設備点検のデジタル化の方法とは?IoTで設備点検を自動化しよう
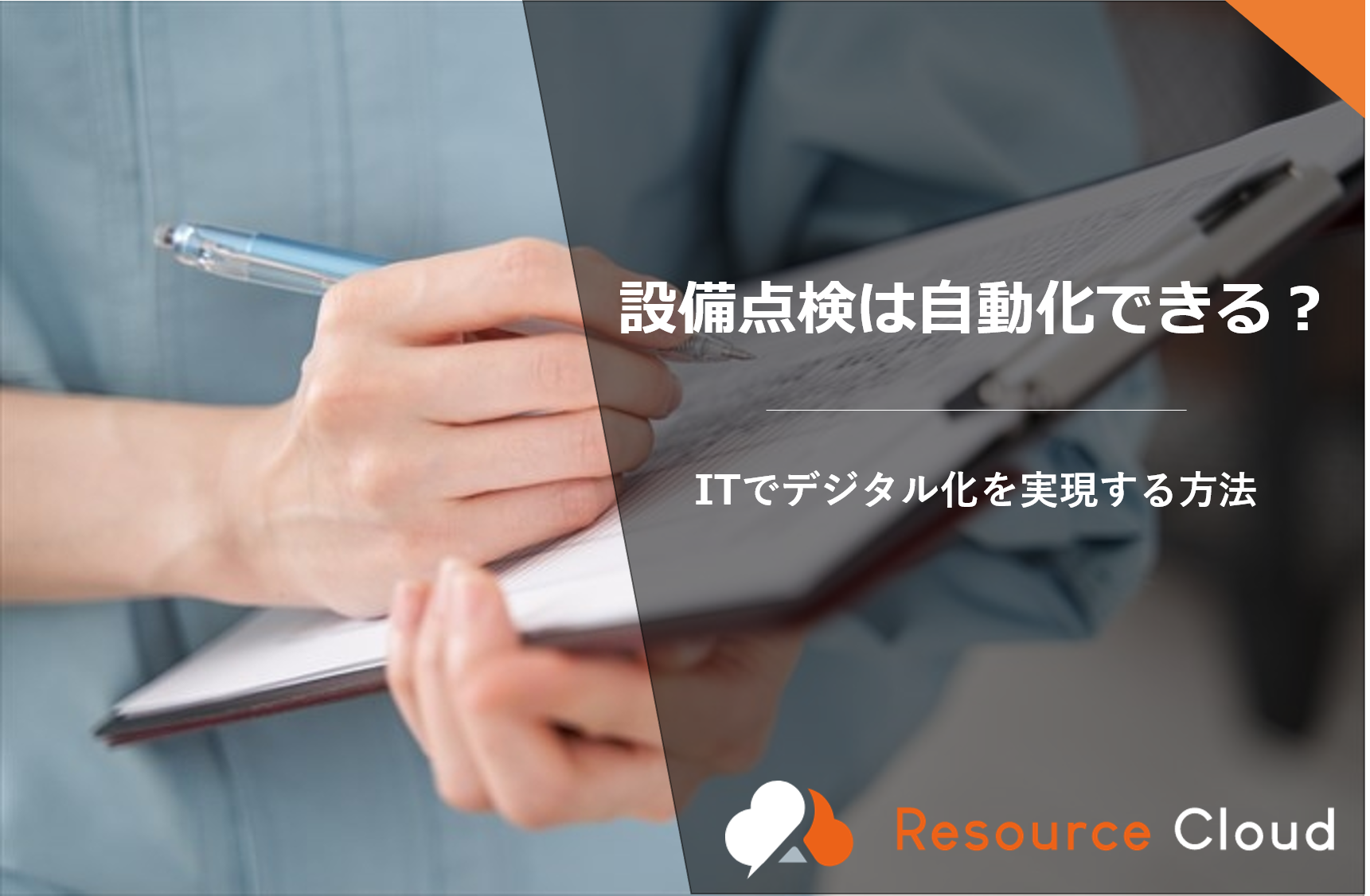
設備点検、という言葉を聞くと、どのようなイメージを持たれるでしょうか。巨大なプラント・工場、ビルの中に設置されている流量管理や空調設備などのインフラに関して、定期的またはトラブルが発生した際に、担当者が現場で点検作業を一つ一つ行なっている、もしくはすべての点検は自動化されている、あるいはその半々であるなど、人によってさまざまなイメージが連想されるのではないかと思います。
本記事では、そんな設備点検の内容や種類、現在の状況から課題点にいたるまで、さまざまな視点からご紹介していきます。
1.設備点検とは? 法定点検や自主点検について解説
工場に設置された生産設備が安定的に生産活動を続けるために必要なのは、最新技術が用いられた生産機械の導入だけではありません。日常の設備点検によって生産機械の異常を早期に察知し、大きなトラブルの発生を未然に防ぐことが重要なのです。そうしたことから、設備点検は生産設備の信頼性を担保するためにも欠かせない活動であるといえるでしょう。
設備点検には、法定点検と自主点検の二種類が存在しています。それぞれについて詳しく見ていきましょう。
1.1 法定点検
法定点検とは、労働安全衛生法や消防法、ガス設備事業法などの法律により、法的に実施が定められた点検を指しています。法定点検は、機械換気設備や換気設備、ガス設備などに実施が義務付けられています。また、これらの法定点検では、数か月や一年に一回などの周期が法律で定められています。
1.2 自主点検
自主点検はその言葉通り、特に法律によって定められた規定や規則は存在しません。自社で設定した点検項目や周期に基づき、工場設備の点検を行うものです。
また、自主点検は作業前点検と定期点検の二種類に分類することができます。作業前点検とは、実際に生産活動を実施する前に生産設備の点検を行うものです。原材料の投入設定など、目的とする生産物が問題なく生産されるように各種の設定に問題がないかどうかを点検します。一方の定期点検は、生産設備に故障などのトラブルが発生することを未然に防ぐため、生産設備に問題がないかどうかを点検していくものです。自主点検では、特に故障が起こりやすい箇所を重点的に確認することが重要となります。
