【DX事例紹介】予知保全とは? 現場課題をIoT×AIで解決!
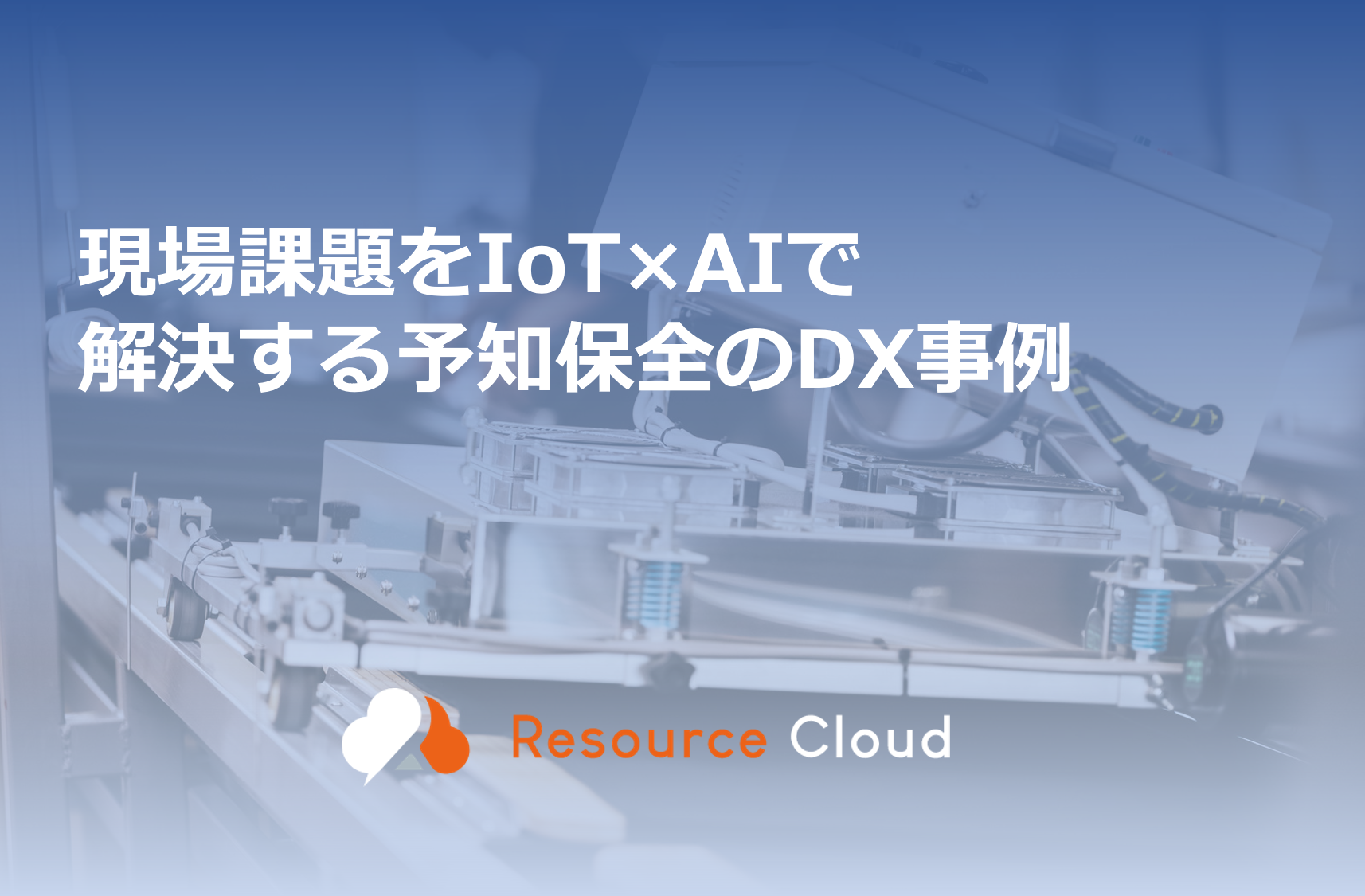
製造業におけるデジタルトランスフォーメーション(以下、DX)の事例として、メンテナンス手法の「予防保全」「事後保全」をテーマにご紹介しました。
先述した通り、メンテナンスは「予防保全」「事後保全」「予知保全」の3つに分類されるため、本記事では「予知保全」をテーマに製造業におけるDX事例をみていきます。
1.予知保全とは? DX推進のためにはデジタル化が必要!
まず初めに、予知保全とは「機器の状態を日常的に計測・監視し、設備の劣化状態を把握または予知して部品を交換・修理する」メンテナンス手法です。従って「故障する前に」行うことから予防保全と予知保全は似ていますが、本質的には大きな違いがあります。
まず、予防保全と予知保全の決定的な違いは大きく分けて「機器」と「計測・監視」の2つの異なるコストが観点としてあります。
【予防保全と予知保全のメリット・デメリット】
・予防保全:一定期間・回数などを基にメンテナンスするため、まだ使うことが出来る機器を交換するリスクはあるが、計測・監視コストは安くなる。
