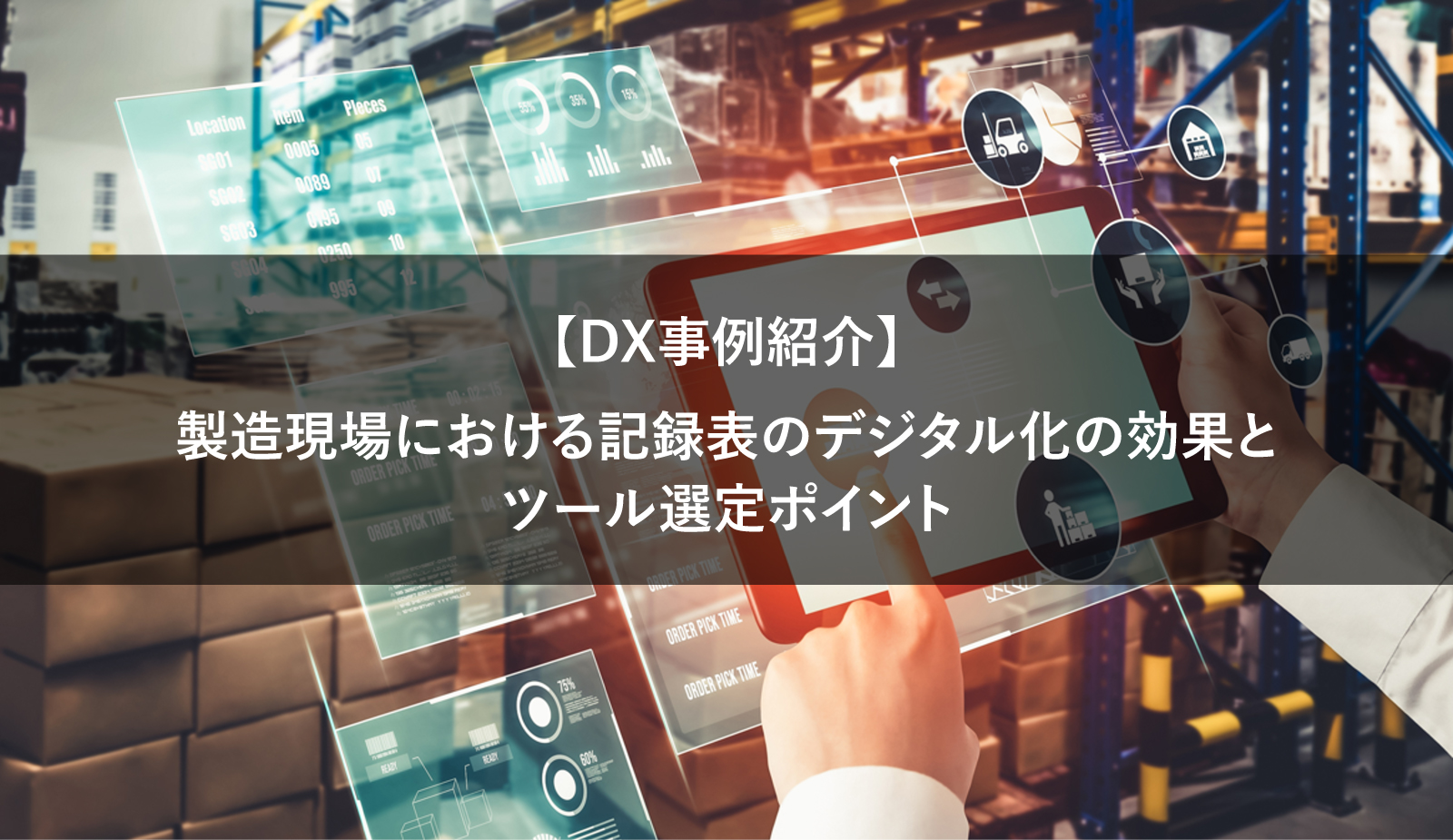
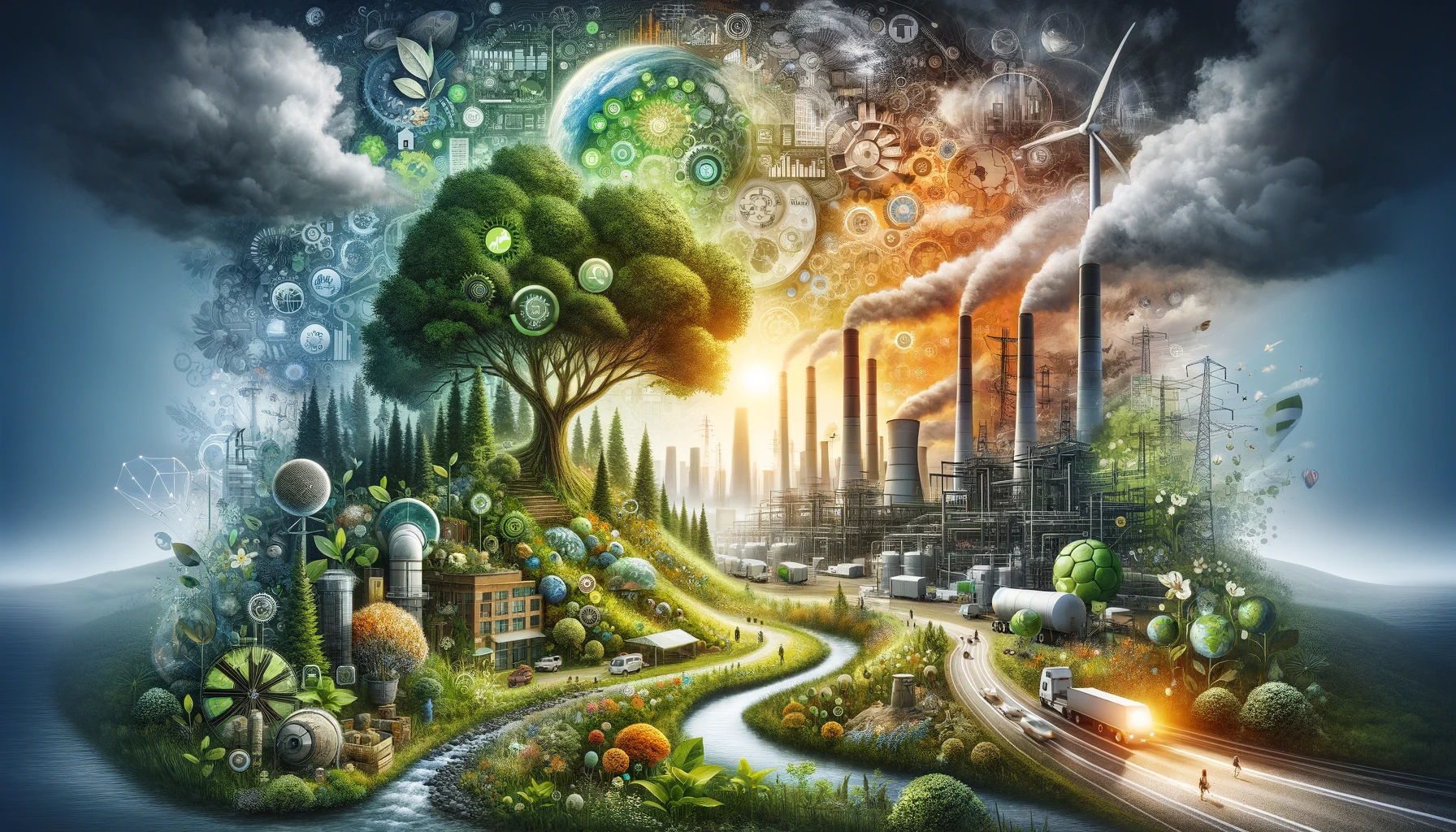
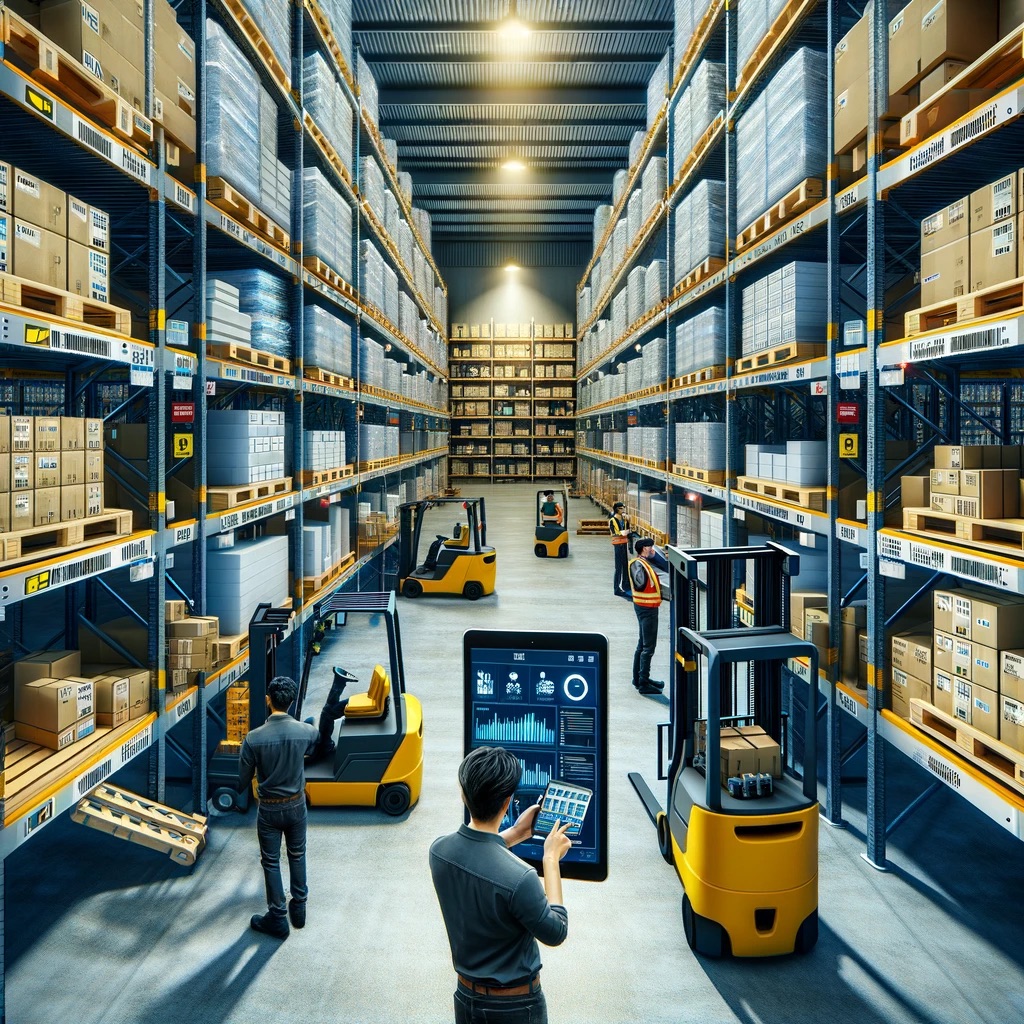
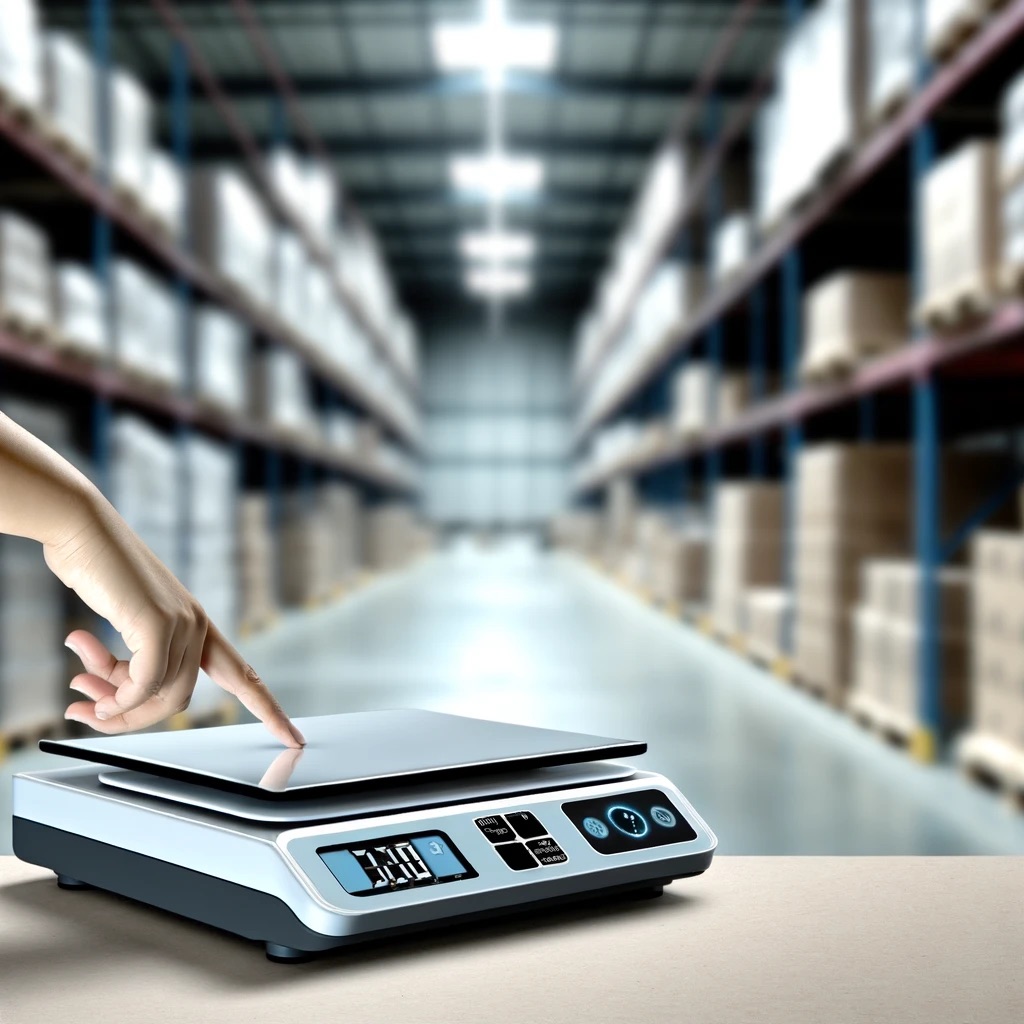
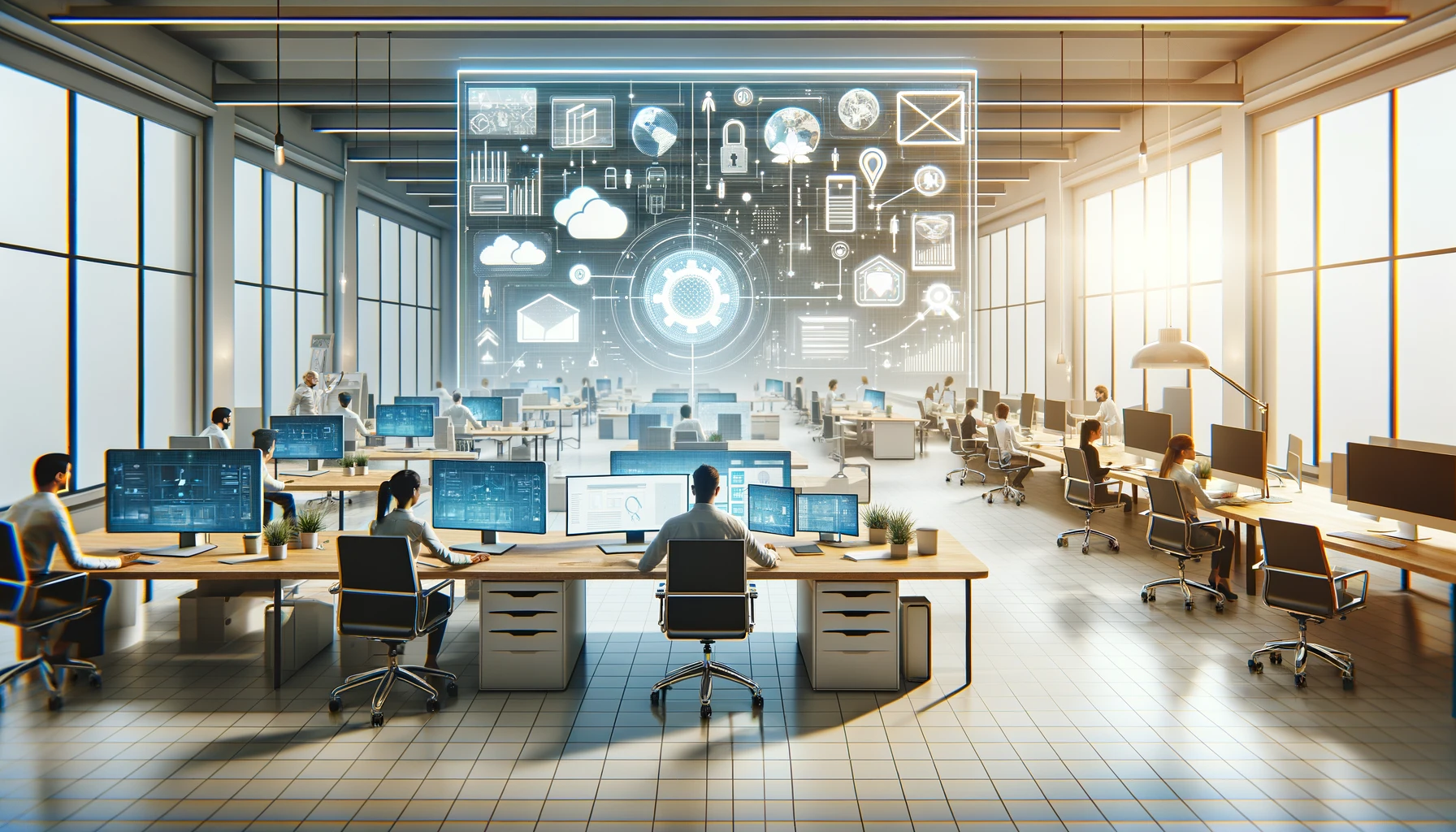
