【DX事例紹介】生産ラインの見える化(可視化)のメリットや導入方法を解説
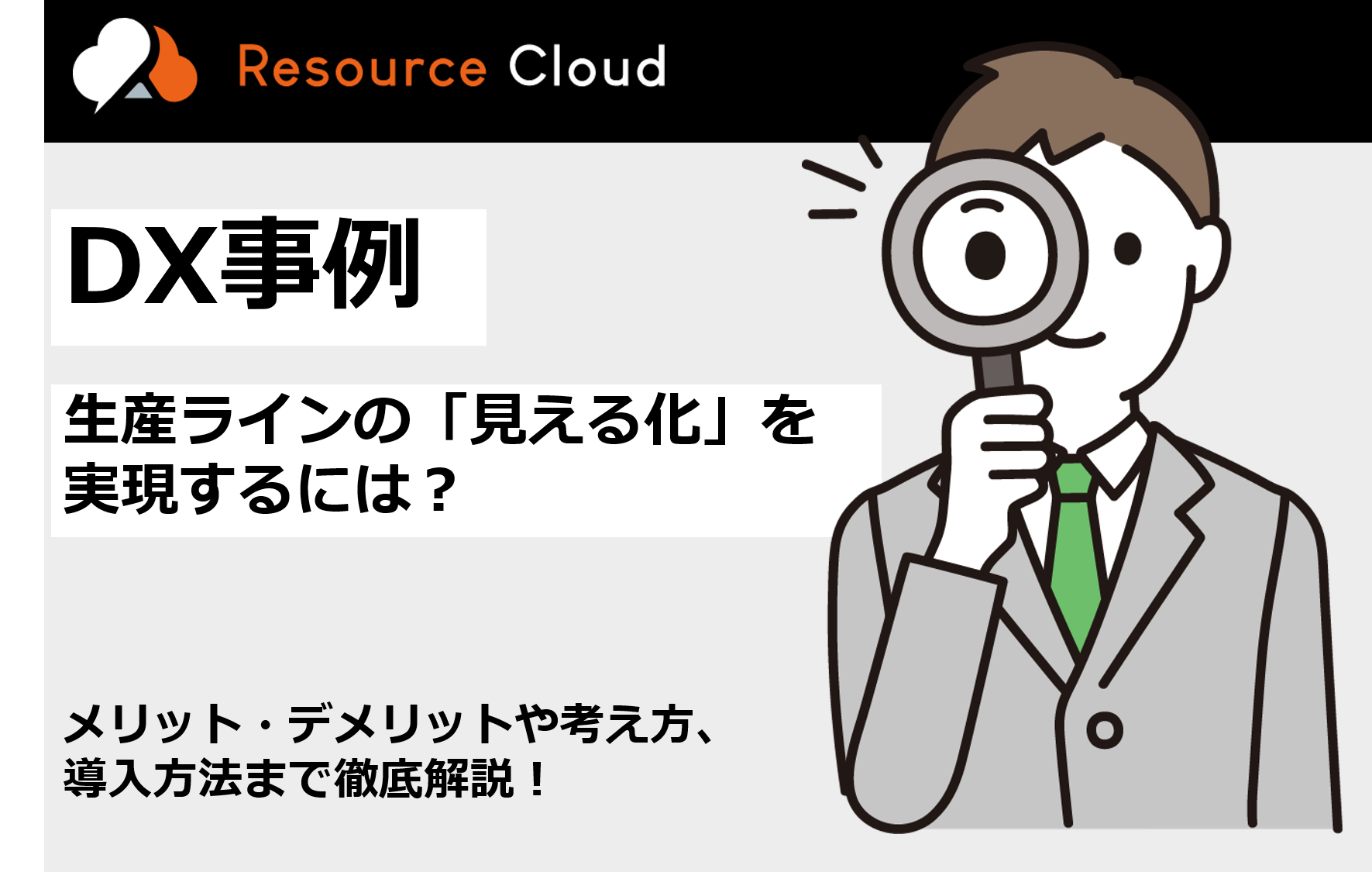
近年、製造業において生産ラインの「可視化(見える化)」が課題となっております。生産ラインの可視化を可能とする技術として「IoT(Internet of Things)」の導入が進んでいます。
生産現場におけるロスの圧縮は、これまでも企業において取り組み続けられてきました。しかし、これまで以上の生産効率を求めるためには、見える部分だけではなく一連の仕組みから改革が必要です。
今回は、生産ラインの可視化を実現するための考え方や手法、IoTを活用した際のメリットなどを具体的な導入事例も含めたDXの事例をご紹介します。
1.生産ライン見える化(可視化)とは
では、「生産ラインの可視化(見える化)」を実現することで、どのような事が期待できるのでしょうか。
1.1そもそも生産ラインとは
そもそも生産ラインとは、「ライン生産方式」における生産の流れを指し、製品を流れ作業によって完成させる方式のことをいいます。
生産ラインでは、作業員の配置を一連化し、機械に部品の取り付けや小加工などをおこないます。比較的単純な繰り返し作業が多く、他の業種では流れ作業ともいわれています。
生産ラインに配置された作業員が決まった工程のみを行います。そのため、生産スキル習熟までの時間とコストを抑えられる利点があります。また、一定の速度でラインが稼働するため、生産量を正確に把握することも可能です。
1.2生産ラインの可視化について
生産ラインの「可視化(見える化)」とは、製造現場における生産ラインの実態をグラフや表などを用いて、目で見えるようにすることです。