・予知保全:劣化の状態から故障する前にメンテナンスするため、限界まで機器を利用することが出来ることから無駄を省略することに繋がるが、計測・観測のコストはかかる。
ここで言う「計測・観測のコスト」とは、計測・観測をするために必要な機器や人員体制に加え、それらの膨大なデータから行う人的な判断などを指します。
より極端な例で言えば、現場経験豊富な人材が「まだ使える」と判断する感覚も予知保全であり、現場経験の長さが計測・観測の期間と言い換えることも出来るため、いずれにせよ中長期的な判断が必要不可欠になります。
しかし、今挙げたような予知保全はスキルや経験に依存することから「属人的」かつ「中長期的」な予知保全になってしまいます。更に言えば、人的な統計では見落としや、そもそも検知出来ない場合などもあることから、不十分な予知保全であると言わざるを得ません。
だからこそ、「IoT機器による計測」と「AIによる機械学習」を活用することで「標準的」かつ「短期的」な予知保全の実現を目指すことが重要視され、その結果として生産ラインのDXを推進することが出来ます。
では、IoT機器とAIによる予知保全を実現する流れを具体的にみていきましょう。
【IoT機器とAIによる予知保全の導入ステップ】
Step1. まず、IoT機器で日常的に設備の数値を計測します。(データは画像なども含む)
Step2. 次に、Step1で計測した大量のデータをAIで解析し、数値化します。
Step3. その後、AIの機械学習を用いることで、それらの数値から「通常」の値と、「異常」な値に閾値を設定します。(異常検知とも言います)
Step4. 最後に、稼働状況や生産状況のデータと組み合わせることで、メンテナンスのタイミングを意思決定します。
大まかな流れとしてはこの4ステップに分かれますが、実は予知保全をするためには次のことを考える必要があります。
2.製造業のDXに予知保全は不可欠!人的・時間的コストの大幅削減が可能
まず、予知保全を行う上では、目的を決めておくことが最重要課題です。
そもそも、どのように省力化を実現したいのか、あるいは品質を向上したいのかを決めて準備をしなければ、予知保全の性能や質なども変わってきてしまうからです。(性能を十分に発揮できない予知保全では、予防保全や事後保全などの方が優れた場面も多々あります)