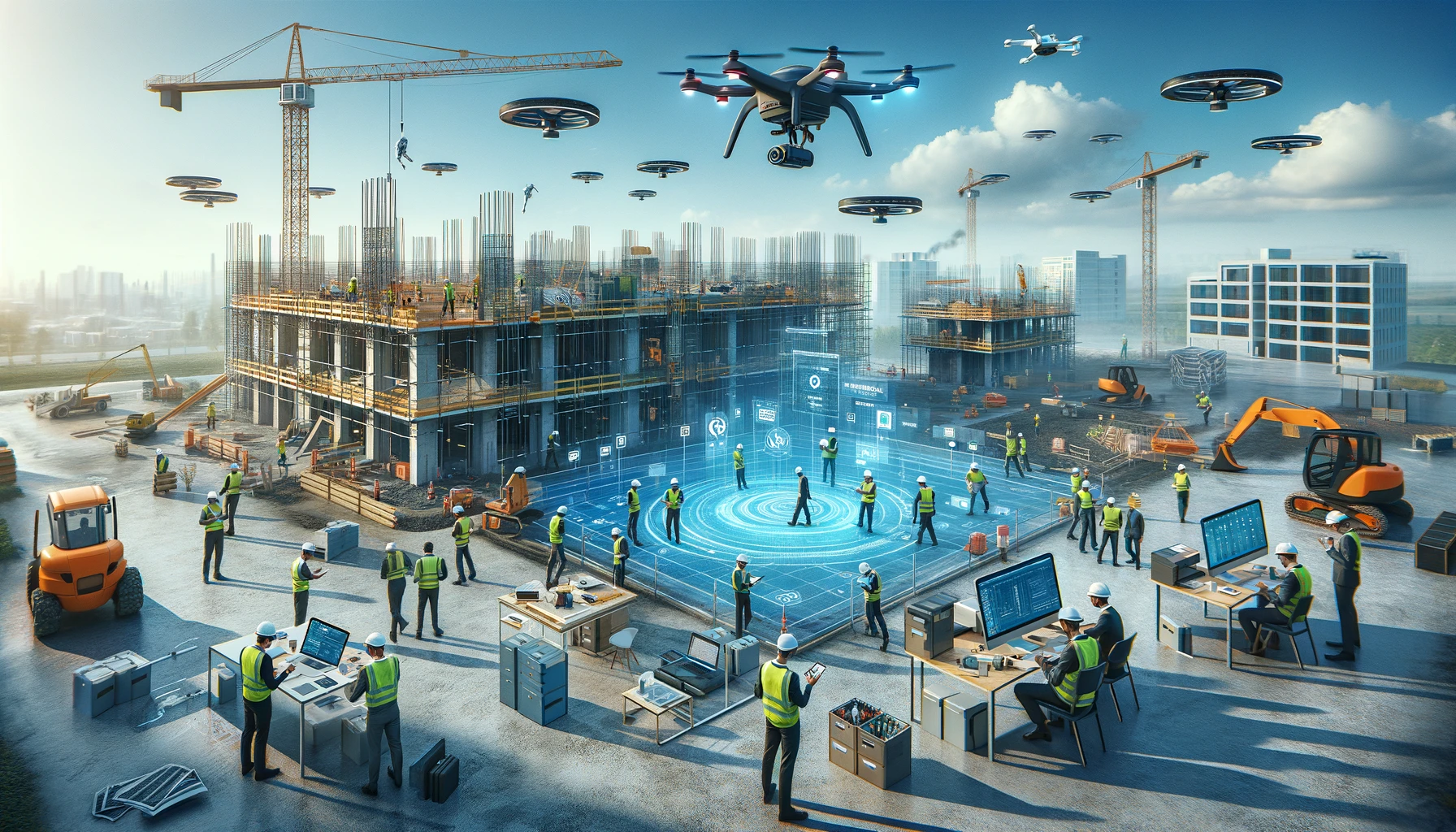
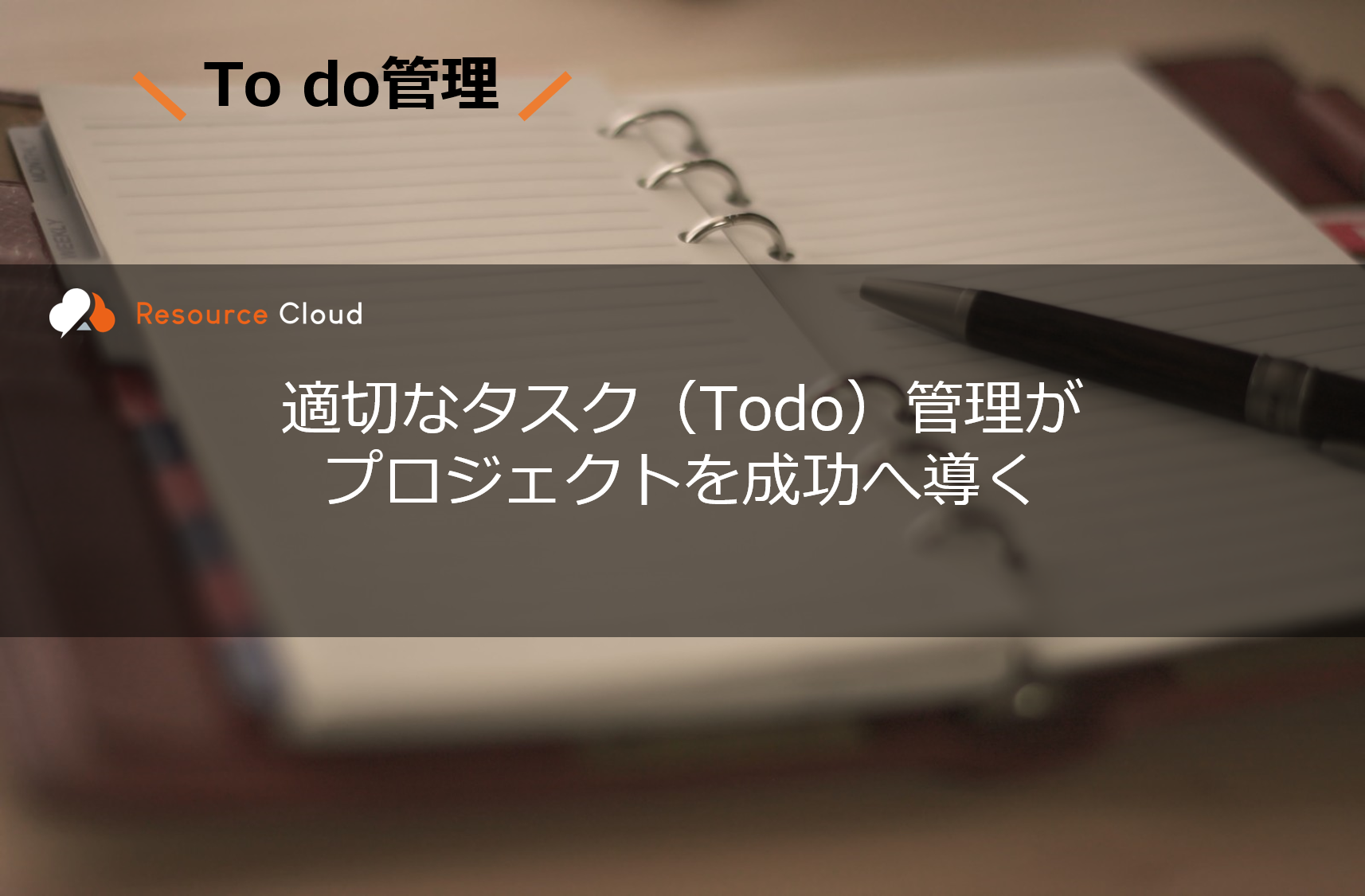

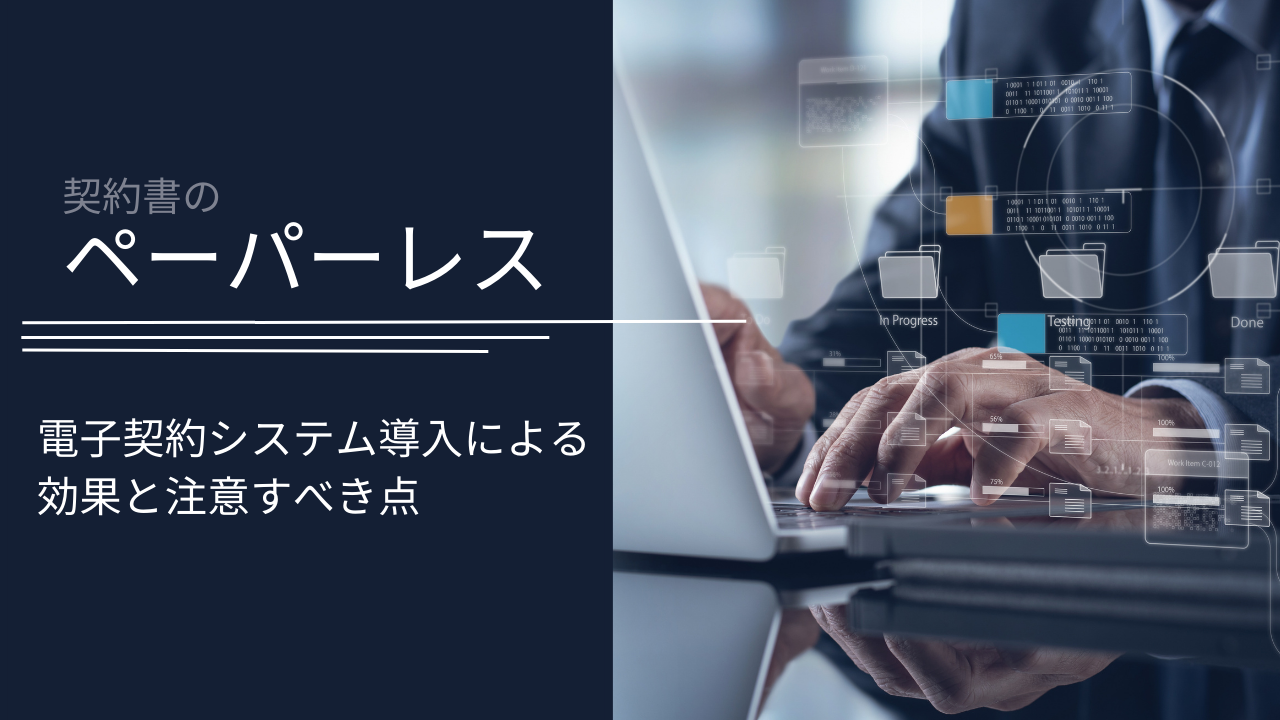
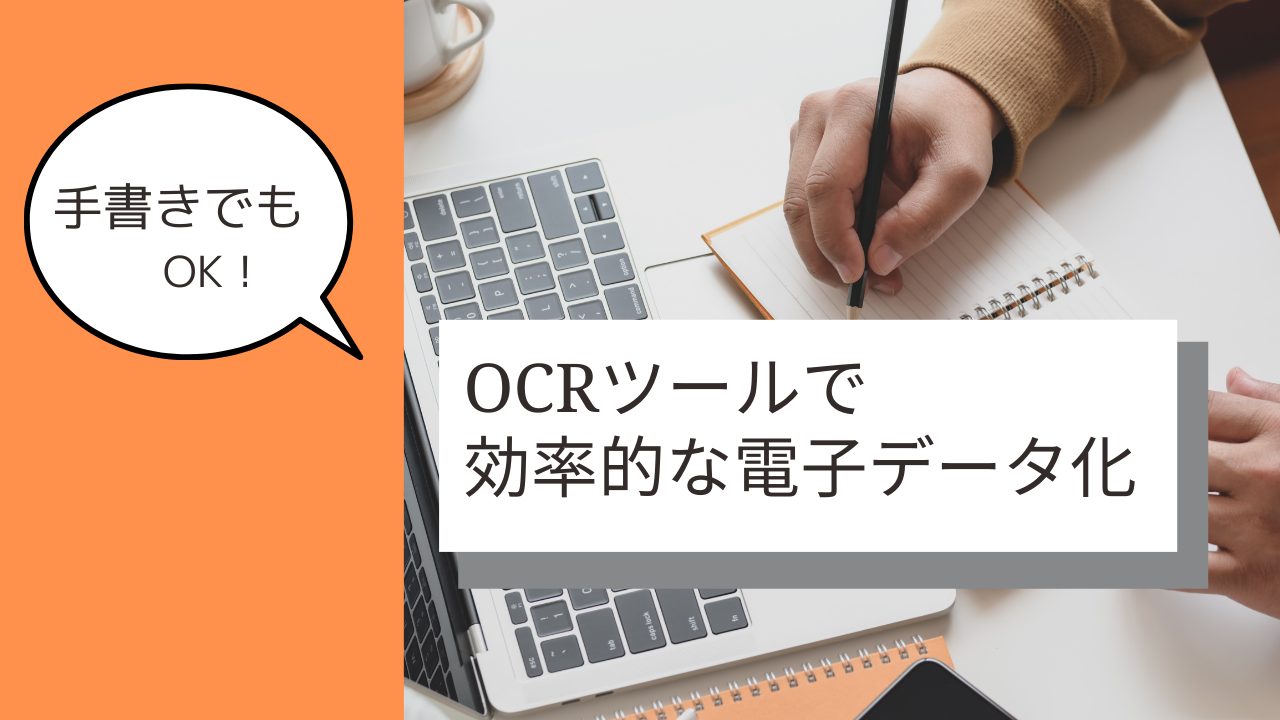
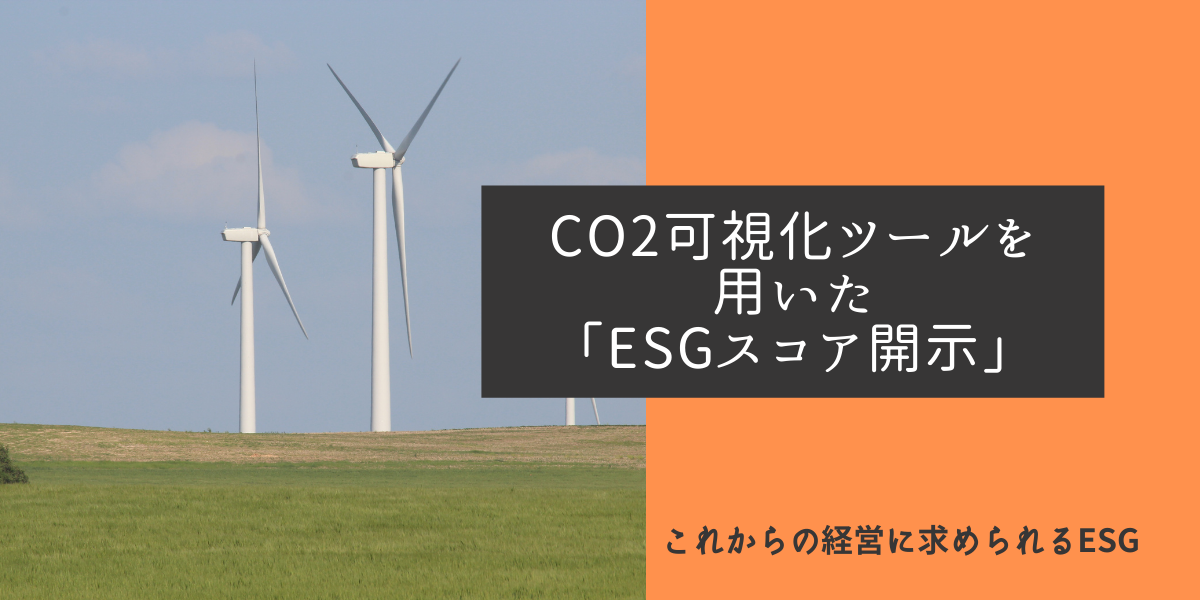