自主点検を実施することで、生産ラインのロスや工場設備の故障、不良品の発生を防ぎ、生産設備そのものの寿命を伸ばすことができます。そのため、自主点検は生産設備が滞りなく稼働することにつながり、結果として会社全体のコストを削減することにつながります。
2.設備点検の具体的な方法
次に、現在まで多くの生産現場で採用されてきた設備点検の具体的な手法について説明していきます。
2.1 人の五感
従来から現在まで広く行われてきたのは、点検を担当する人間の五感を頼りに設備点検を行なう極めてアナログかつ属人的な方法です。例えば、ハンマーやライナー、回転盤、ベアリングのバランスなどを目視で確認する、機械の音を聞き、通常とは異なる音を察知する、通常とは異なる匂いで異常を検知する、などの手法が採られます。
ベテランになってくると、ポンプが稼働している機械室に入っただけで、その音から以上箇所を特定する事ができるようになるというのですからすごいものです。
2.2 システムやメーター
生産設備のシステムに登載されているメーターなどの数値を頼りに設備点検を行なう方法です。例えば、メーターに普段の数値とは異なる値が表示されていた場合、何らかの異常がその生産設備に発生したと判断することが可能です。古い設備ではアナログメーターであり、機械設備と連動した値を常時表示し続けるのが一般的な方式です。デジタル表示のメーターであっても、現場でのスタンドアロンであり、ネットワークに繋がるような事は無かったのが一般的な子の業界の常でした。
2.3 アナログ計器の問題点
これまで広く行なわれていたのは、上記のようなアナログな手法に頼る設備点検でした。この方法の問題点として、設備点検の対象となる生産設備や機械の状況を常に把握することが難しい点が挙げられます。従来のアナログ計器による表示では、読み取りが必要なため生産設備の状況を継続的にモニタリングすることが困難です。同様にデジタル計器であったとしても計器の示す値の変化を記録しようとした場合、その作業を行う担当者を設けておく必要があり、人材と記録のための作業工数が余計に掛かることになります。