例えば、稼働している製造の流れを数値化することで、無駄な生産や不適切な製造フローなど、製造現場における課題を浮き彫りにすることができます。また、生産ラインの状況を知ることで、早期に品質異常を発見し、生産ロスと機会ロスを減少させることにも繋がります。
生産ラインを見える化していくことで、「作業ミスの予防」「生産性向上」「安全作業の確保」などの課題に対して、具体的な打ち手を挙げやすくなります。
2.生産ラインを可視化するメリット
生産ラインを可視化することで様々なメリットがあります。
2.1詳細なデータ分析ができる
生産ラインに設置されている生産設備の稼働率や故障率などを把握することで、生産効率に直結するトラブルが発生する前に対策を講じることが可能です。
従来までは、機種や号機ごとの回転数などから個別で生産量を算出する方式です。ところが、各設備の仕様が異なるために生産設備ごとにこれらの稼働率を把握することは非常に困難であり、またその方式もアナログでの集計方法に頼らざるを得ない実態がありました。
しかし現在では、各生産設備にIoT技術を導入することで、データの見える化を実現し、生産設備における稼働率などの詳細なデータを可視化することができるため、生産ラインの分析や改善に役立てることができるようになっています。
2.2新たな課題を発見できる
生産ラインの可視化により、組織内の全員が分析、抽出されたデータを共有することができるようになります。皆が同じデータをもとに生産実績などを把握できるため、トラブルの原因やその改善の方向性などの議論も可能となります。また、生産ラインの状況を現場の責任者や管理者がすぐに把握できるため、よりスピーディーなトラブルなどへの対処が可能となります。