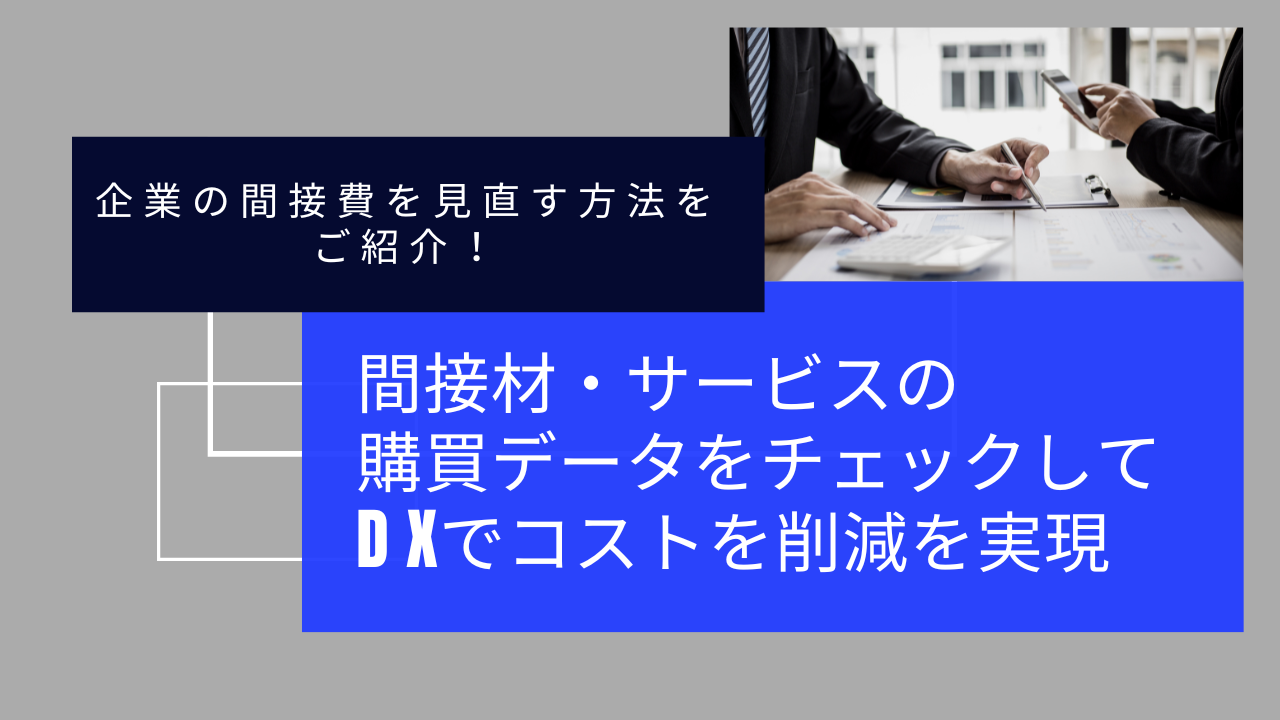
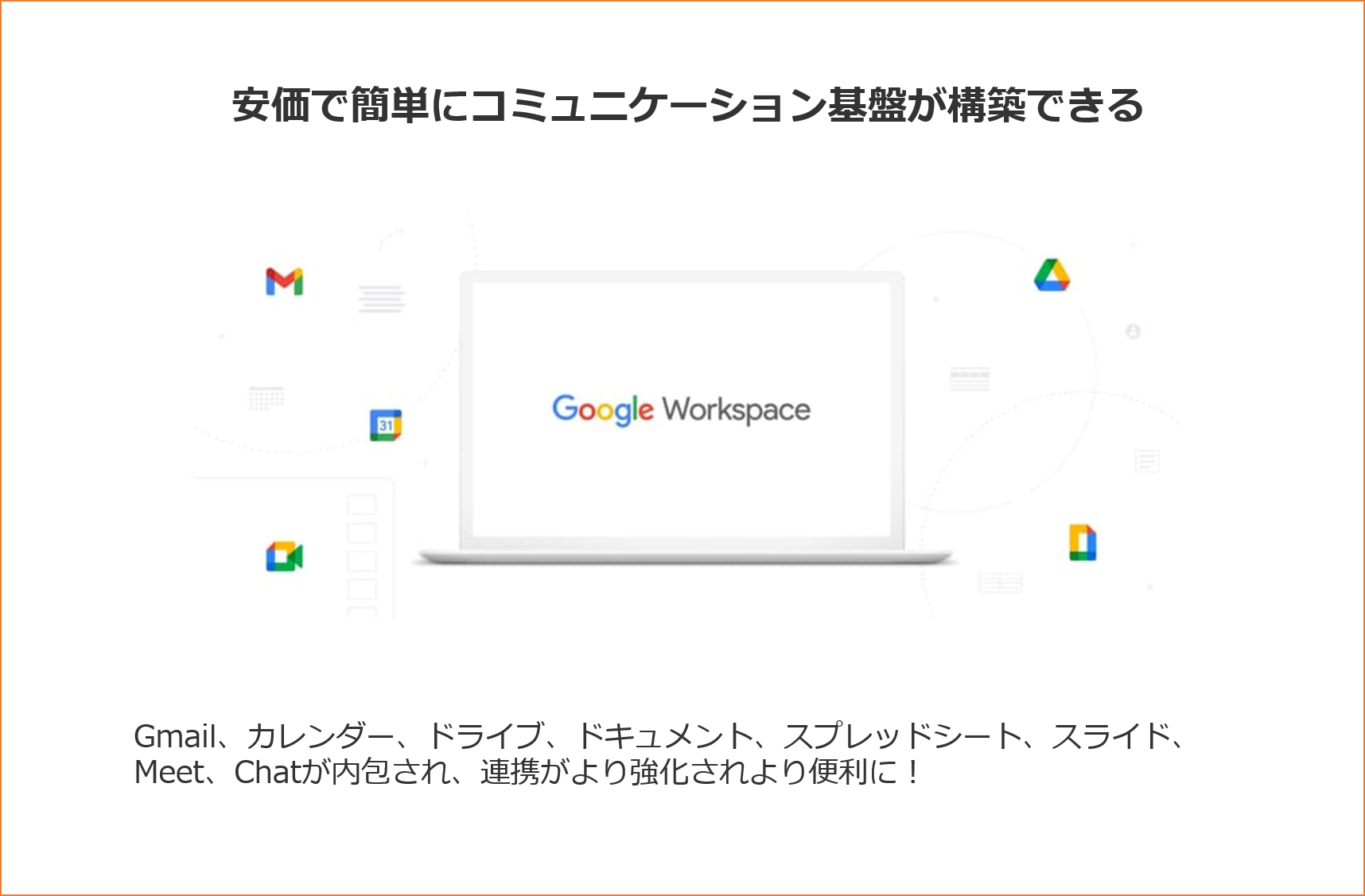
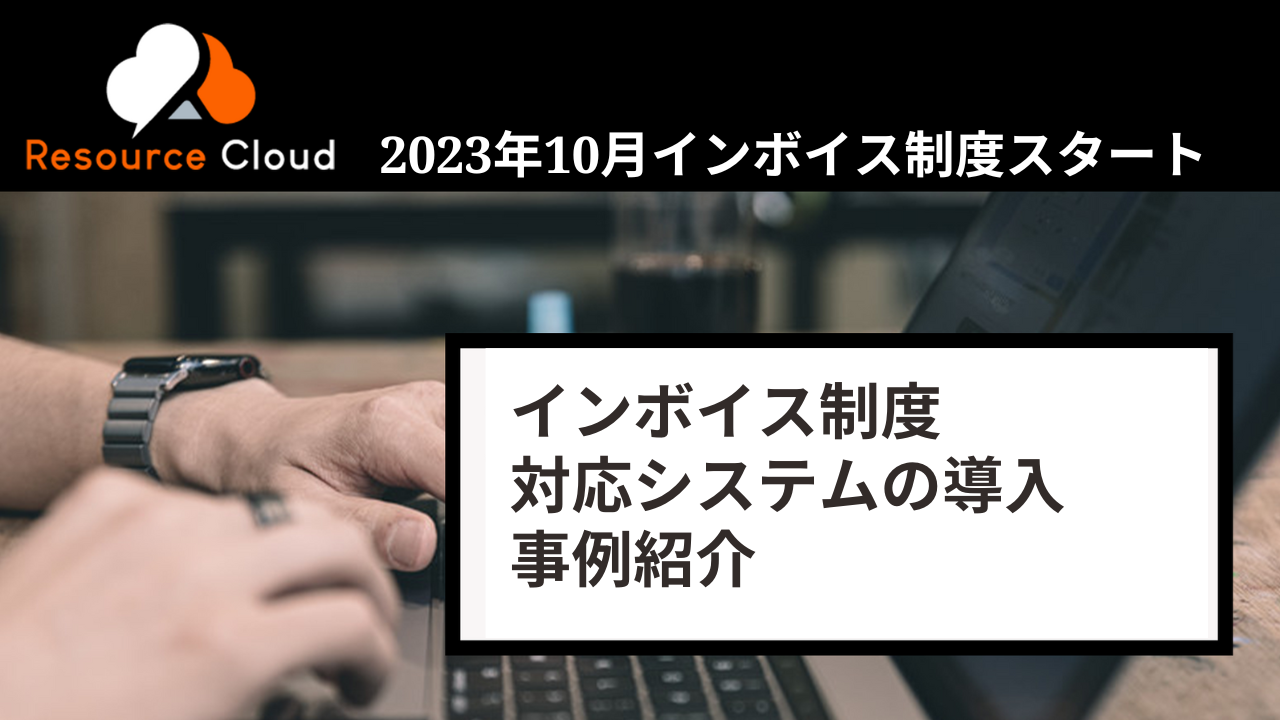
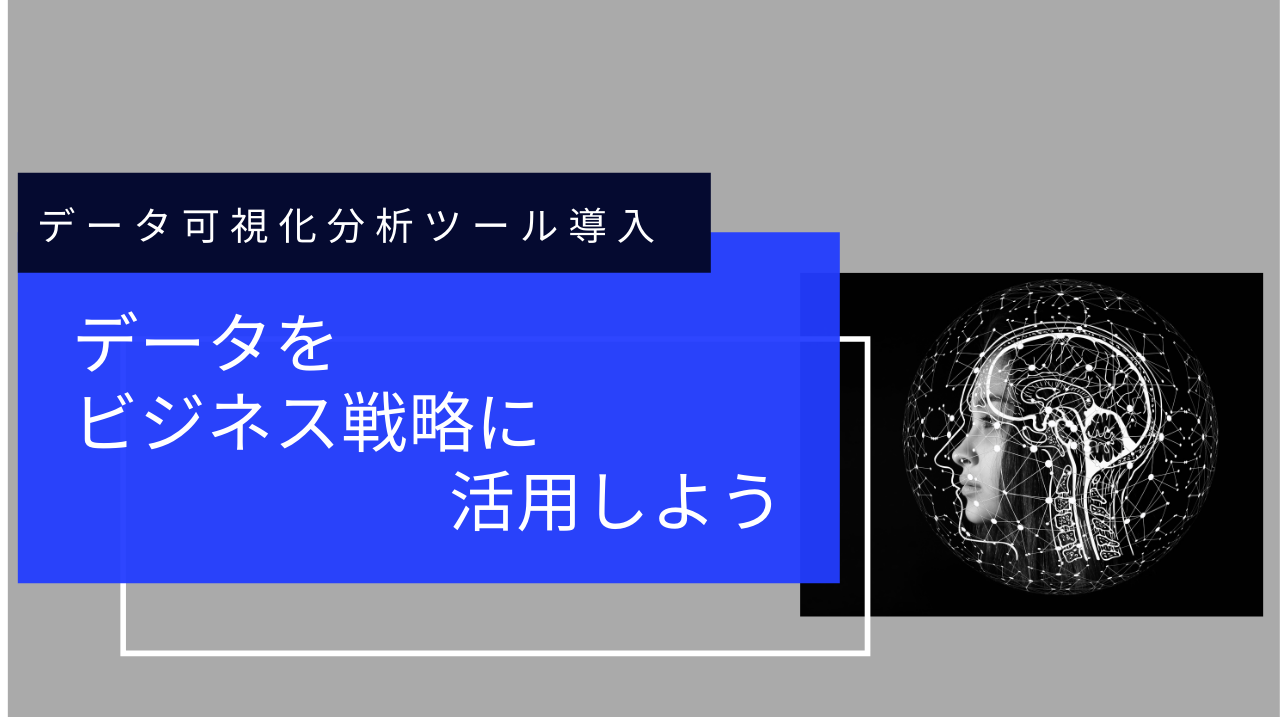
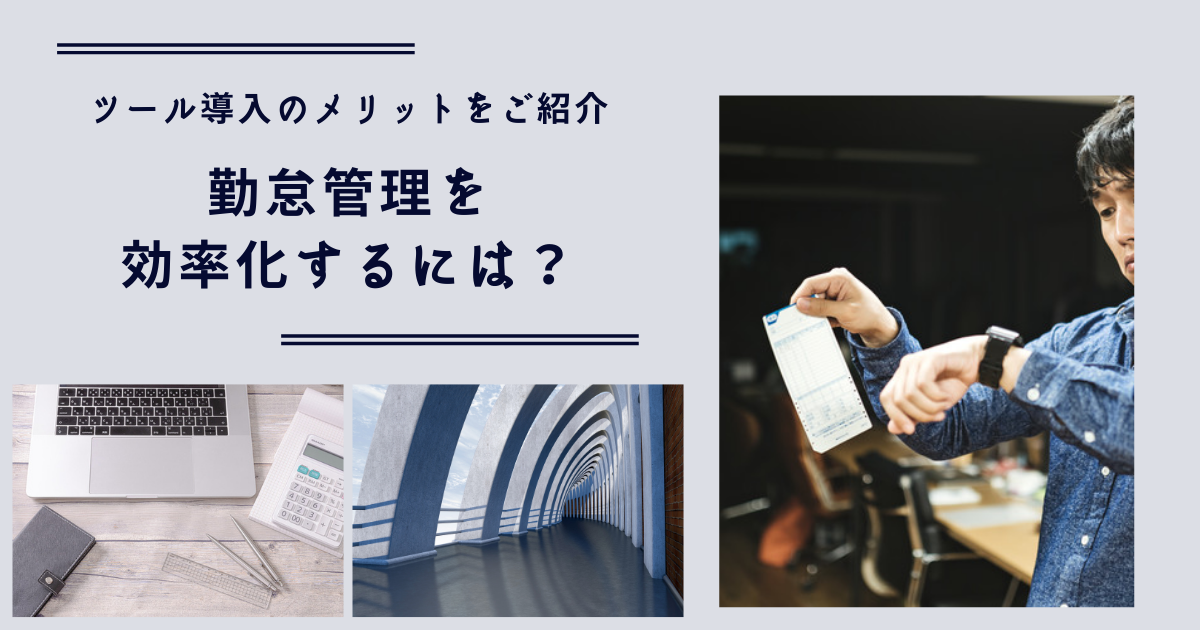