さらに、アナログ計器による設備点検では、あくまでも人間を介した作業が必要です。そのため、担当者が紙面のチェックリストを持ちながら点検を行い、手書きでチェック済みの印をつけ、留意点を書きとめてチェックリストをバインダーにはさみ、事務所では事務員が日次の集計を行うといったような管理が行なわれることになります。この一連の作業の中で、チェック漏れや記載事項の誤読、チェックシートの紛失などのケアレスミスの発生しやすいことは否めません。
このように、従来のアナログ計器に依存した設備点検には、多くの問題点が内包されていると指摘することができるでしょう。
3.設備点検における課題感
次に、設備点検におけるさまざまな課題についてお伝えしていきます。人の目や手による点検作業や入力作業が、多くの課題の原因となっています。
3.1定期点検における工数
定期的に行なわれる設備点検は、多くの場合それぞれの生産設備を使っている製造ラインの担当者が行ないます。特に詳しい知識が必要な箇所については、設備保全専門の担当者が行うことになります。
そのため、定期点検では本来の業務である生産や製造以外の余計な工数が担当者にかかることになります。そうした工数がかかるだけ、当然必要なコストも増大する結果となります。
3.2 設備点検業務の漏れ
先ほどもご紹介したように、人間が設備点検を行なっている限り、そこにはケアレスミスが発生する可能性があります。「点検していたつもりだったのに、つい見逃していた」「チェックリストを見損ねていた」「計器の値を読み間違えた」などの原因で設備点検業務に漏れが起こることは、或る程度見越しておく必要があるでしょう。
3.3 点検データの入力作業
設備点検によって取得したデータをそのままにしていても意味がありません。設備の経年による変化や何らかの異常を察知するためにも、蓄積されたそれらのデータは分析を行っていく必要があります。そのため、データは何らかの形で記録していく必要があります。実際の現場では、Microsoft Excelなどの表計算ソフトを使って入力が行われている場合が多いようですが、当然その作業に対する工数が必要となるうえ、入力ミスなどが発生する可能性は否めません。
表計算ソフトに入力はなんとかしたものの、そのまま放置されている例も後を絶ちません。取得しなければならないデータが多くなればなるほど、その分析作業は面倒にもなるものです。分析作業に時間を確保するためには、データの収集・蓄積段階に時間を掛けるのではなく、できるだけ自動化しなければならないという発想になります。