2.3適切な人員配置ができる
現場の状況が把握できることで、必要な工程に最適な人員配置が可能となります。生産現場におけるボトルネック工程は単位時間あたりの生産量などで把握できますが、その原因として、前提となる工程における作業の停滞や、加工単位(最低投入必要量)が確保できていないなどの要因が隠れている場合があります。また、工程によっては、投入から加工完了までの待ち時間が長いものもあるでしょう。生産ラインを可視化することで、「手待ちロス」を削減するために最適な人員配置が可能となります。
2.4作業効率化ができる
多くの生産ラインでは「標準作業時間」が導入されており、作業時間を守ることで生産数量の予測が可能になります。
多くの場合は、作業者毎またはライン毎のどちらかが基準となっていますが、効率化するためには両方を意識する必要があります。「作業者」「ライン」双方の見える化をおこなうことで、作業者間における作業方法の改善をすすめ、ラインごとの実績を把握して生産現場全体のレイアウトを改善することで、生産ラインを一層効率化することができます。
3.DXで生産ラインの見える化(可視化)をするには?
生産ラインの可視化を実現するためには、単に業務を見える化だけとは限りません。
生産ラインの現状を把握することで問題や課題を発見し、さらなる現場の改善につなげることが重要となります。そのため、時間や費用だけでなく、改善を完遂するための目的意識の共有や、生産ライン全体の協力が必要になります。
全員が同じ目的を共有し、コンセンサスを得るための定量的な判断基準が必要不可欠です。
3.1見える化にはIoT技術が不可欠
生産ラインの見える化に取り組むためにはIoT技術の導入が必要不可欠でしょう。