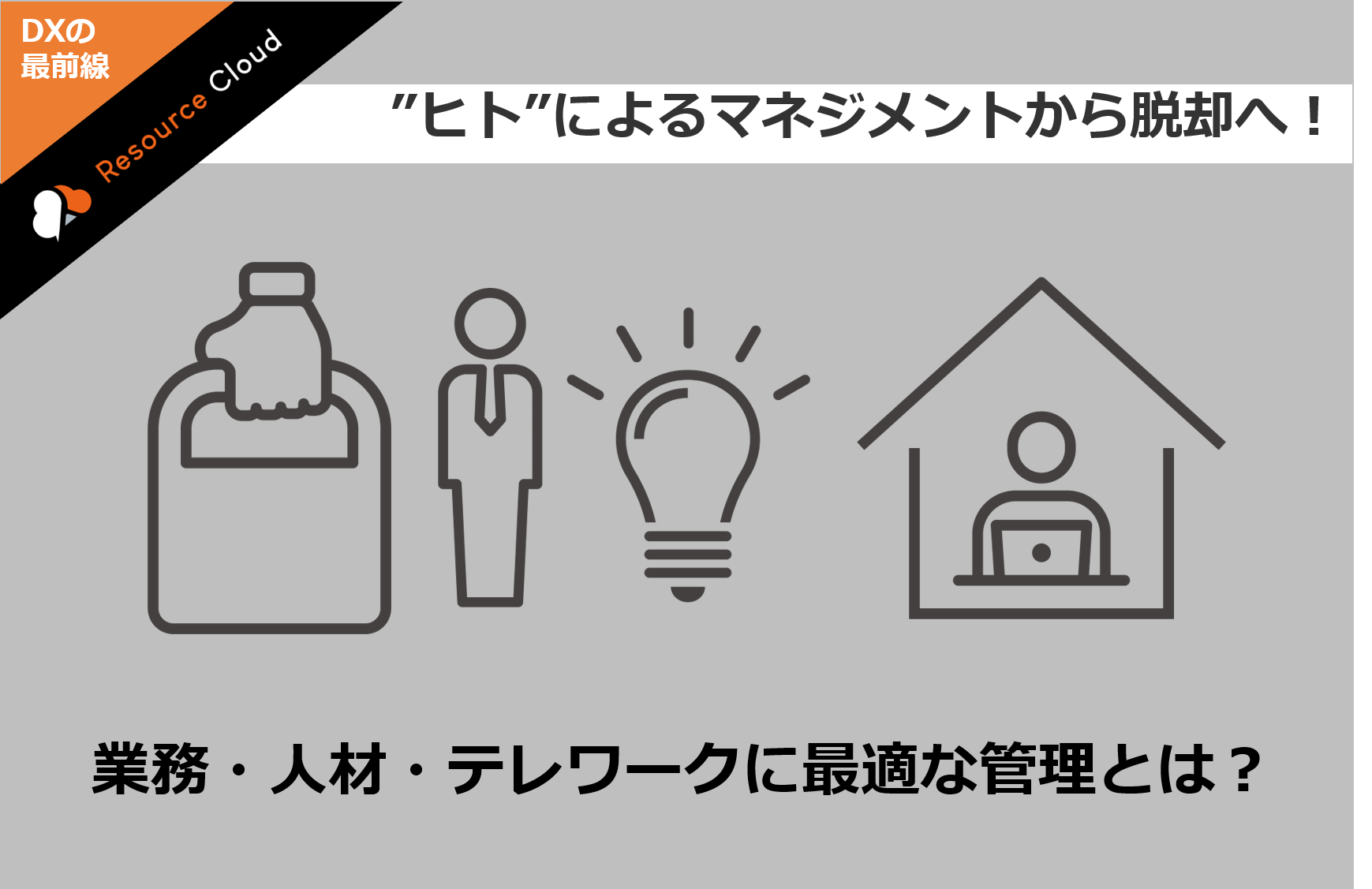
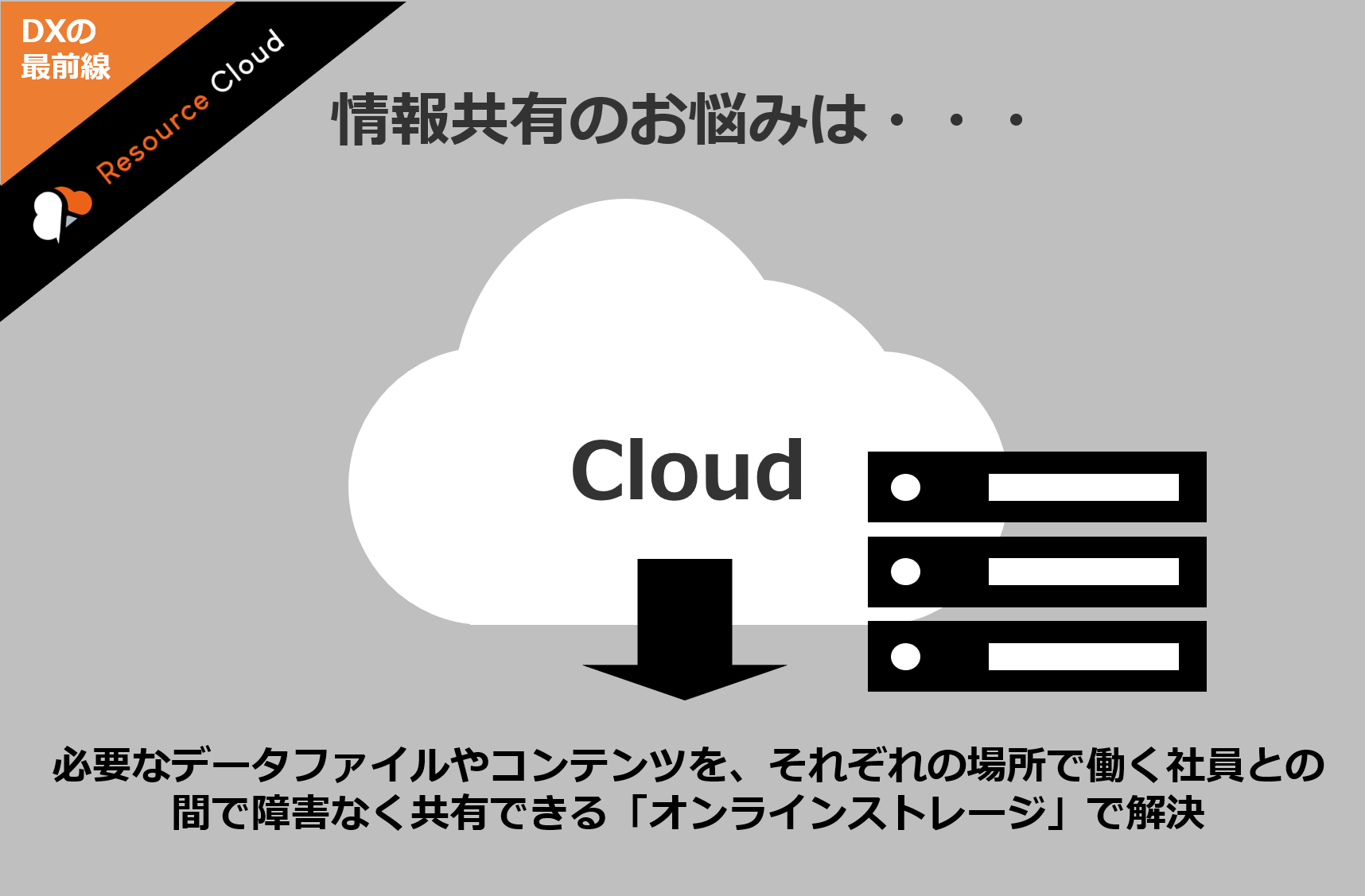
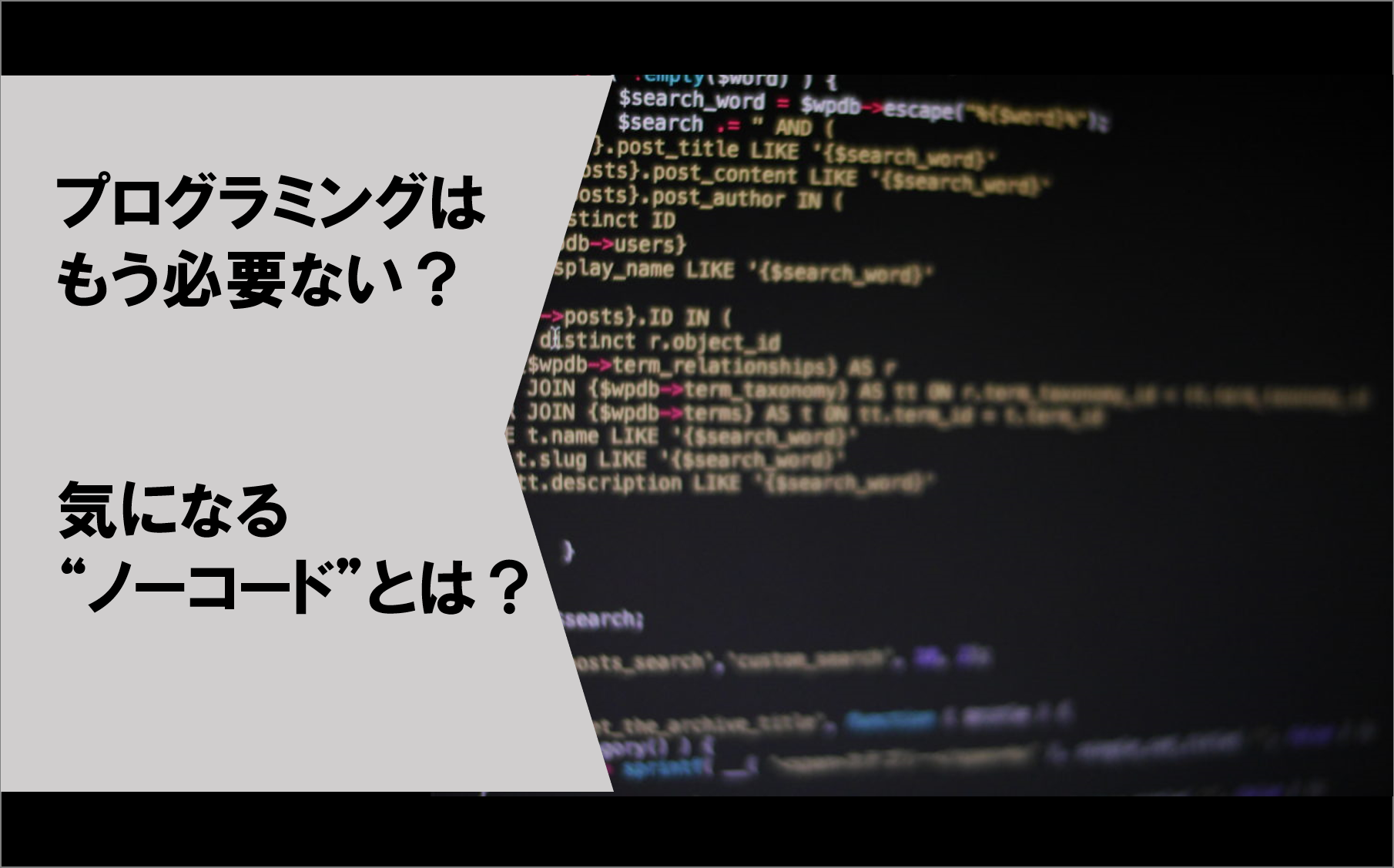
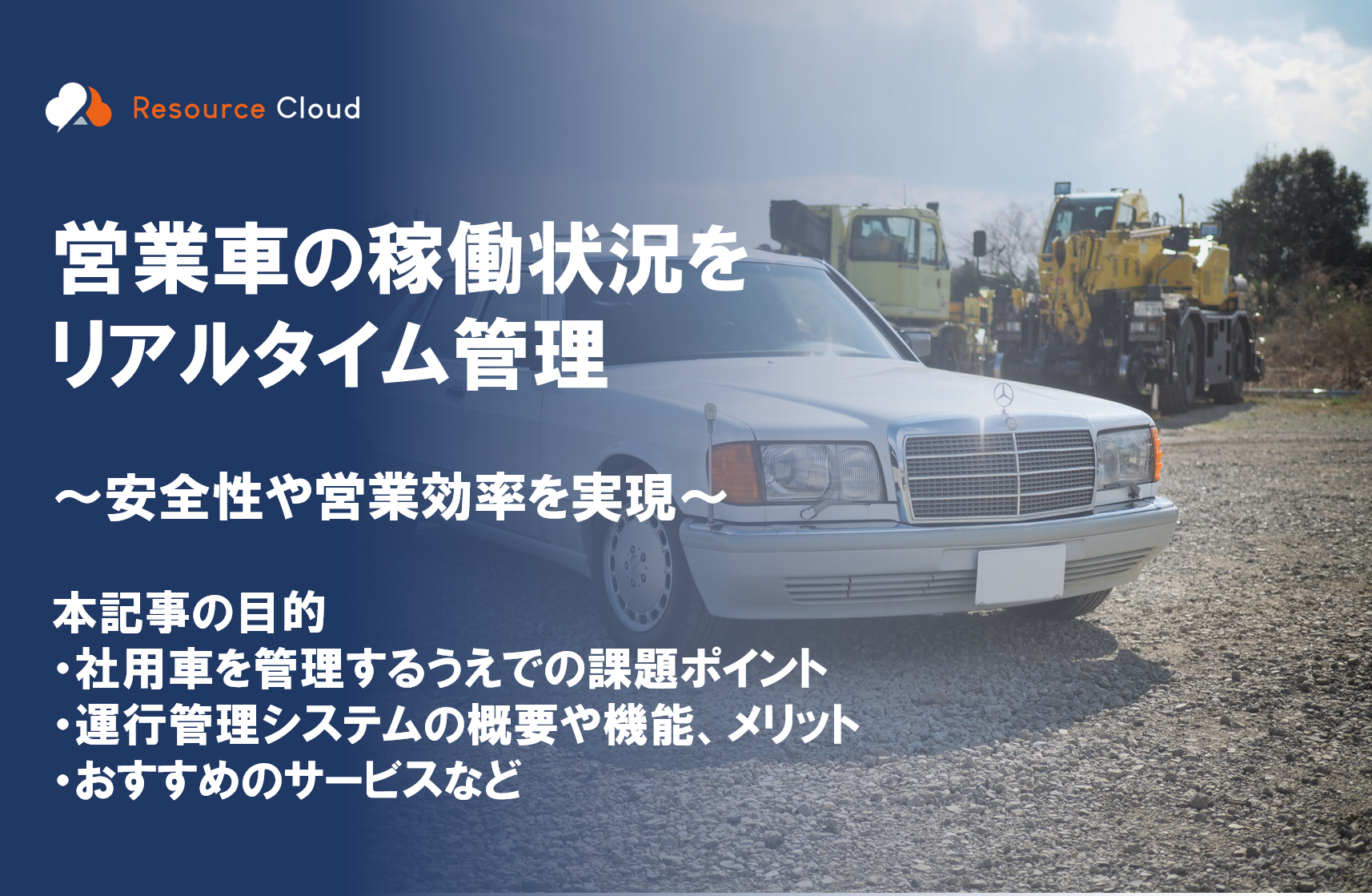
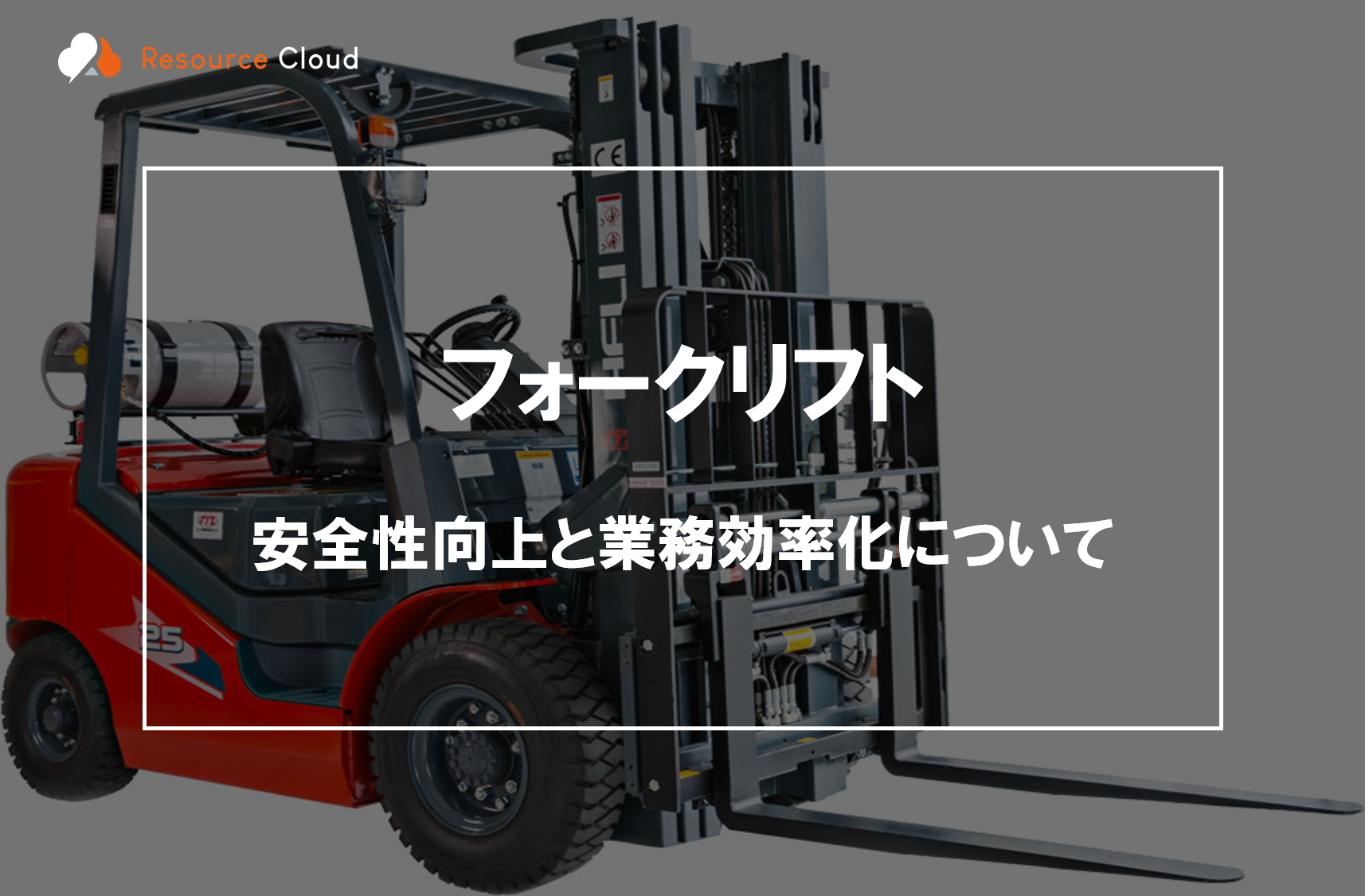