4.設備点検をIoTで自動化はする方法
ここまで、主に人間の手による設備点検についてご紹介してきました。ここからは、そのような設備点検における自動化の可能性についてお伝えしていきたいと思います。
4.1 IoT導入による効率化
現在、設備点検の自動化を探るうえで注目されているのが「IoT(Internet of Things)」です。IoTとは、さまざまな設備がインターネットに接続され、相互に情報を通信しあい、データとして現場を化し可視化した上で最適化を行う仕組みを指しています。
IoTにより、生産設備の設置されている場所まで赴かなくても、インターネットを経由した監視システムにより設備の状況を確認できる、点検に必要な入力作業をAIを導入したチャット形式で行う、異常が発生した際の通知が手許のウェアラブルデバイスに即時に届く、などの使い方がすでに現実のものとなっています。また、担当者からの入力だけではなく、AIが必要と判断した点検項目をチャット経由で担当者に提示するシステムも実現ずみです。さらに、点検結果の入力についても、従来のパソコン入力などに頼ることなく、IoTで把握したデータに基づき閾値などを判断してシステムがすべて自動で行なってくれるサービスが提供されています。
このように、IoTが設備点検の現場に投入されることにより、その作業は大きく効率化されています。これまですべて人間が担当していた作業の多くが自動化、システム化されることにより、必要な工数を大幅に削減し、それに伴う時間や資本などのさまざまなコストを低減することにつながっているのです。
4.2 全自動化は難しい
それでは、設備点検の作業をすべてIoTにより自動化することができるのでしょうか。
結論からお伝えすると、設備点検に必要なすべての作業を自動化することは、現実にはなかなか難しいようです。
その理由には、未だに多くの設備点検が人間の五感によって行なわれている状況にあります。先ほどお伝えしたように、人間の嗅覚や聴覚などの諸感覚と、これまでの経験値に基づいて設備の異常を検知する点検方法は広く行われています。最近ではようやくIoTで接続されたセンサーを用いて現場の環境をデータとして捉えることが出来れば、それらのデータから判断や自動化ができるようにはなってきました。