その一方で、まだ十分にシステム化されていない生産現場では、IoT技術の導入に対して抵抗があったり、業務フローが変わることに不安を感じたりなど、導入までに何かしらの課題を抱えていることも事実です。
そこで、IoT技術の導入から運用支援までを行っているサービスを利用することで、スムーズな導入を実現することも可能です。
3.2「生産ライン可視化」事例
IoTによる生産ラインの可視化を導入して成功した事例として、「共和電機工業株式会社」の取り組みをご紹介します。
共和電機工業株式会社では、設備が稼働している時間と停止している時間を正確に把握することで、残業の削減が可能となりました。
生産現場では「段取り替え」と呼ばれる、生産品種を切り替えるために諸条件を変更する作業が発生します。そこで、設備が停止する原因のうち、「段取り替え」により停止する回数を削減するために停止原因の調査を実施しました。その結果、設備が停止する要因の大半は「段取り替え」にあることが明らかになりました。IoT技術を導入することにより、人為的な原因で設備が停止したことに気付くまでのタイムラグを含めることなく、正確な停止時刻を収集できたことが大きなポイントです。この調査をもとに作業の改善を実施し、対象生産ラインの停止時間を1日に1時間も短縮することが可能になりました。
4.DXで生産ラインを見える化(可視化)する上での注意点
これからの生産ラインでは、IoT技術を導入することが重要です。
しかし、通信機器やセンサーの設置費用に加え、無線通信方式の通信料などの費用が発生します。また、莫大なデータを収集して活用していくとなると、IoT化しなければならない設備の数も自然と増加し、結果として数千万以上ものコストがかかることもあります。