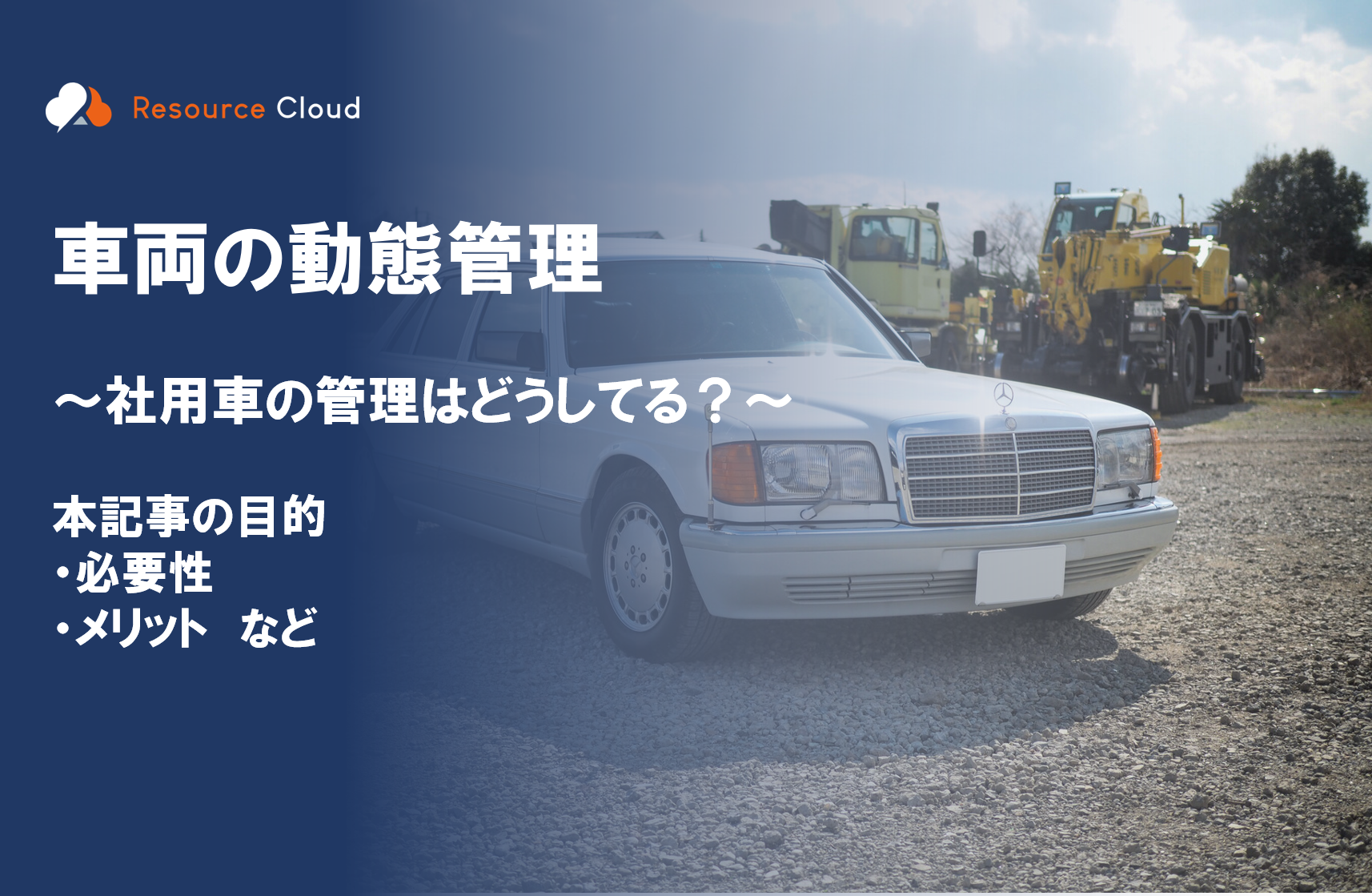
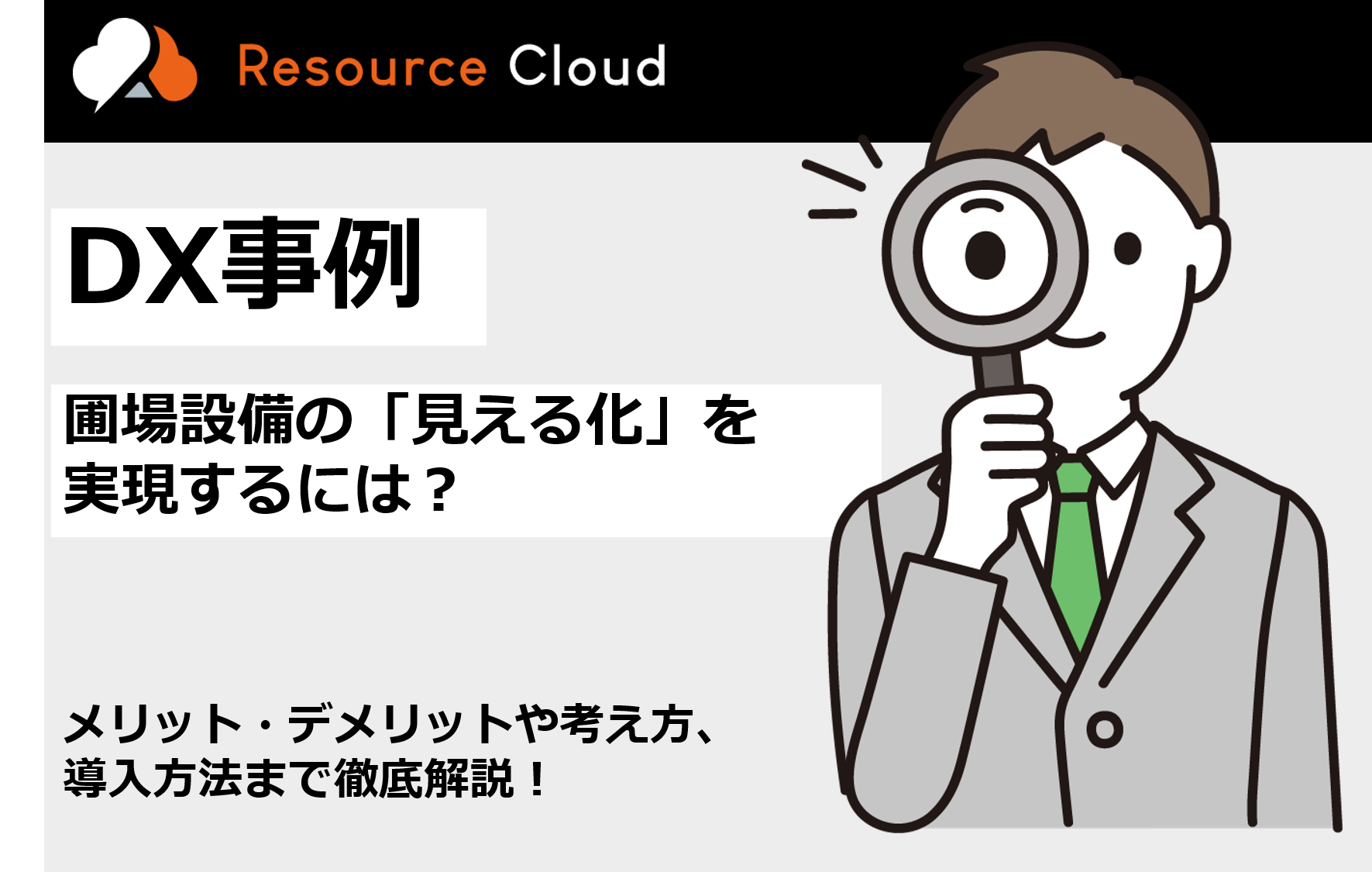
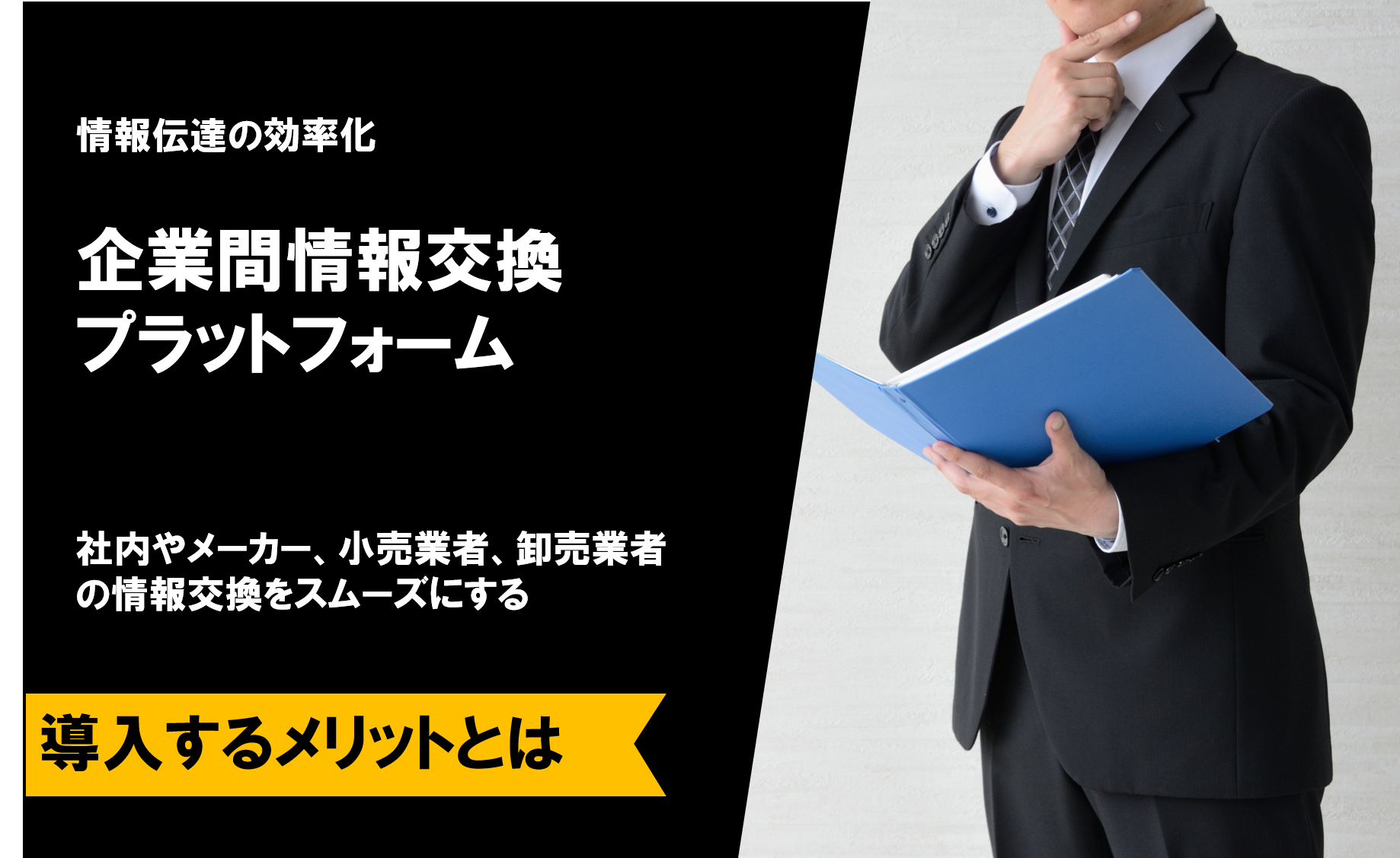
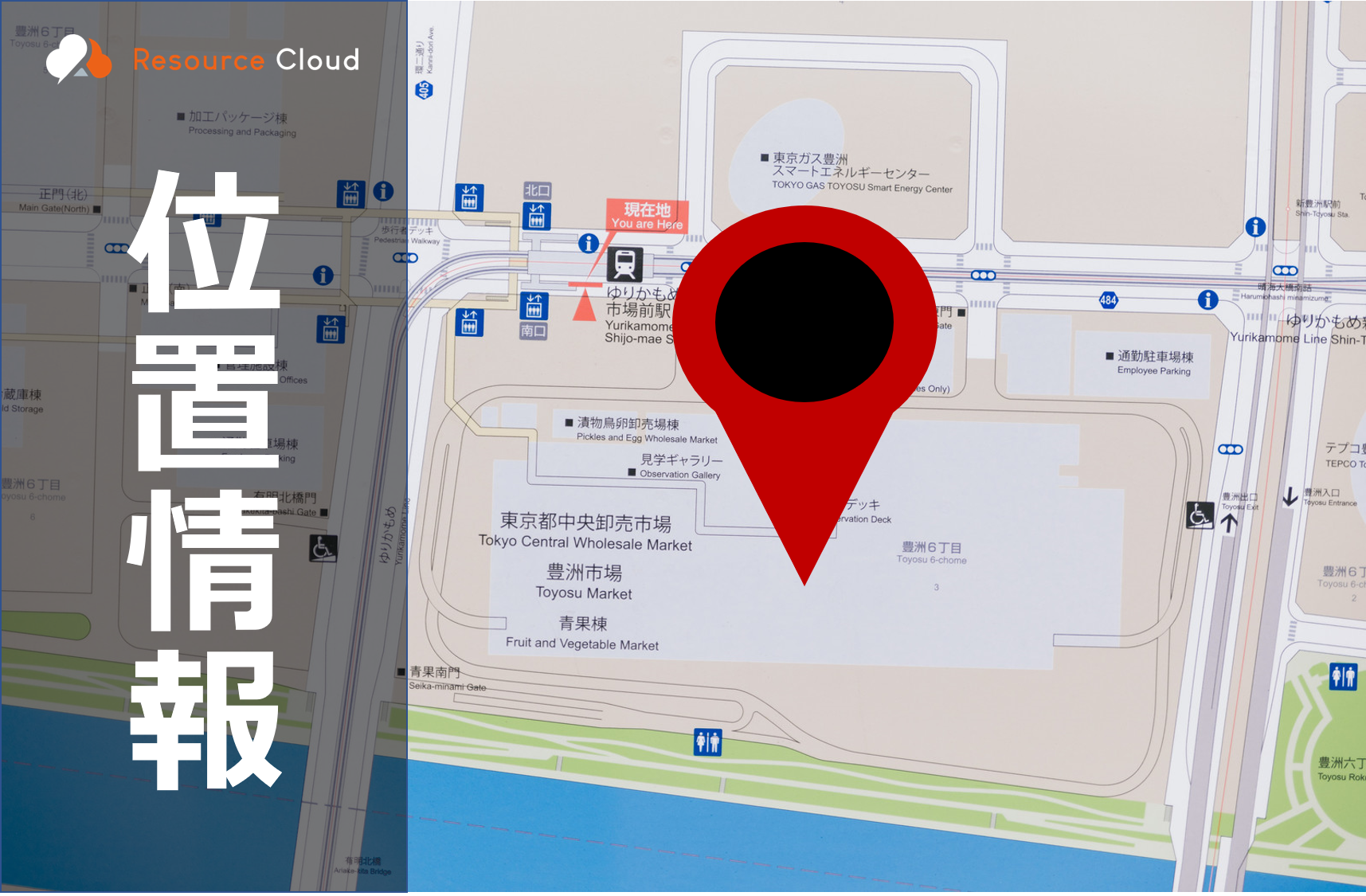
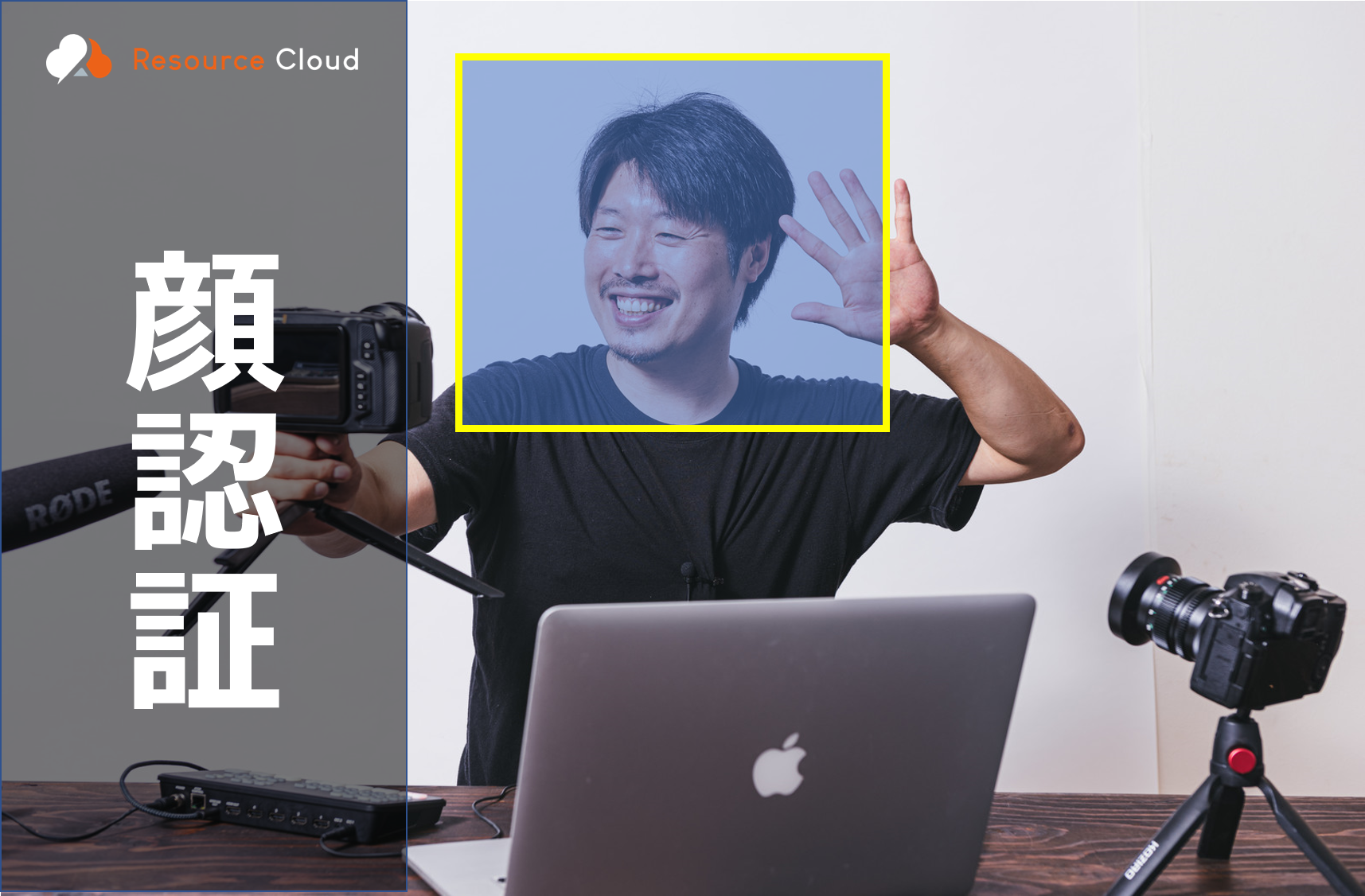