だからこそ、まずは目的の策定を行い、その上で予知保全の環境を整えるようにしましょう。適切なプロセスを踏むことで、品質に影響するヒューマンエラーと、技術的な検査能力の限界を突破できるため、生産ラインのDX推進には欠かせない存在となっています。
品質検査の際にヒューマンエラーが起こってしまった場合、生産者の責任が強く問われ、信頼問題に発展することは明らかです。しかし、品質管理のために生産数を絞ってしまえば、その分コストが上がってしまい、営業面においても大きな課題となってしまいます。そのため、この問題を解決できる予知保全の導入はDXの成功事例と言えます。
また、予知保全を利用することで、品質管理を担う人材の不足という問題にも対処可能です。生産の現場で人間が全てチェックする場合、1日の生産個数も限られますが、予知保全では生産品の品質をシステムが機械的に処理して評価していくため、品質チェックにかかる人的または時間的コストを大幅に削減可能です。その点においても、予知保全の仕組みの導入はDXの成功事例であると言えます。
3.まとめ~予知保全で生産ラインの現場課題を解決しよう~
いかがでしたか?今回は予知保全をテーマに、生産ラインの現場課題を解決することでDXの事例を紹介しました。とは言え、これまで紹介してきた予防保全や事後保全との組み合わせをしなければ、過剰な設備投資となってしまうことも十分に考えられます。
生産設備における異常検知システムの導入コストは、手軽に導入できる価格からエンタープライズ向けの製品まで様々です。そのため、自社に合う適切なシステムを選ぶことが重要です。
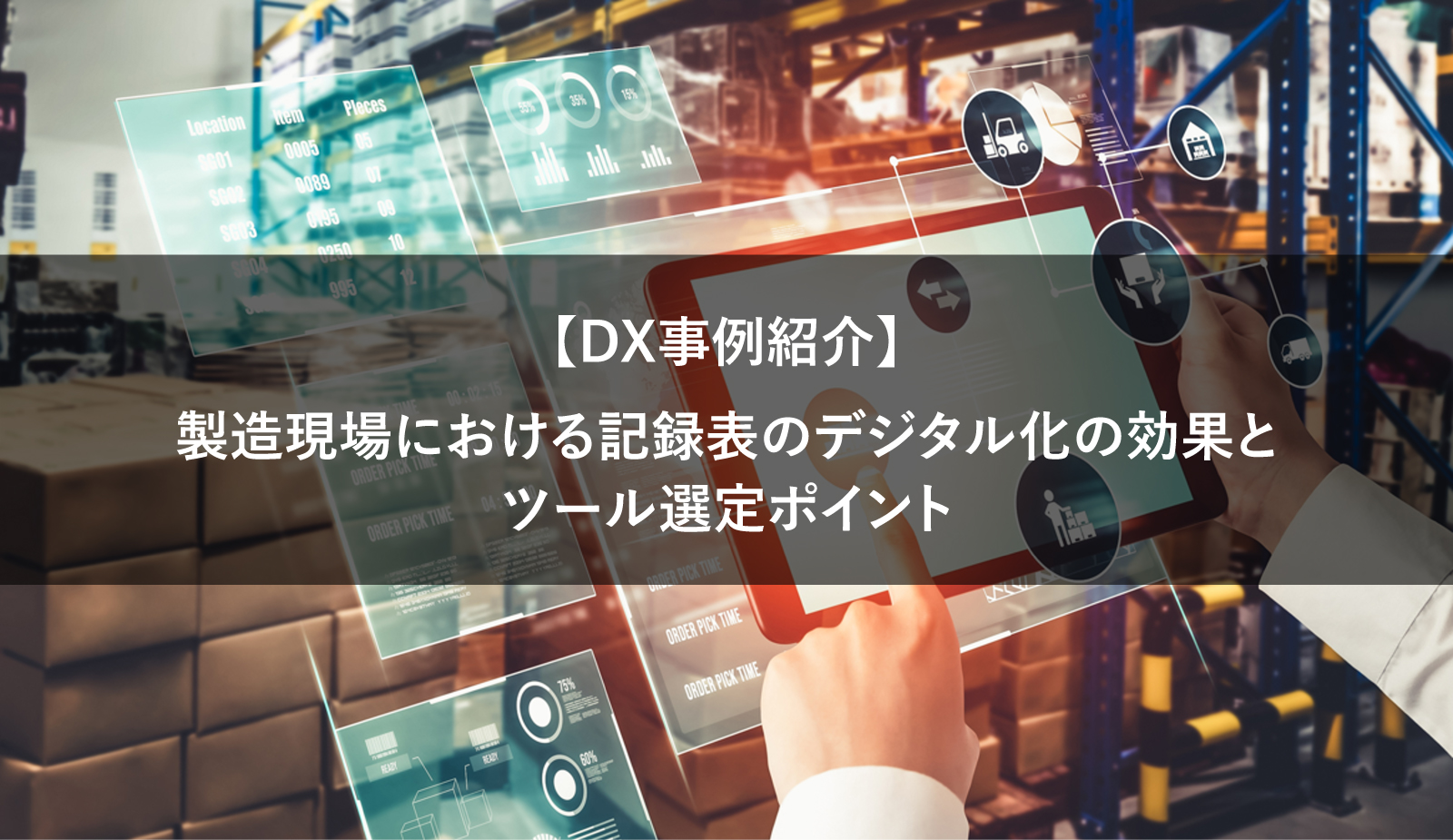
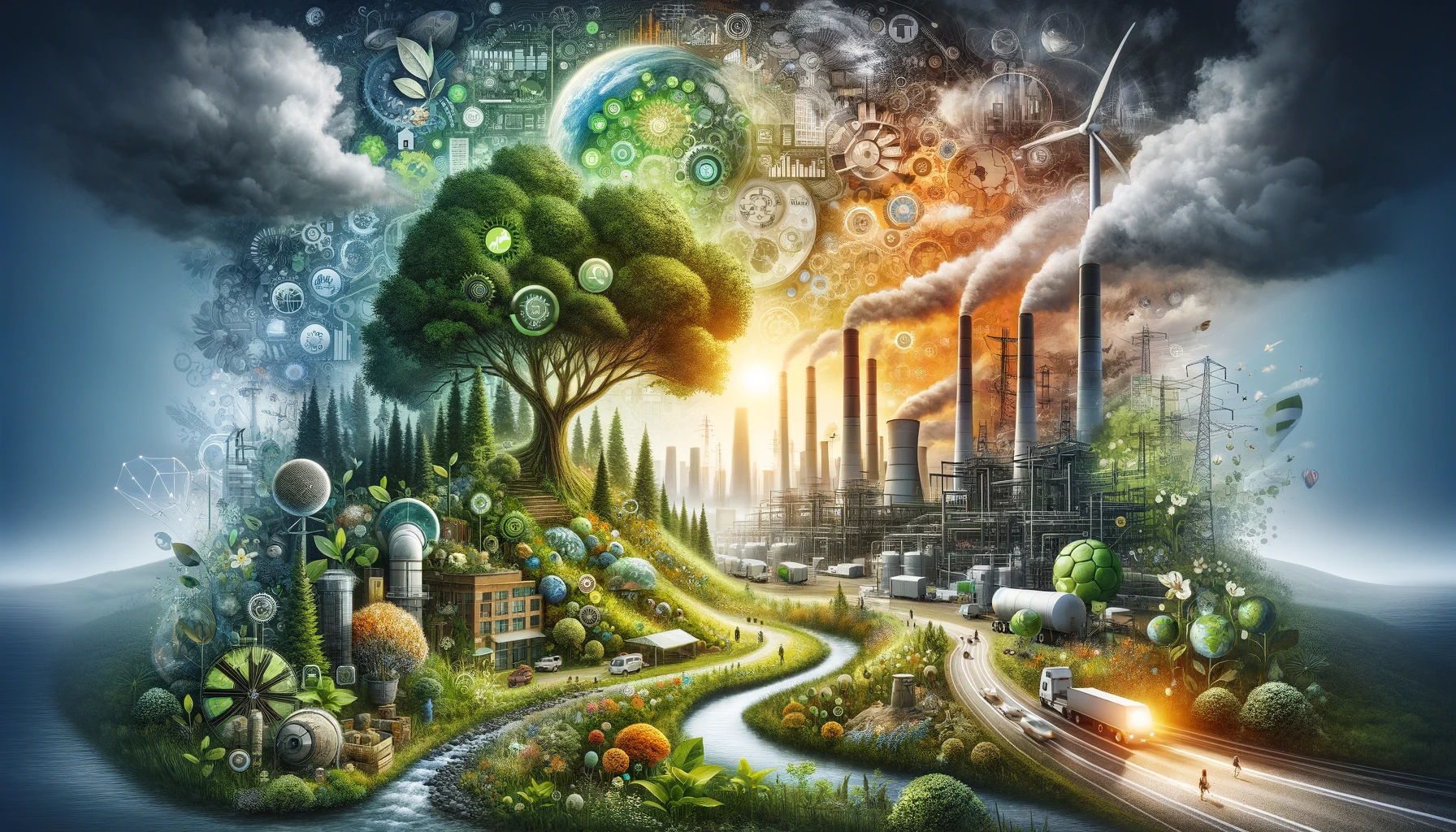
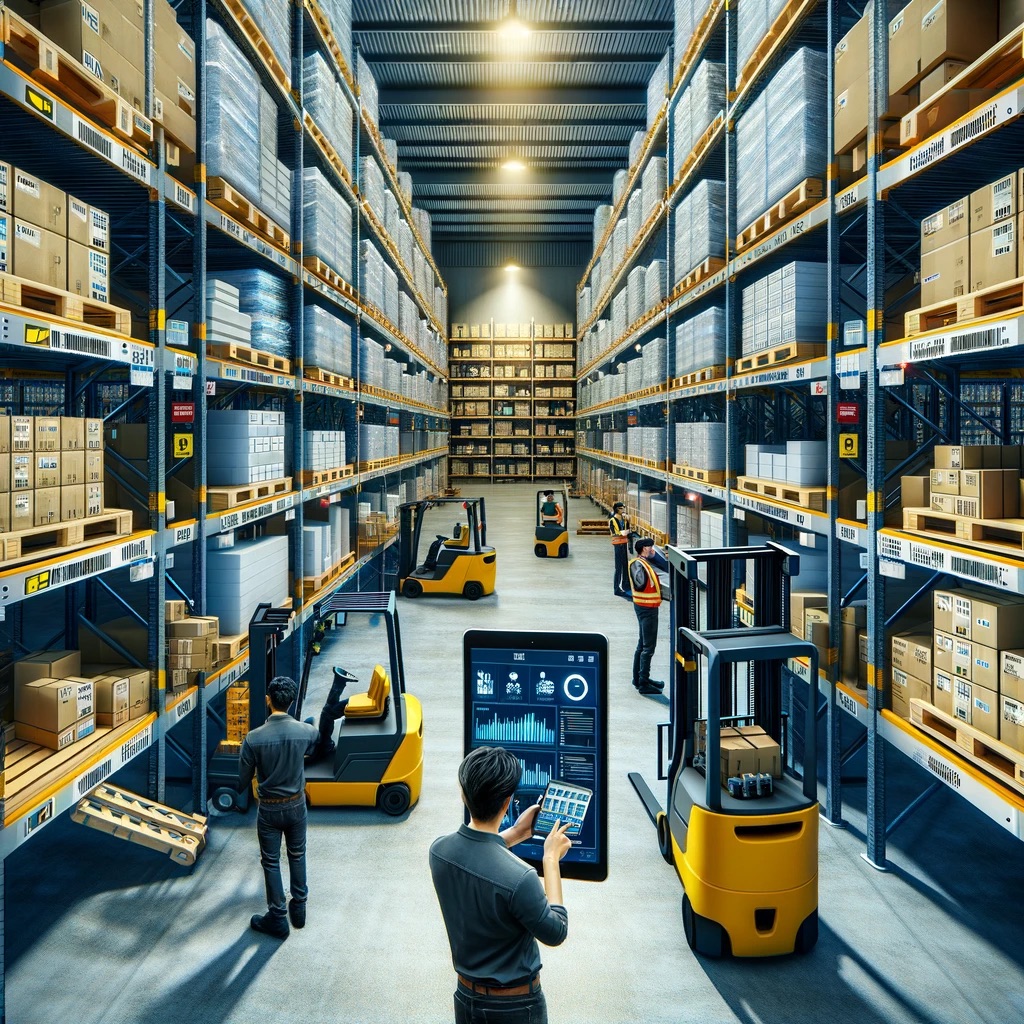
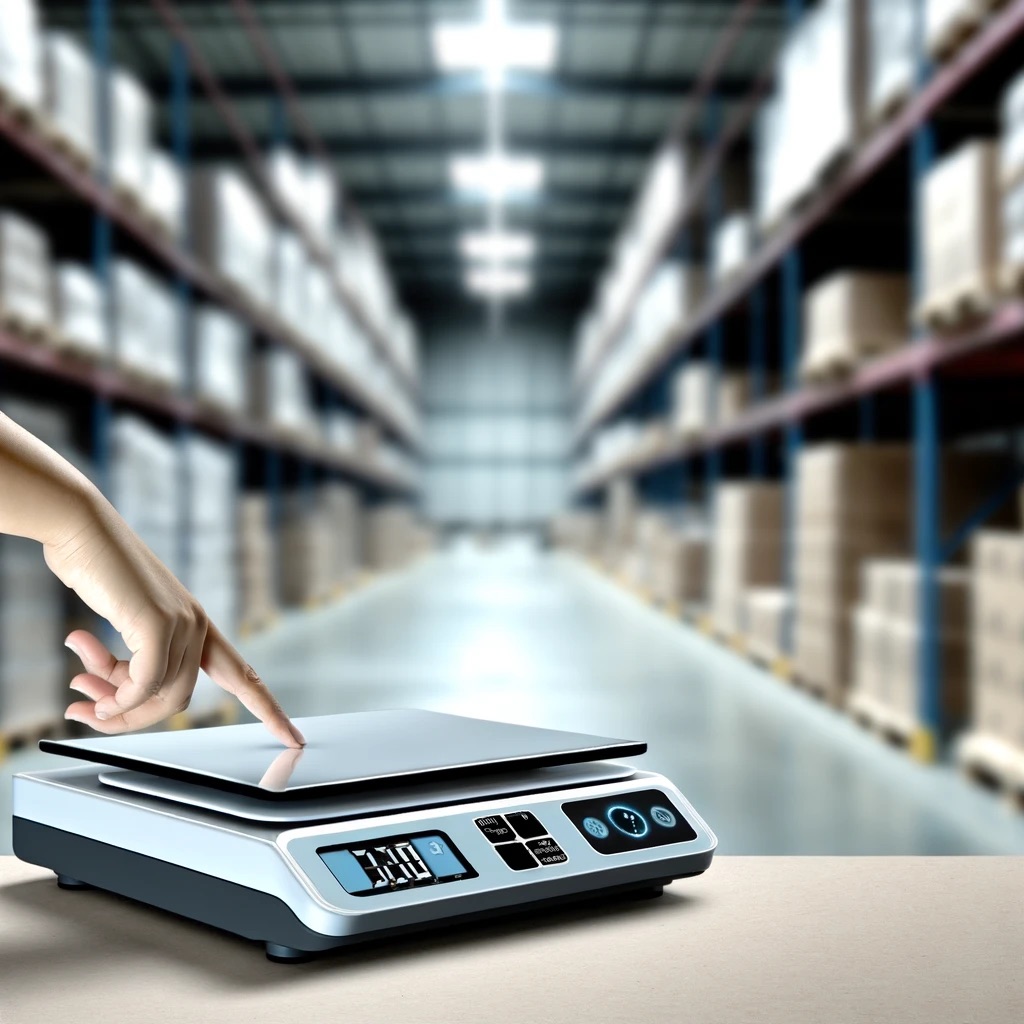
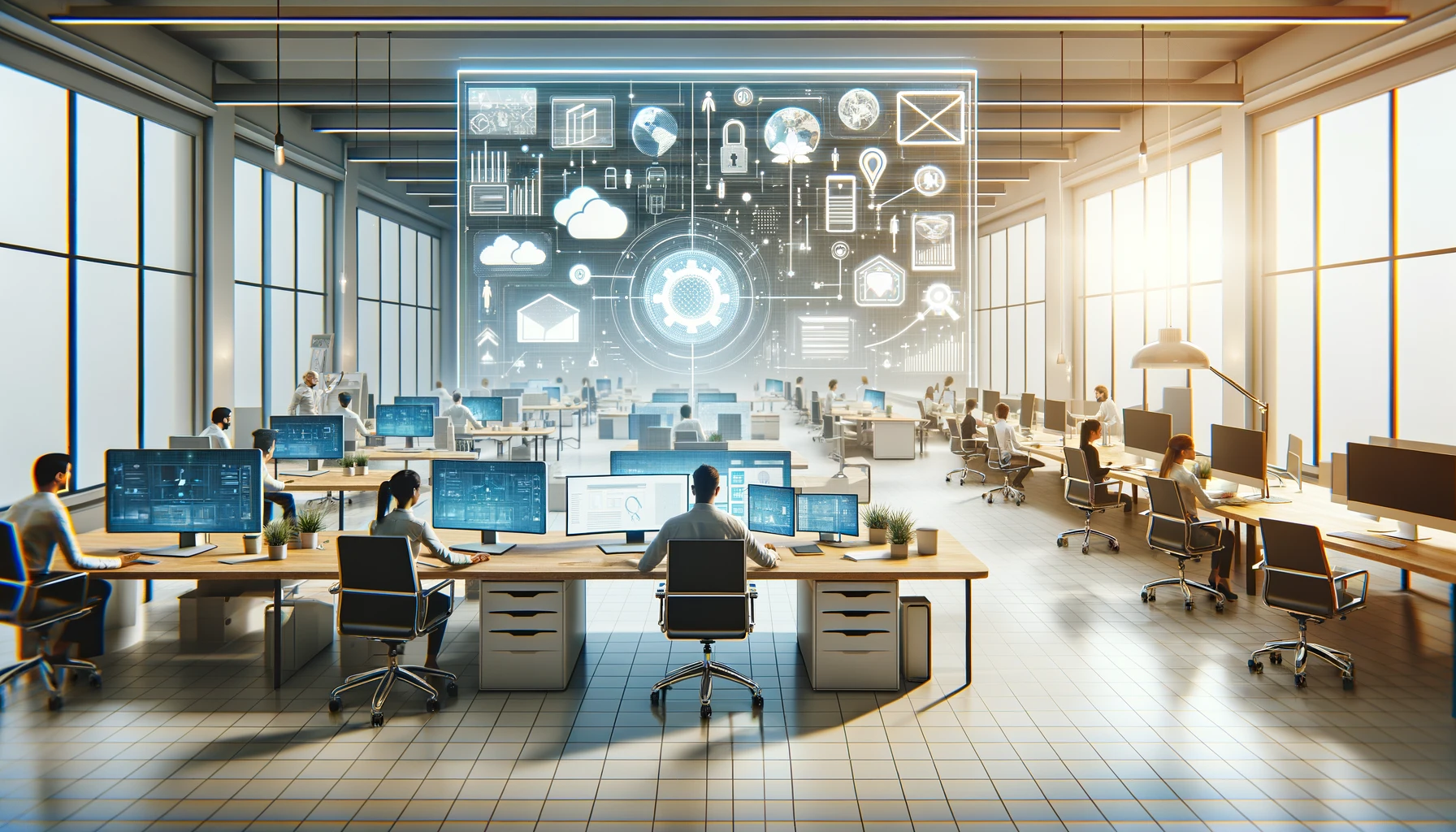
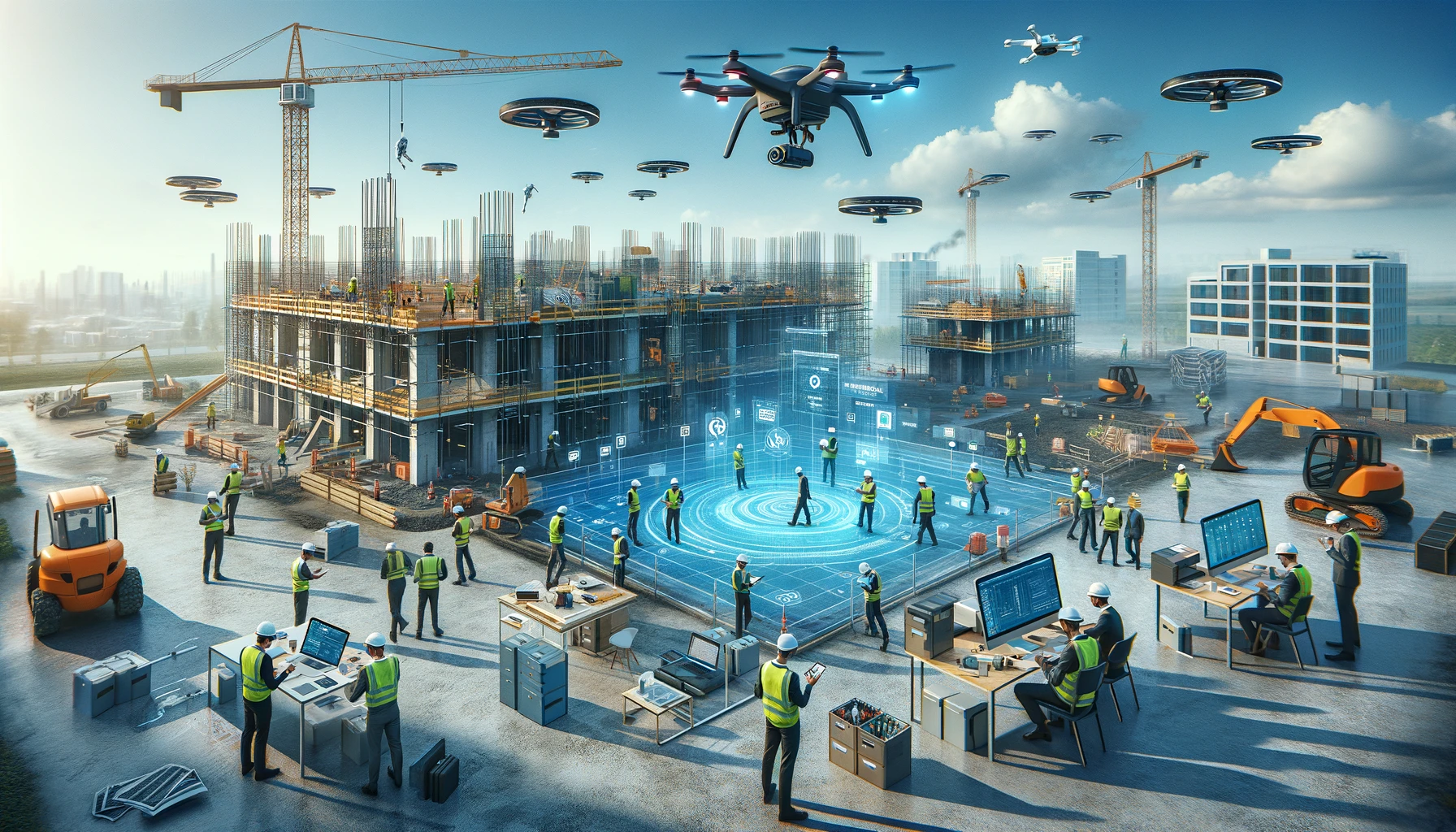
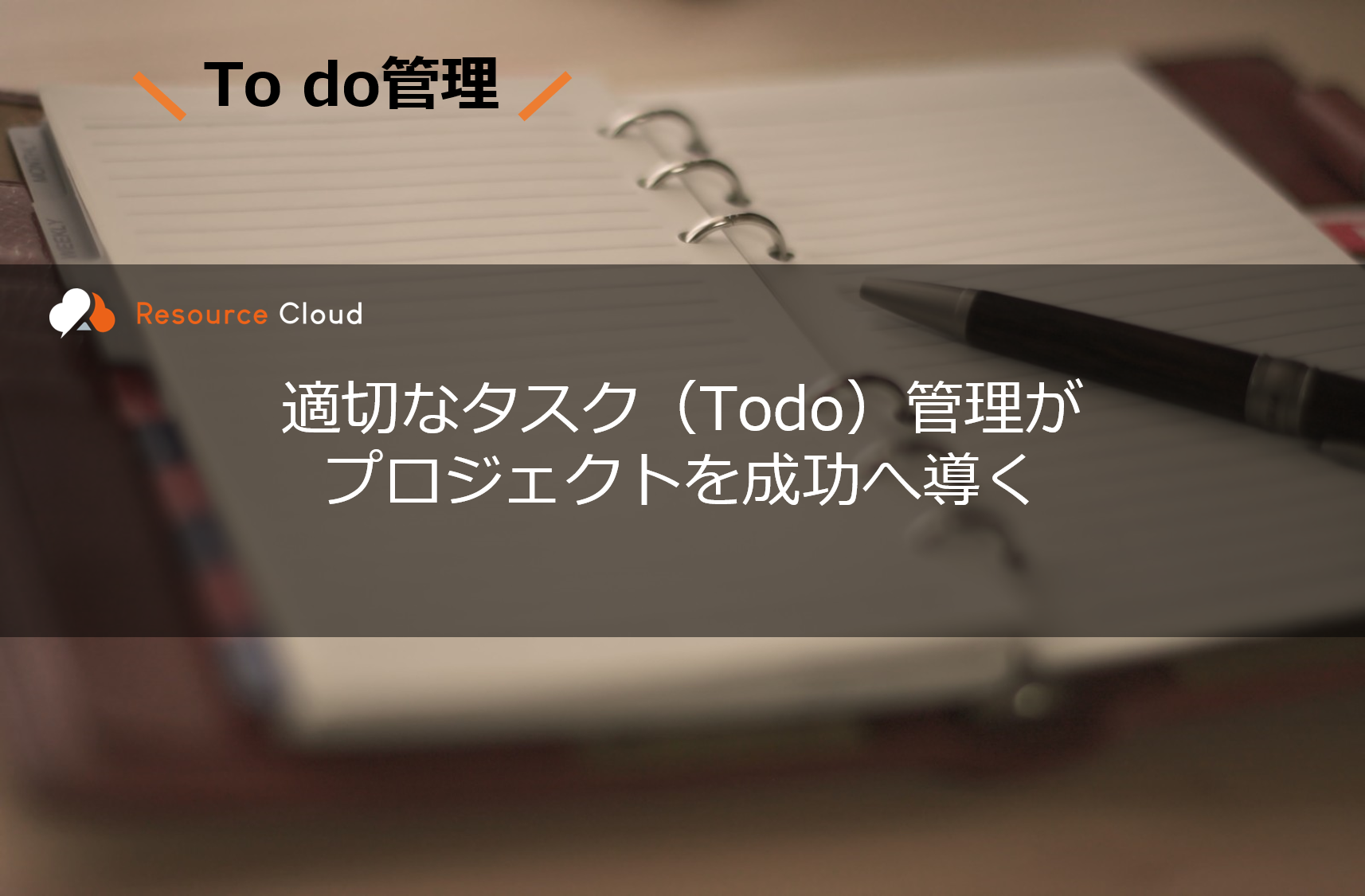