そのため、中小企業でIoTを導入する場合は、「強い目的意識」と「明確な目標」が不可欠です。
4.1むやみにシステム導入しない
生産ラインを可視化すれば生産性が改善される訳ではありません。
「人件費を削減したい」、「ラインの稼働率を改善したい」などの具体的な目的がなければ、ただ「便利になった」だけになりかねません。
また、IoT技術を導入する際には、それらの機器設備が操作でき、さらに収集したデータを分析して有効活用できる人材の確保や育成も必要となります。IoT化には、多くの設備がインターネットに接続されるため、サイバーセキュリティへの投資も欠かせません。そのため、自社内での人材の育成や確保が難しい場合は、アウトソーシングを活用するのもひとつの方法です。
組織全体でのコンセンサスは得られているのか。強い目的意識を持ち、長期的な視点で取り組めるのか。明確な目標は設定できているのか。まずはこれらを十分に確認したうえで導入を検討しましょう。
4.2データを可視化するだけで終わらせない
生産ラインにおけるIoT導入を成功に導く際に最も重要なことは、「可視化したデータをどう活用していくか」です。
IoTによって可視化させるだけでは、あくまで現状を把握できたに過ぎません。そこで、把握した情報を活用し、さらなる生産現場の改善につなげることが重要です。
生産現場には、在庫管理や生産ロス、設備保全、固定費の上昇など、非常に多くの課題があります。IoTで得られたデータの分析によってこれらの原因を顕在化して改善を図ることで、本当の意味での生産ラインの見える化を実現します。
さらに、取り組みの中でPDCAを回すことにより、はじめて生産ラインの効率を改善し続けることが可能となるのです。