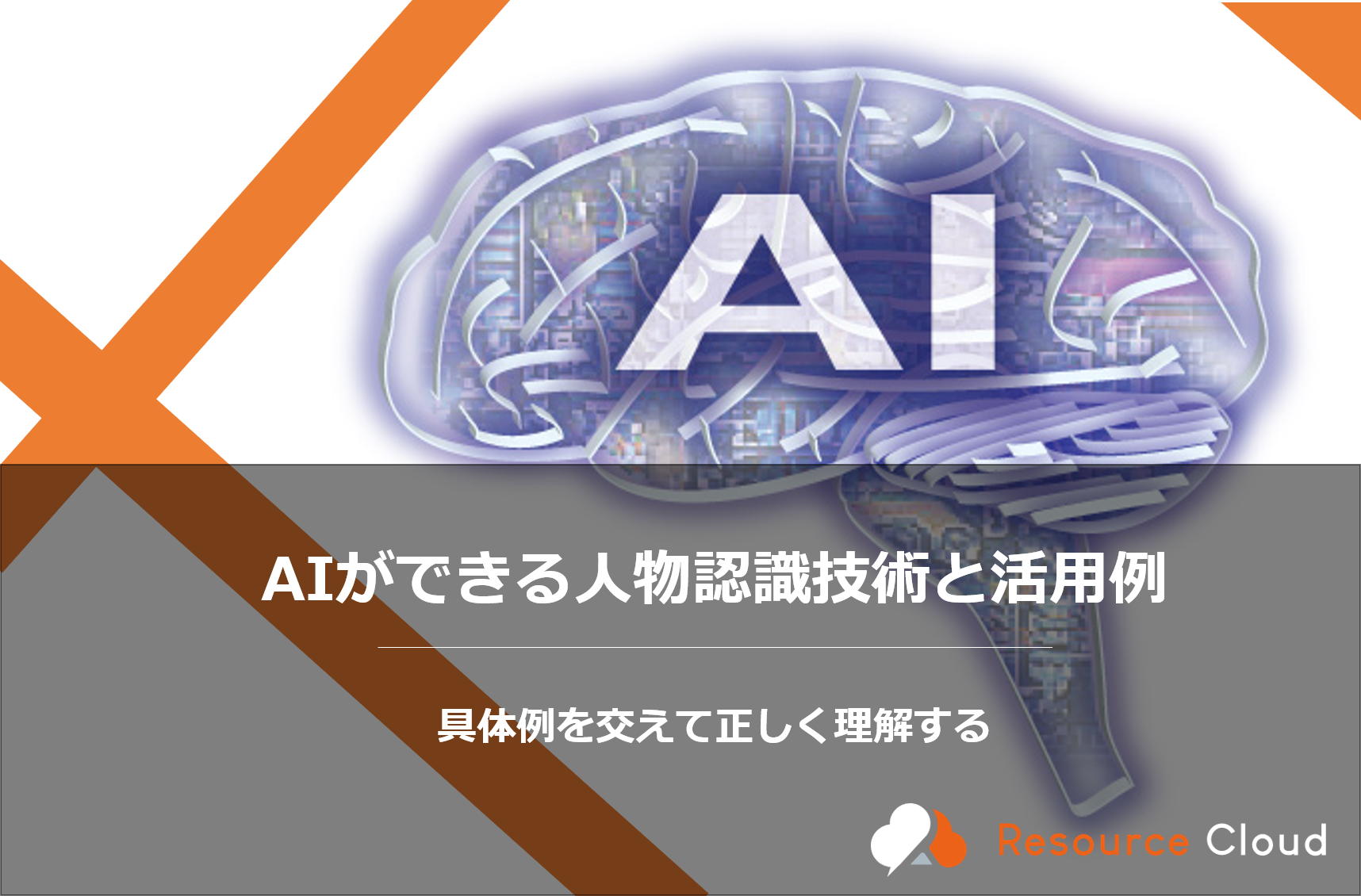
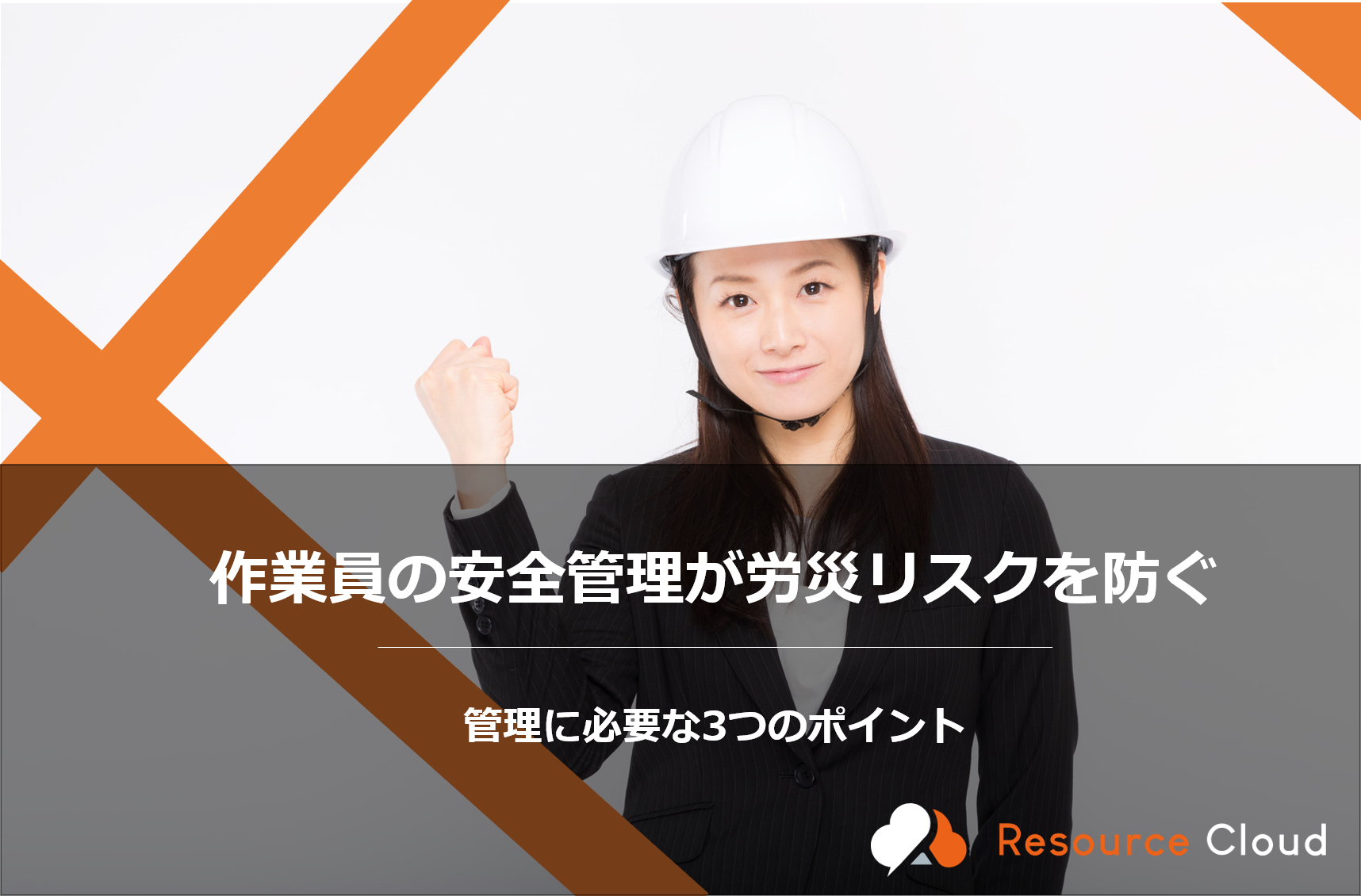
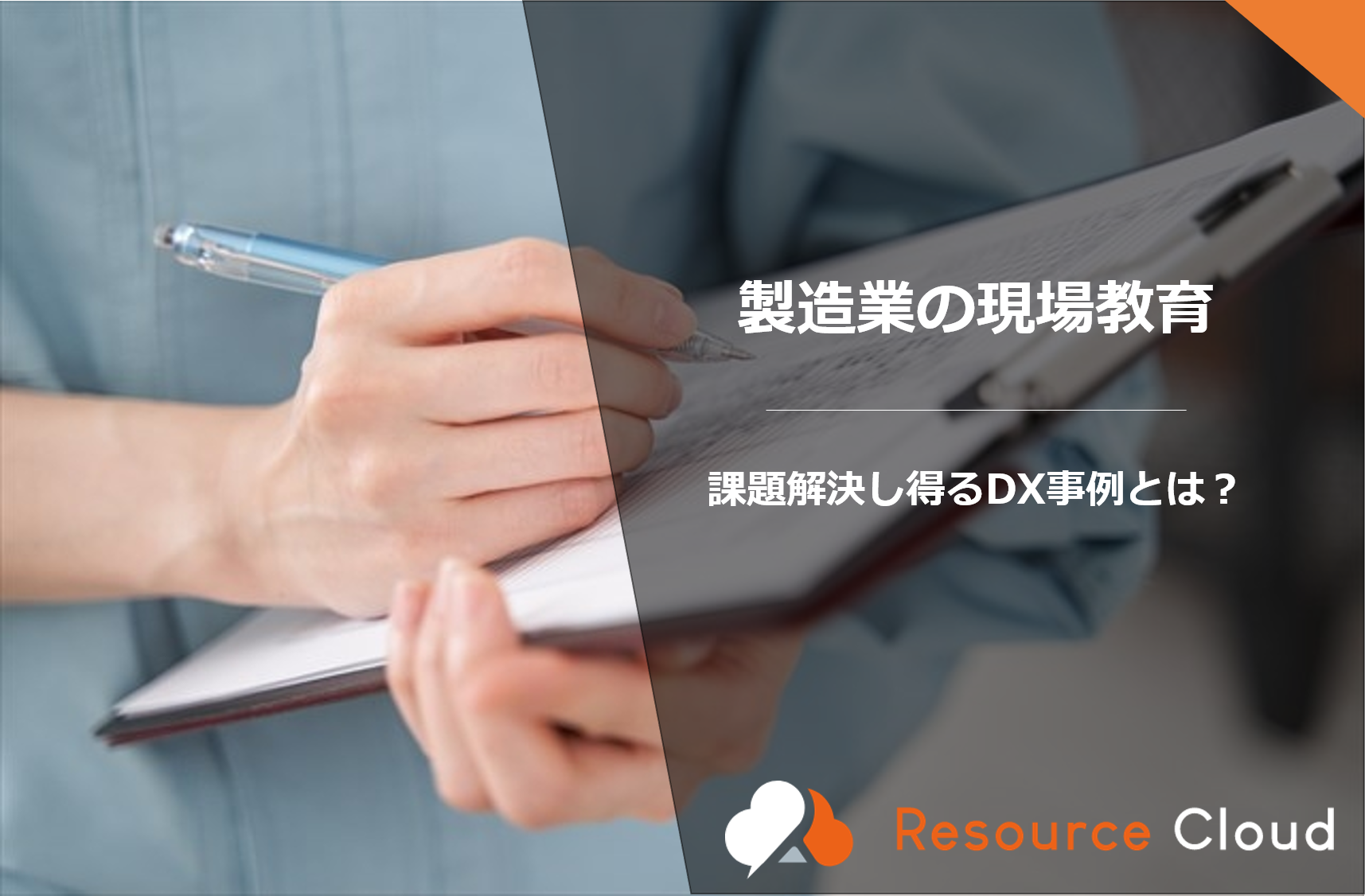
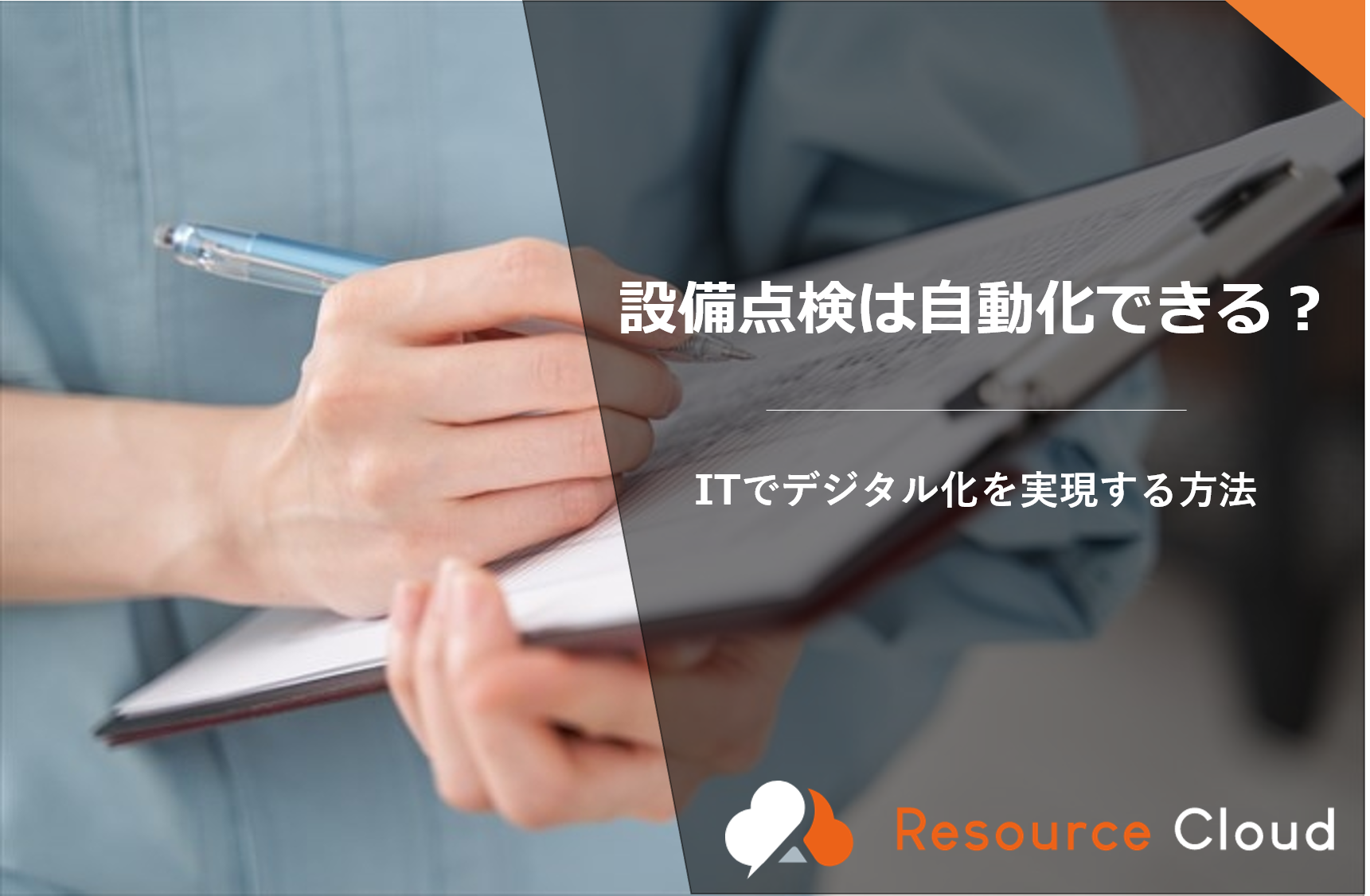
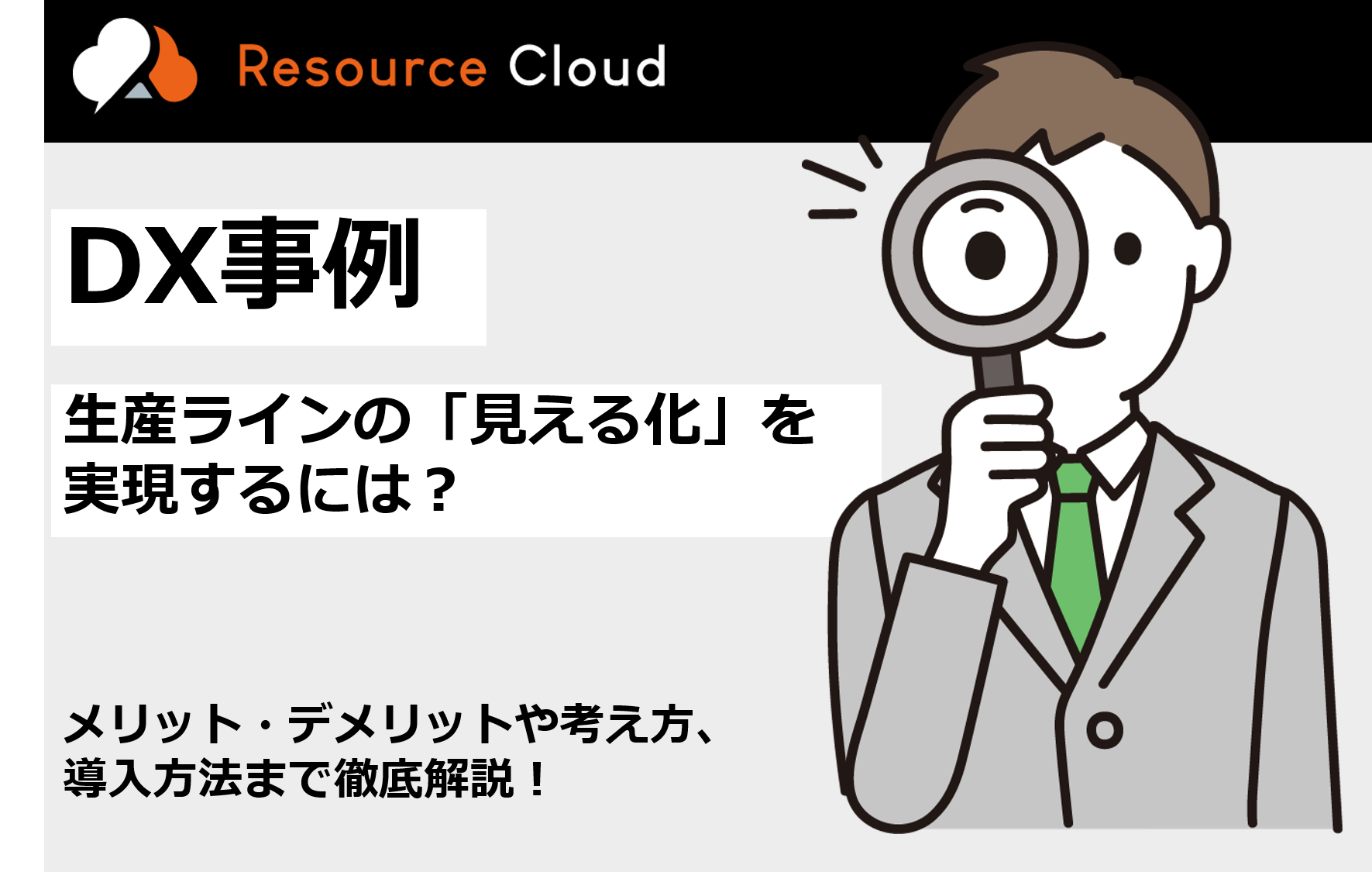