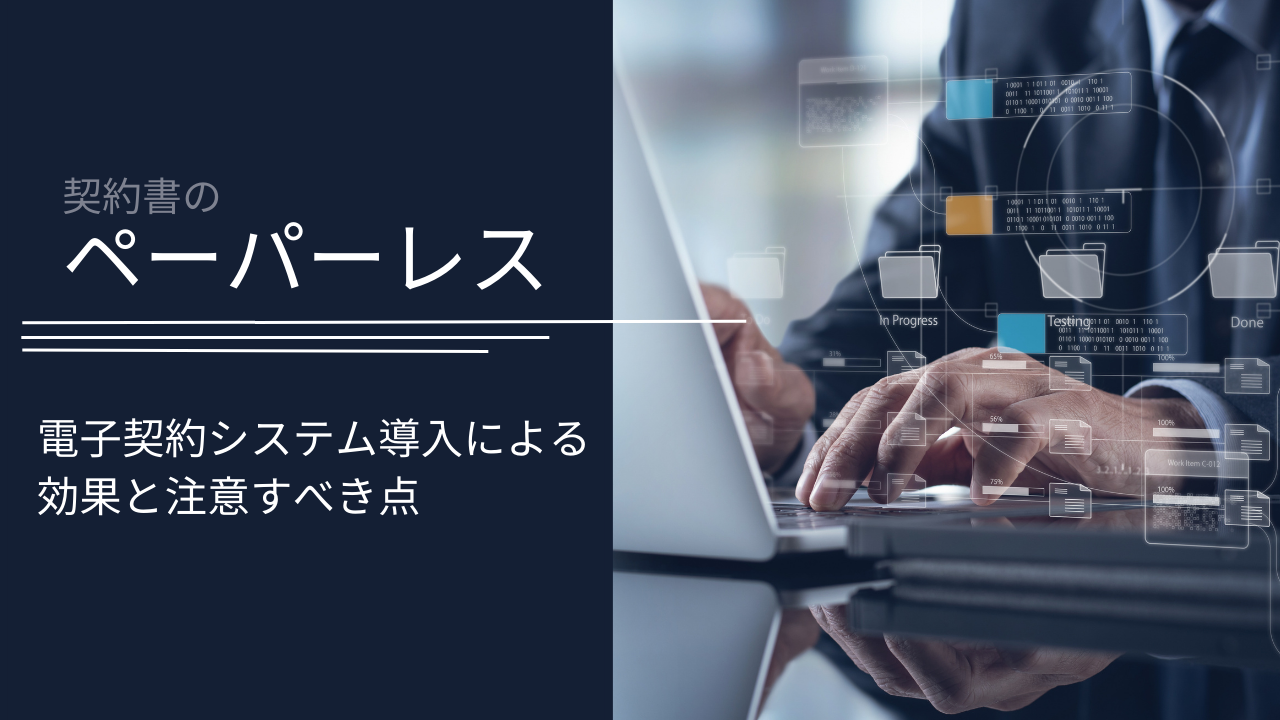
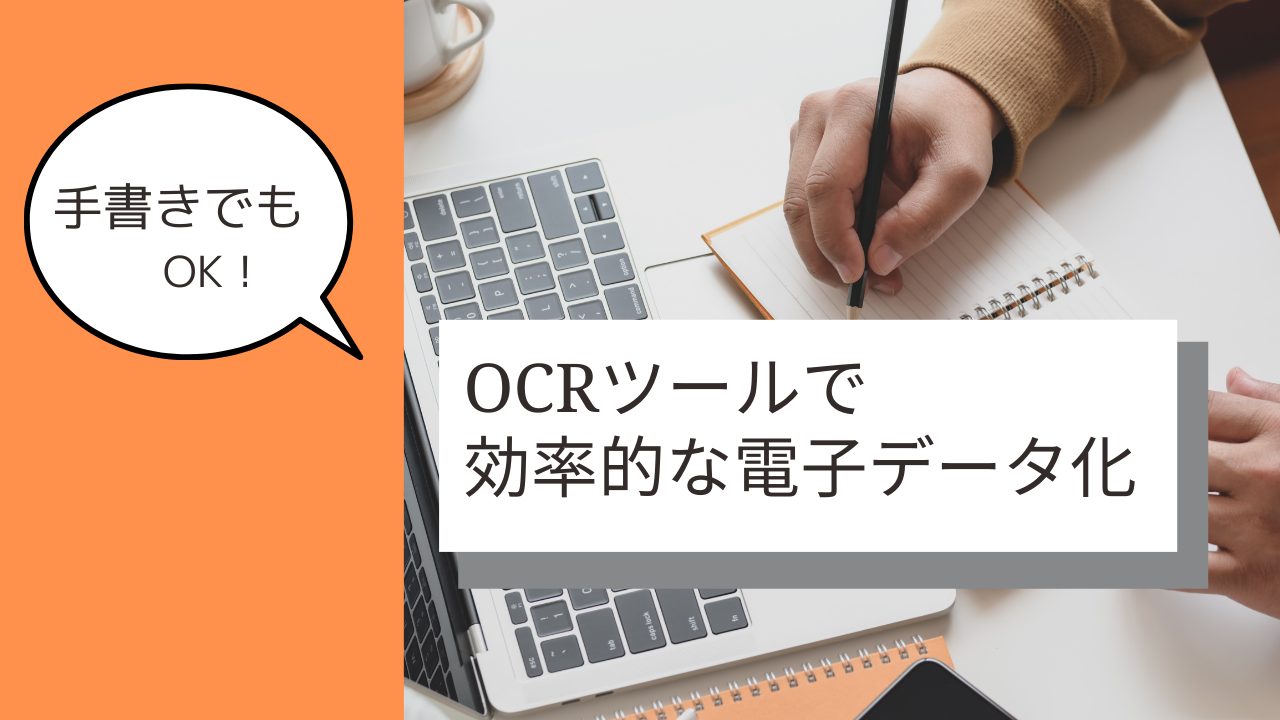
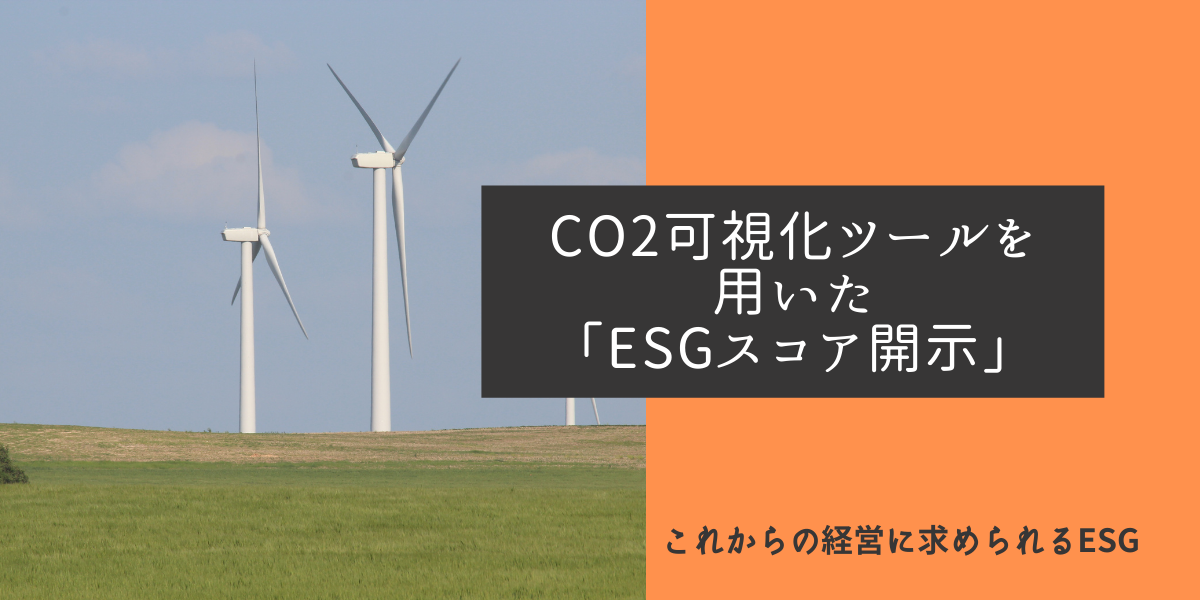
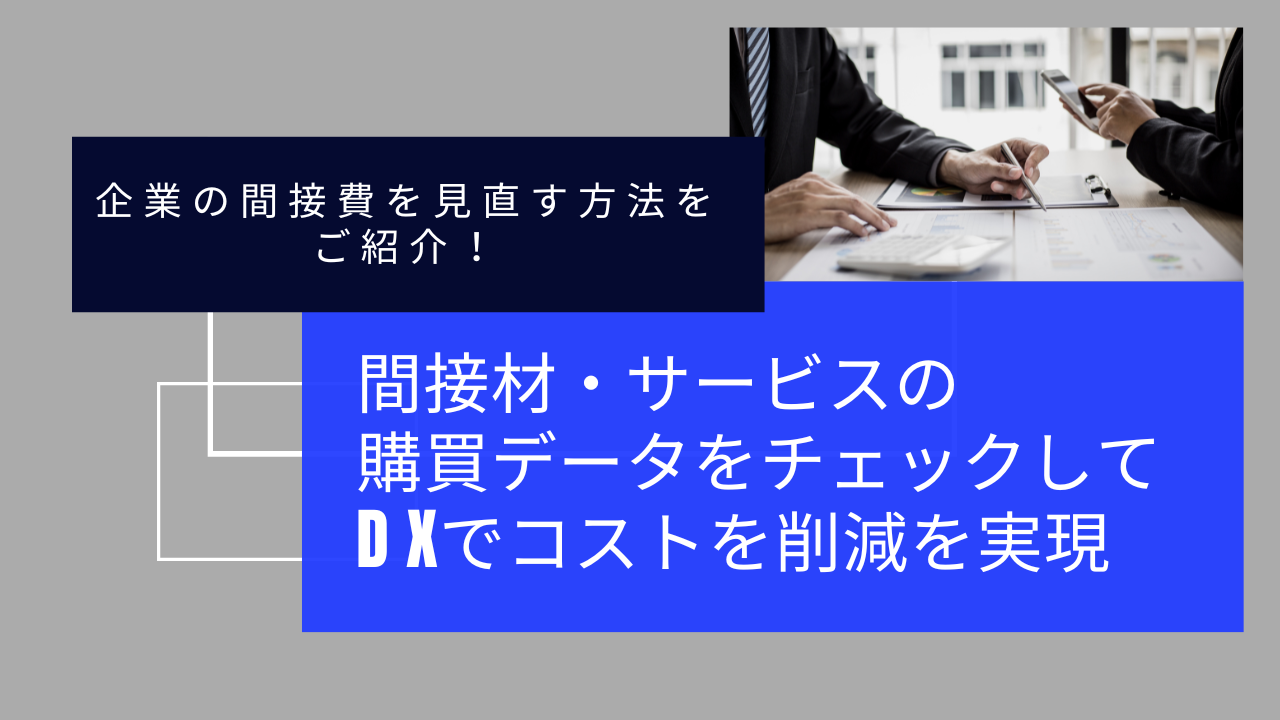
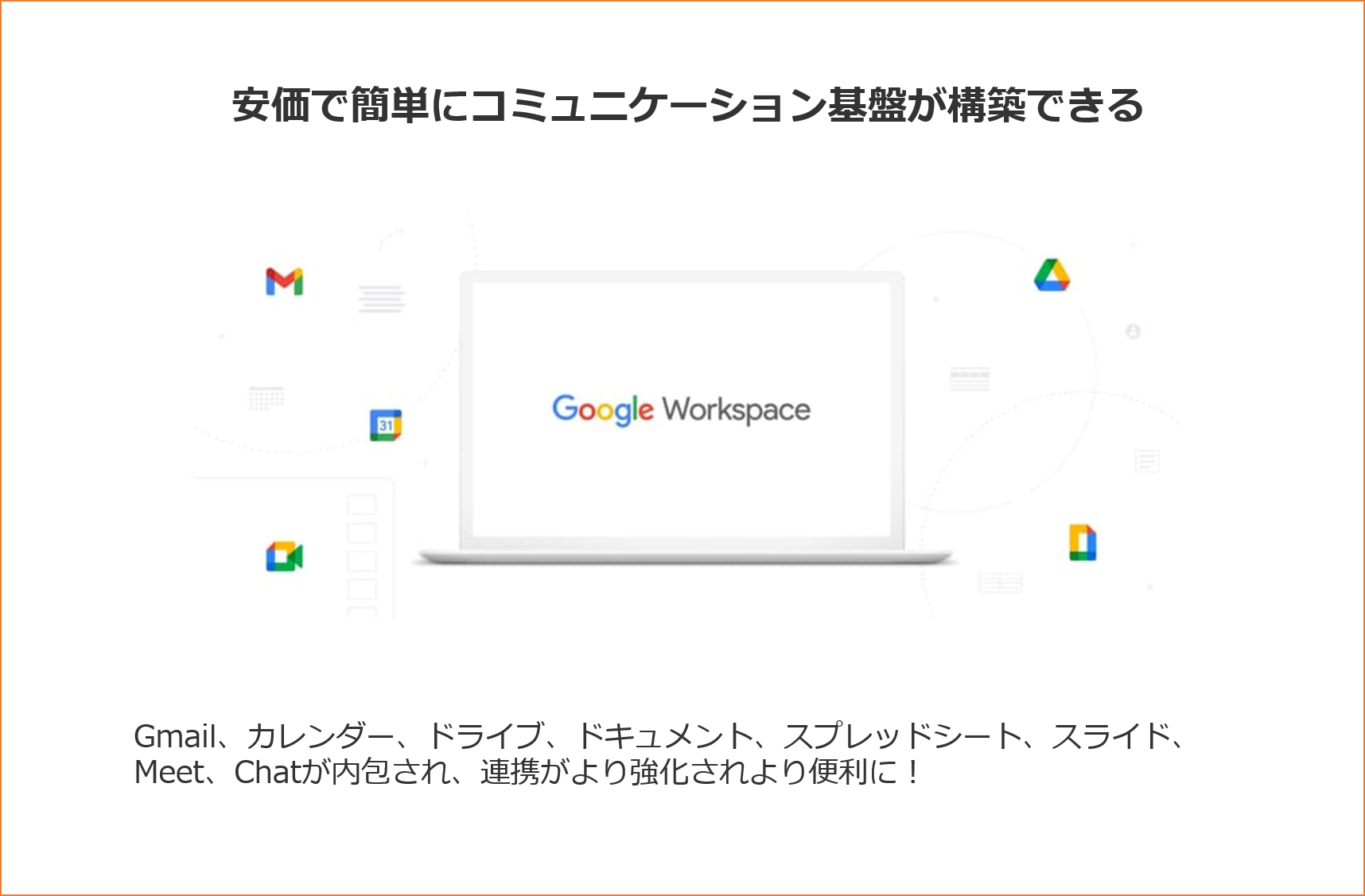
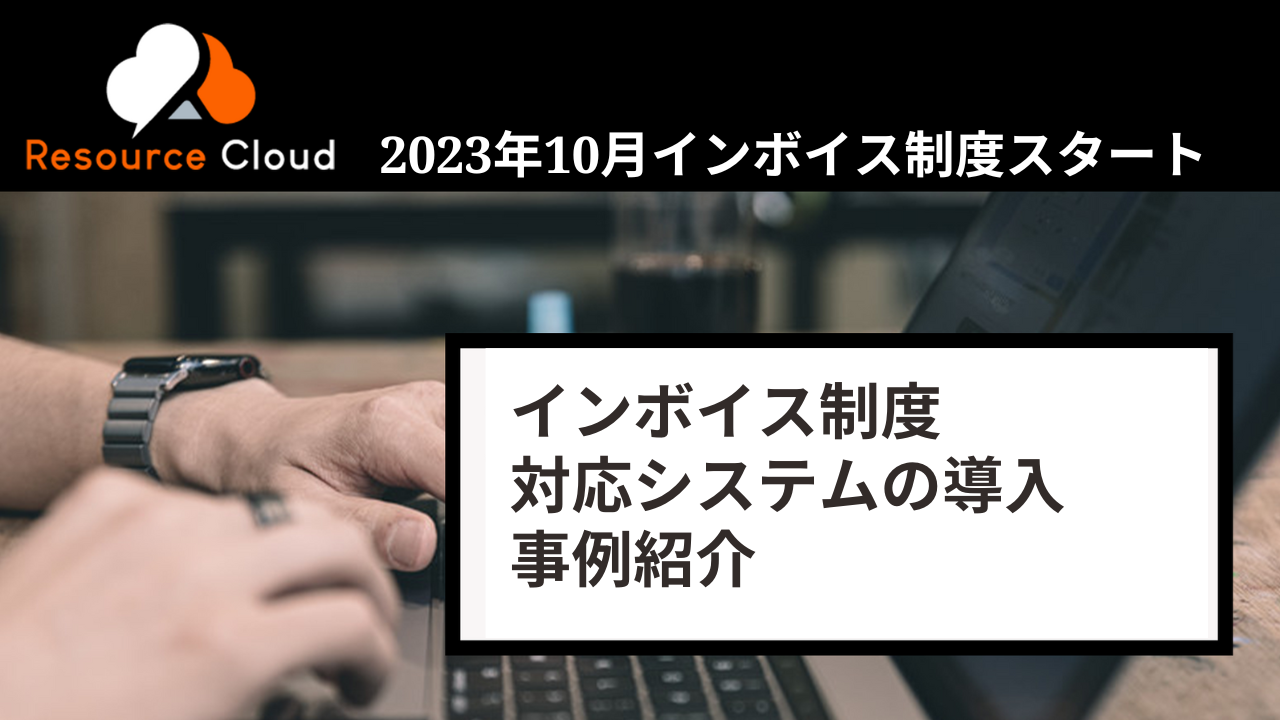
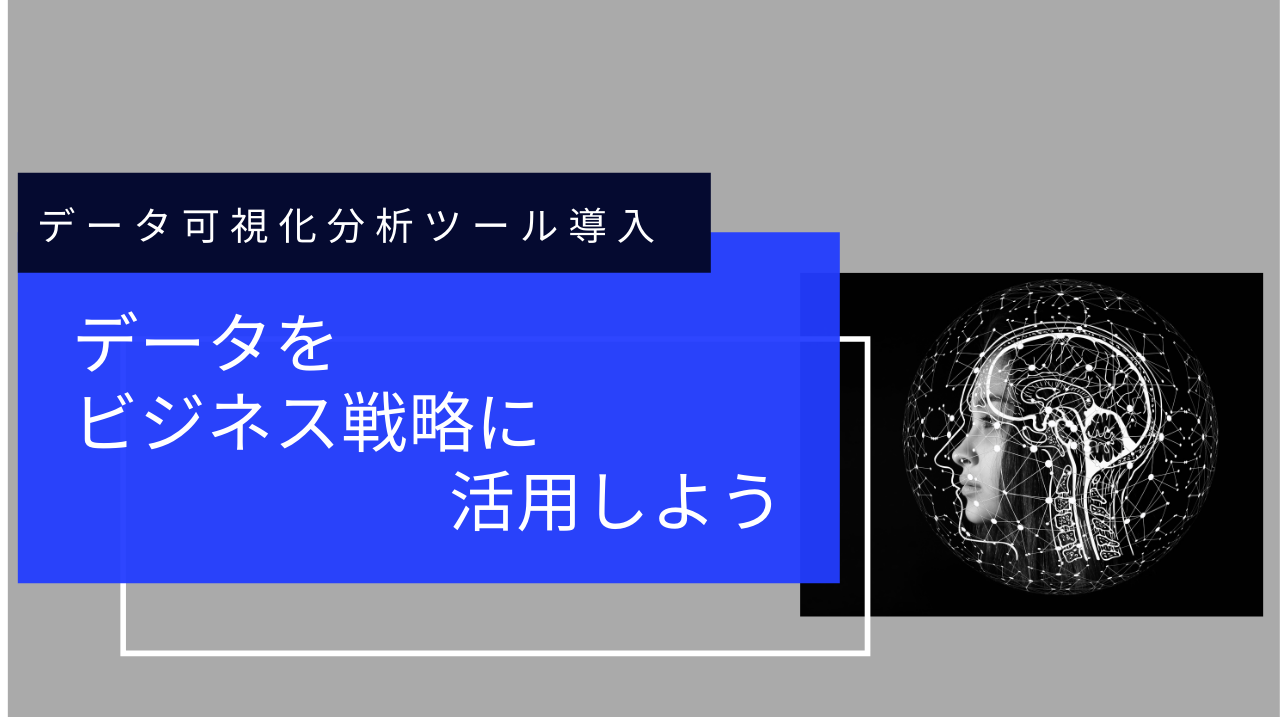
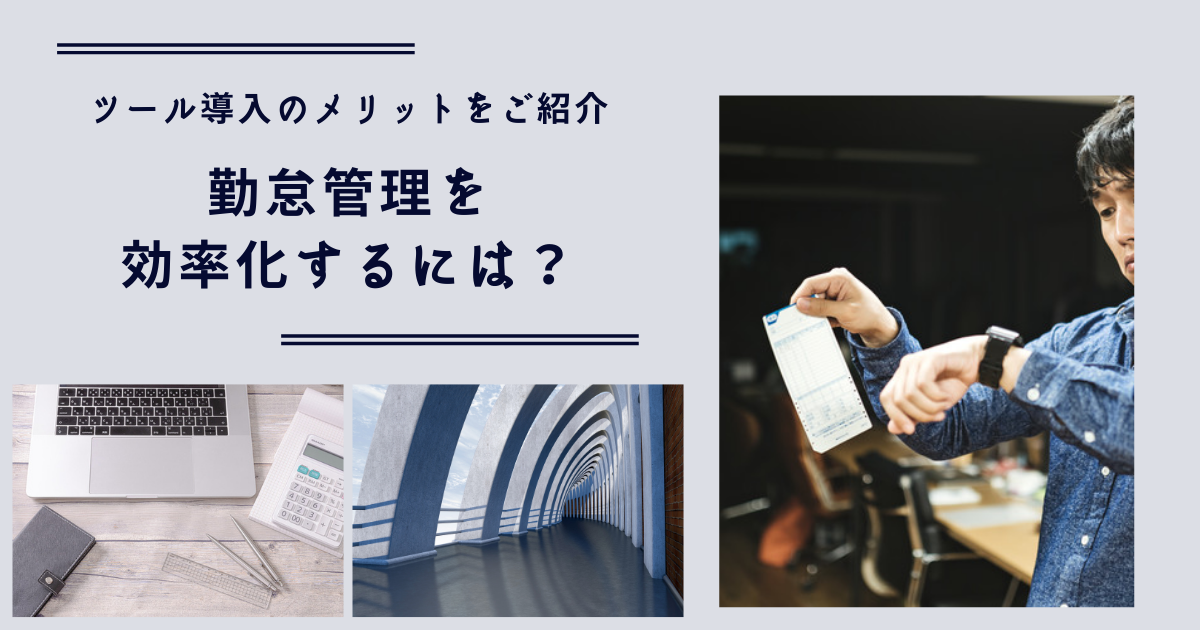
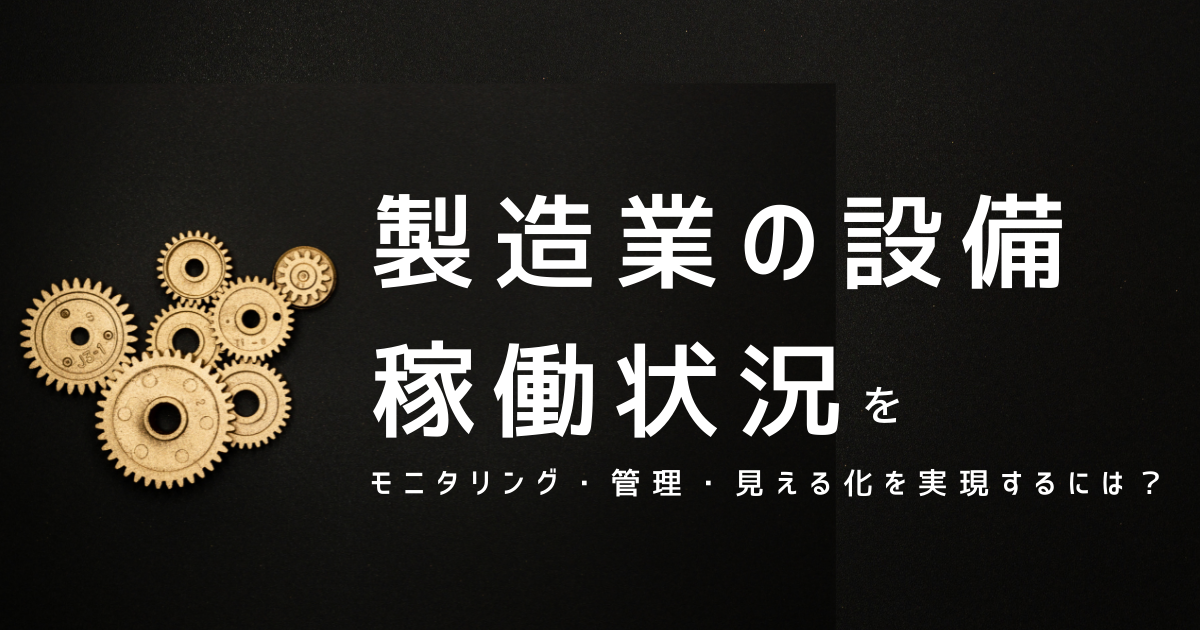
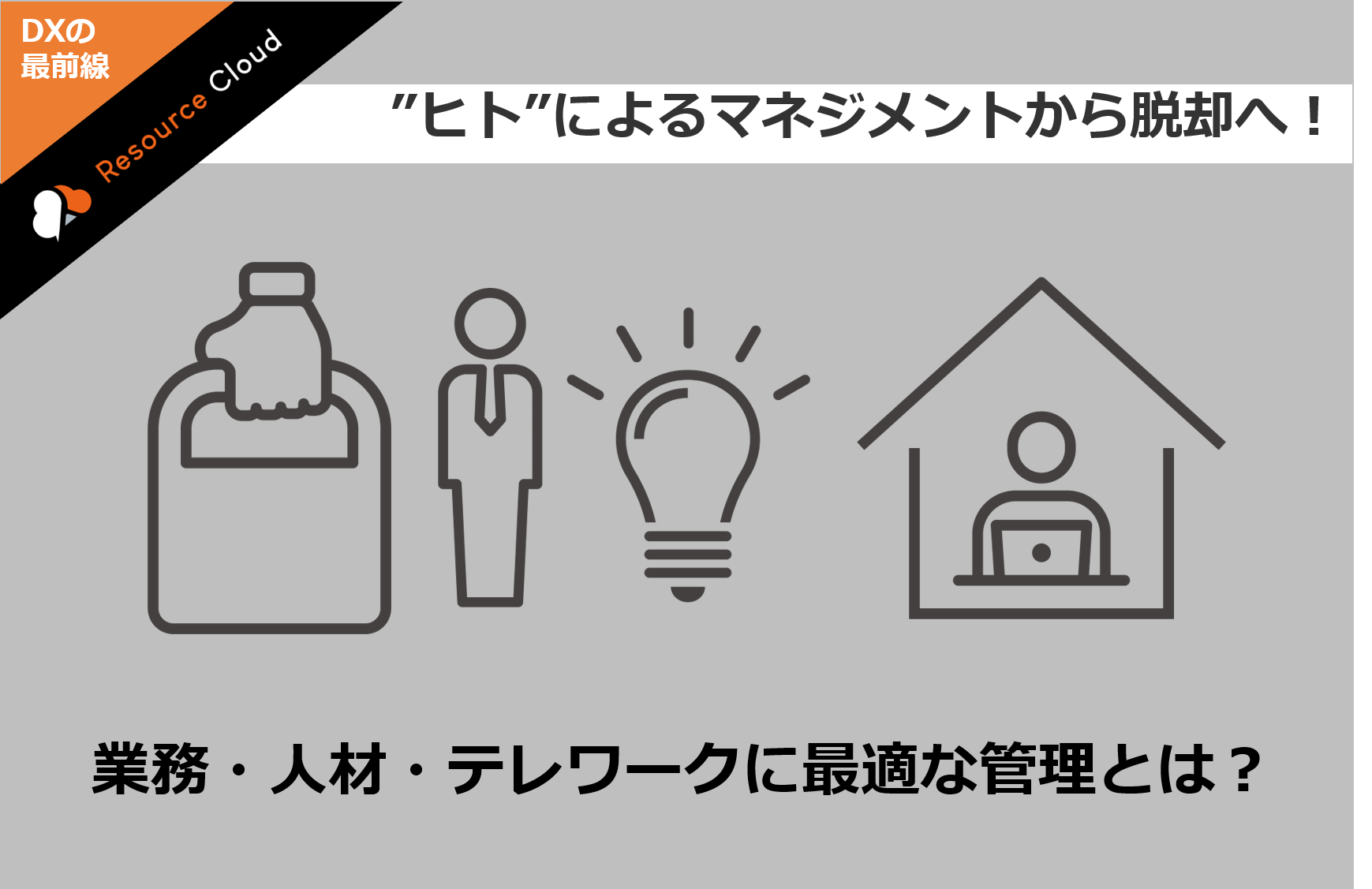
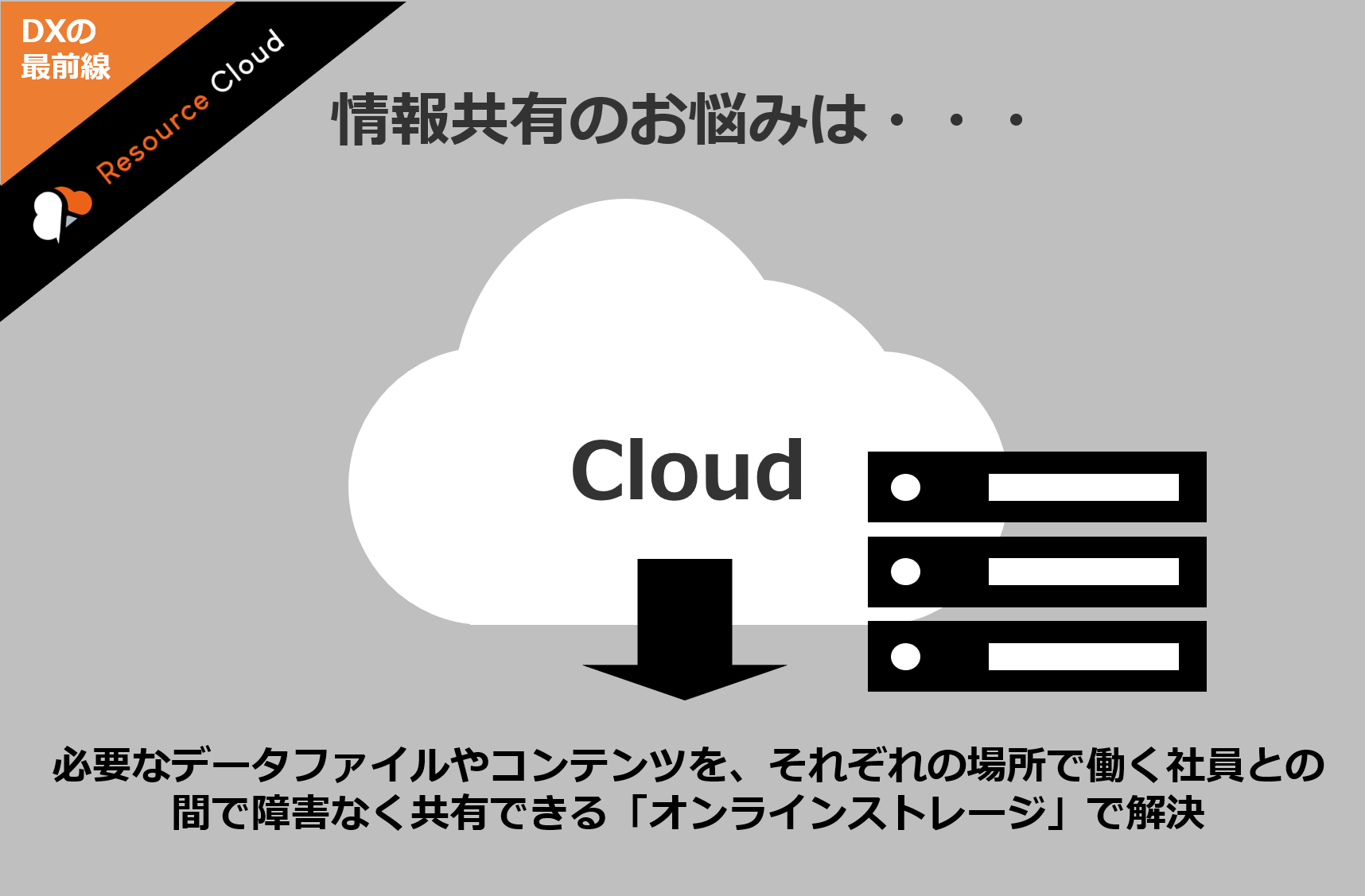
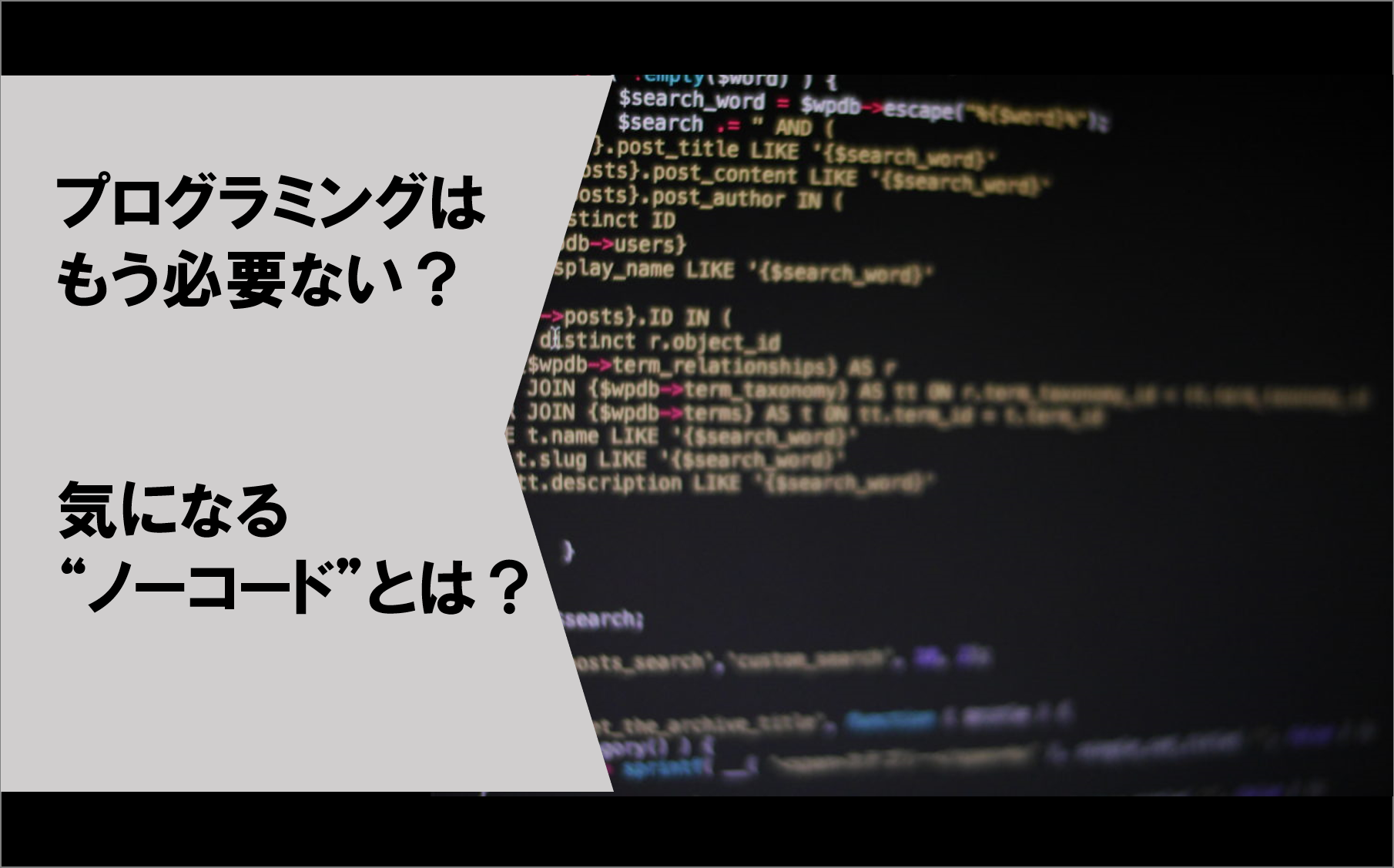