5.まとめ〜生産ラインの見える化(可視化には)課題の整理や導入環境の整備が必要〜
いかがでしたでしょうか。ここまで、生産ラインを見える化することで実現可能になることや、それにより得られるメリットなどを解説してきました。
生産ラインの見える化には、強い目的意識や明確な目標、全体のコンセンサス、導入コストの把握や長期的視点での計画などが必要です。そのため、IoTの導入を拙速に検討するのではなく、まずは現状の生産ラインの課題の整理と、IoTをより良く導入するための環境の整備から進めてください。また、生産現場や組織の性質に合ったシステム選定の必要性も考えられます。
見える化は、生産現場におけるロスの圧縮には非常に有効な手法です。生産ラインの見える化は、現場に潜む非常に多くの課題を解決するための有効かつ効果的な手段となるでしょう。
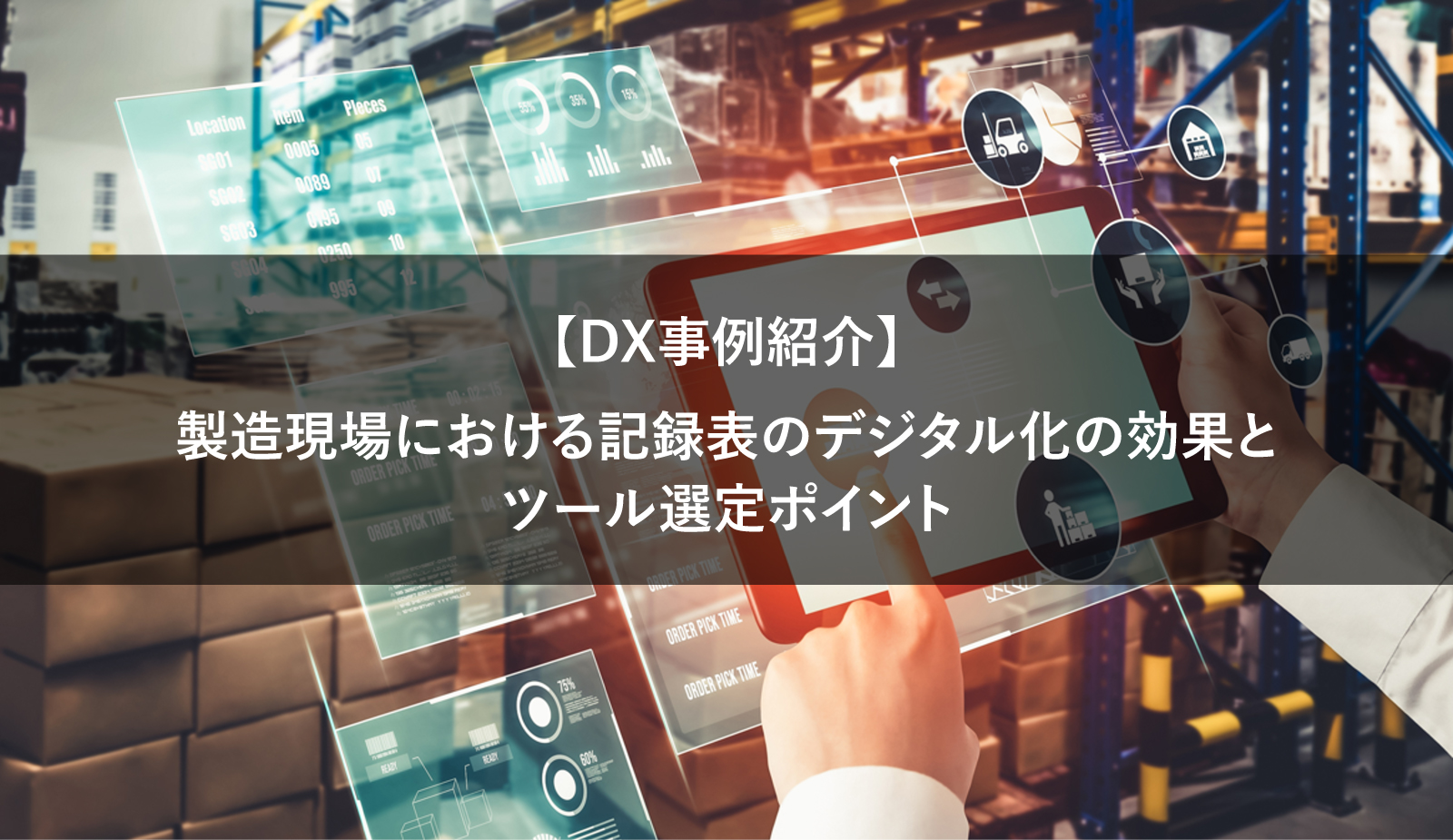
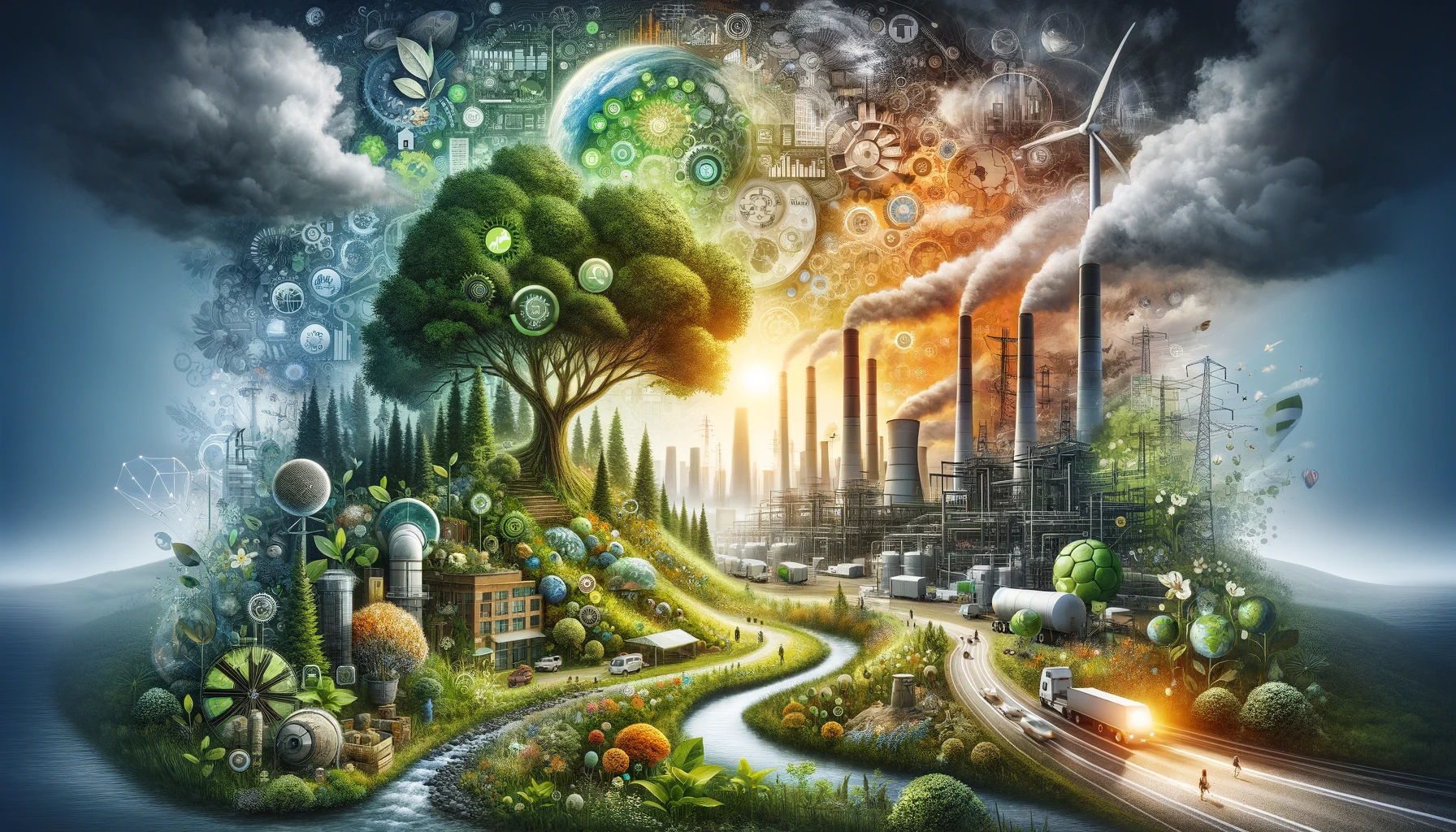
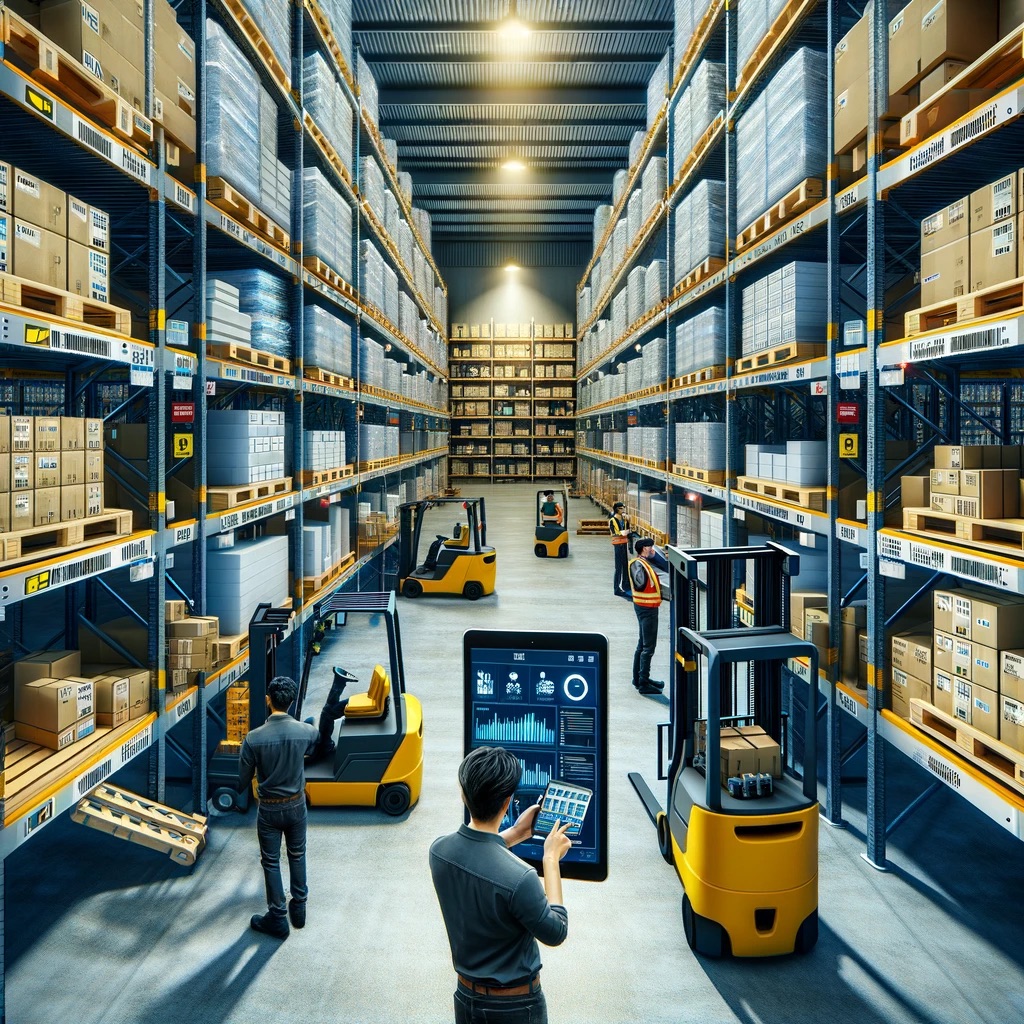
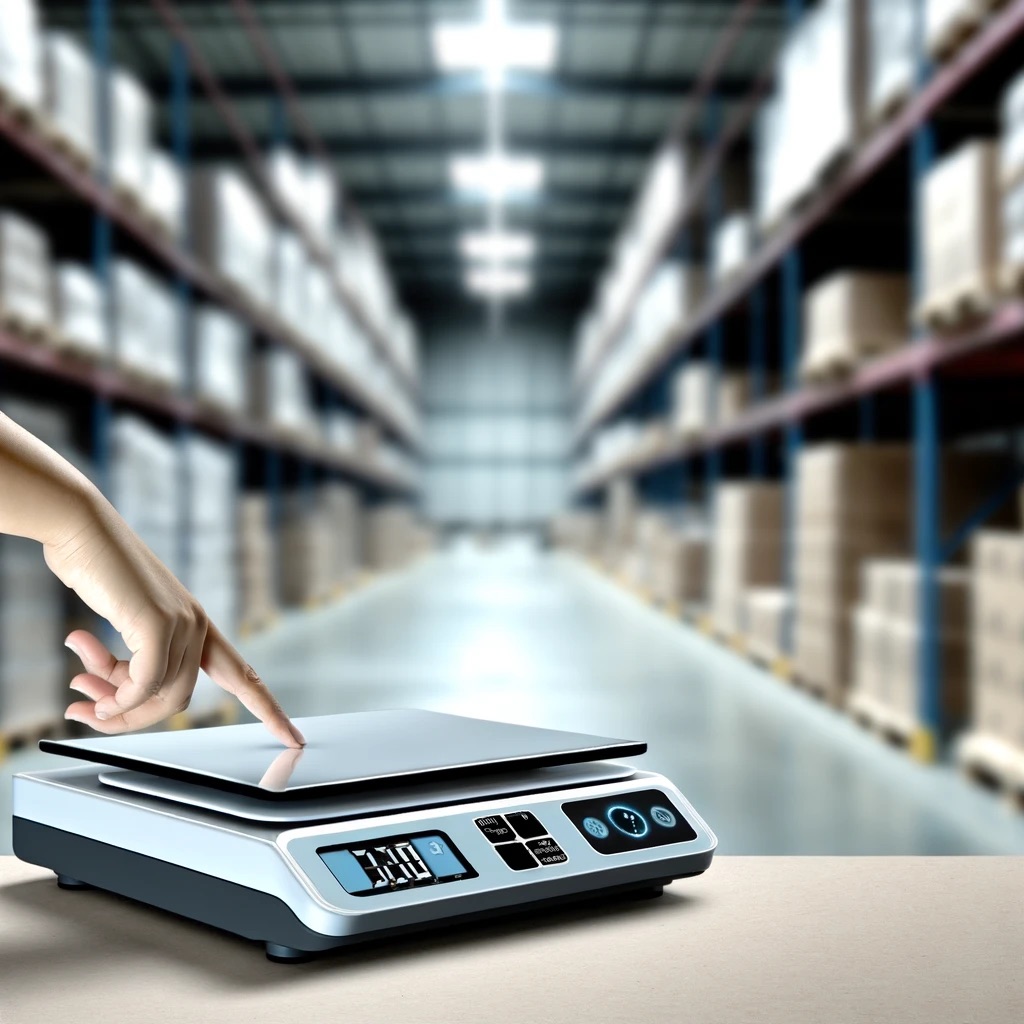
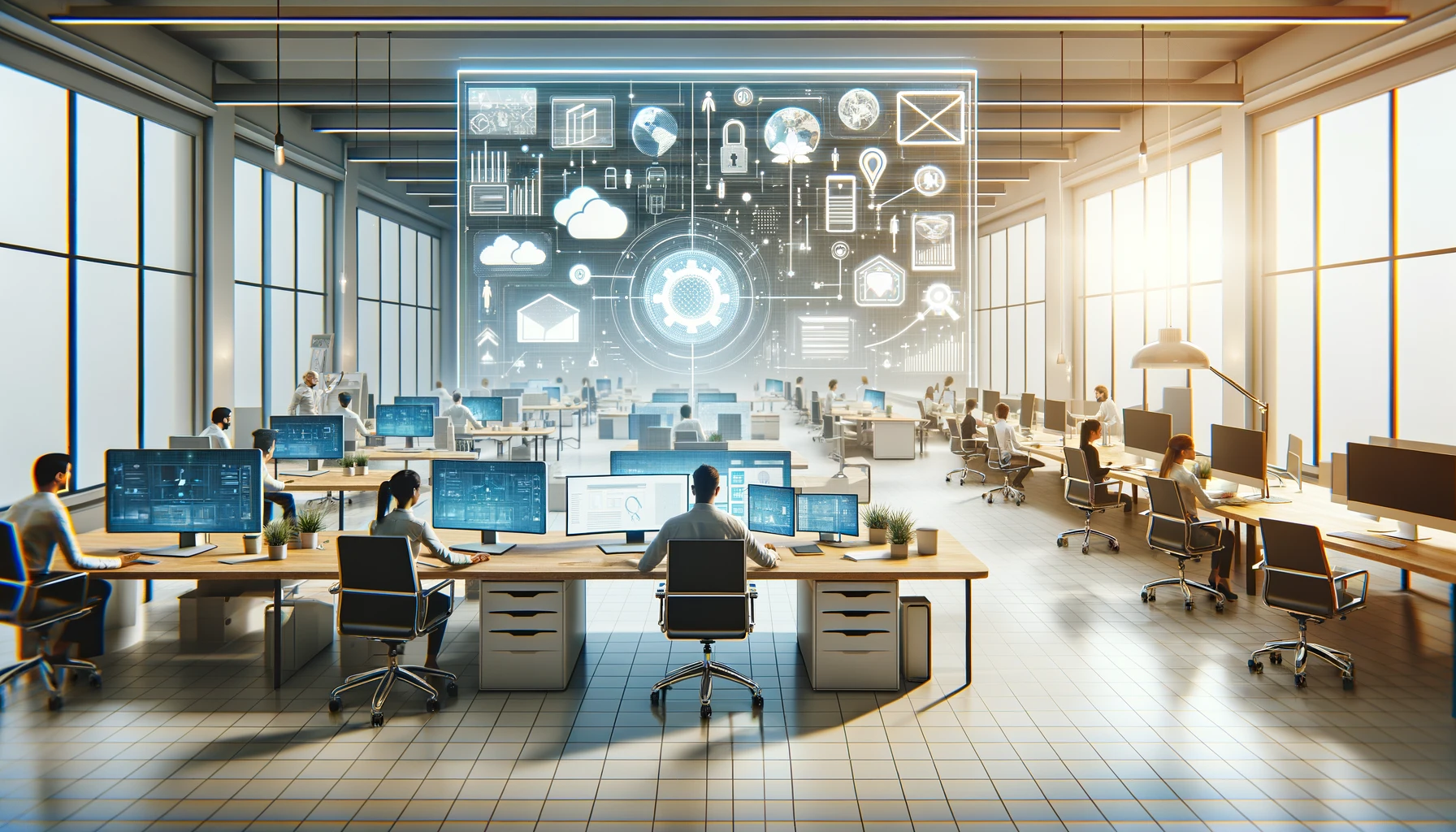
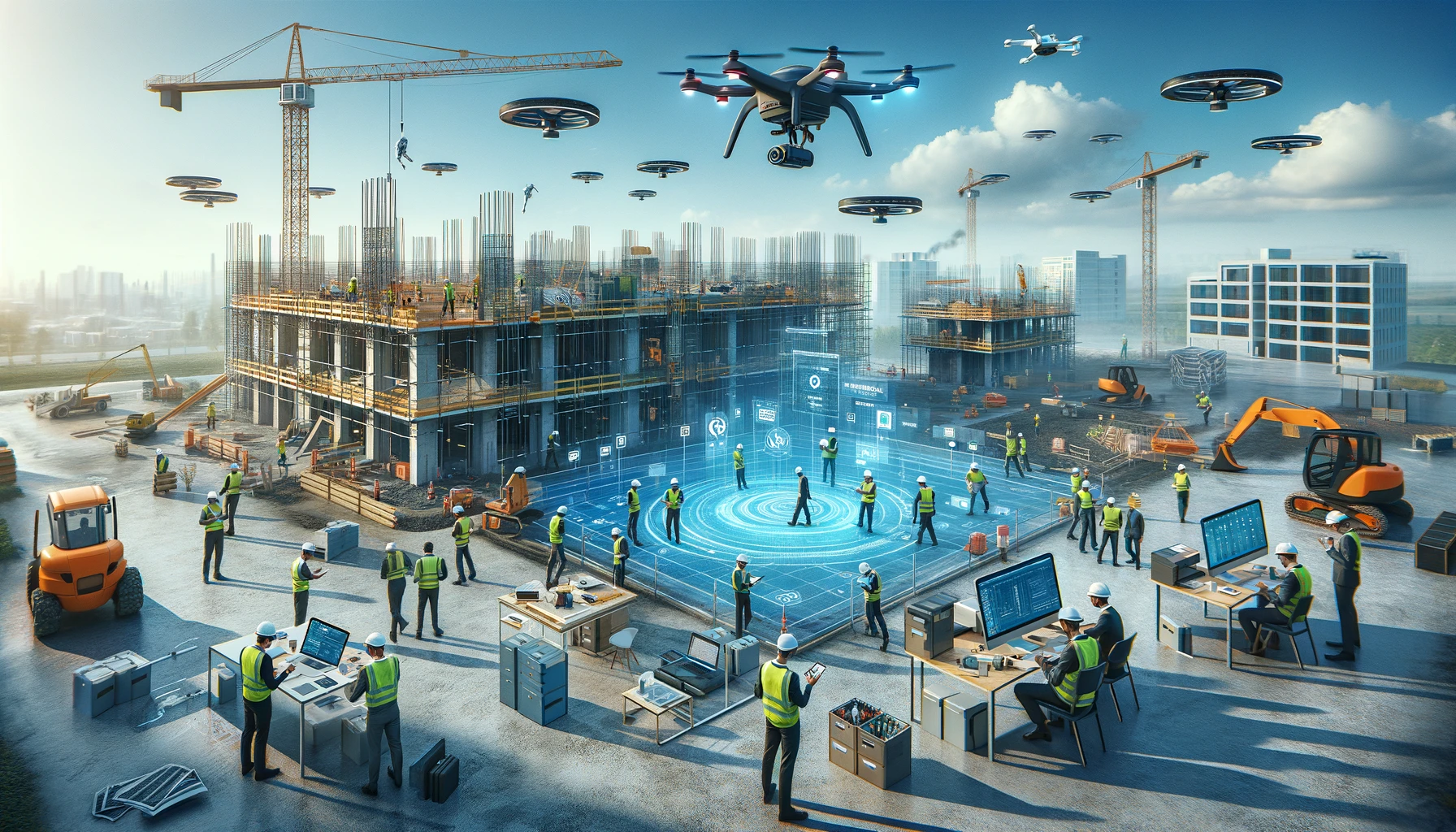
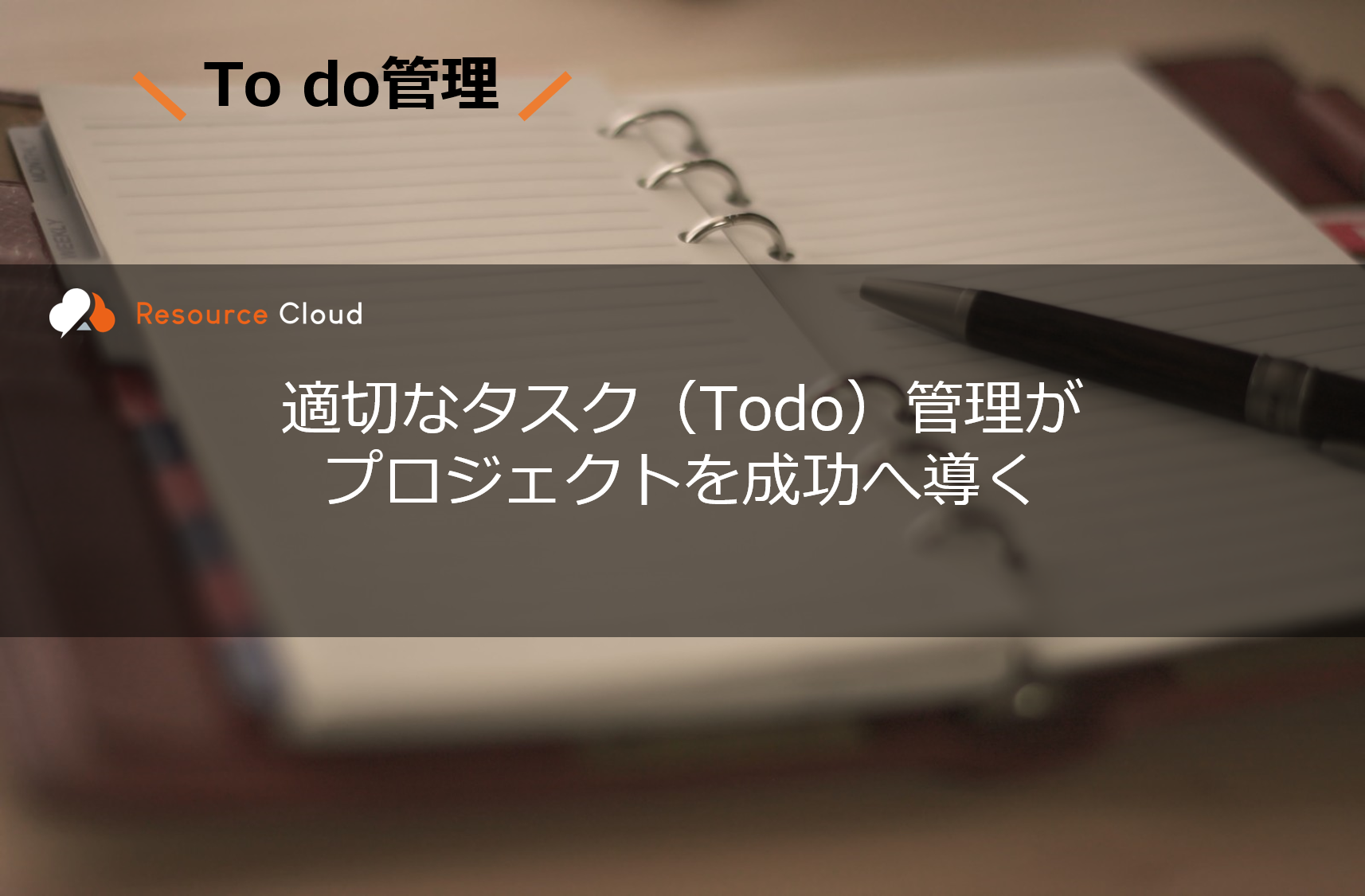

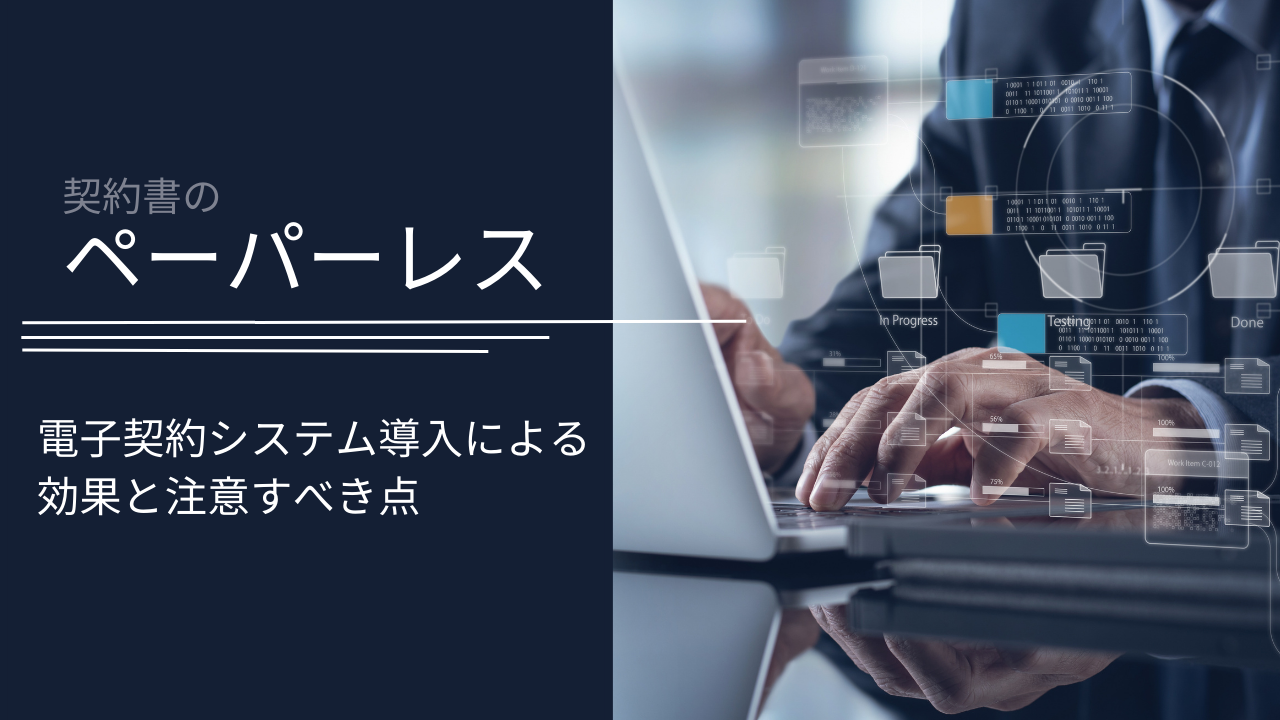
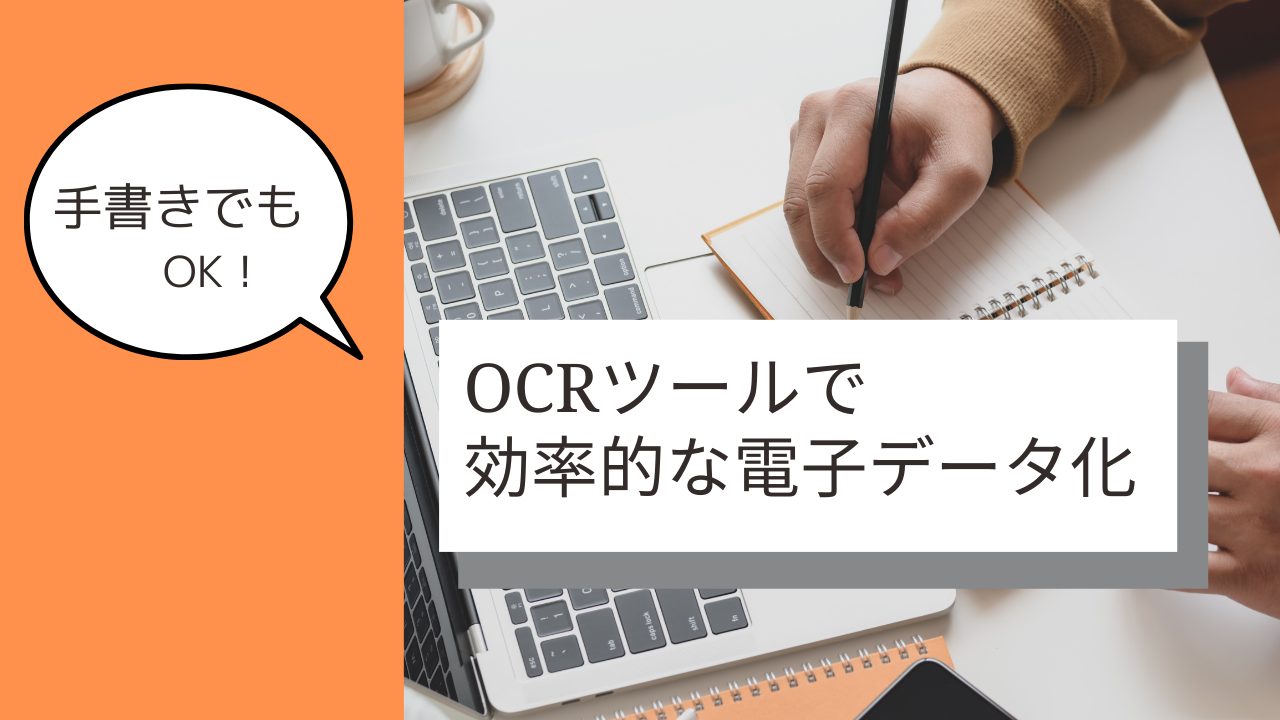