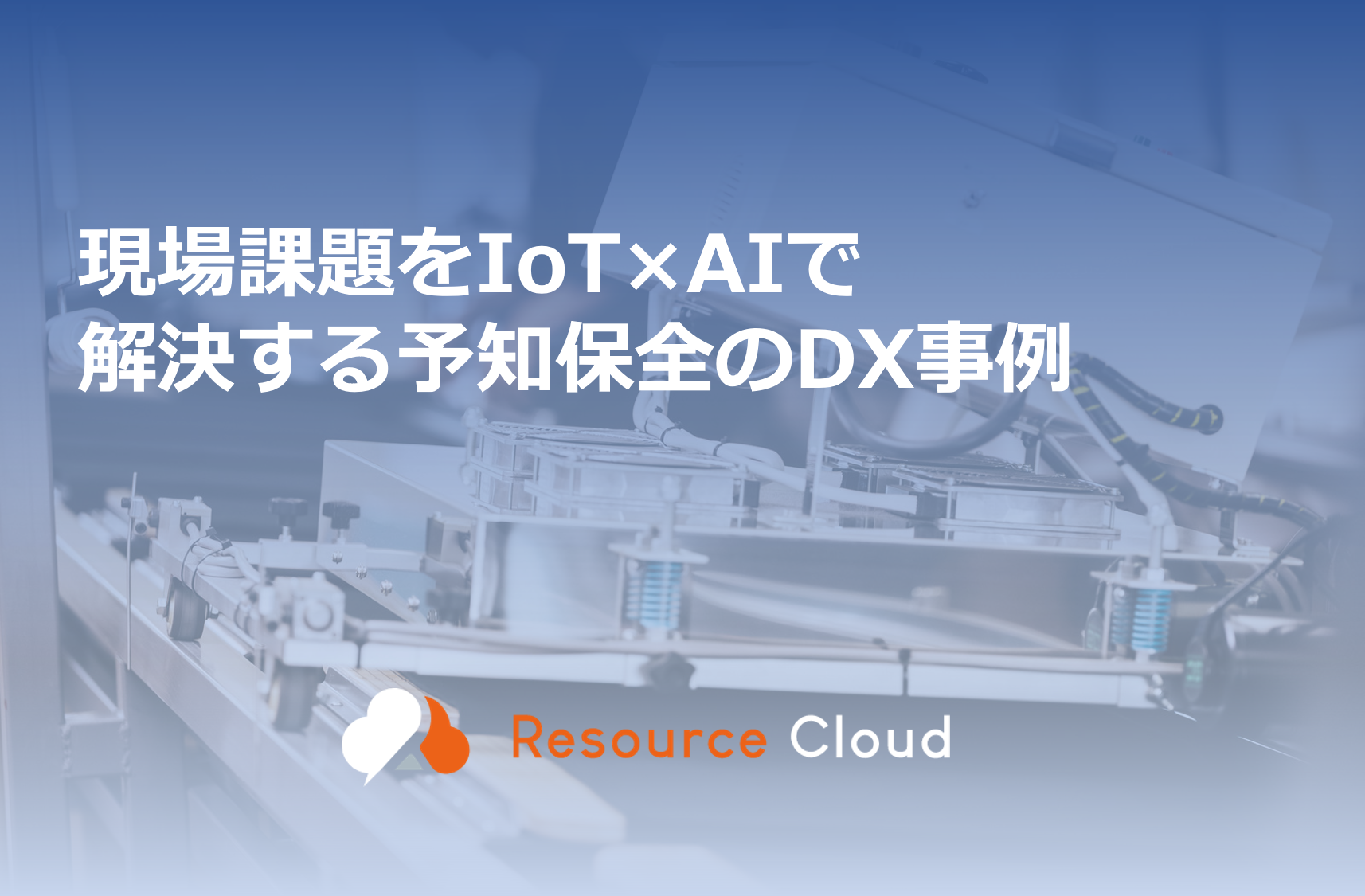
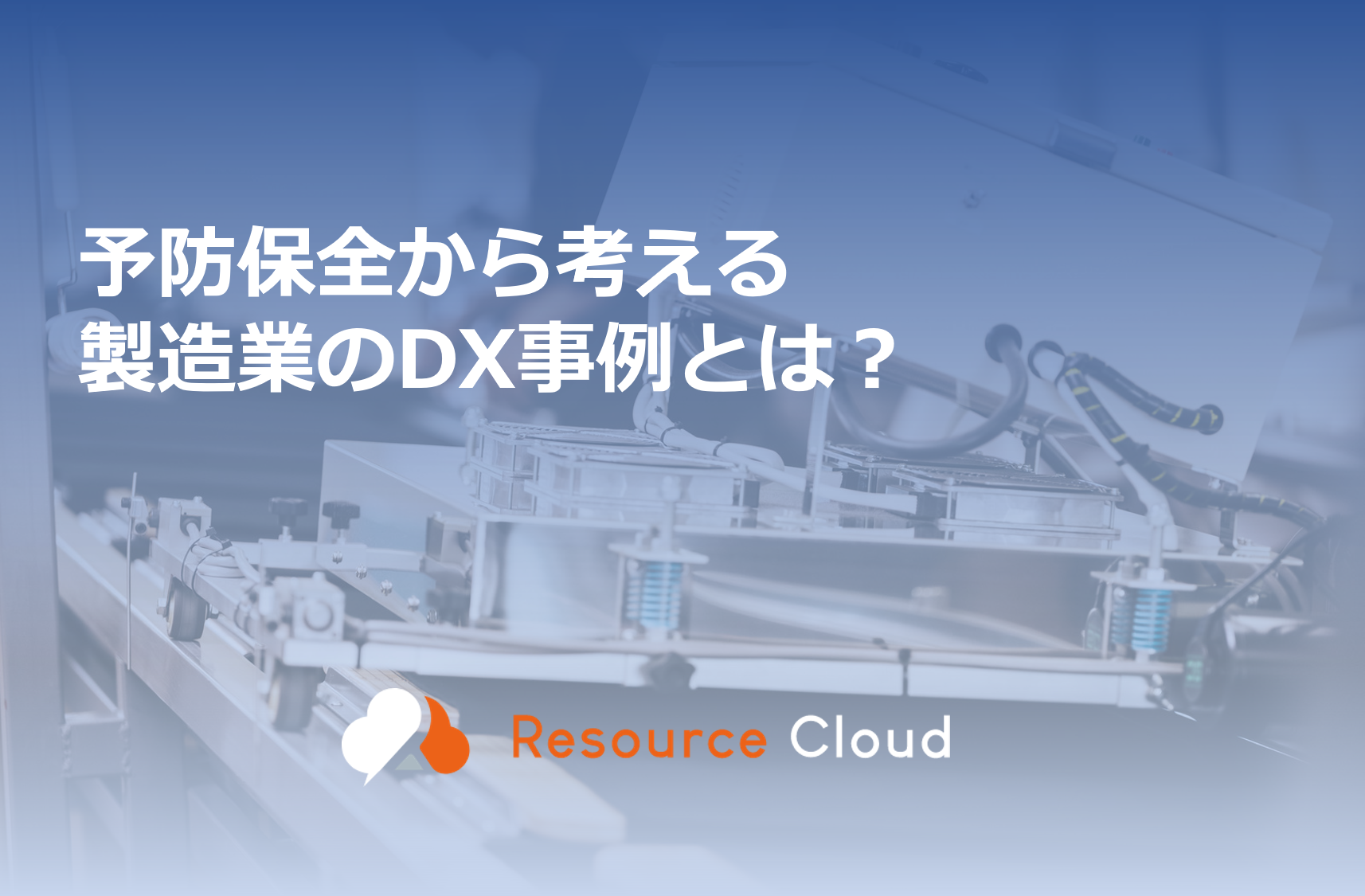
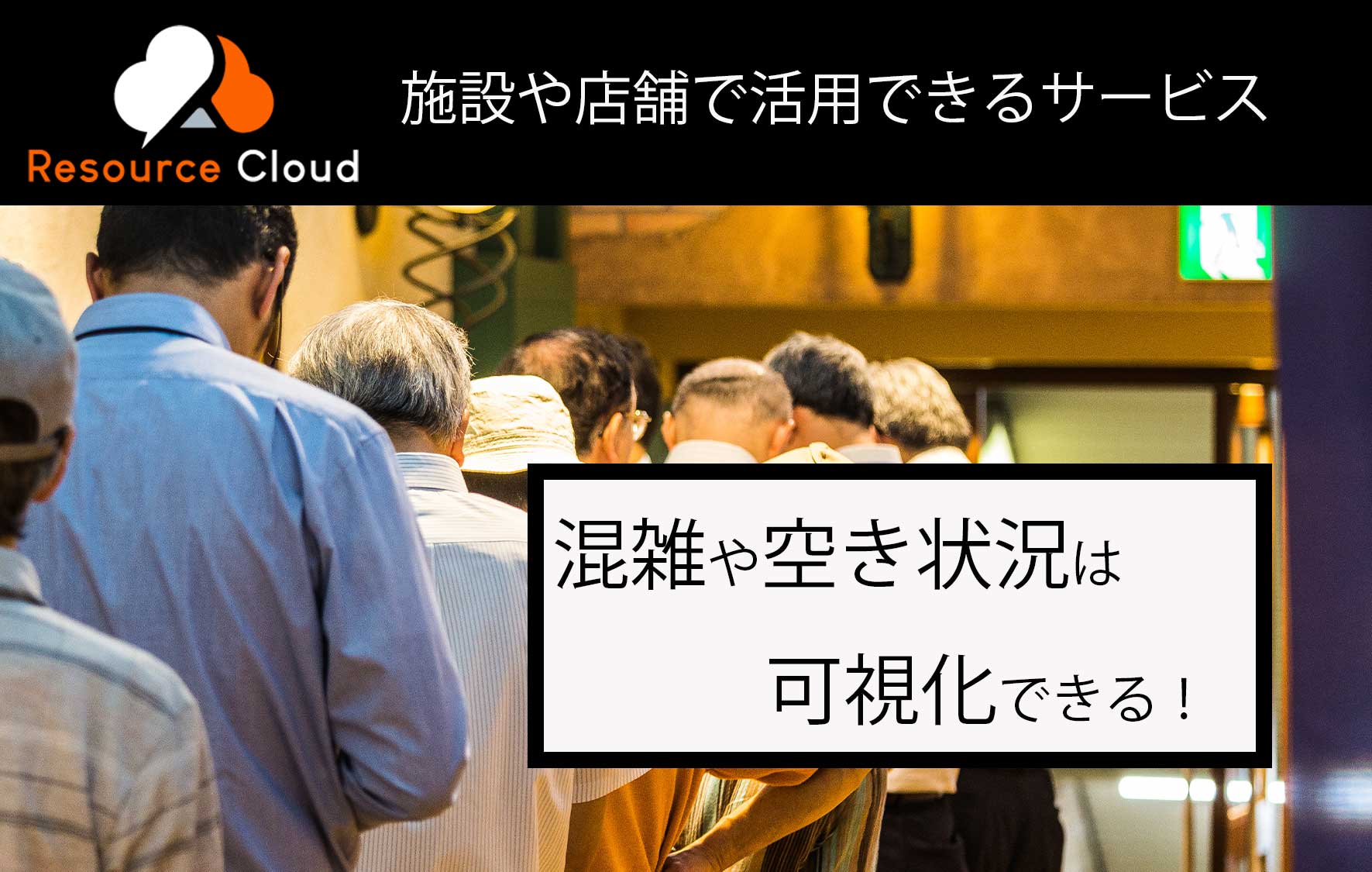
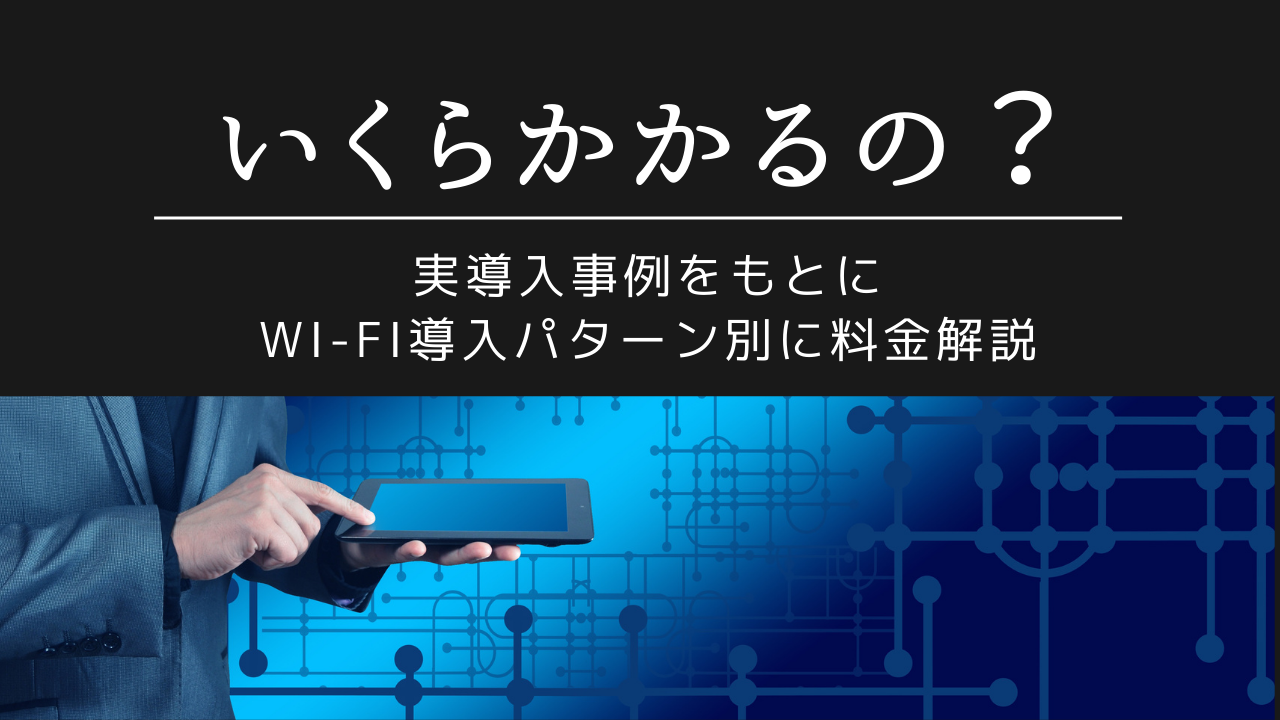
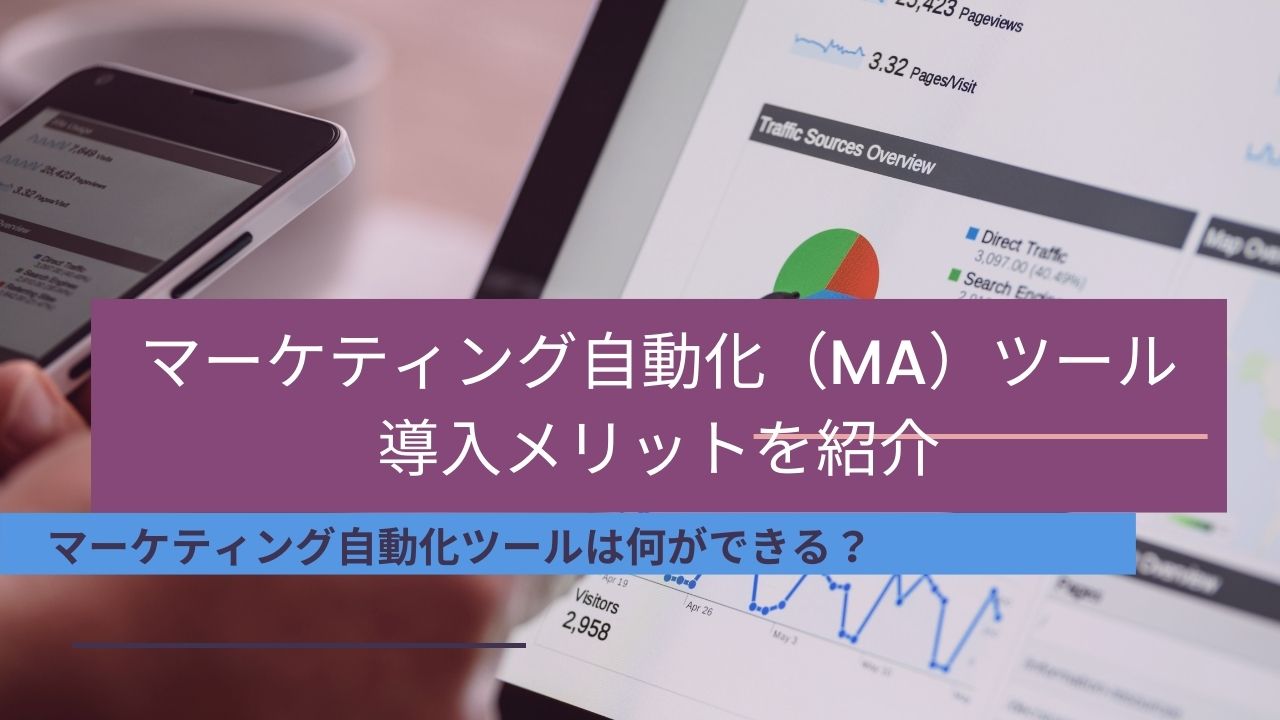