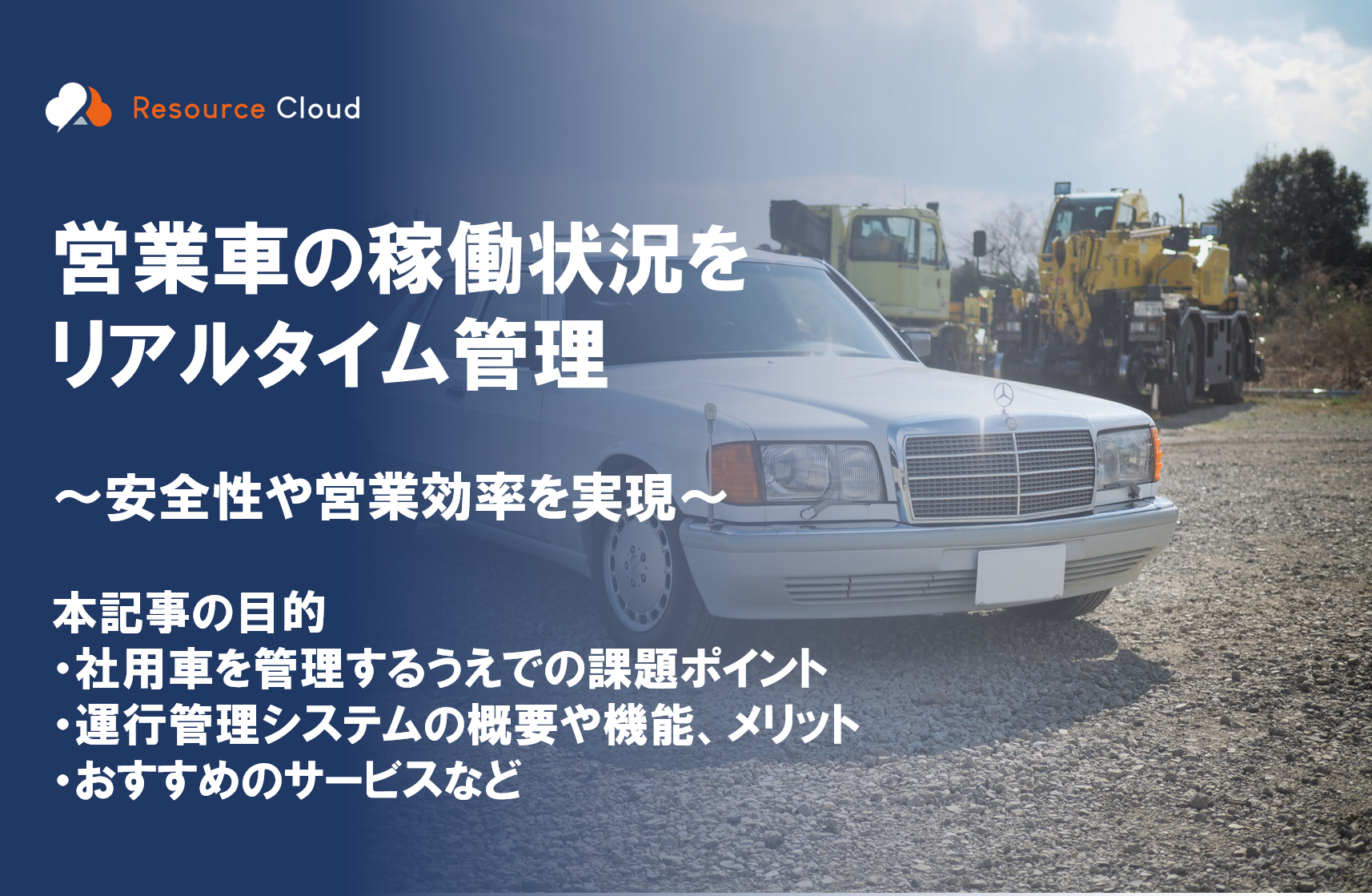
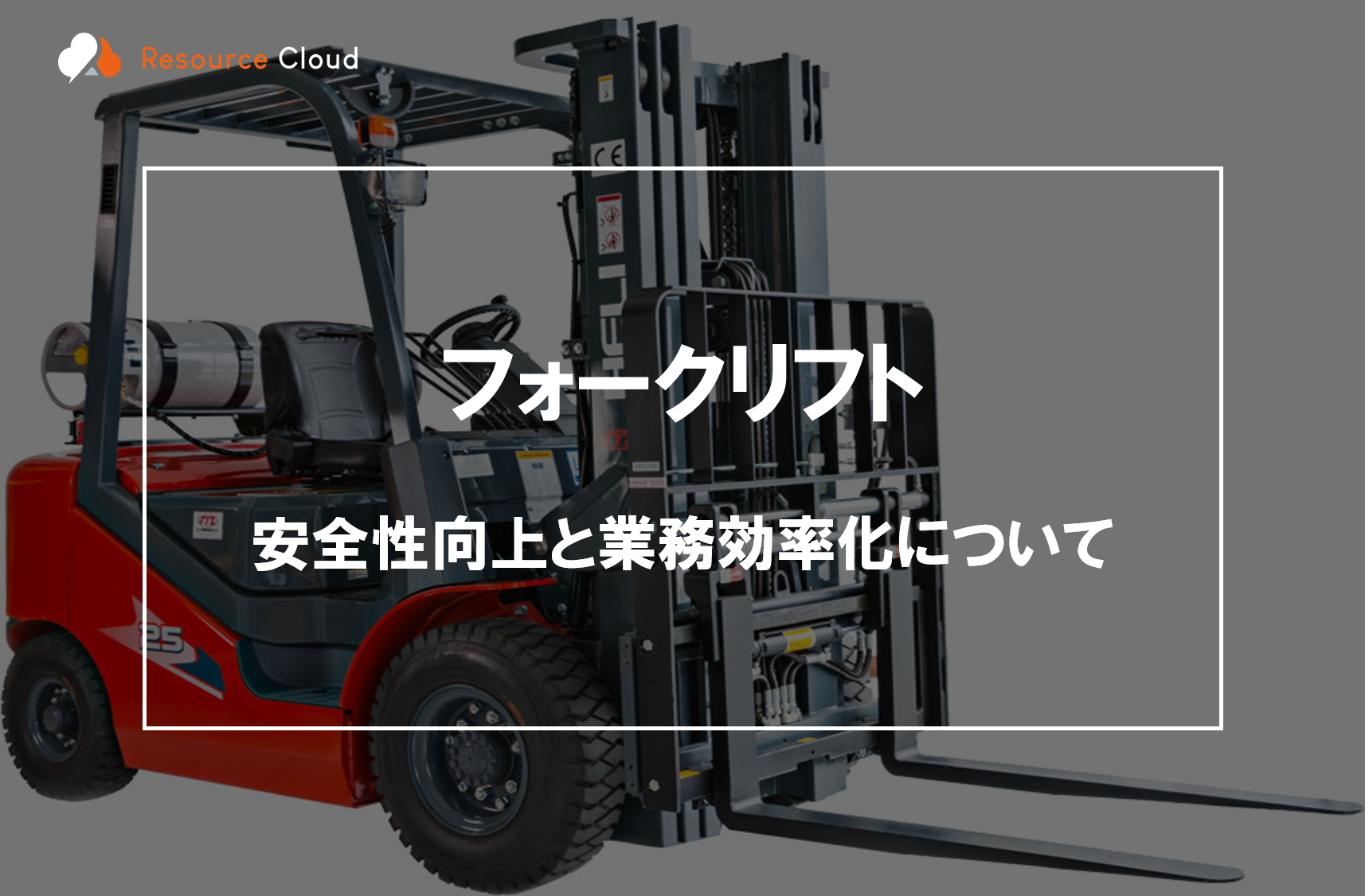
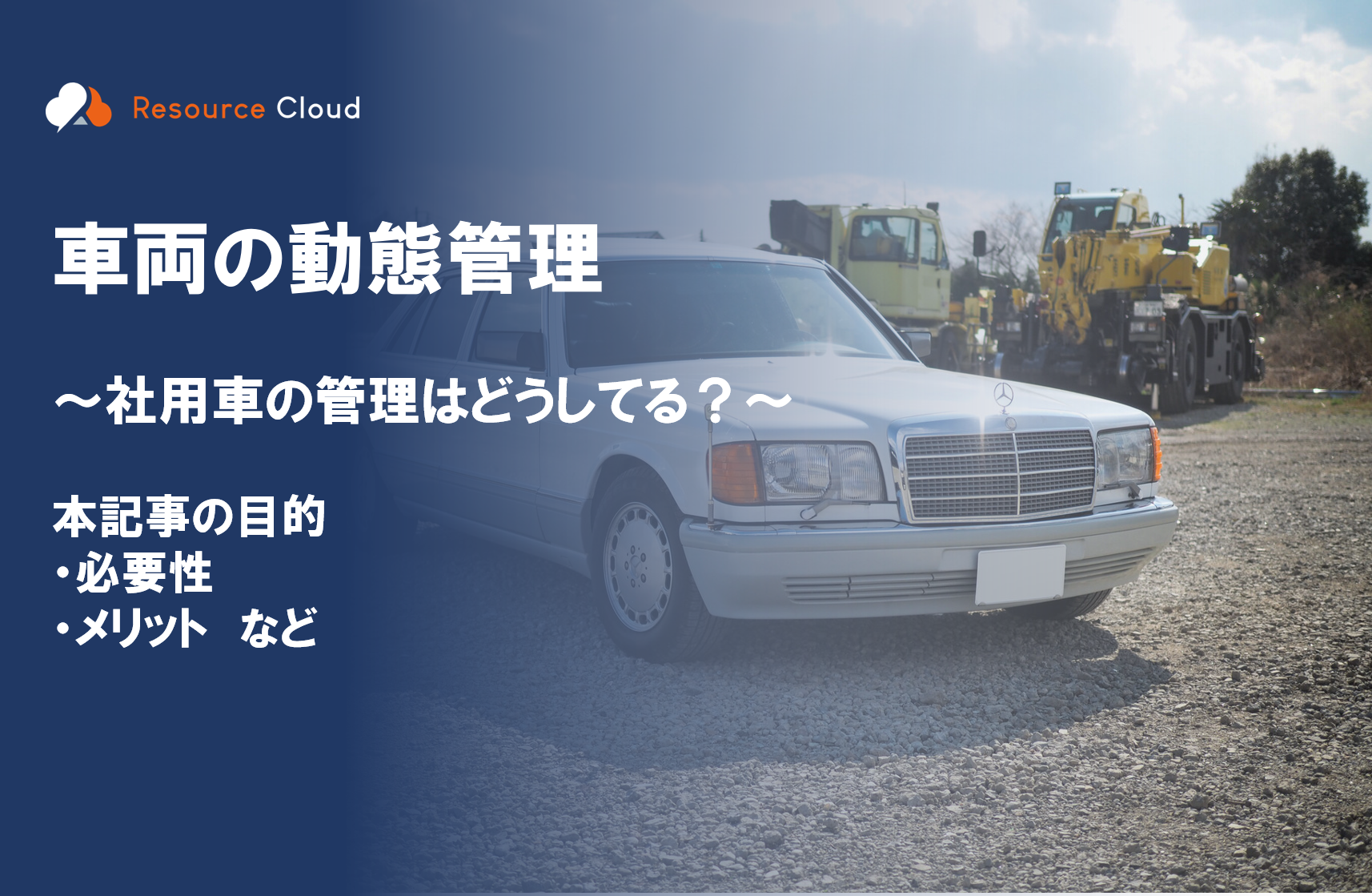
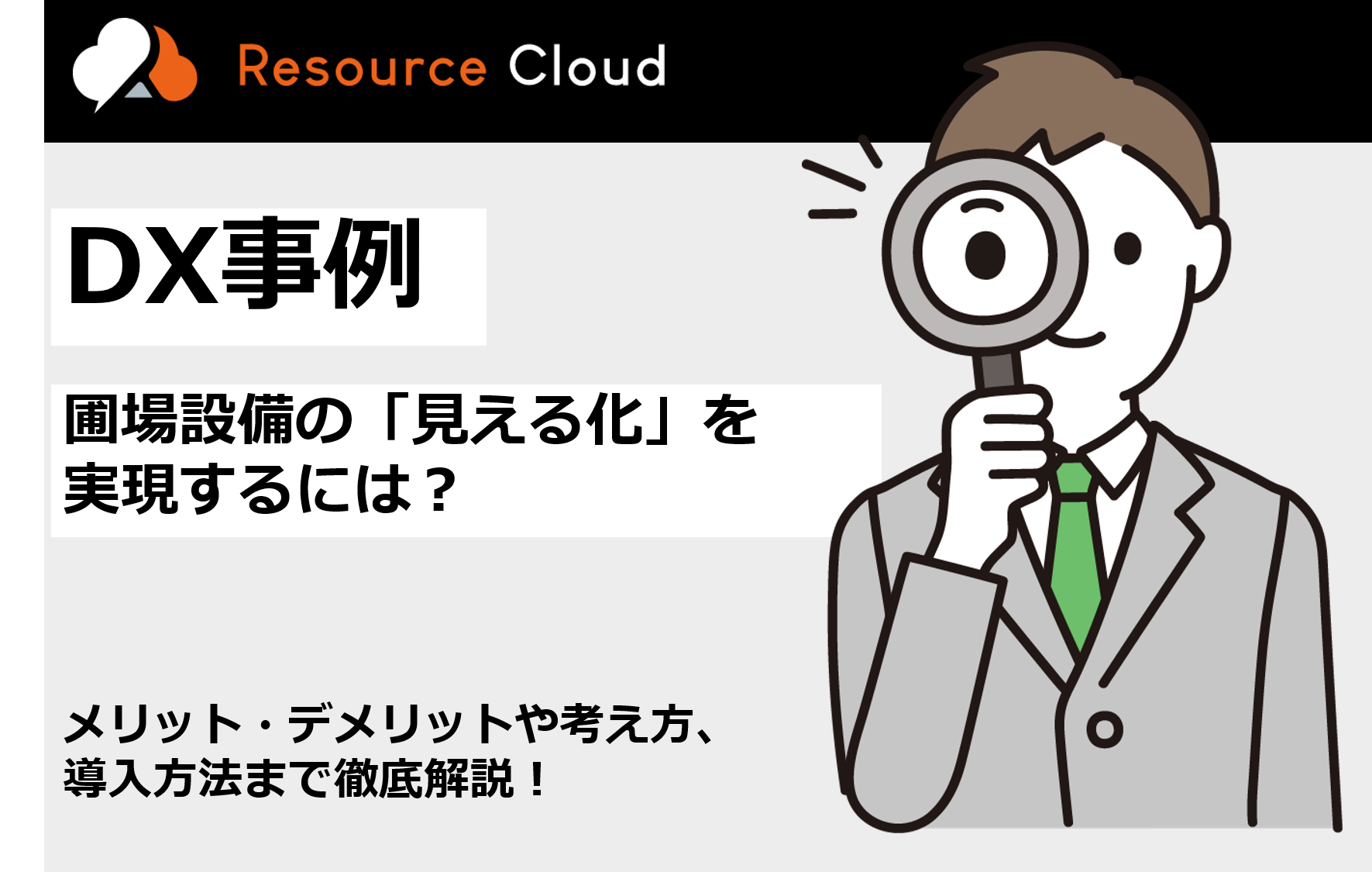
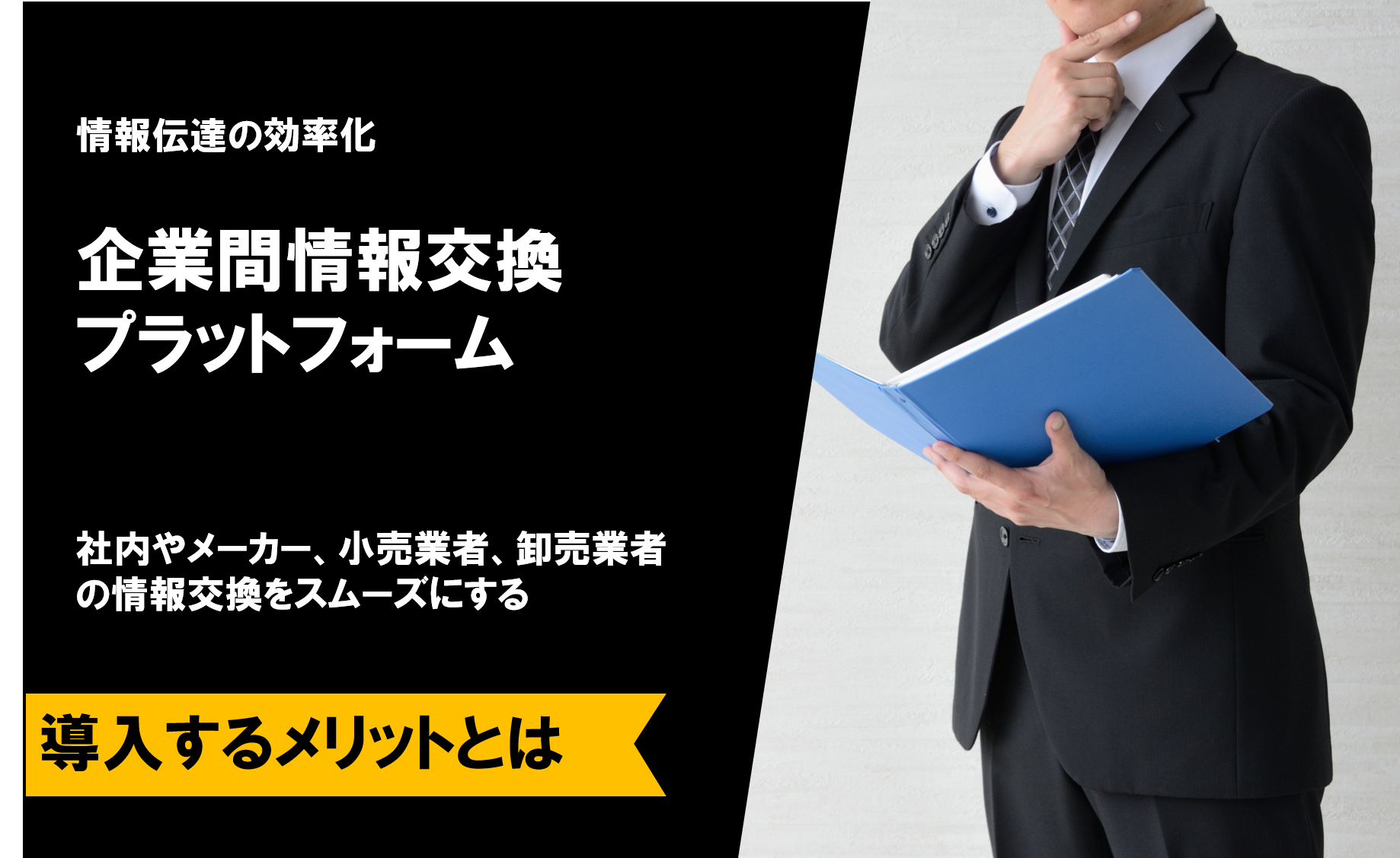
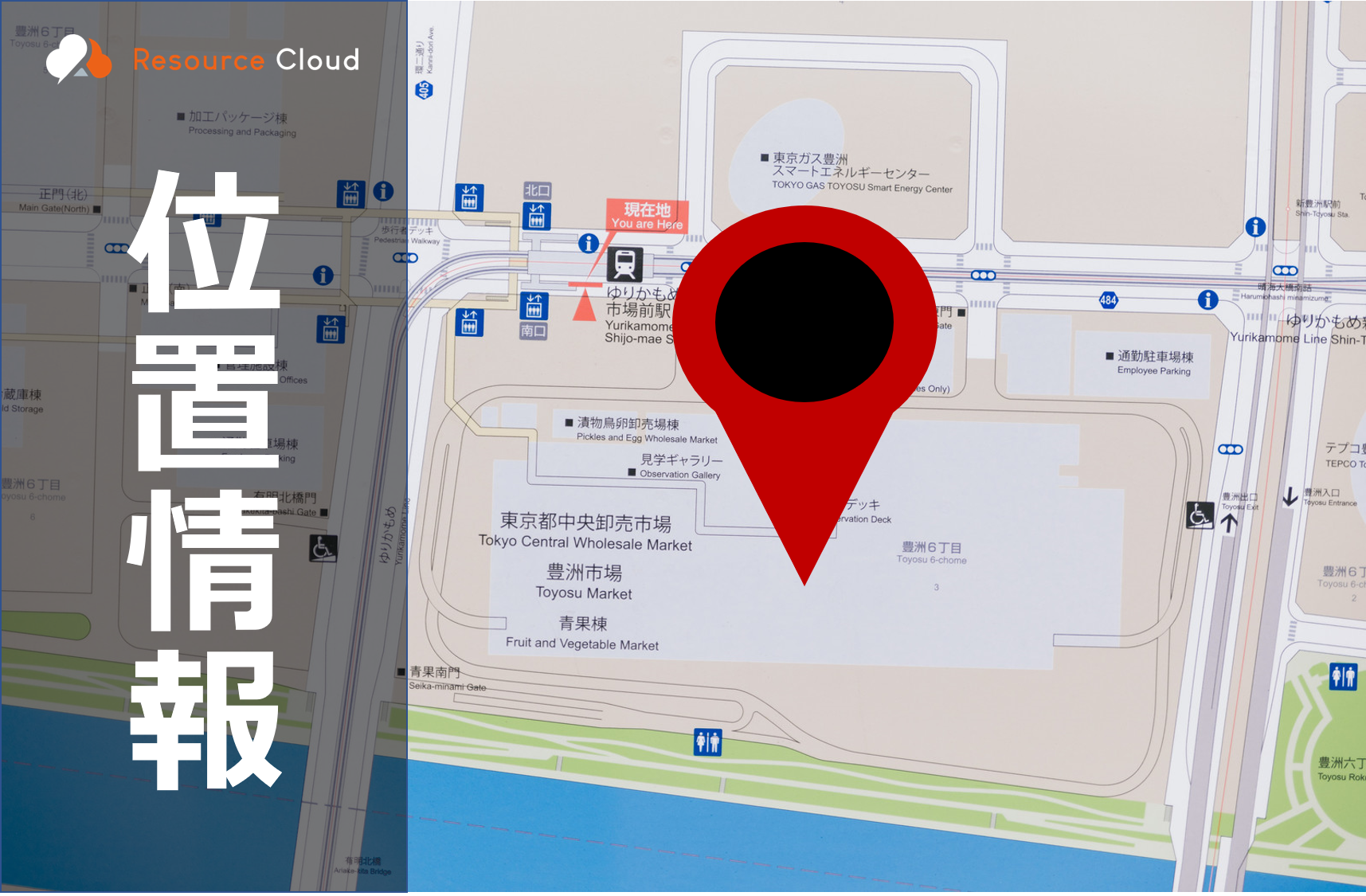
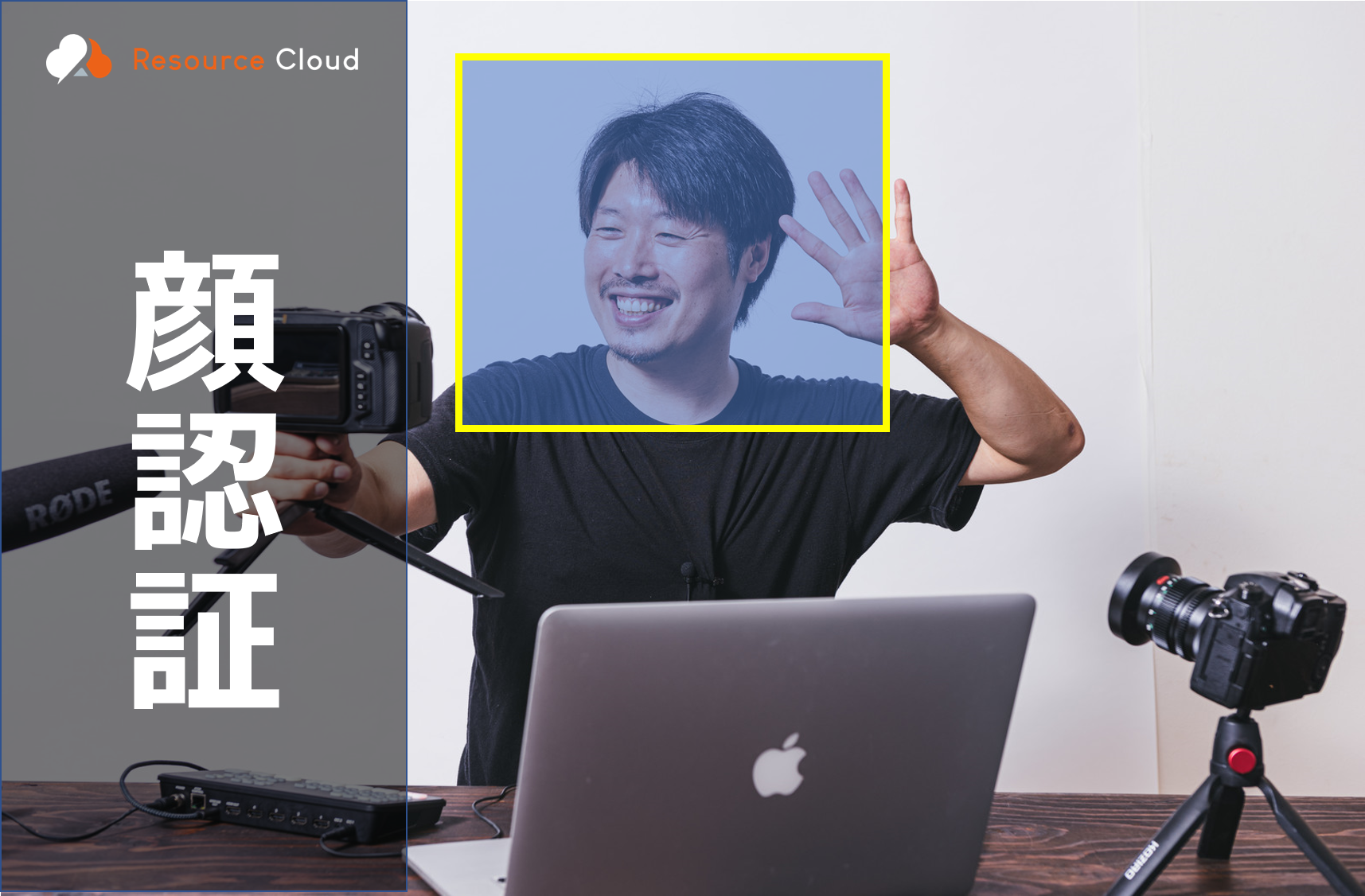
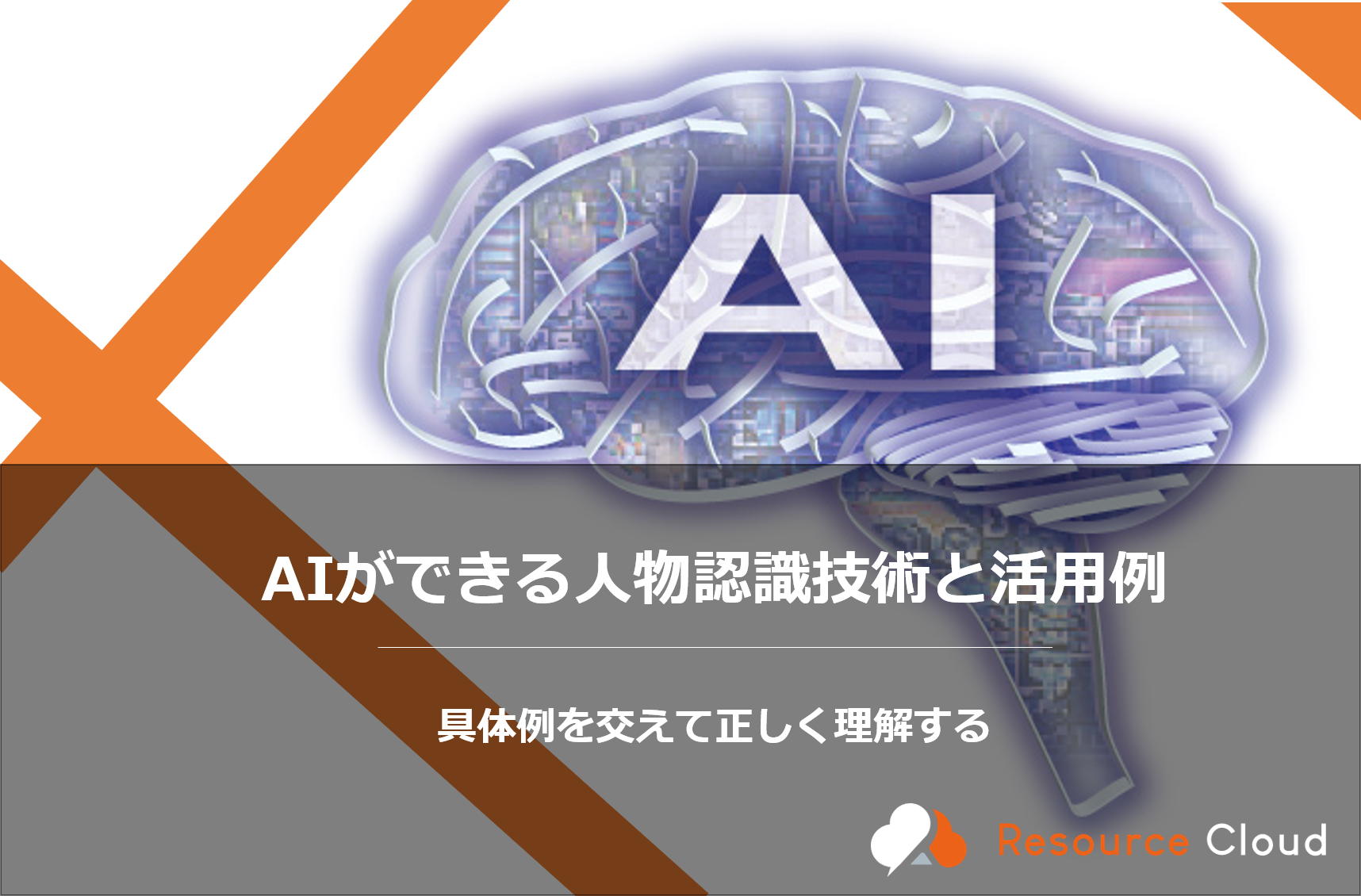
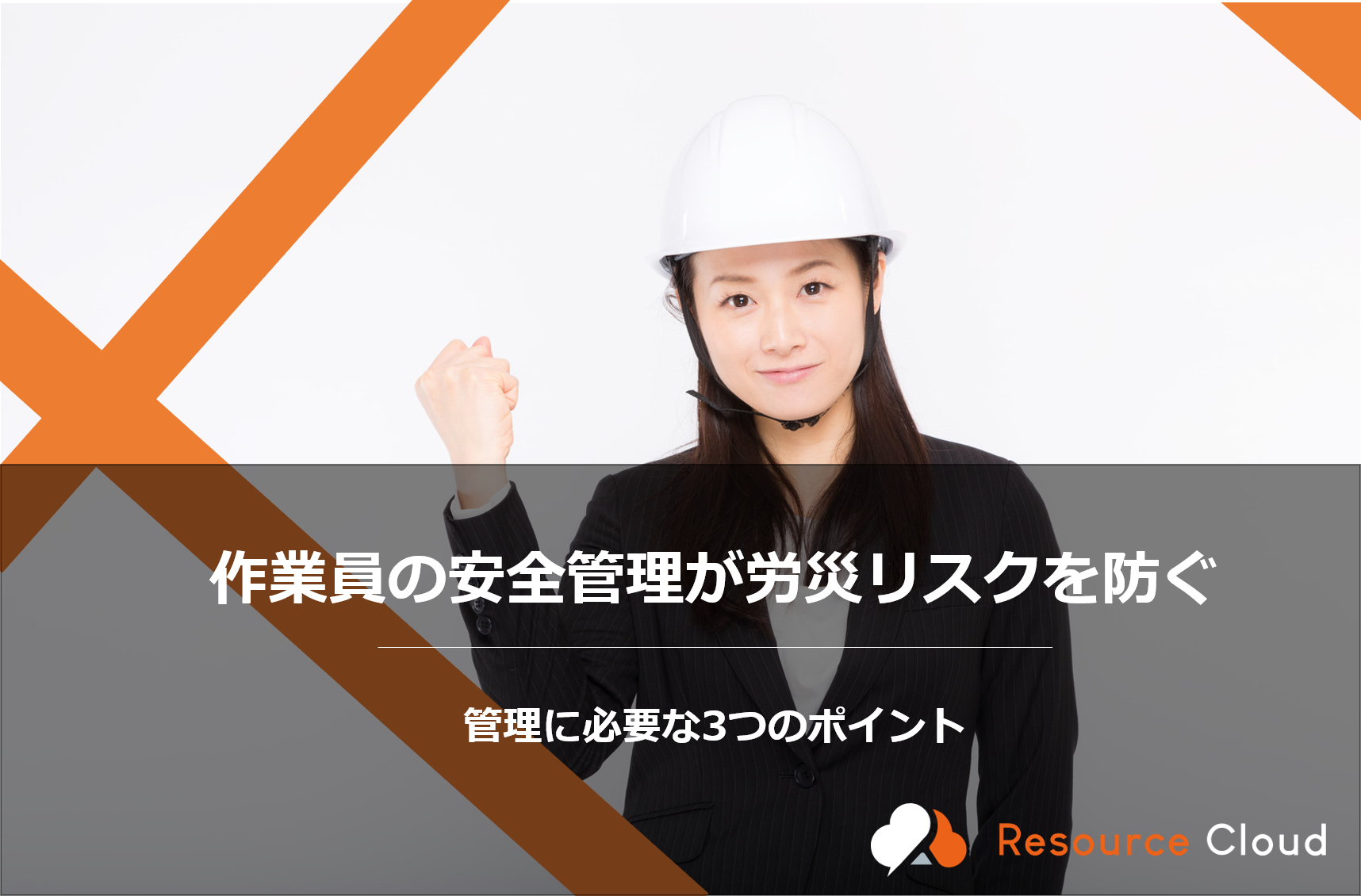
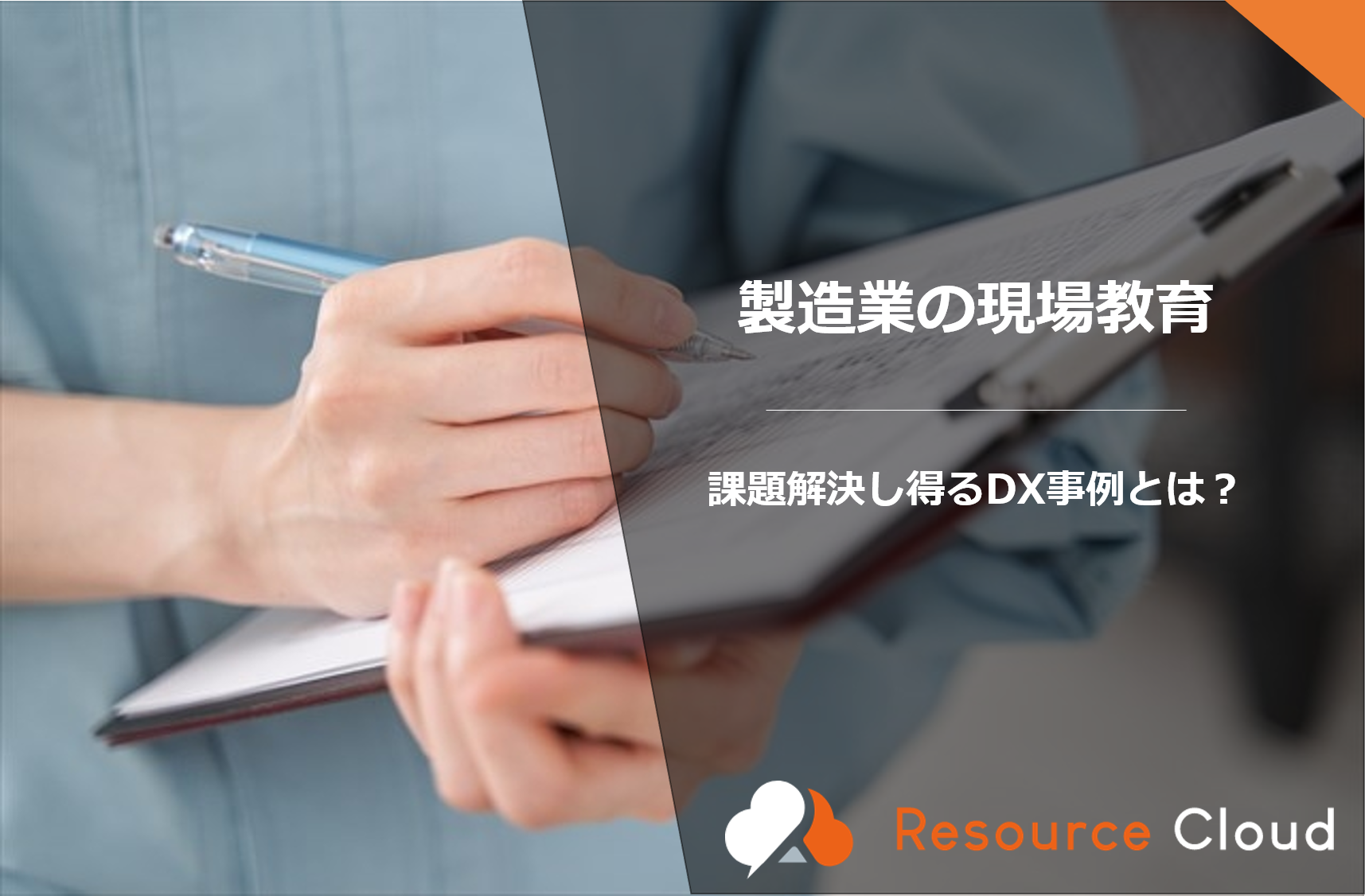
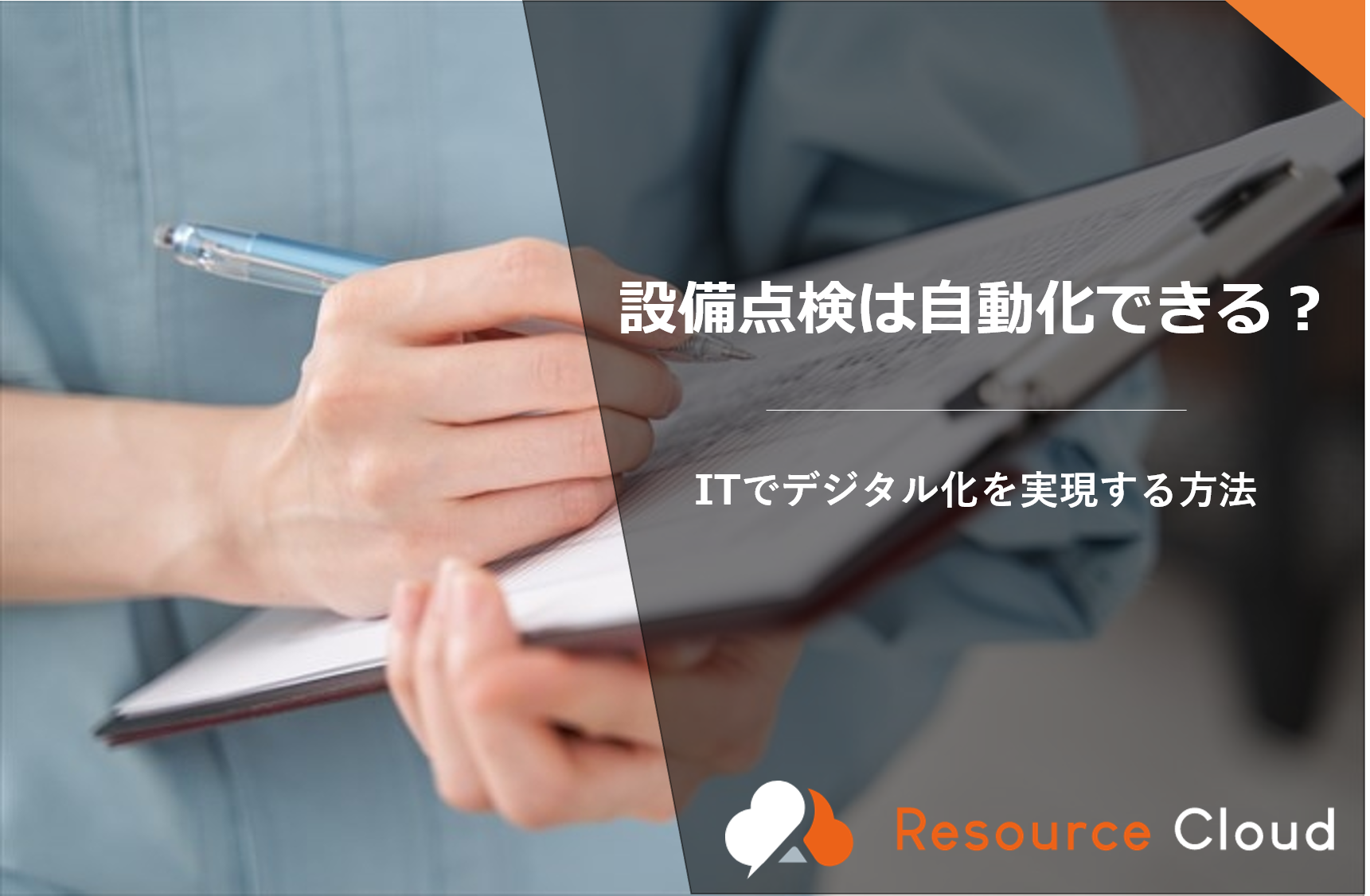
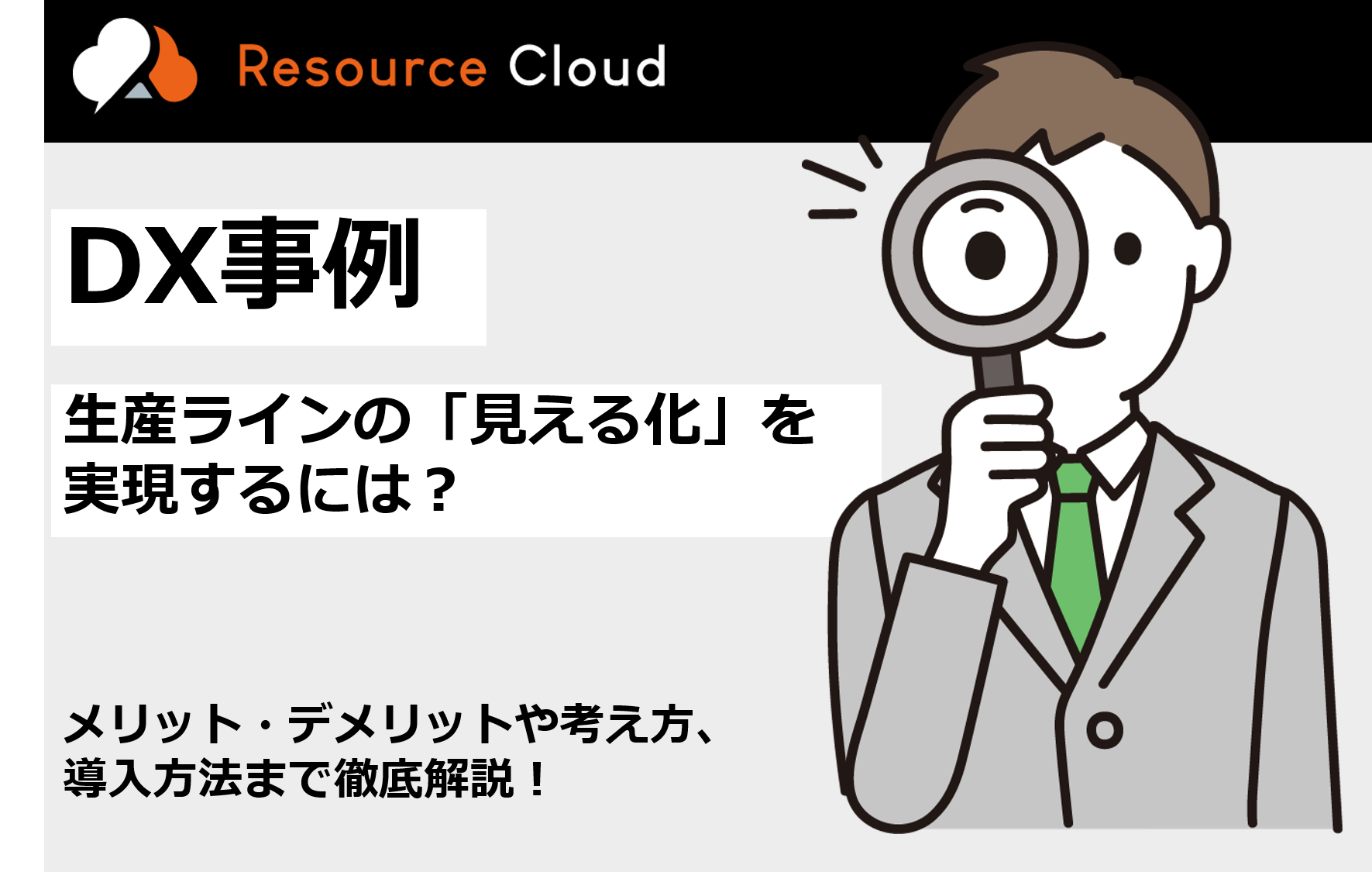