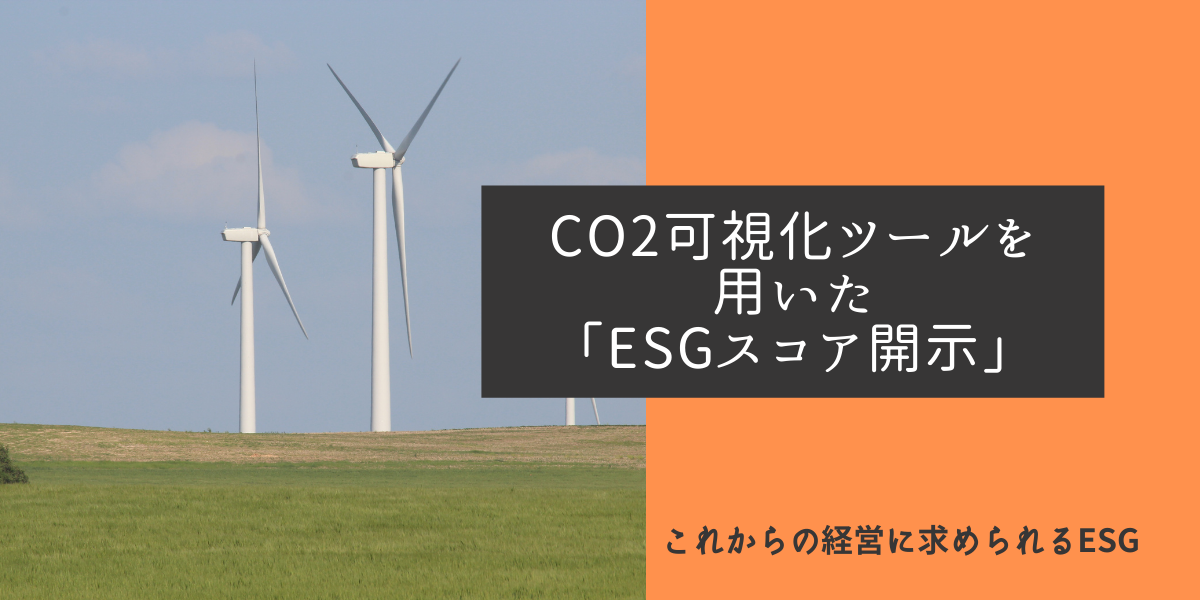
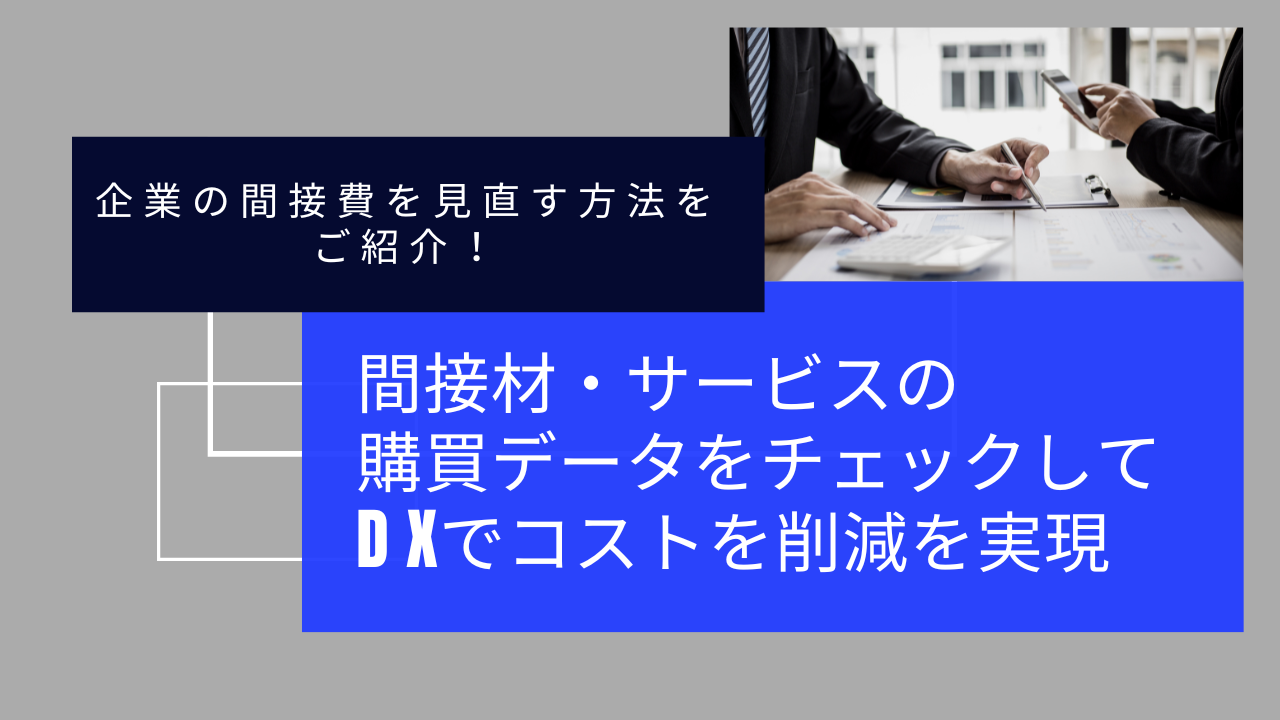
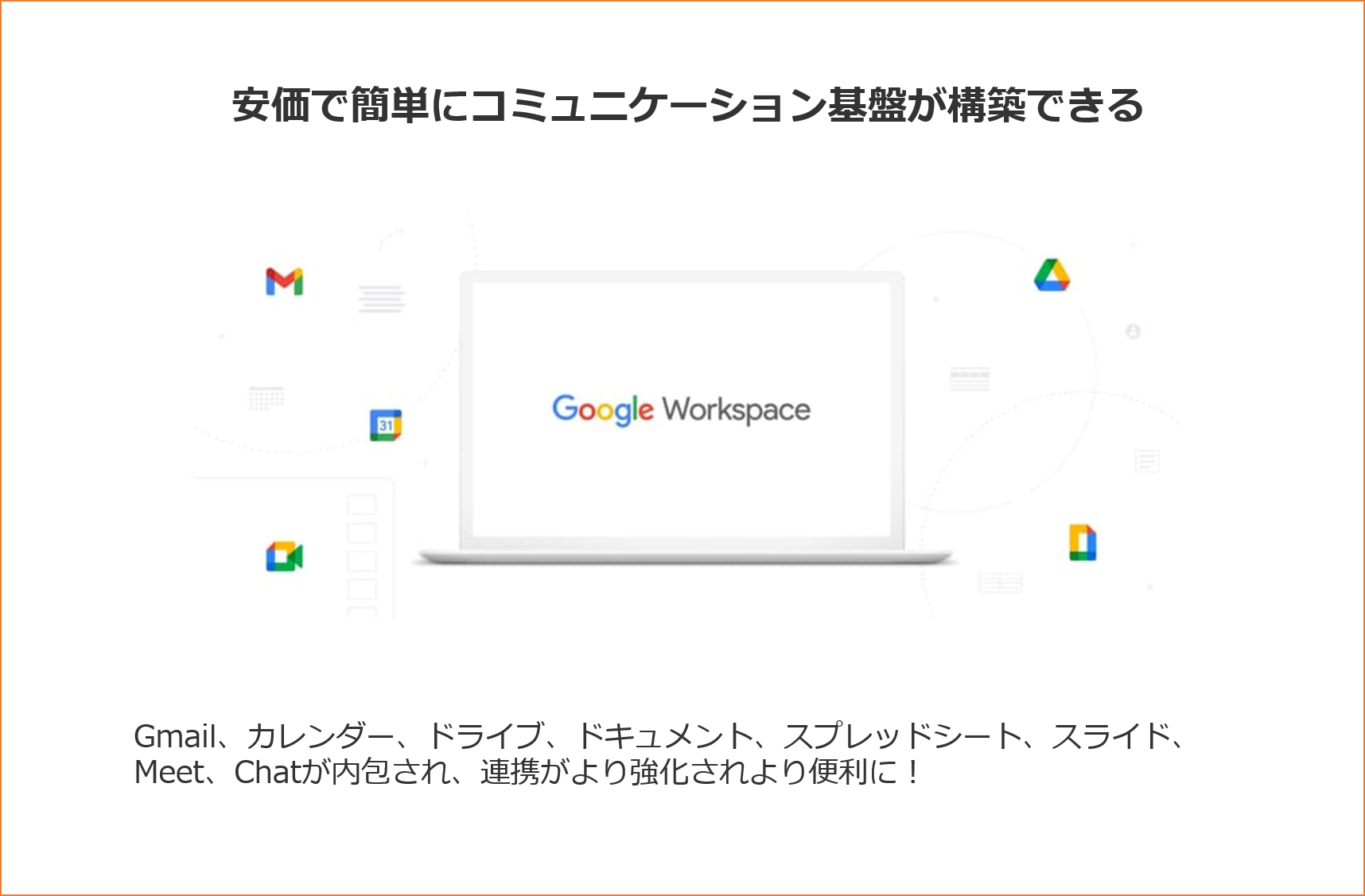
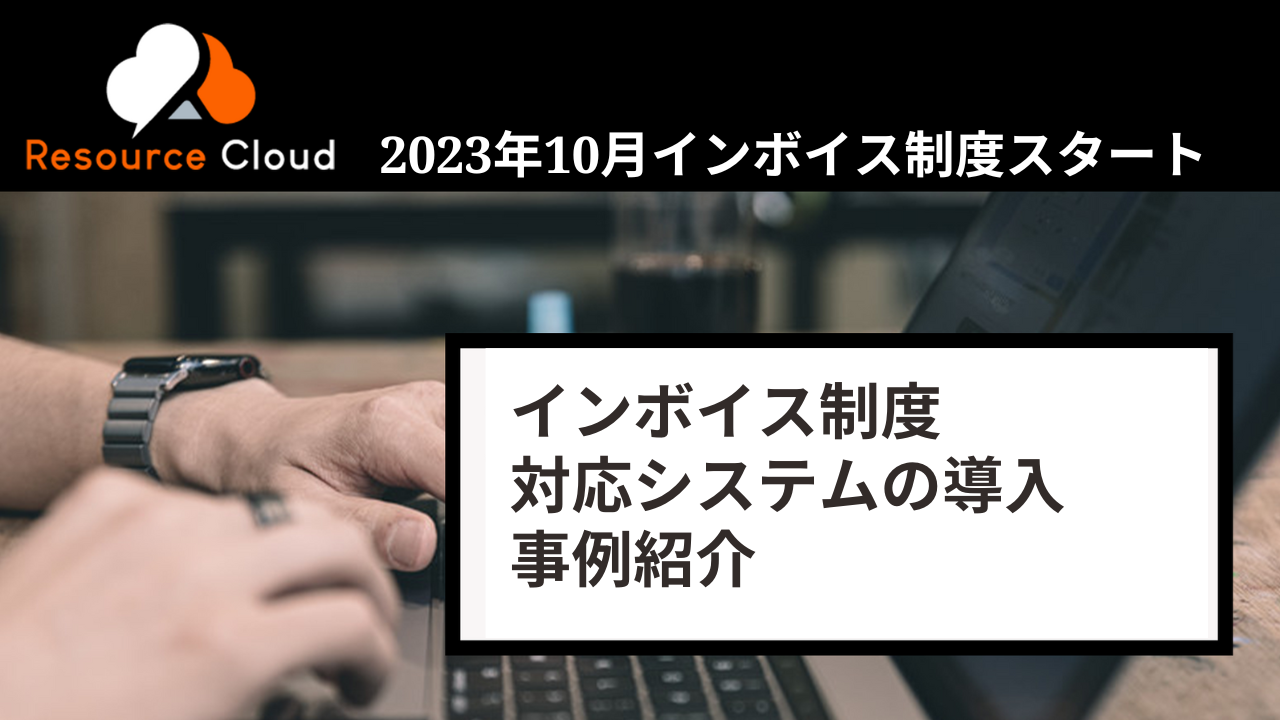
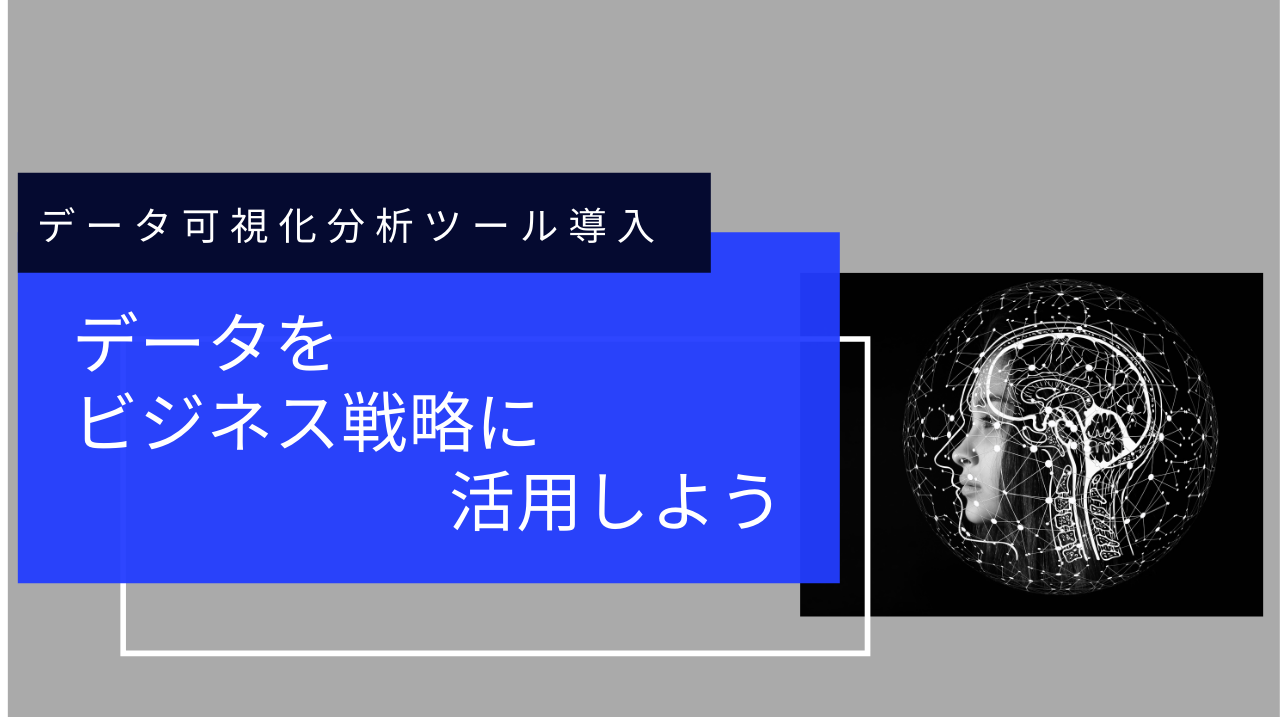
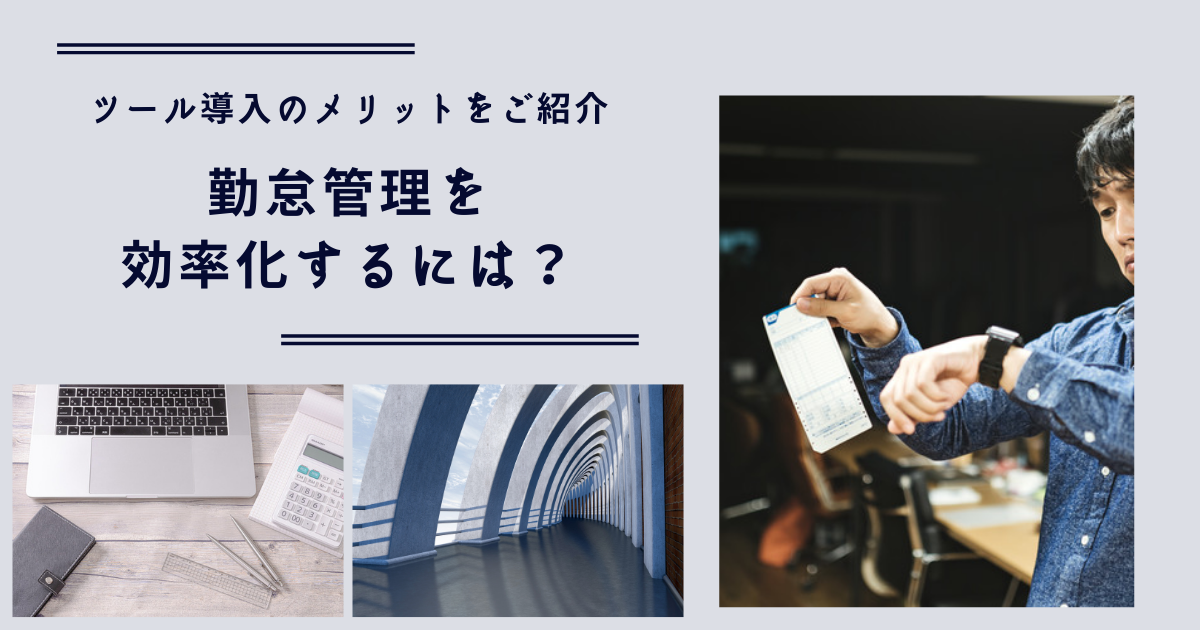
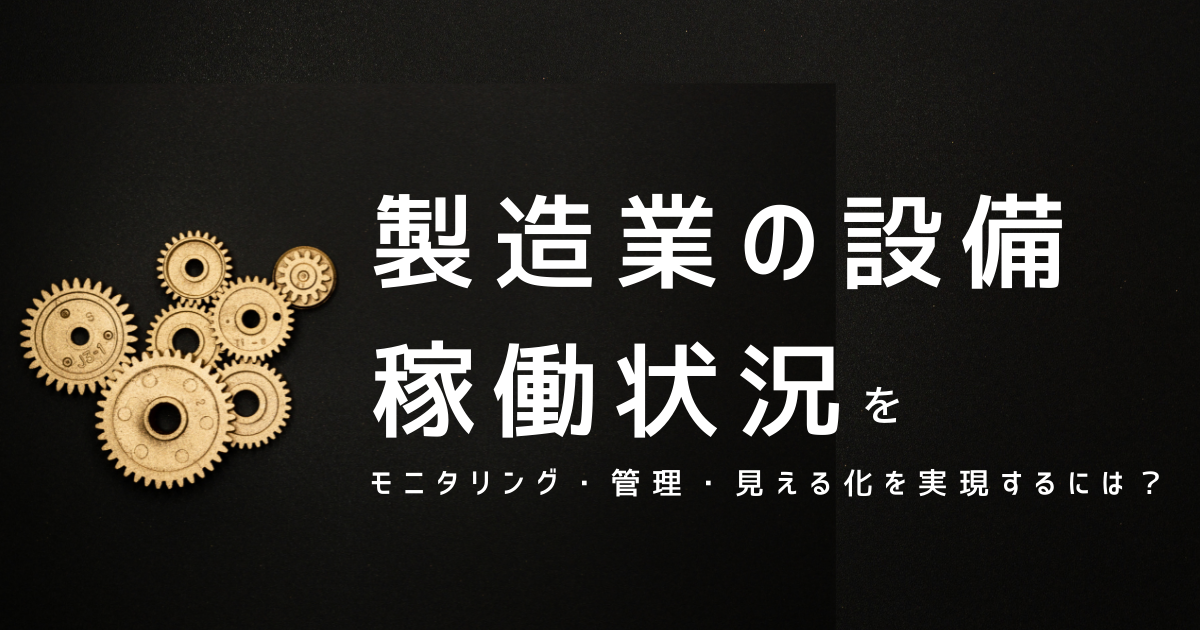
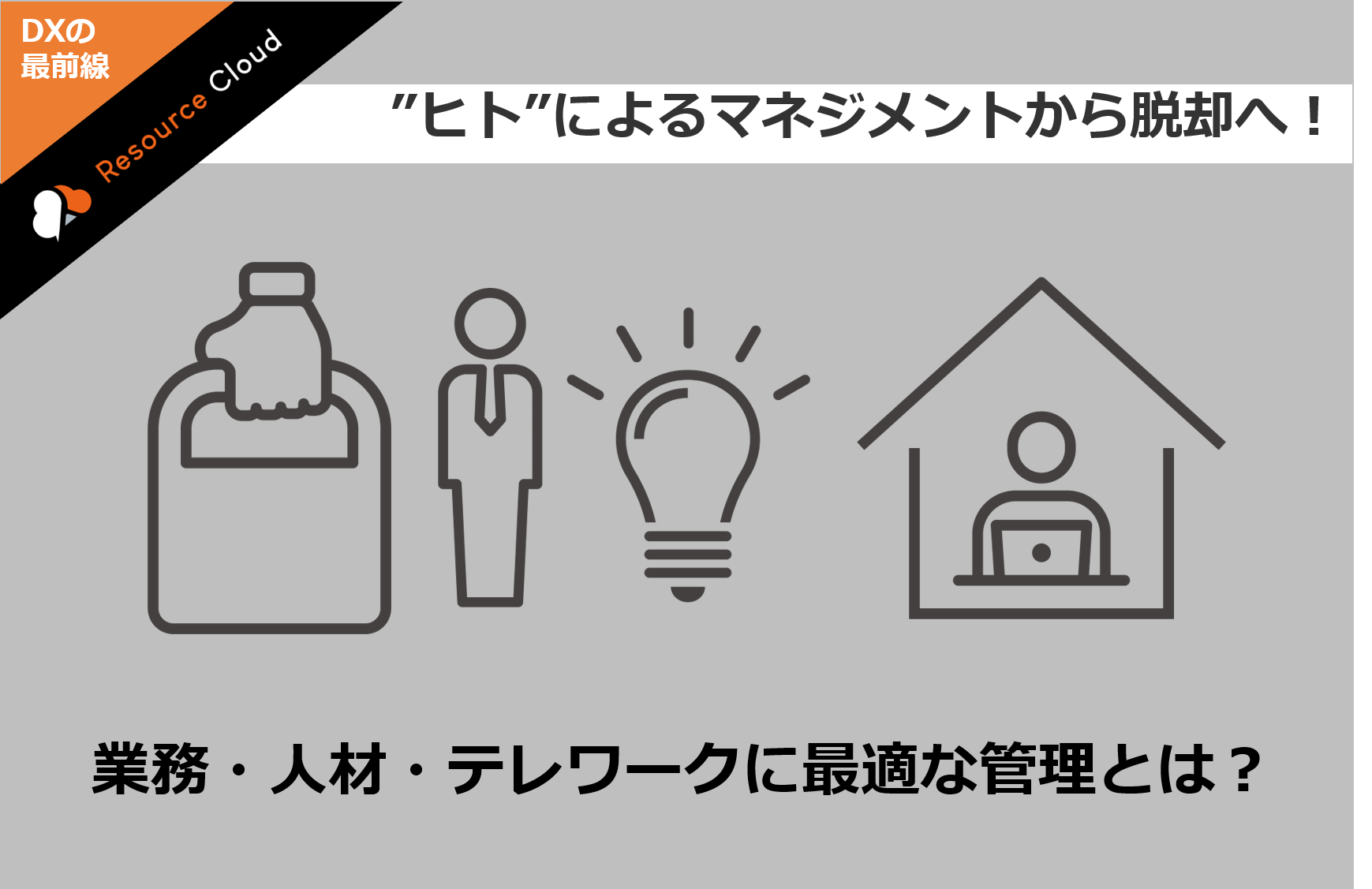
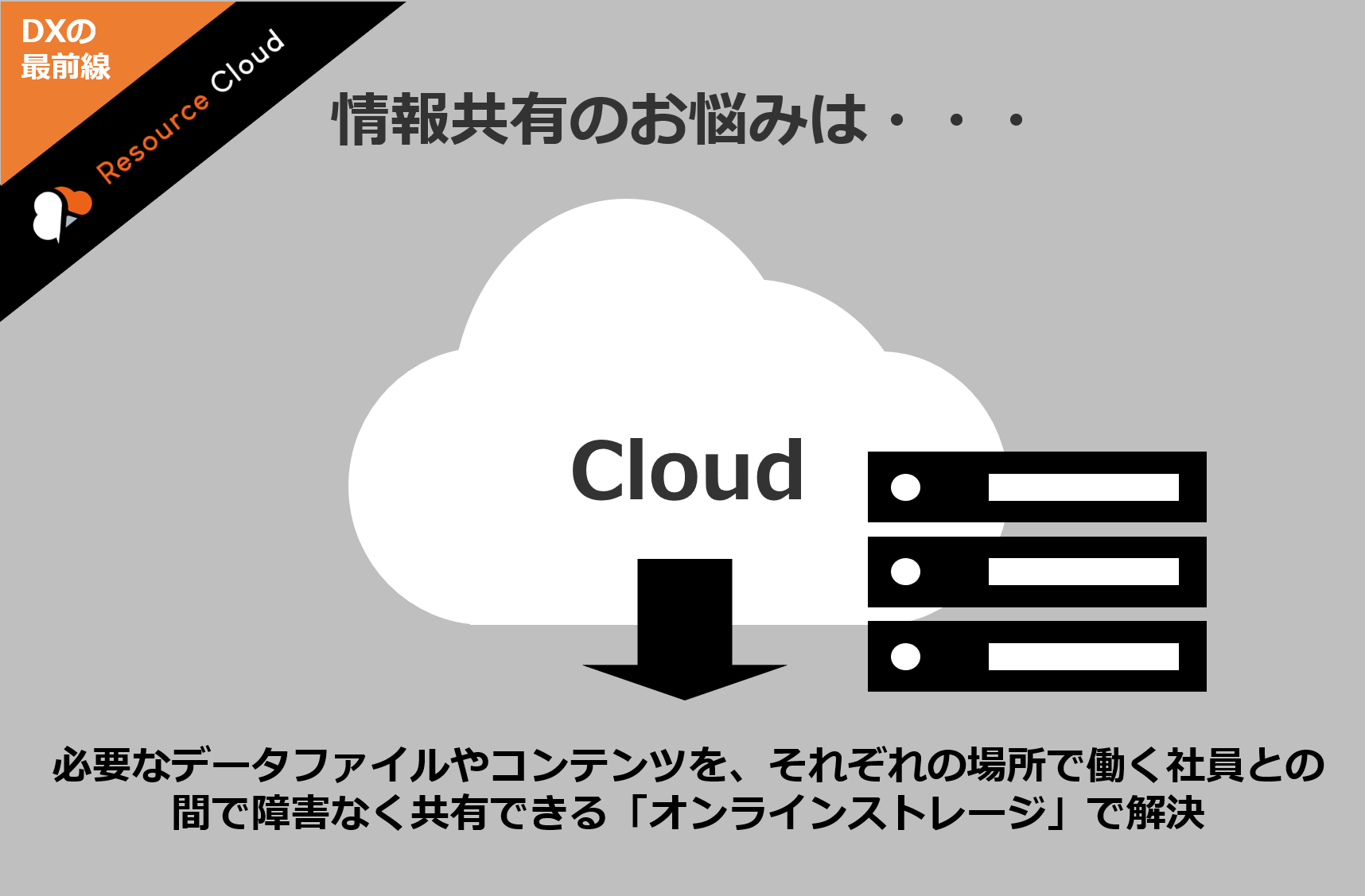
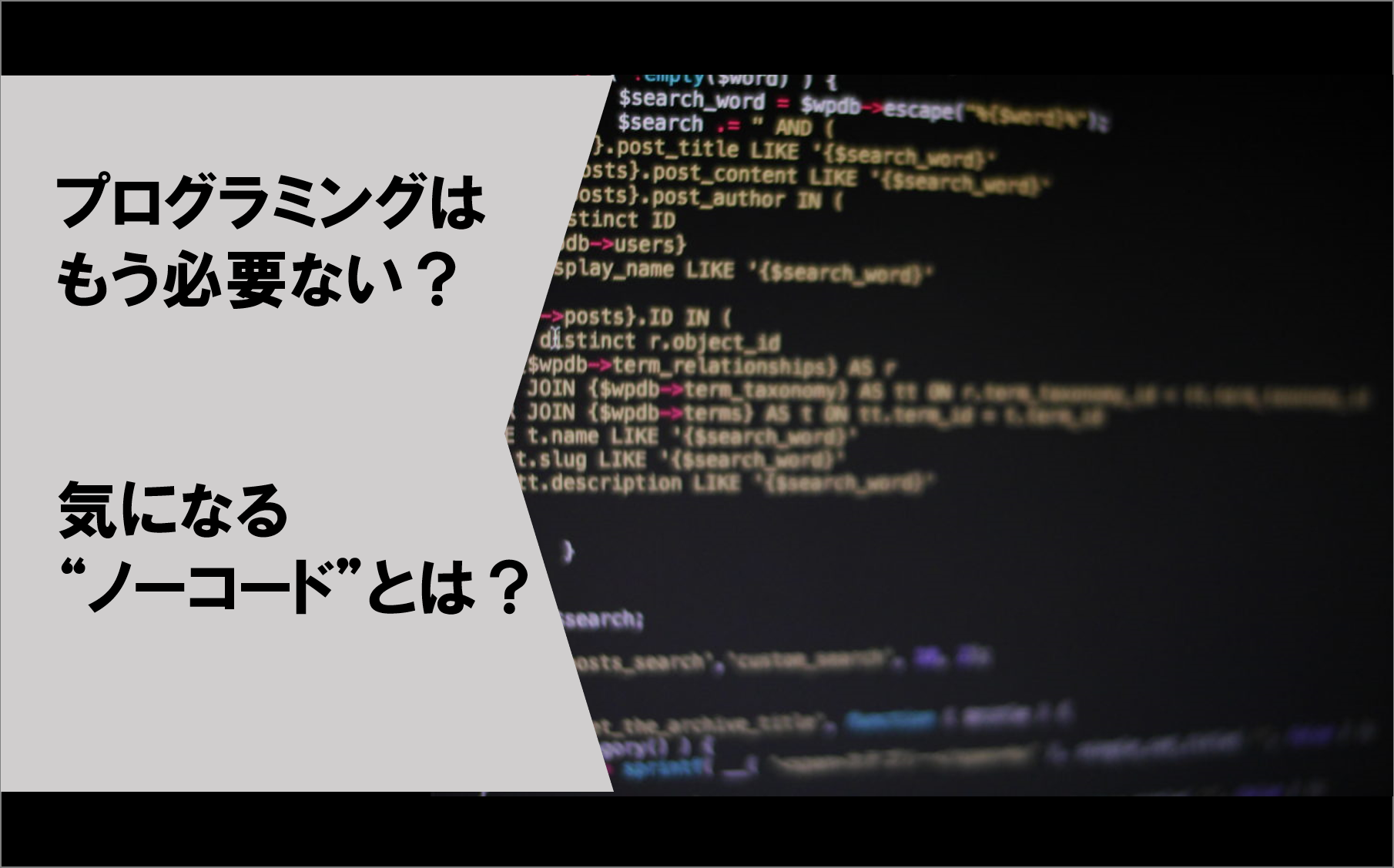
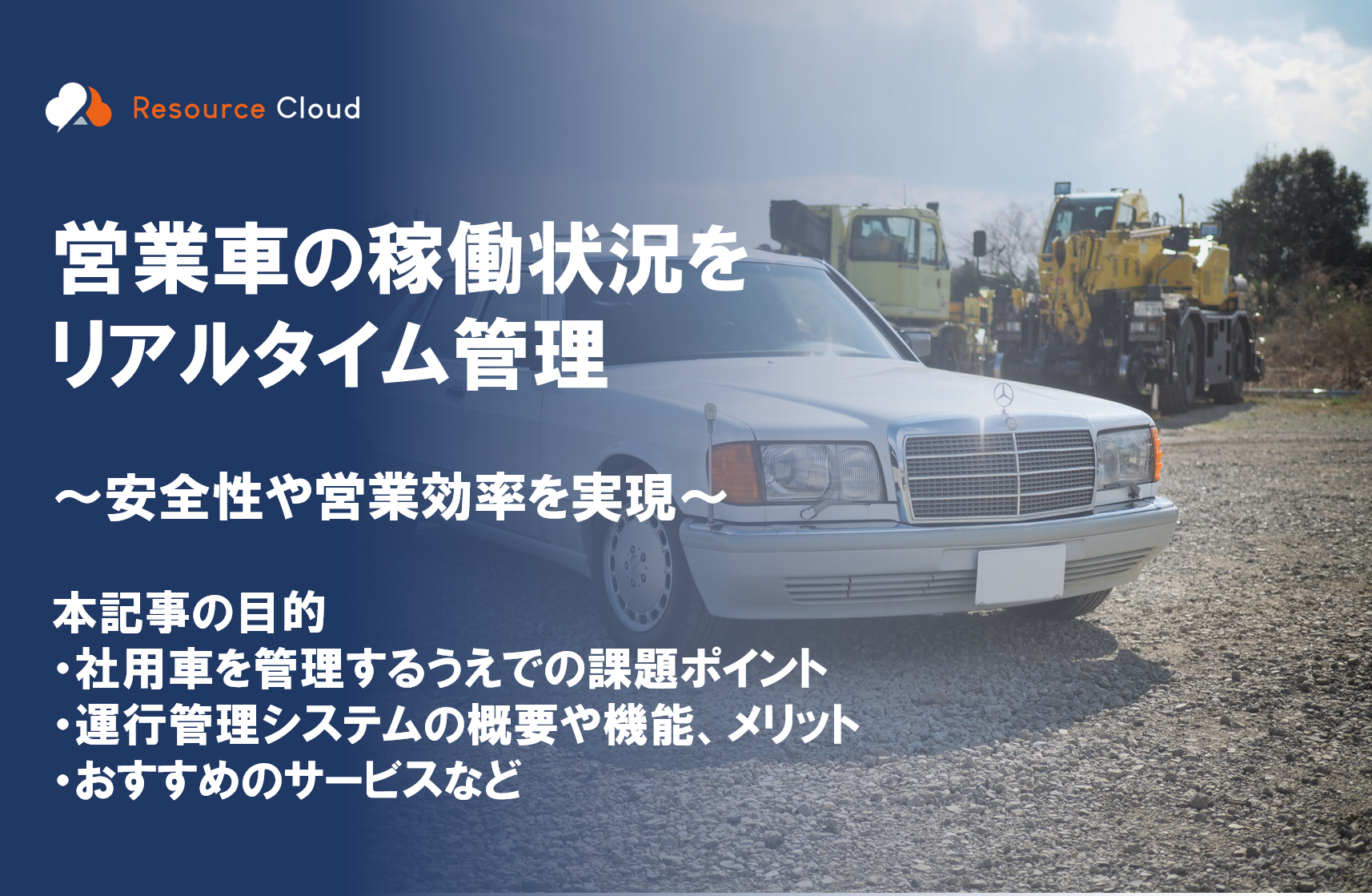
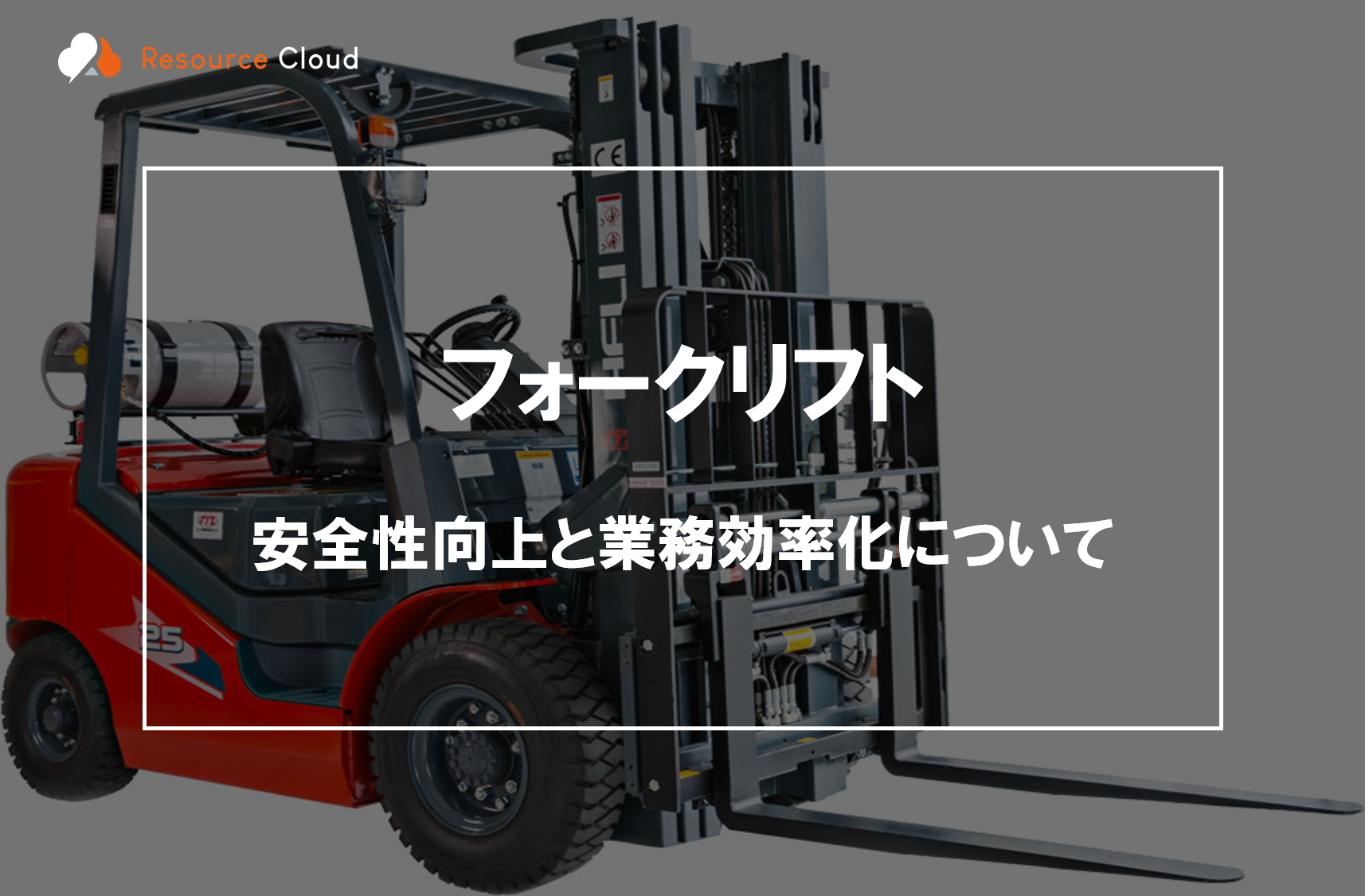
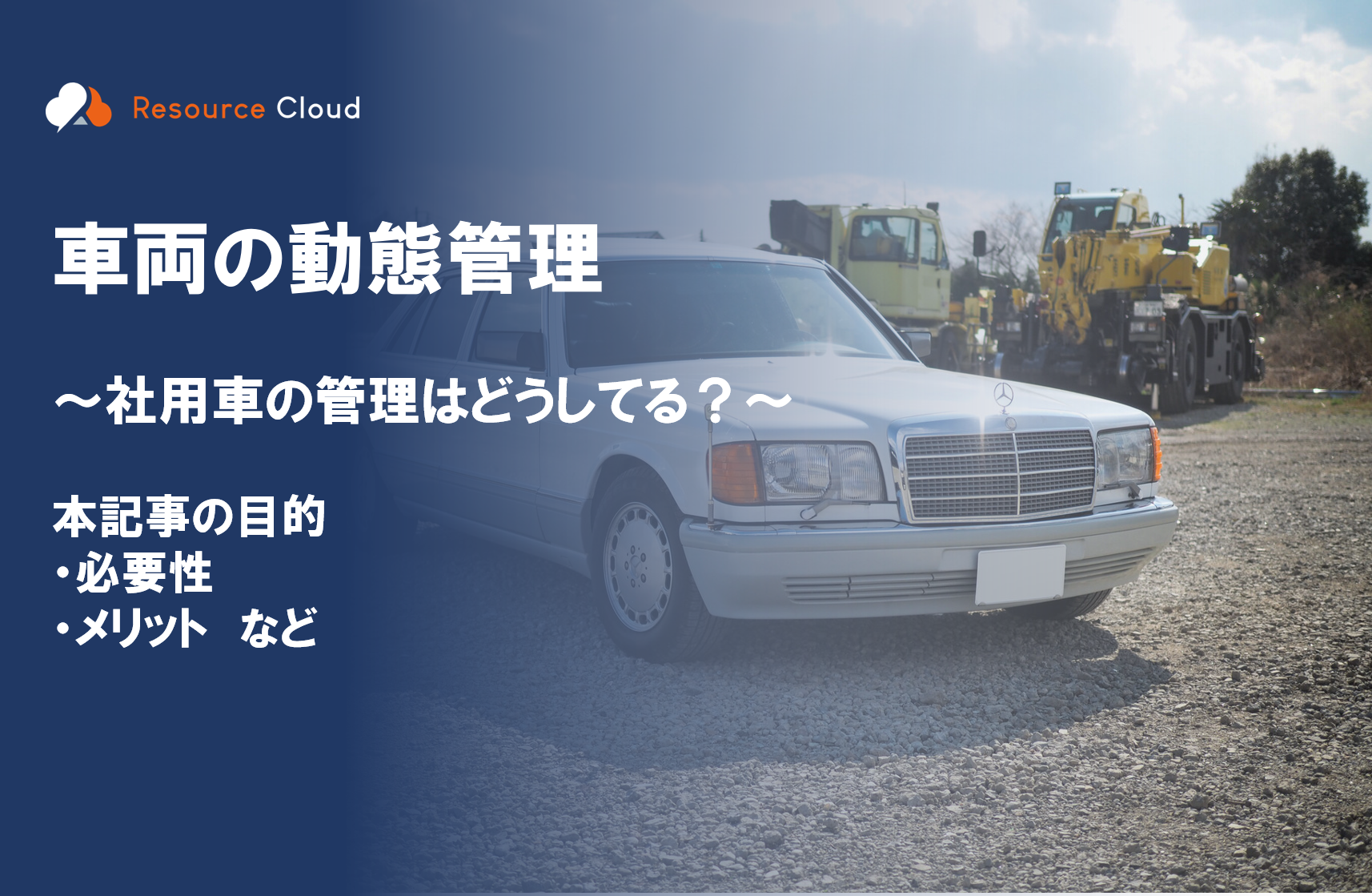
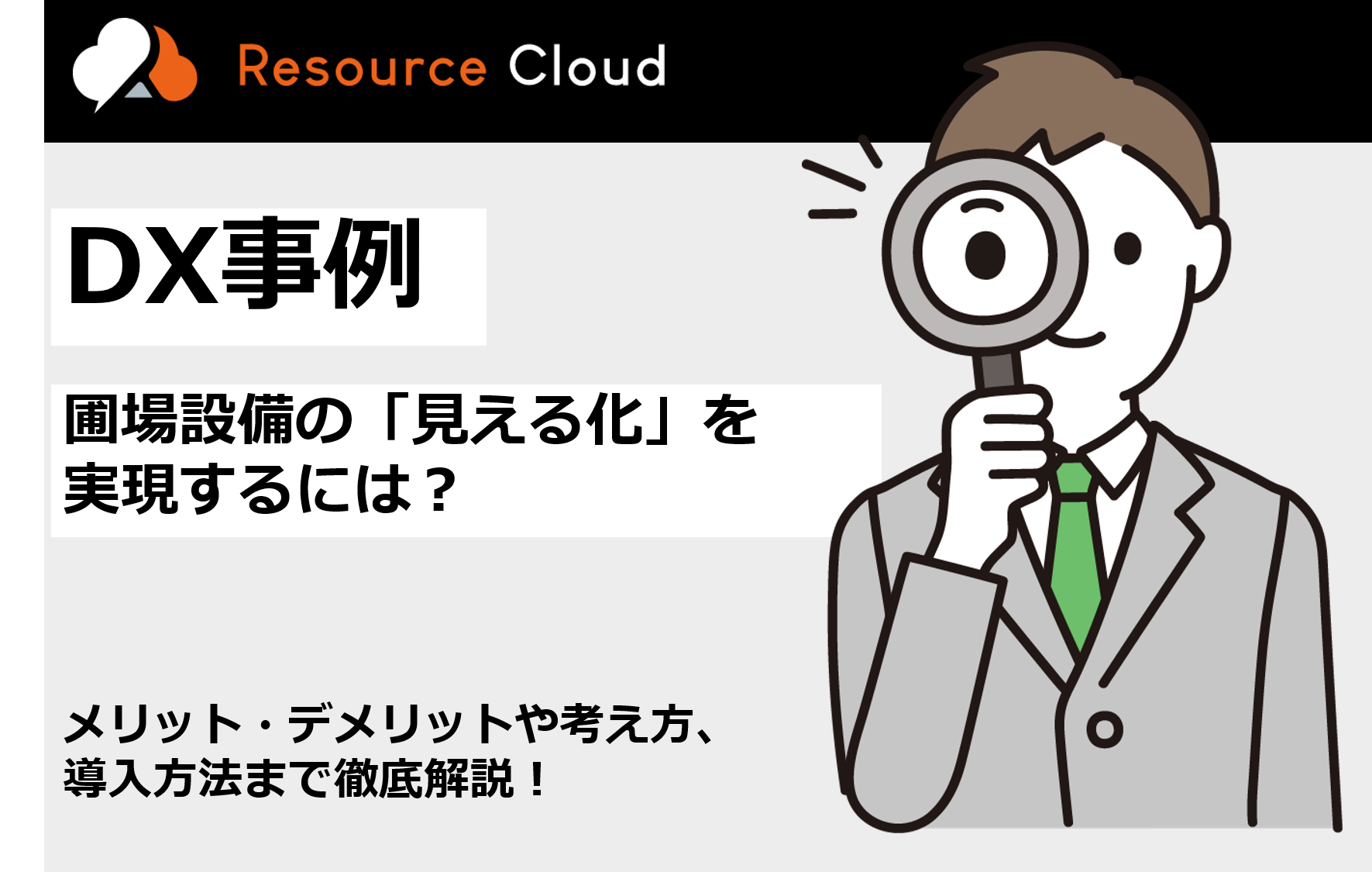
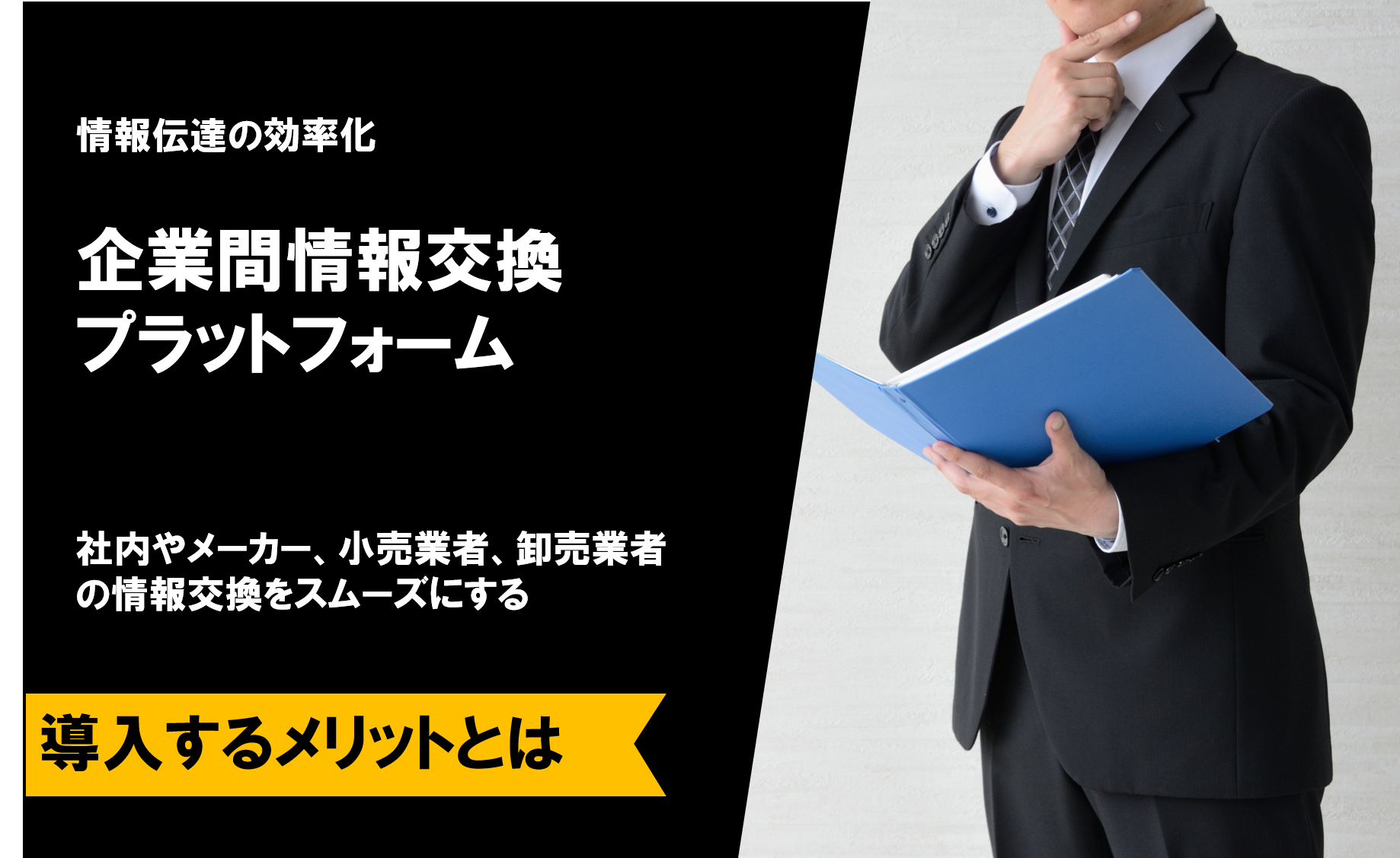
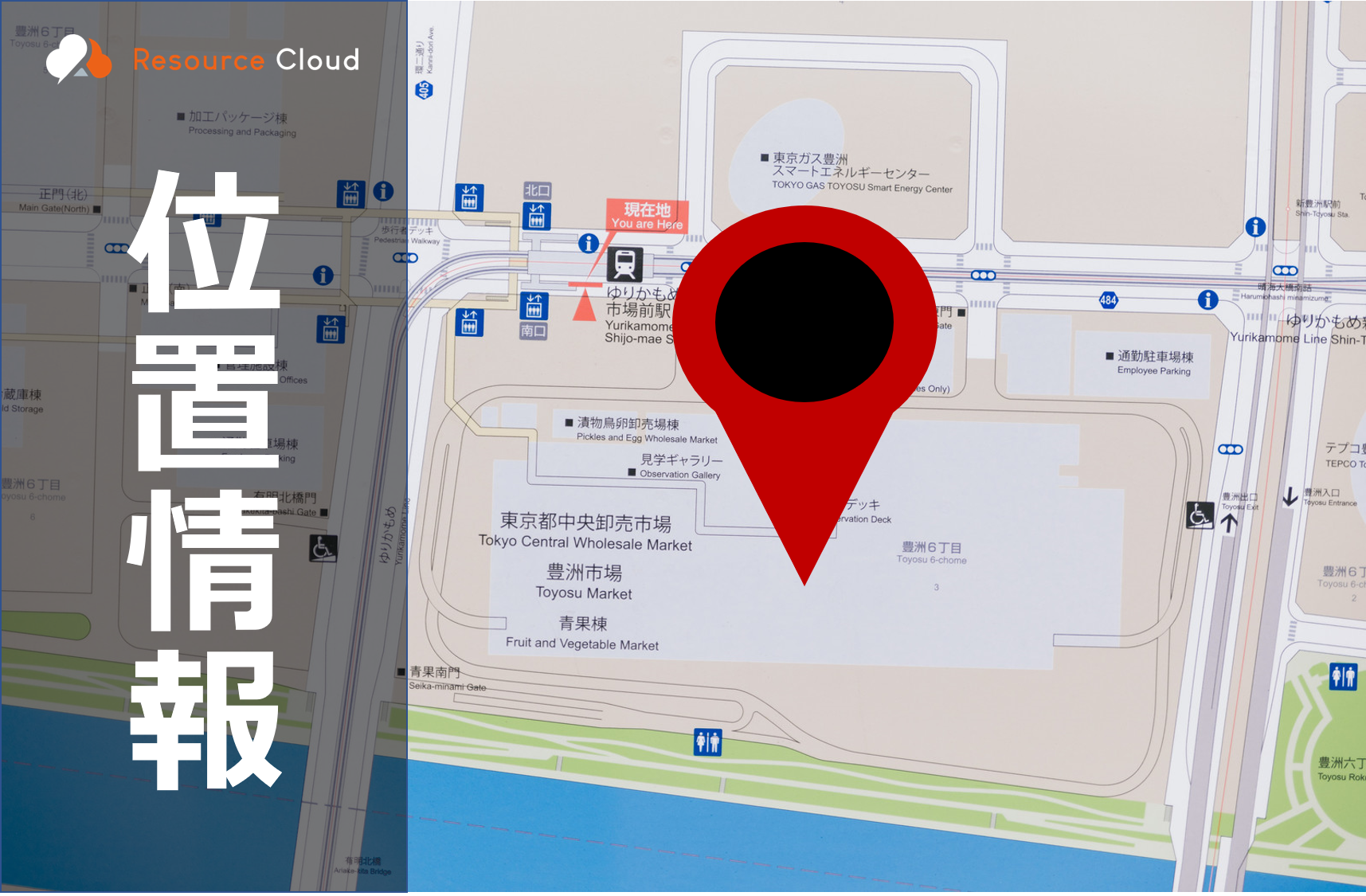
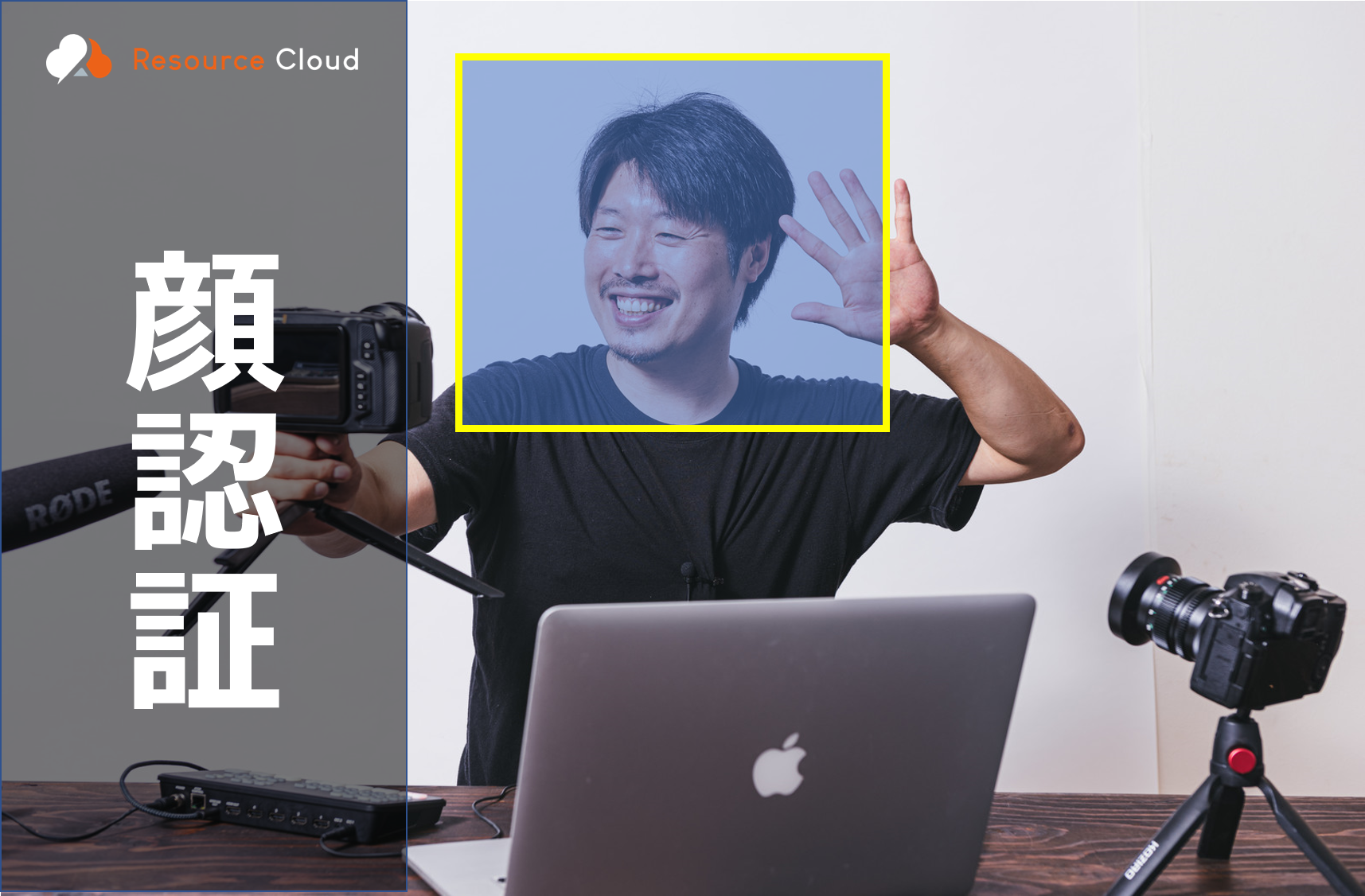
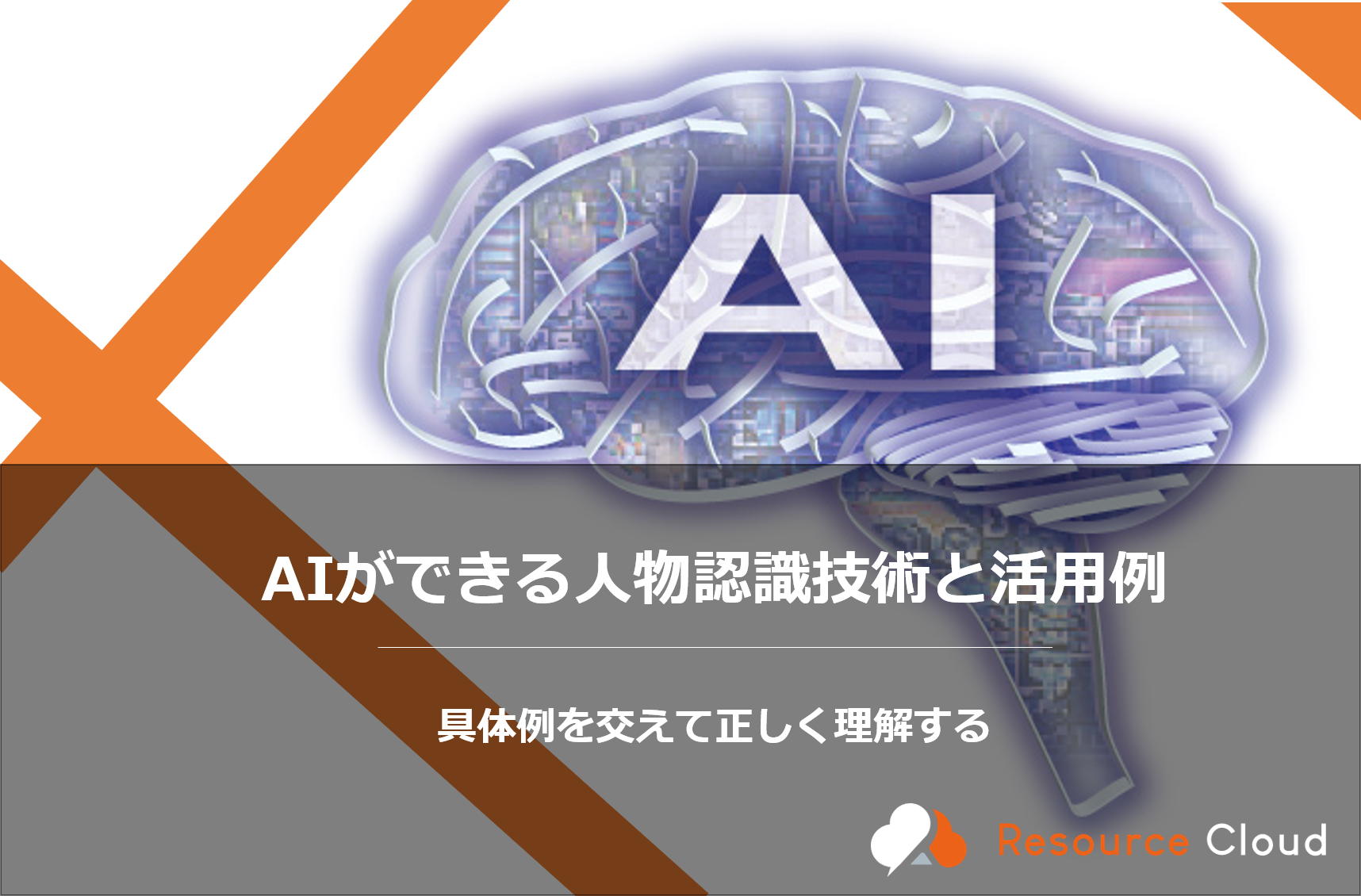