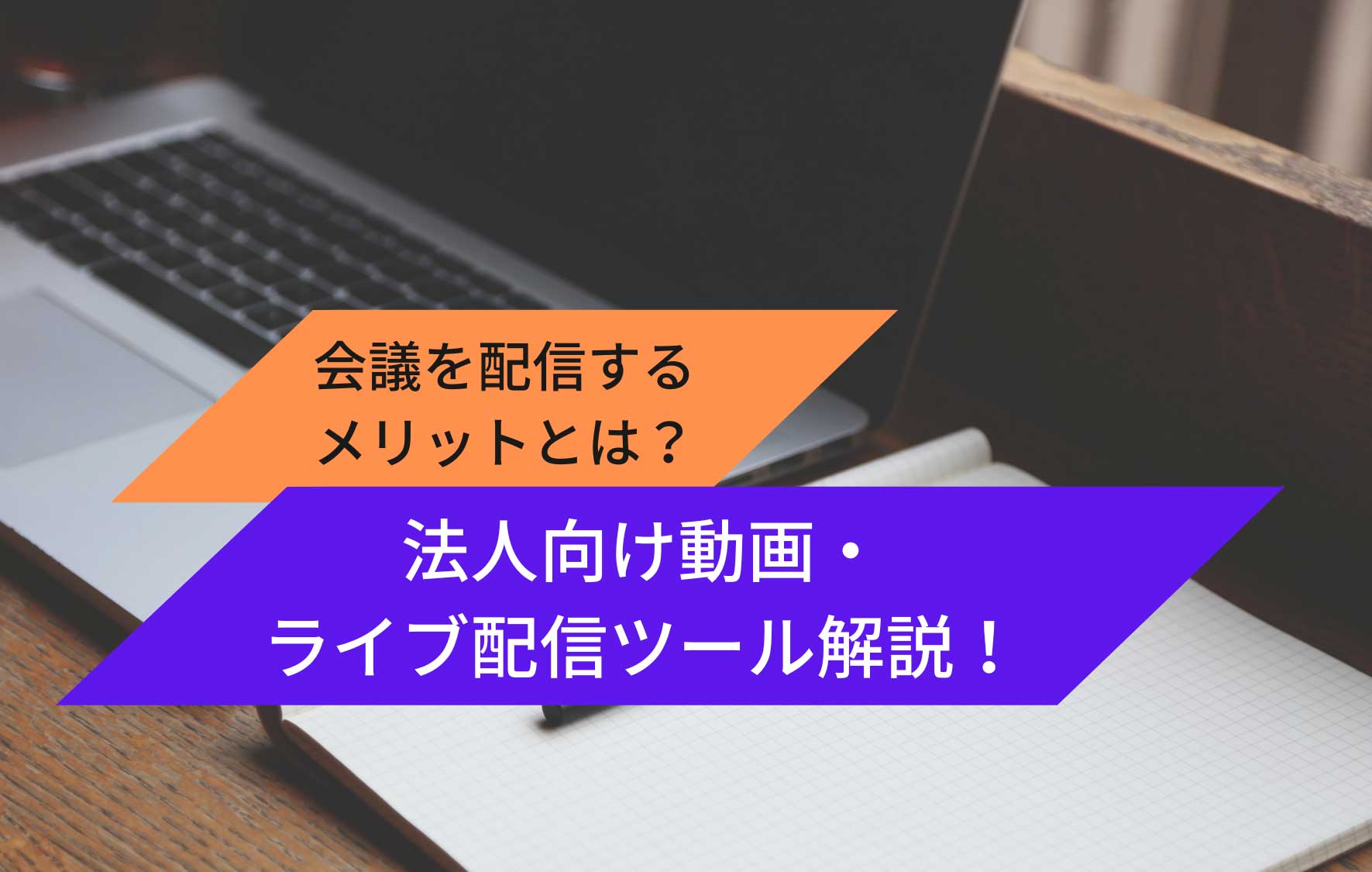
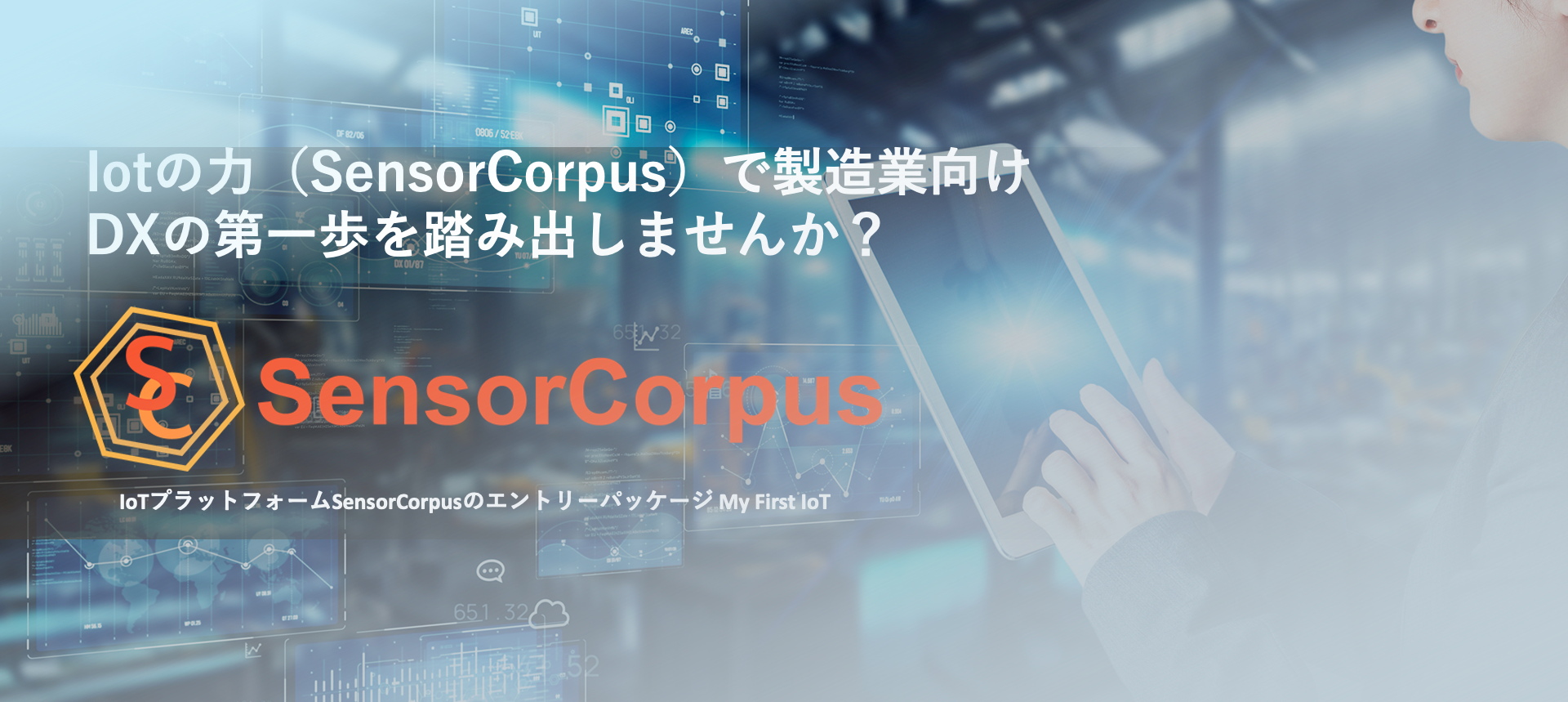
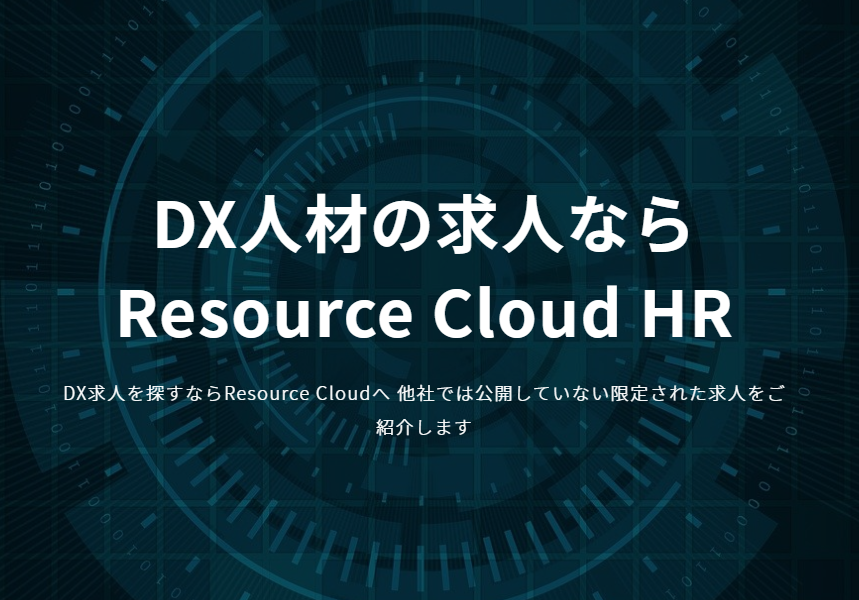
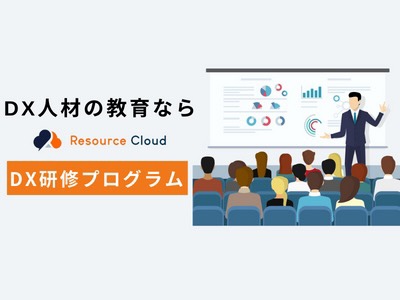
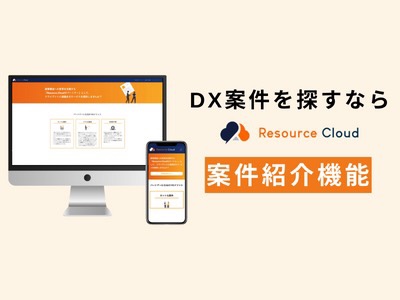