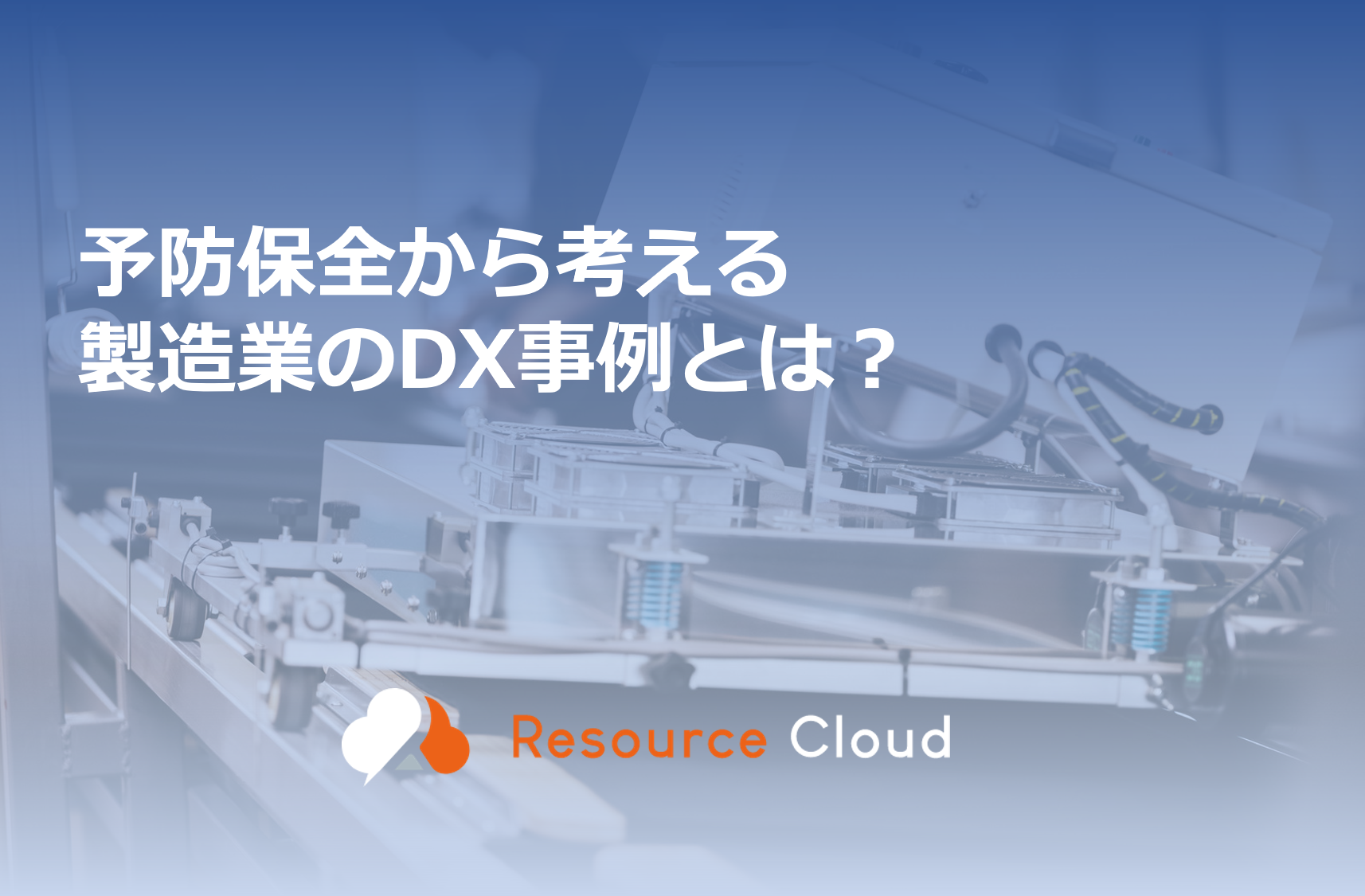
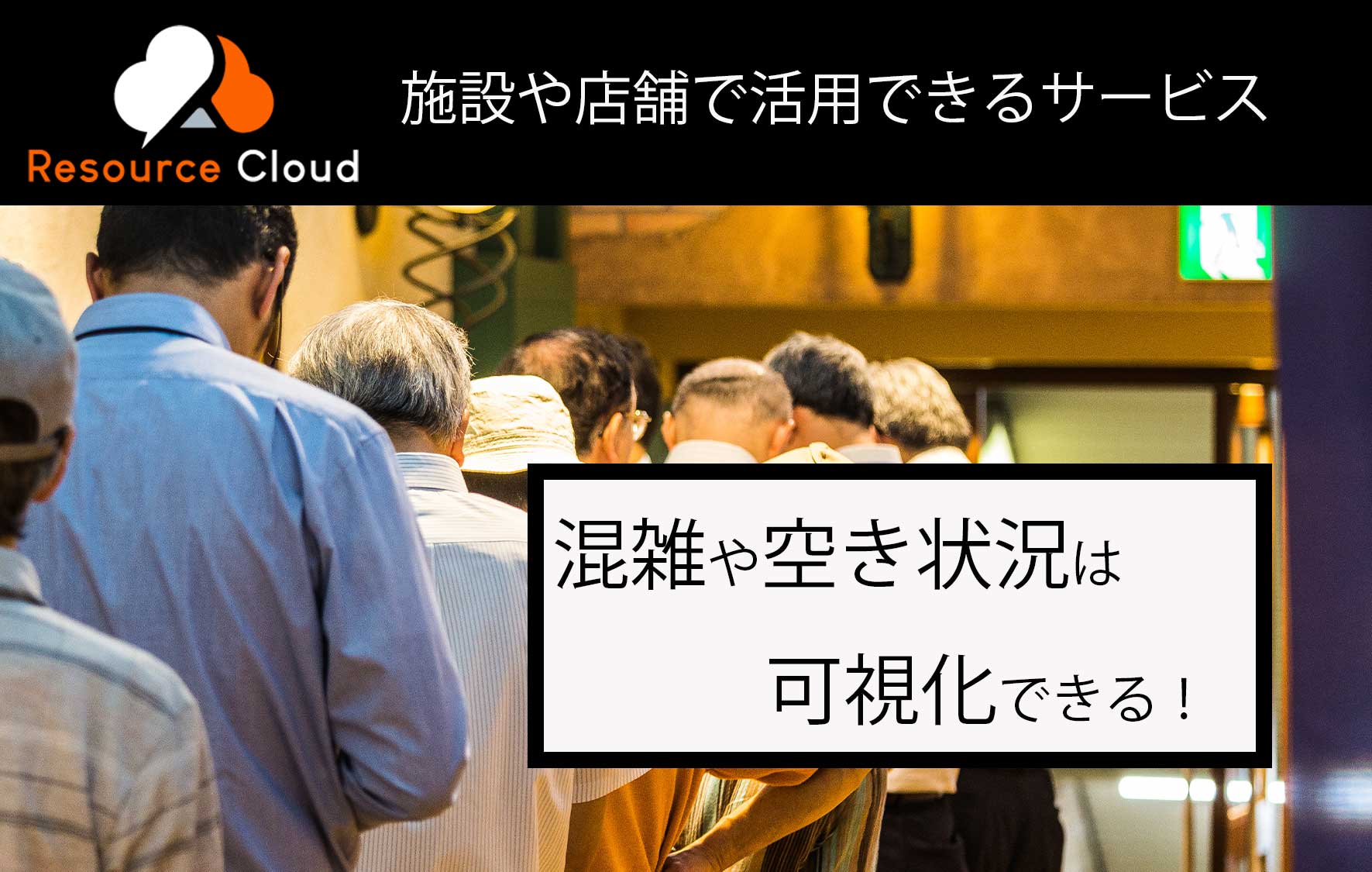
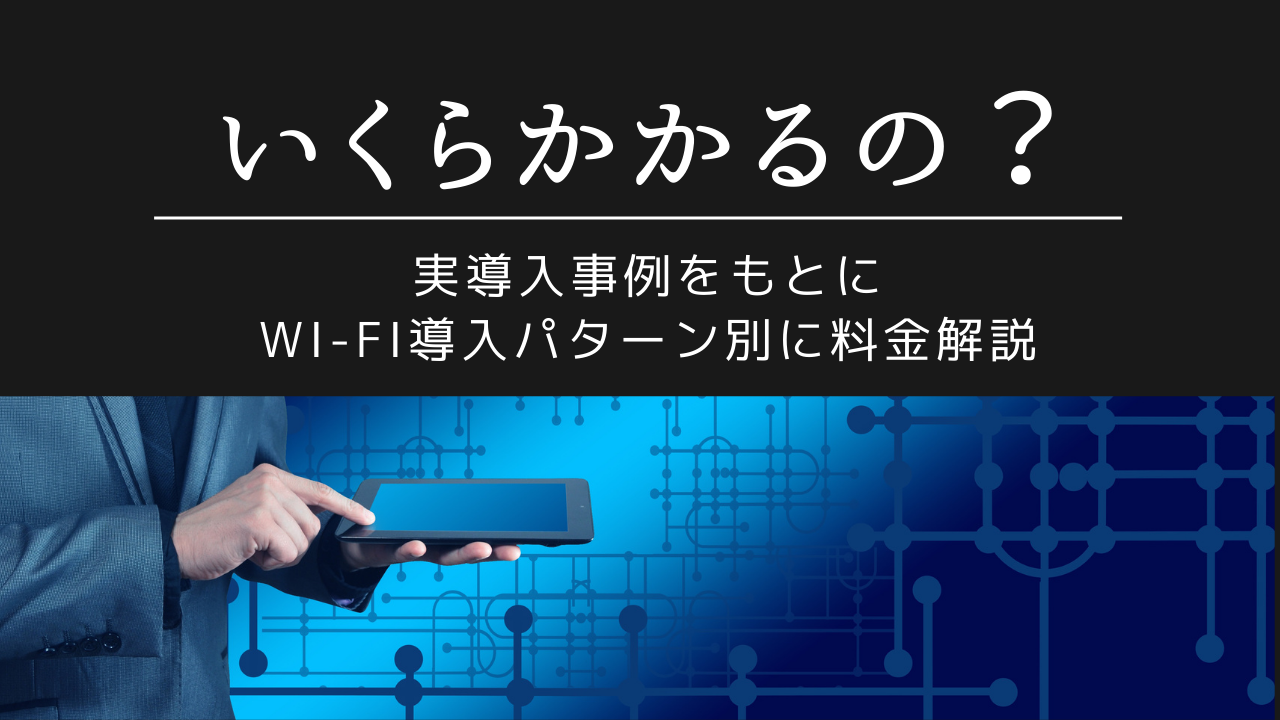
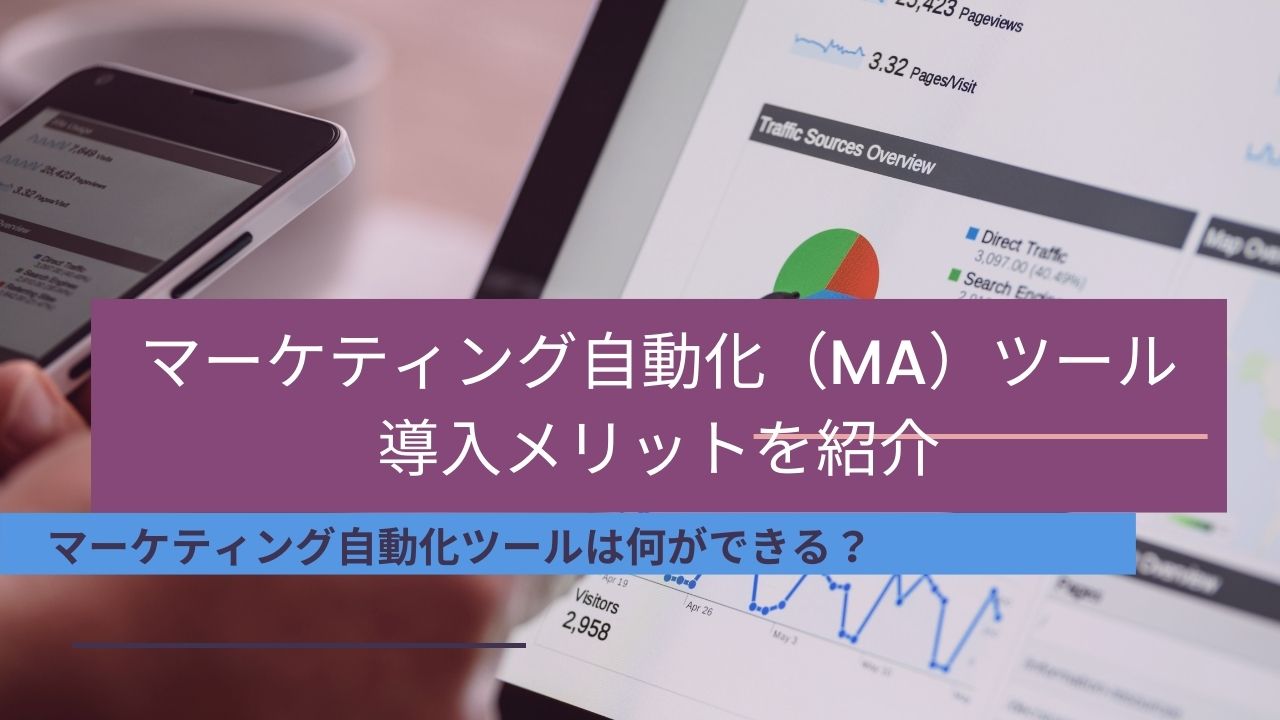
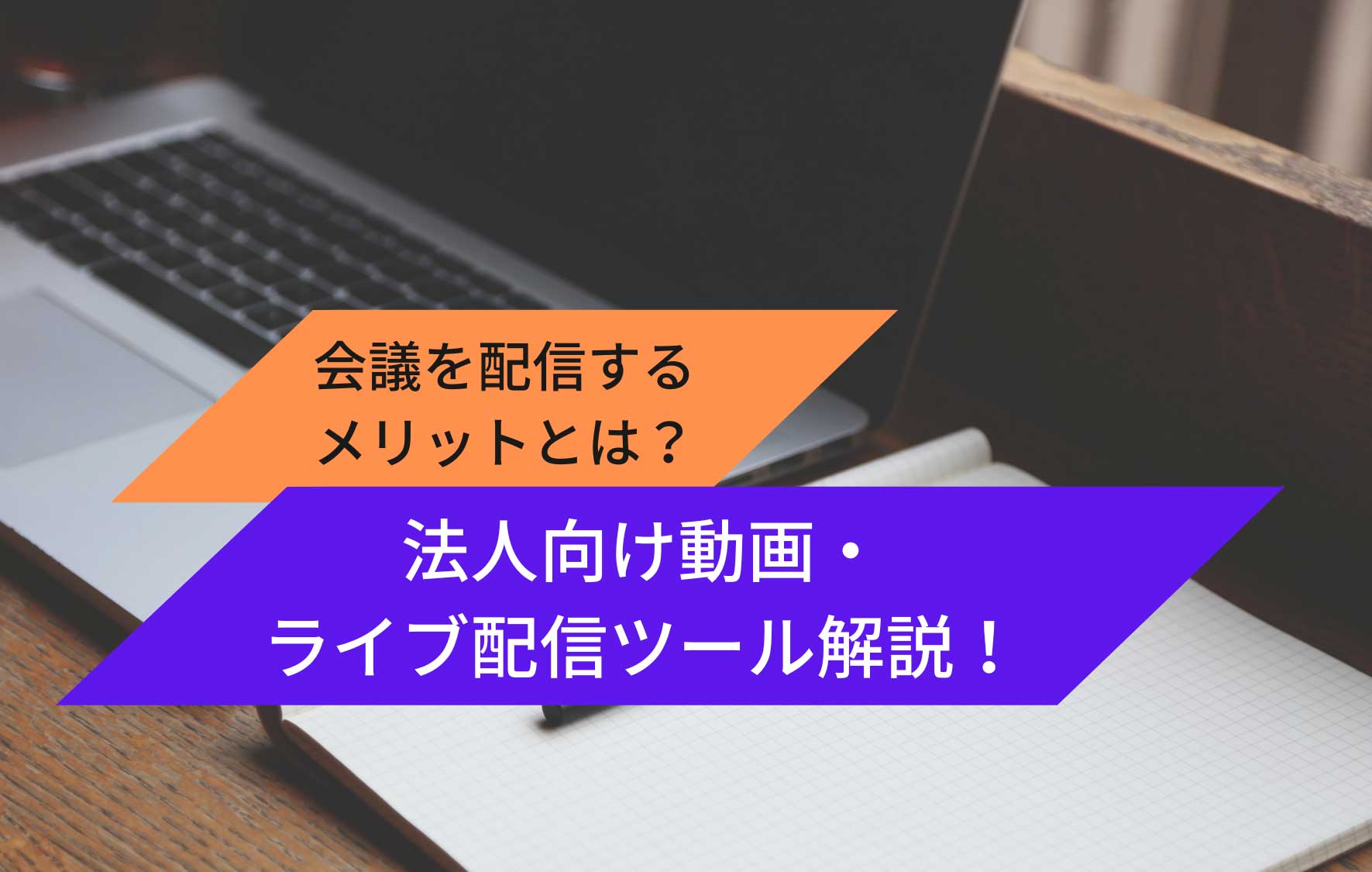
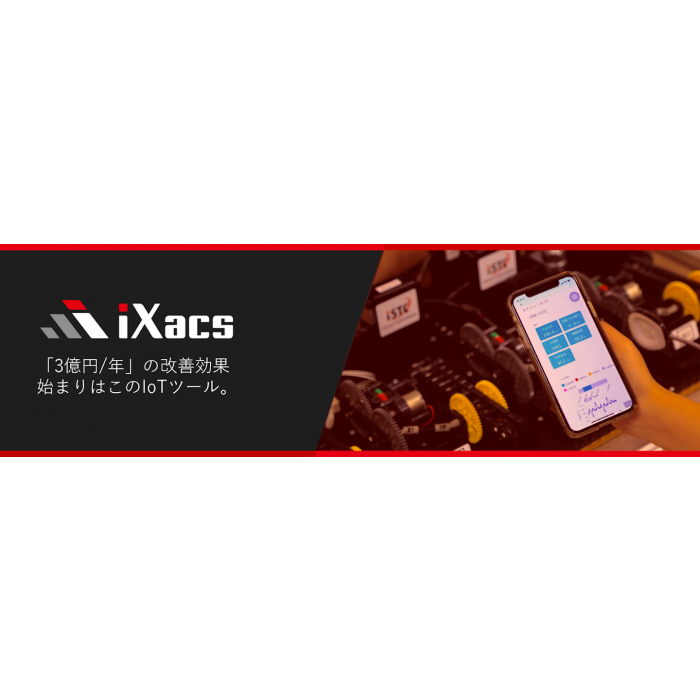
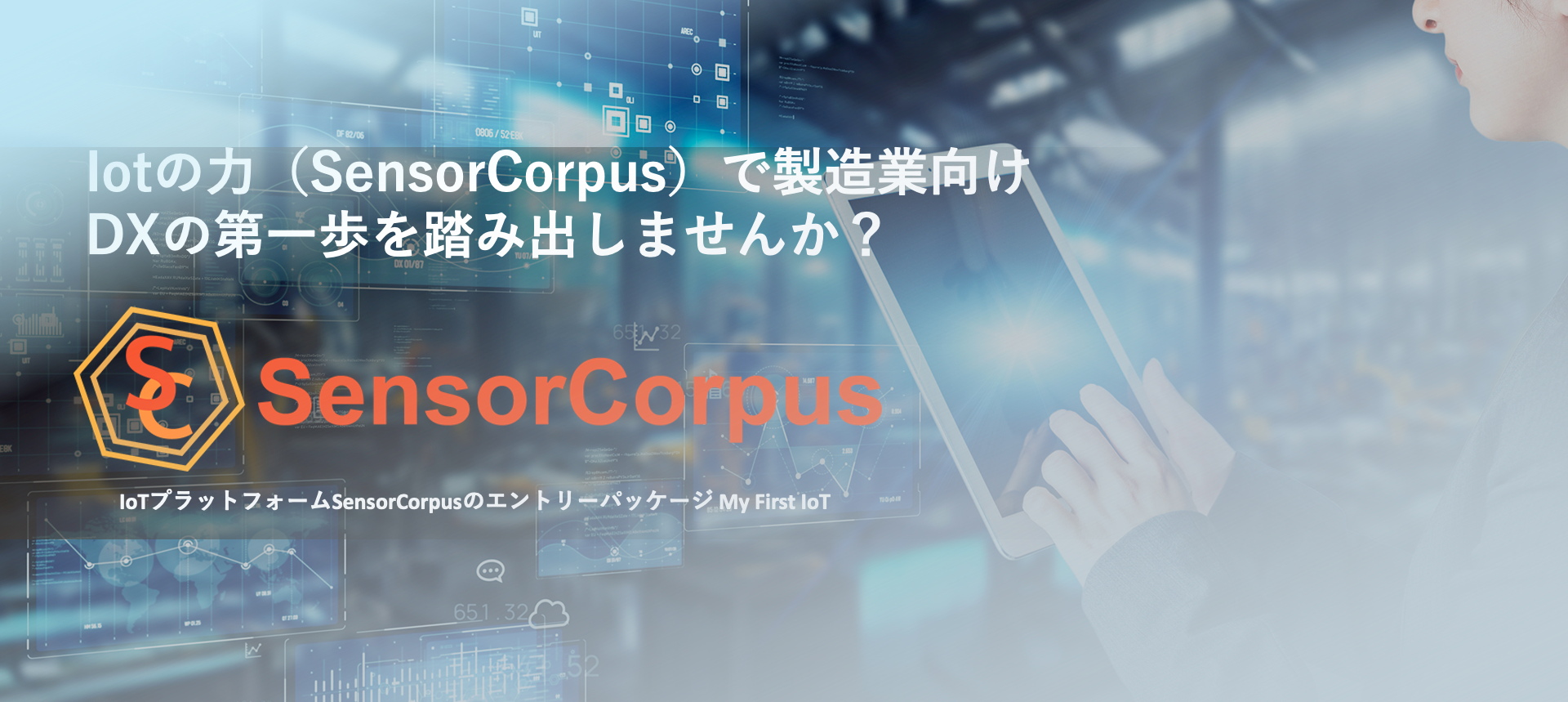
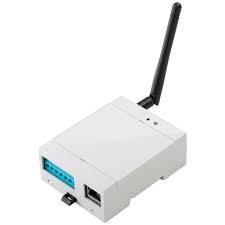
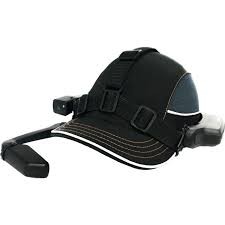
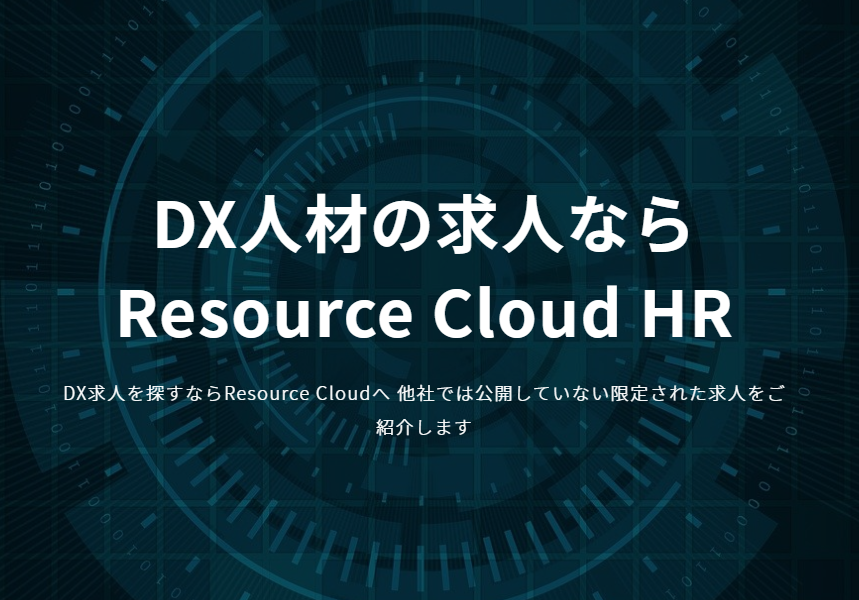
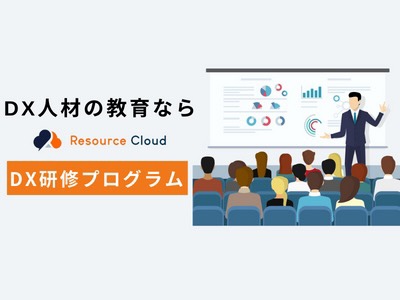
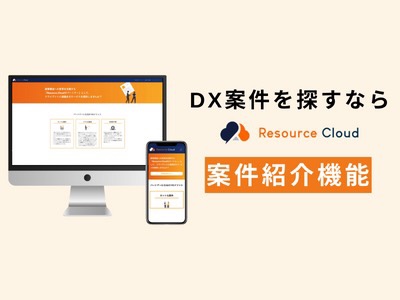