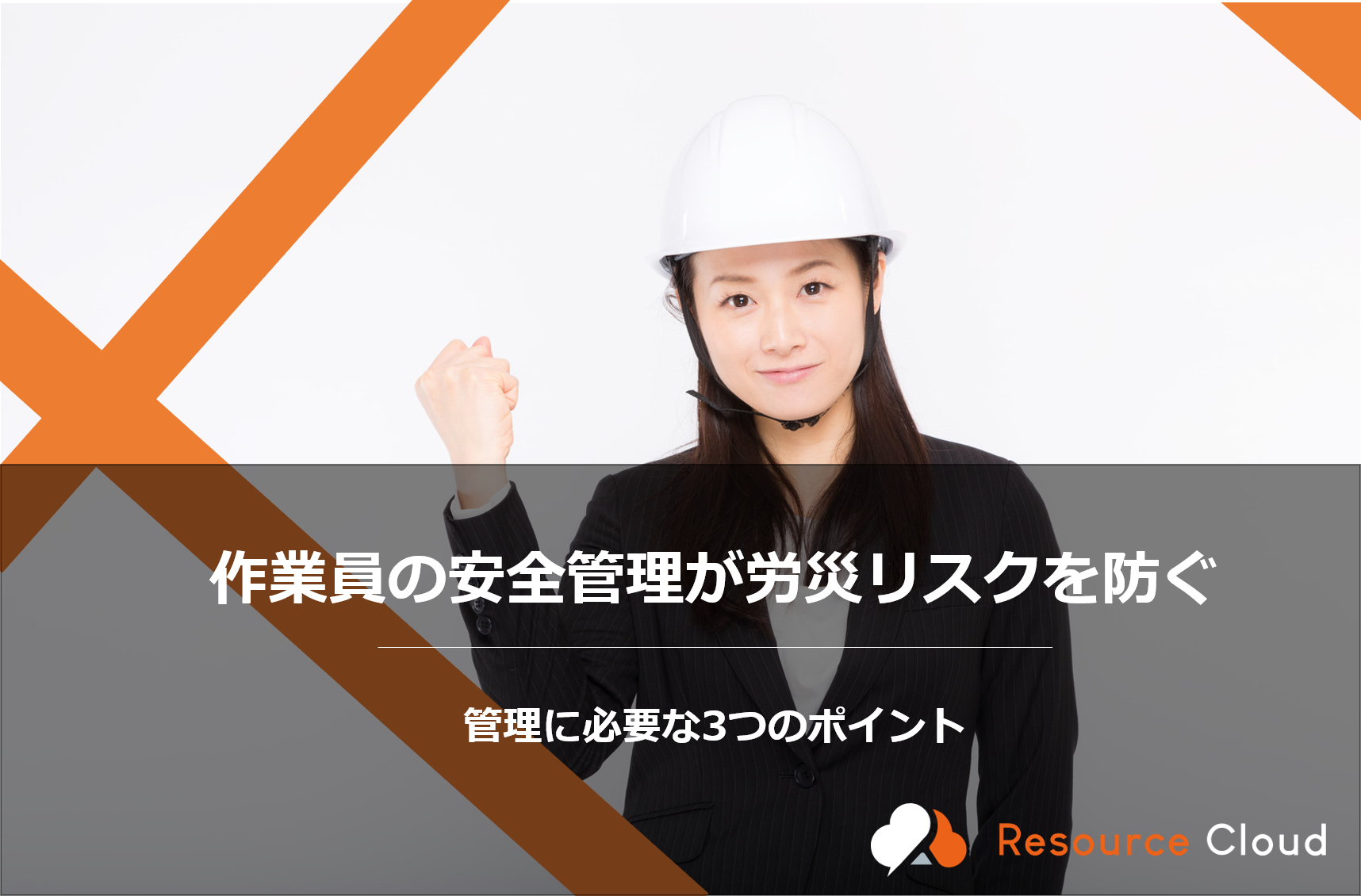
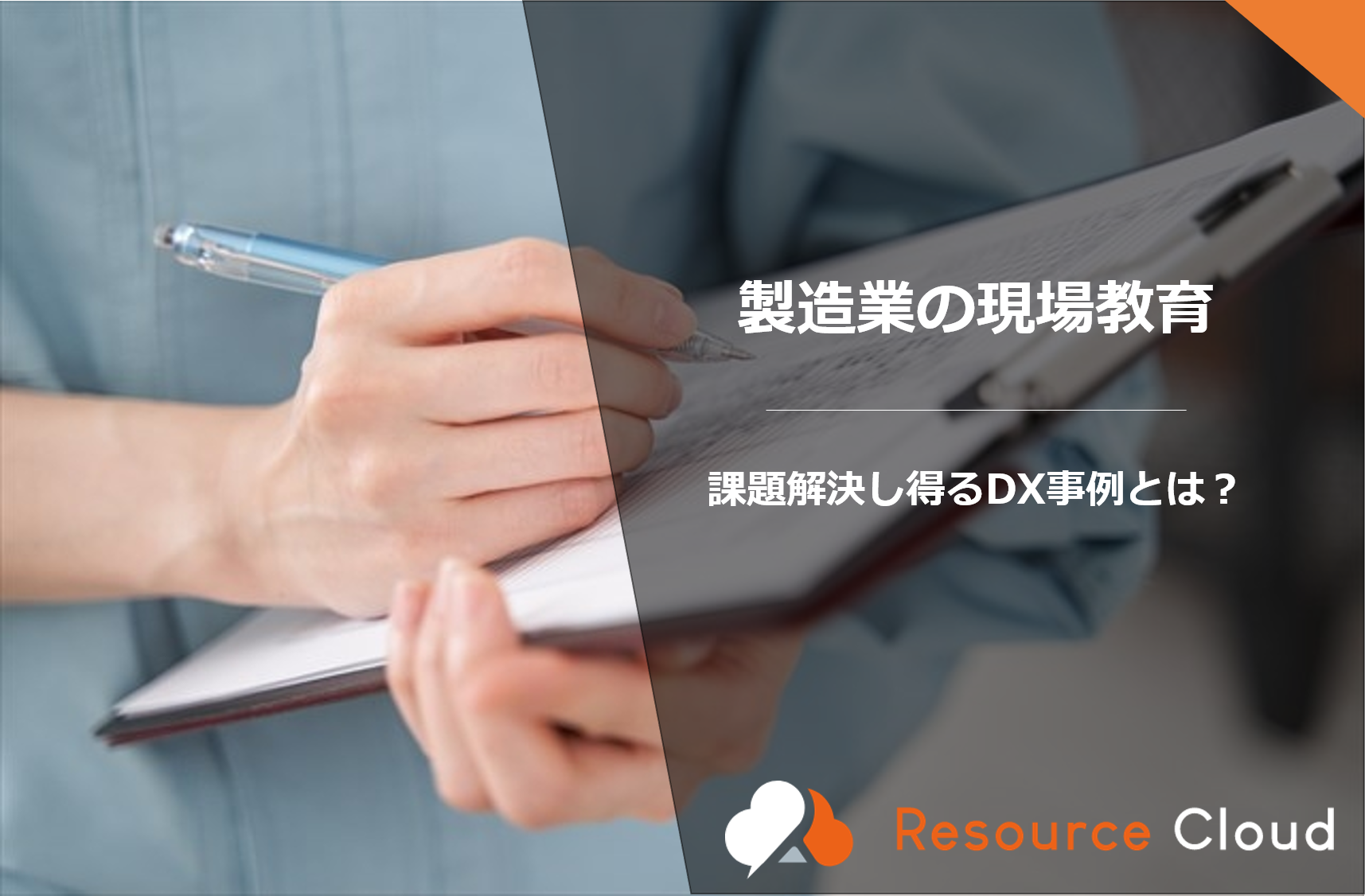
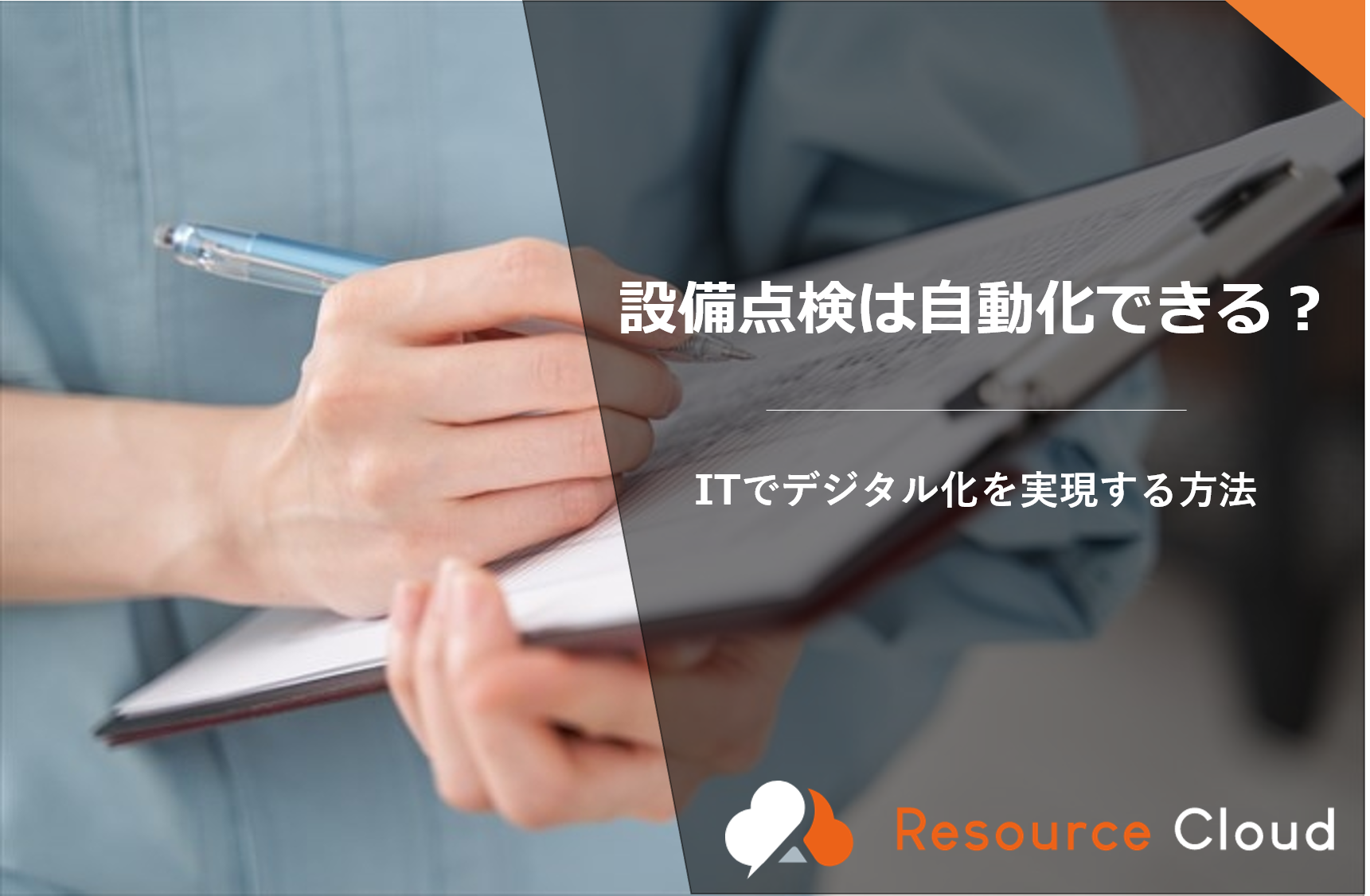
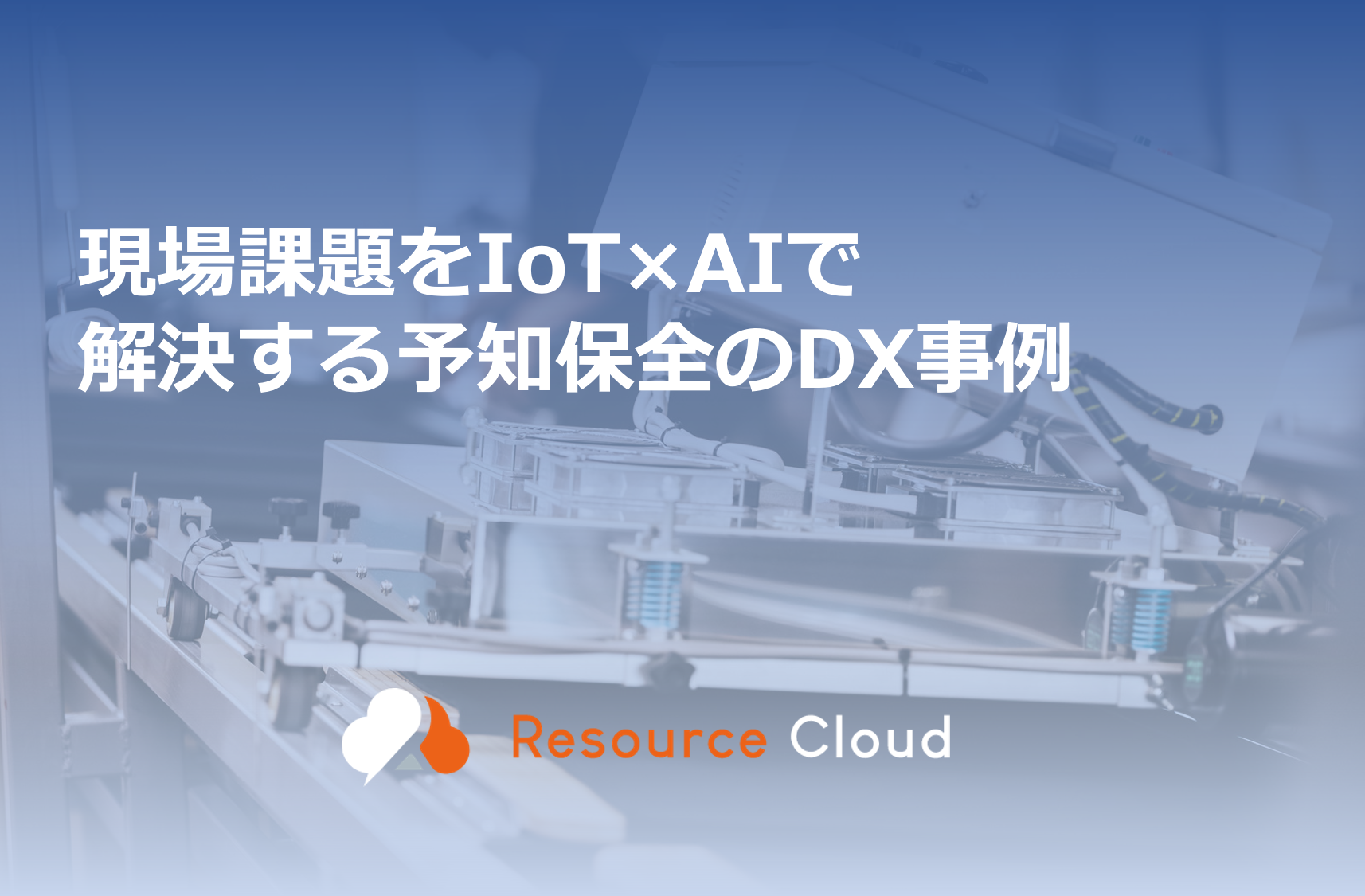
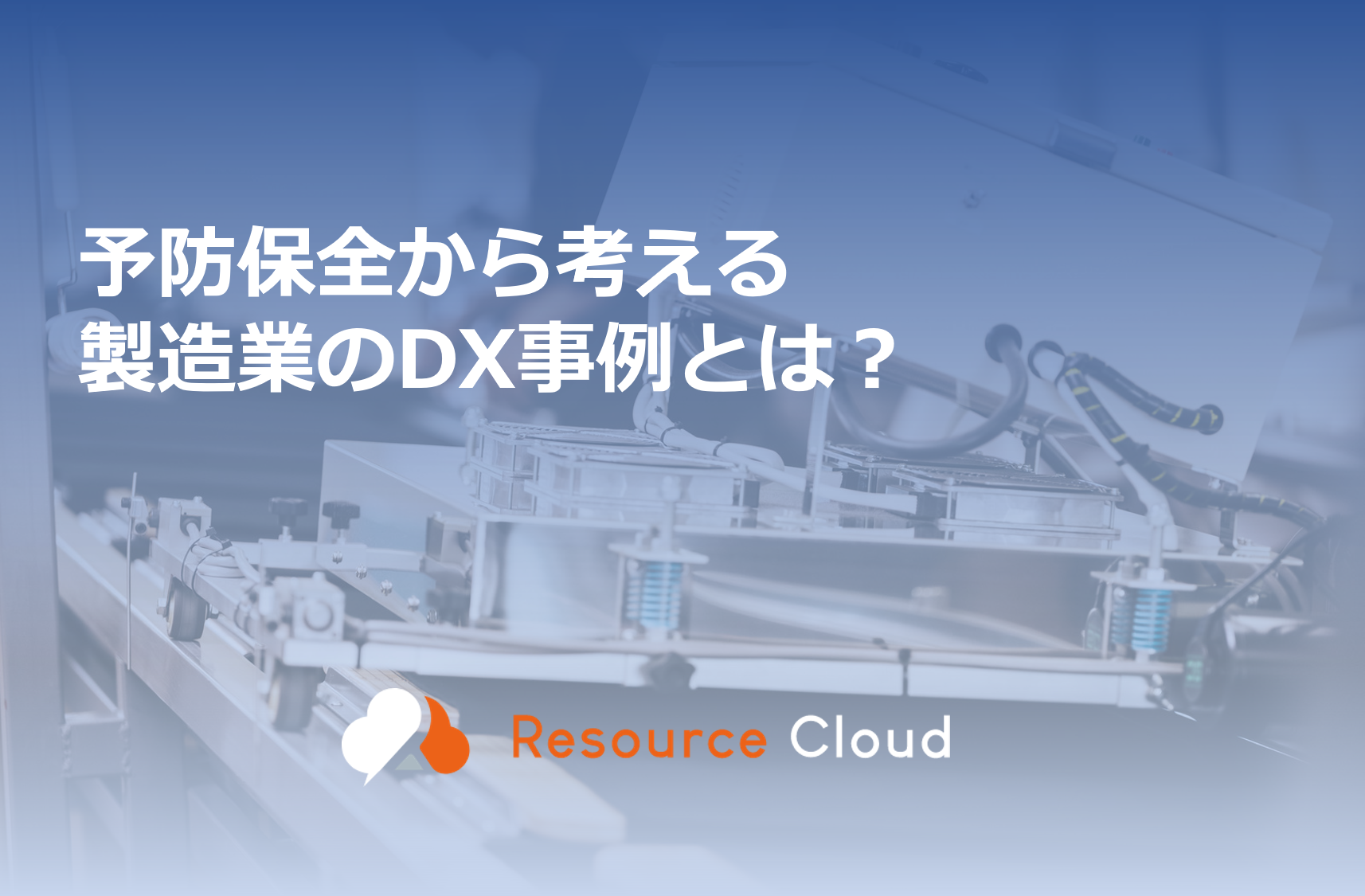
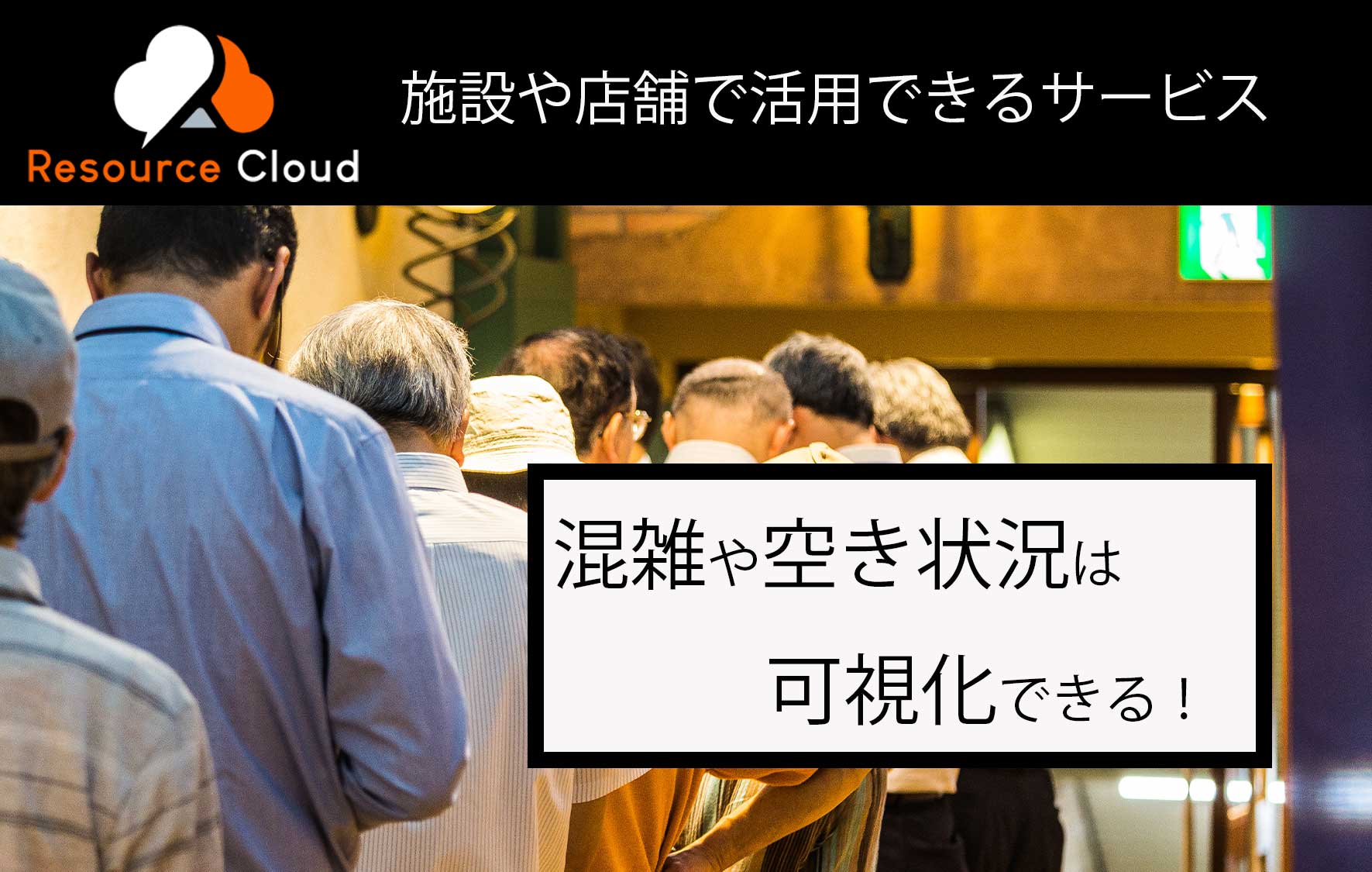
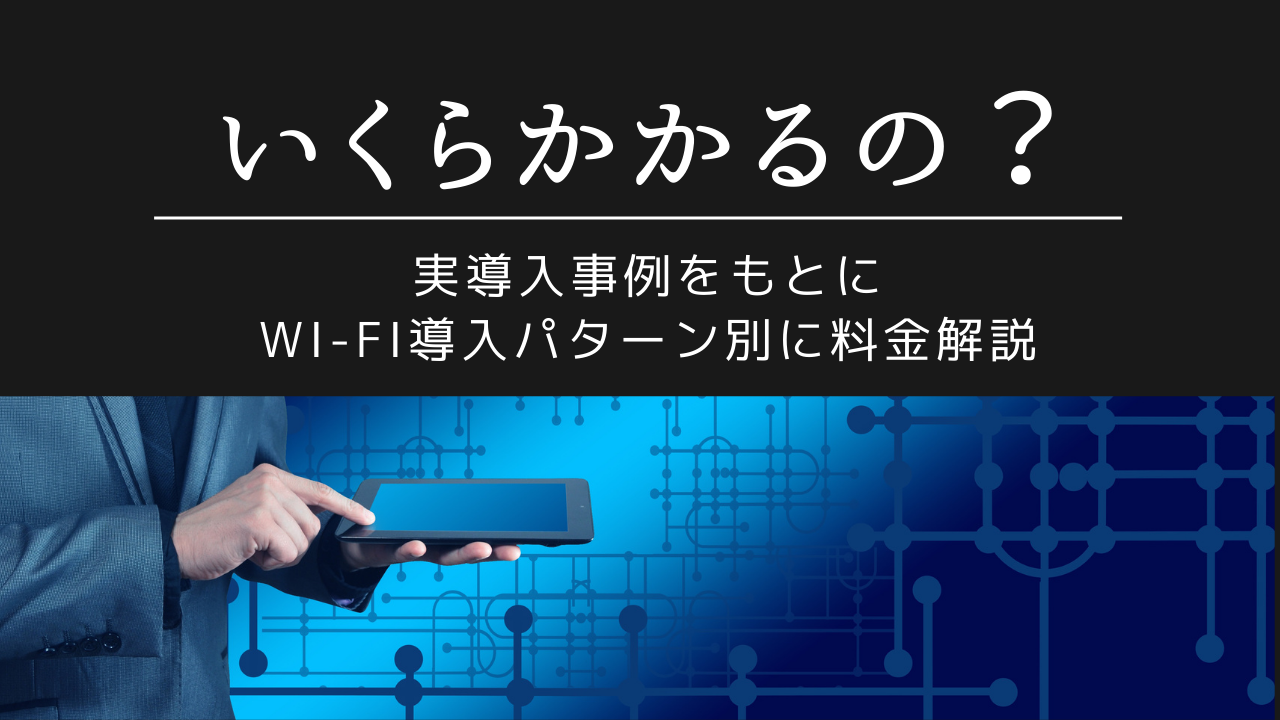
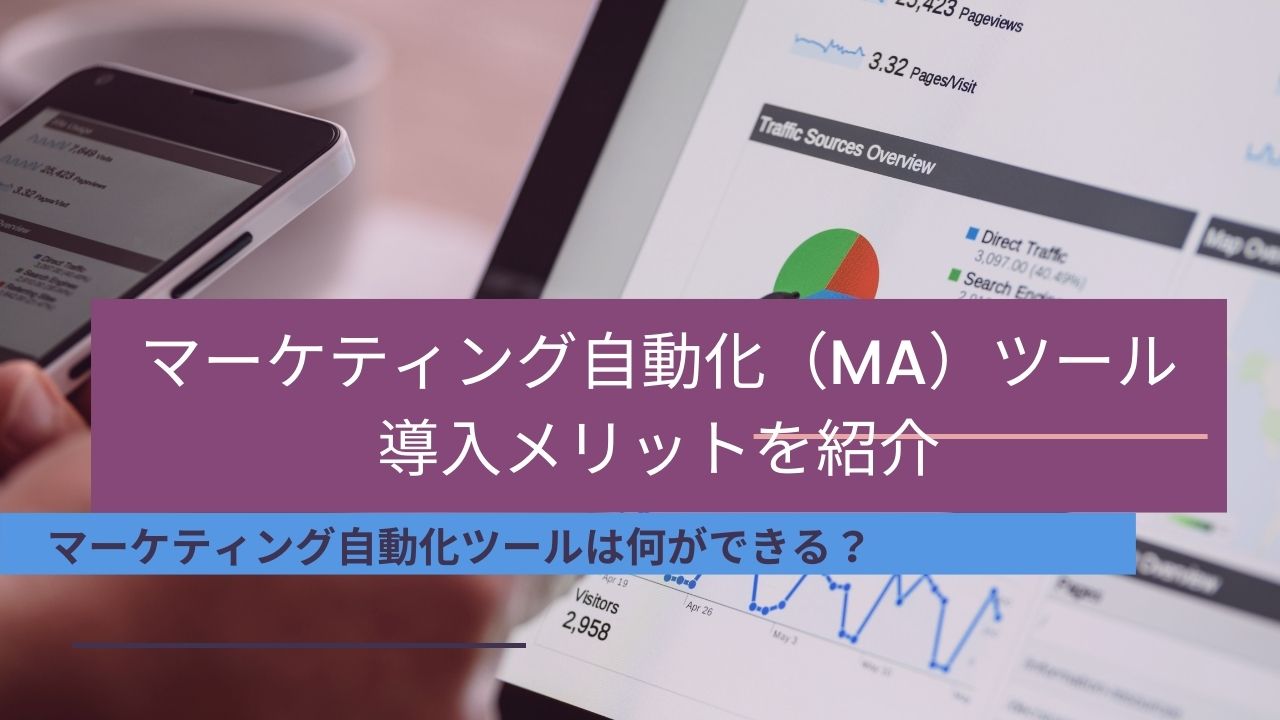
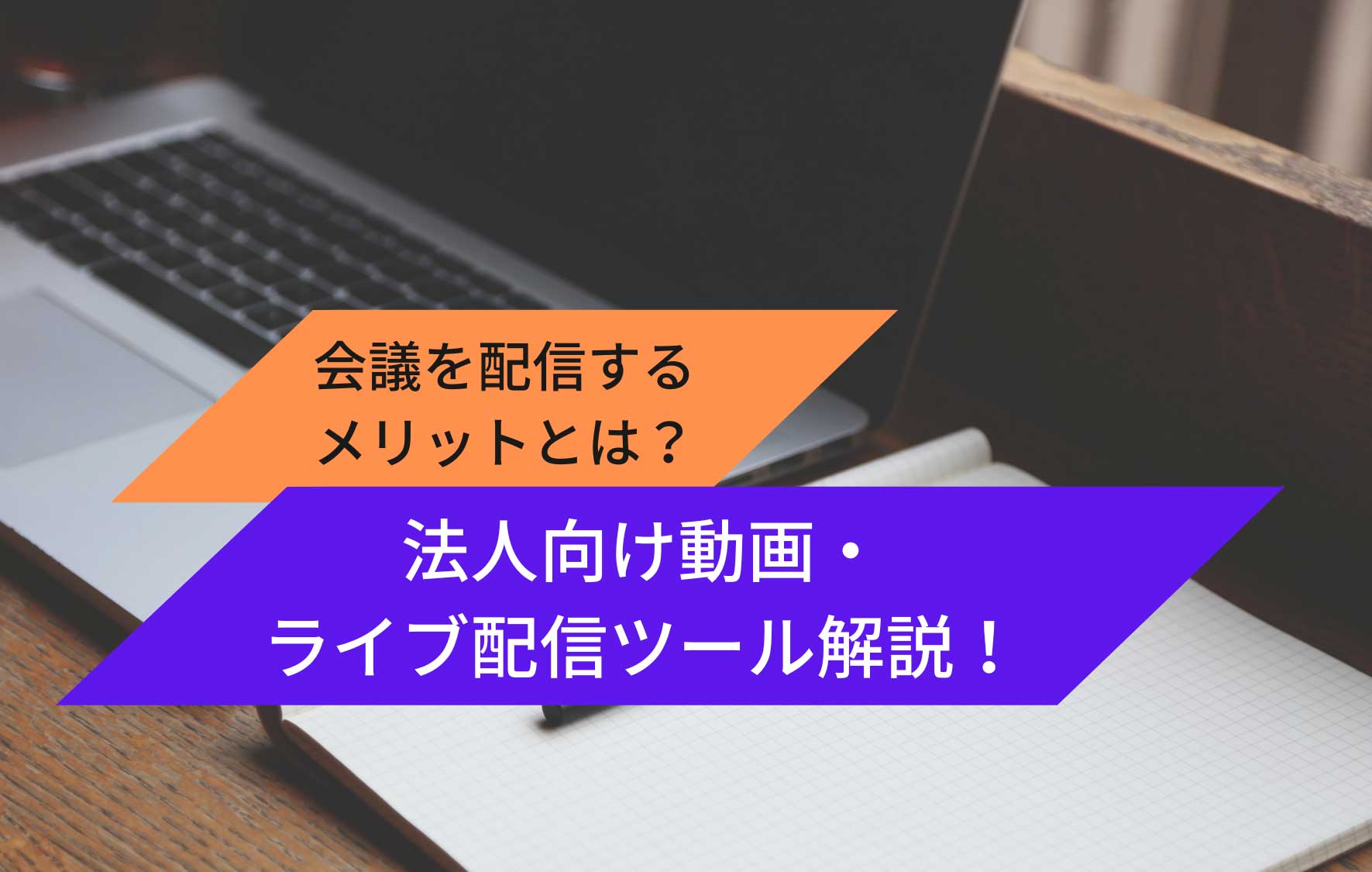
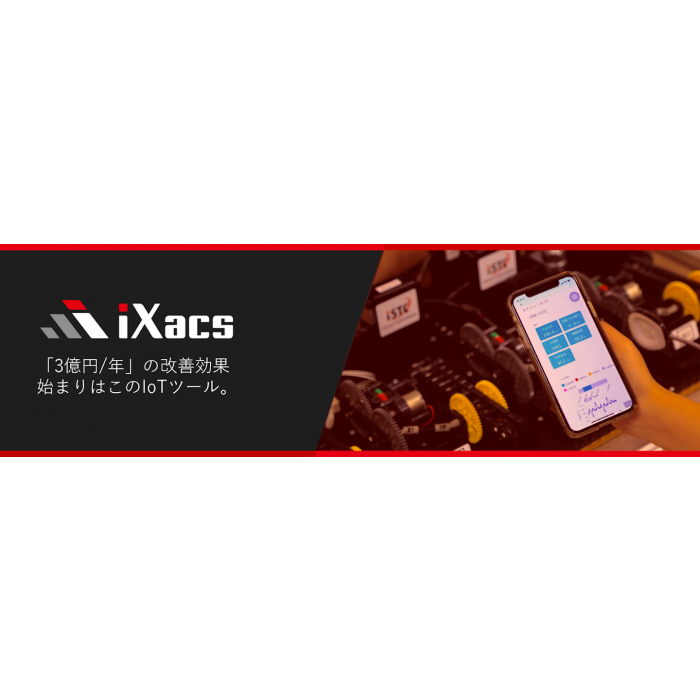
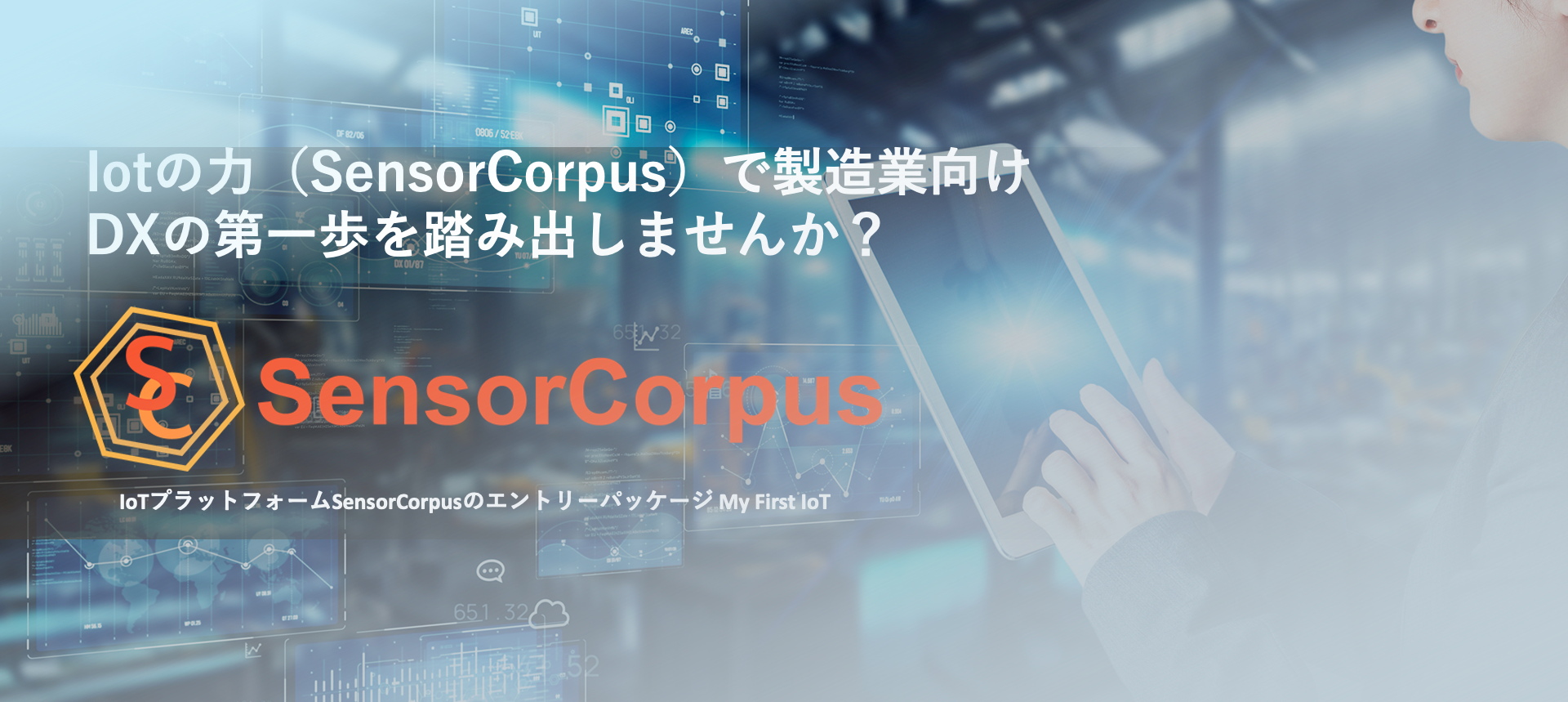
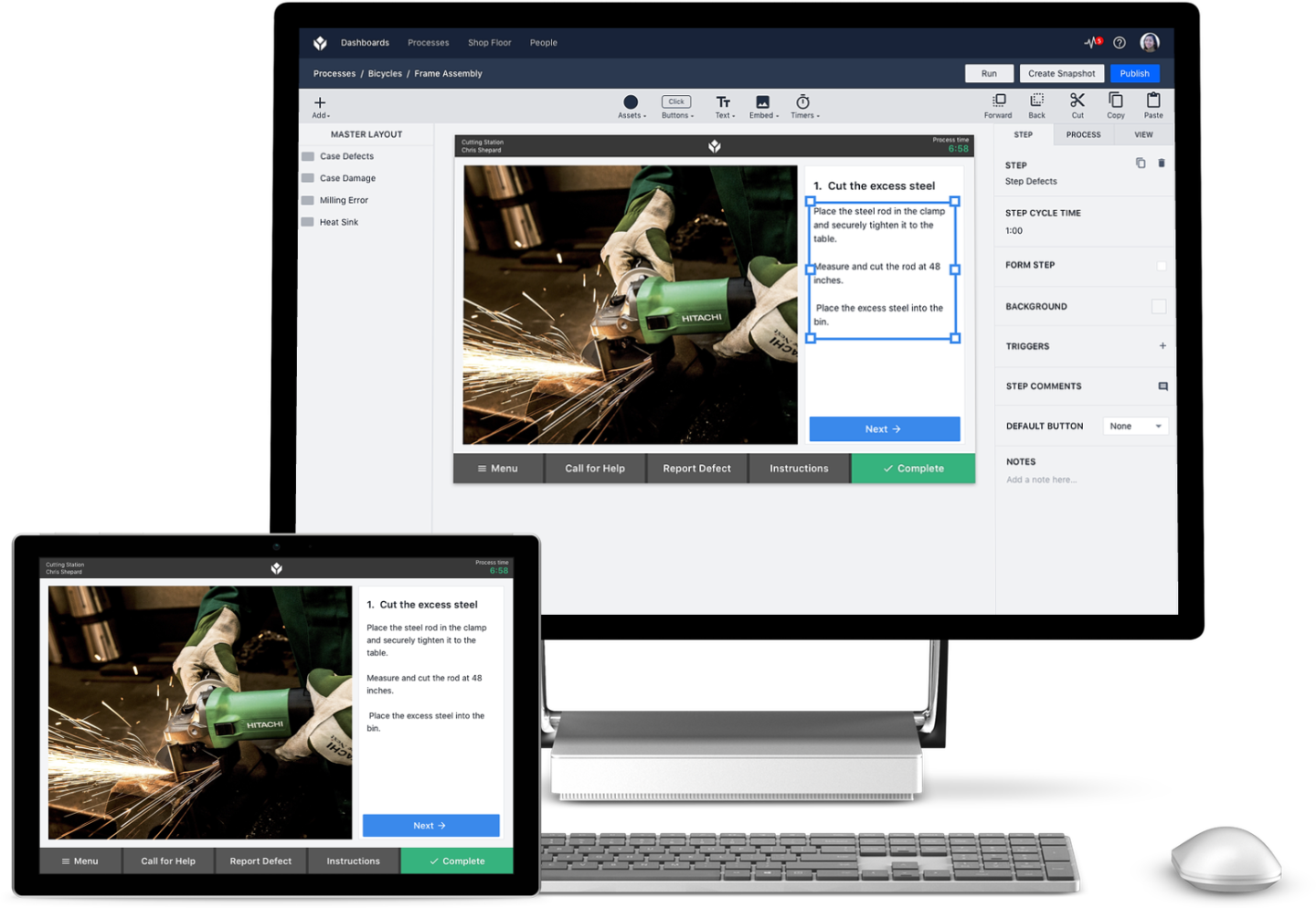
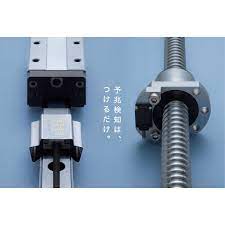
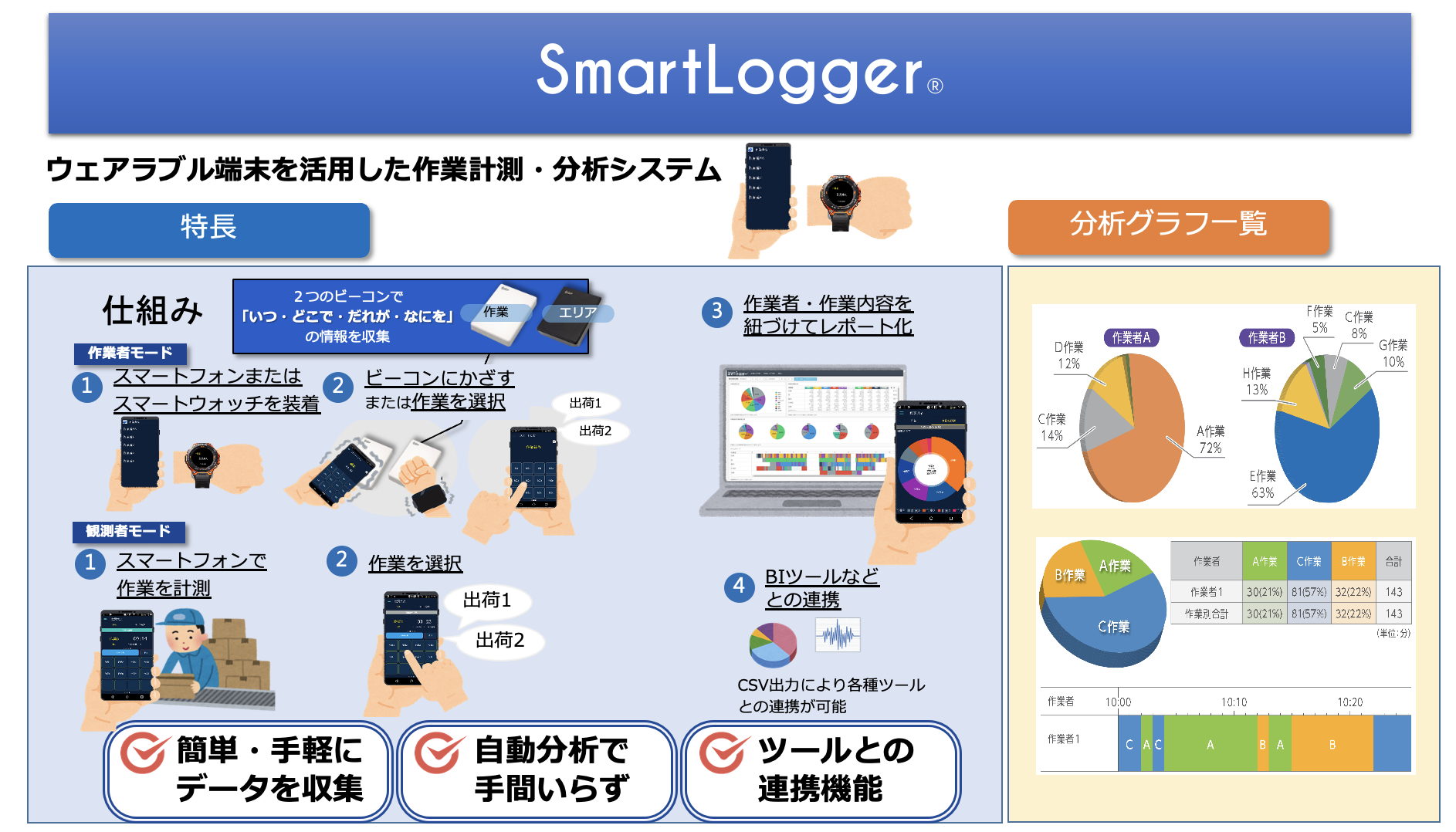
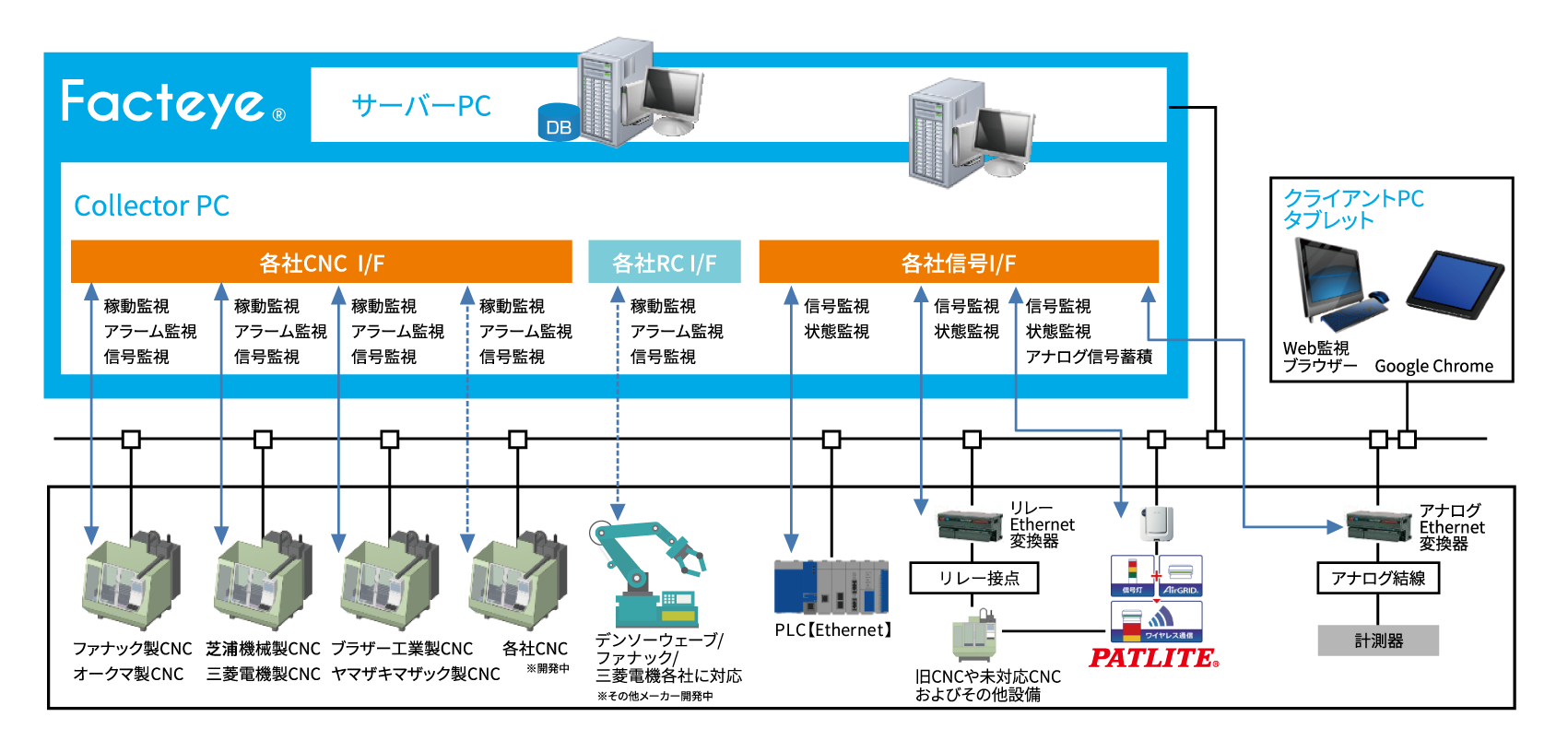
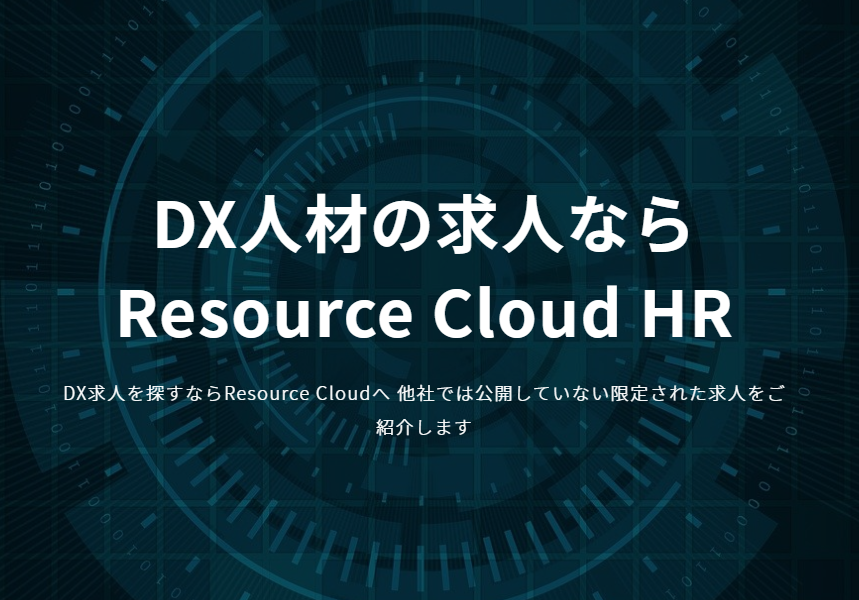
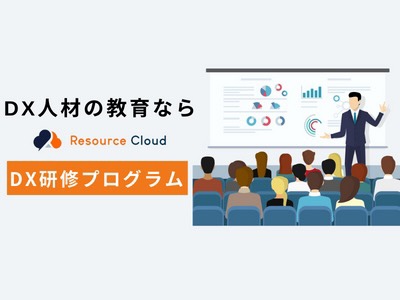
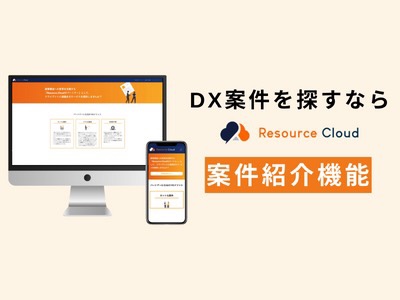