しかしながら、まだまだアナログメーターなどのセンサーではデータ化できず、ネットワークにも繋がっていない設備機器が多量に存在しています。近年ではセンサーのみならずIoTカメラを用いて生産設備の監視を行うなど、人間の持つ視覚の一部を代替するシステムが登場してきています。しかし、IoTの進展やAIの学習などによって現場での点検作業を完全に代替することは未だに実現してはいないのが現状です。
しかし、たとえ一部であっても、可能な部分はIoTを活用したシステムに設備点検の作業を行なわせることにより、これまで設備点検に必要だった工数やコストを大幅に削減できることは間違いありません。
5.設備点検を自動化するIoTサービス紹介
ここまで、設備点検の意義や種類、その方法、課題点、IoTを導入した効率化などについて、幅広くご紹介してきました。
最後に、設備点検に関してIoTを用いたサービスを提供している、LiLz Gaugeについてご紹介します。
5.1LiLz Gauge
LiLz Gaugeは、低消費電力IoTカメラと機械学習を活用し、アナログメーターの目視巡回点検を効率化するクラウドとエッジコンピューティングを融合したサービスです。1日3回撮影できるカメラにより、電源のない現場でも遠隔点検をすることが可能です。また、画像解析と機械学習により、計器の値を自動で読み取ってくれるため、点検時の入力作業を効率化することができます。さらに、これらのデータを取得して管理システムなどと連携することができます。
電源やネットワークの工事や、大規模な設備投資が必要ない点も大きな魅力となります。
ここまでご説明してきた設備点検の自動化を推し進める一手となることでしょう。
株式会社INDUSTRIAL-Xでは、最も効率的にクラウドとエッジで判断を行うにはどうすればよいか、その最適化や判断ツールの導入支援およびそのコンサルティングを多く手掛けています。当社で導入サポートしますので、お気軽にご相談ください。
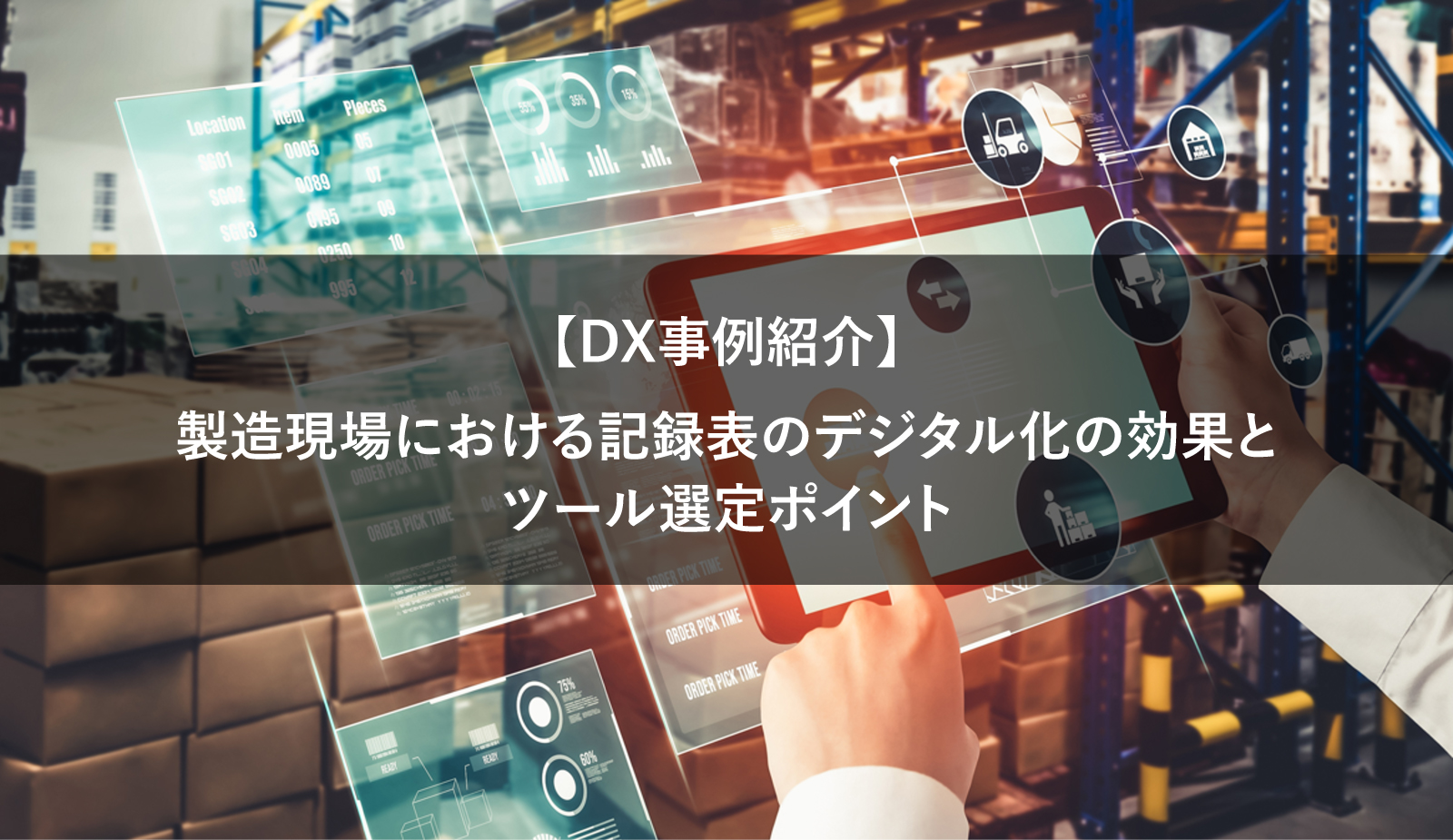
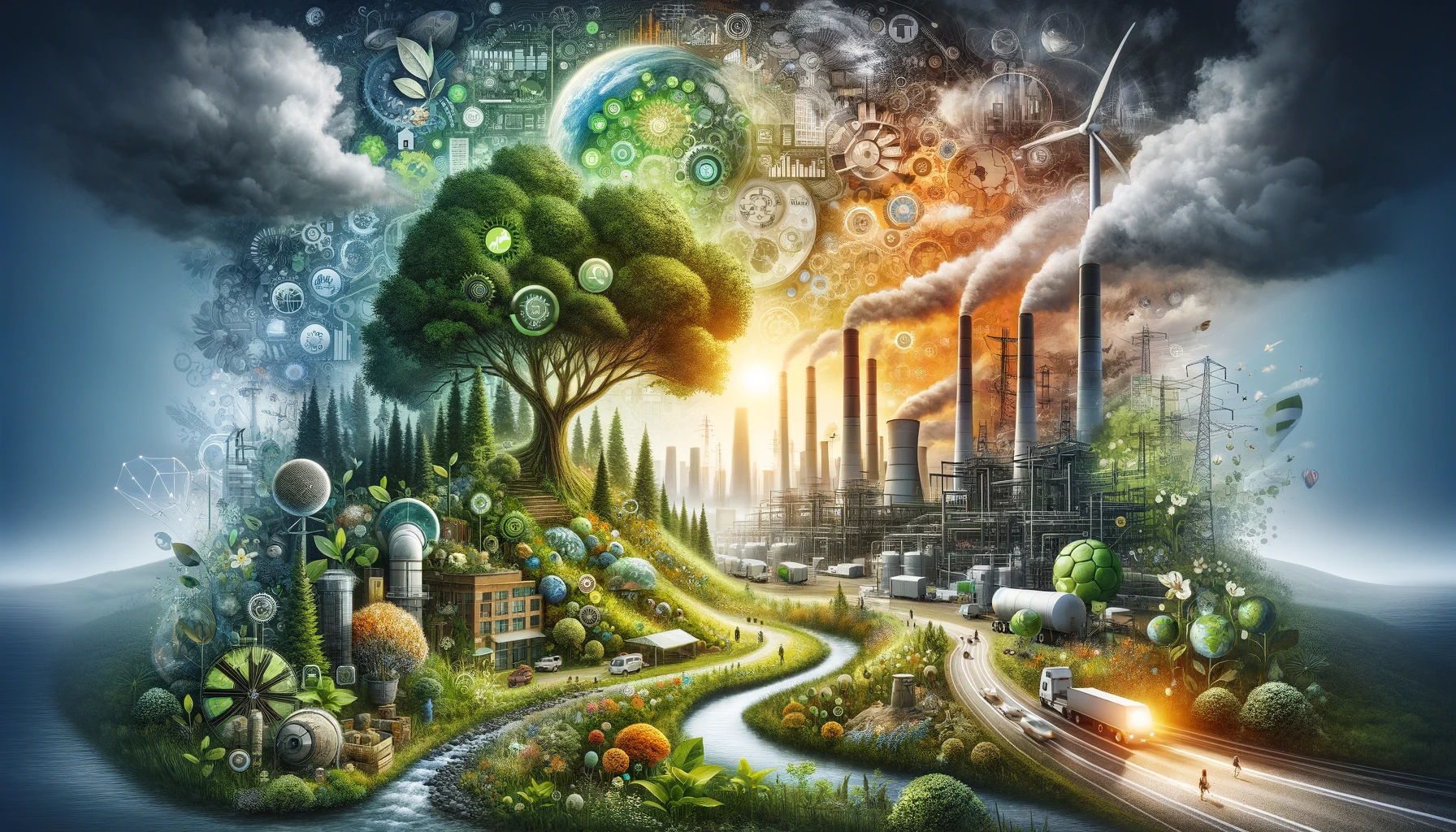
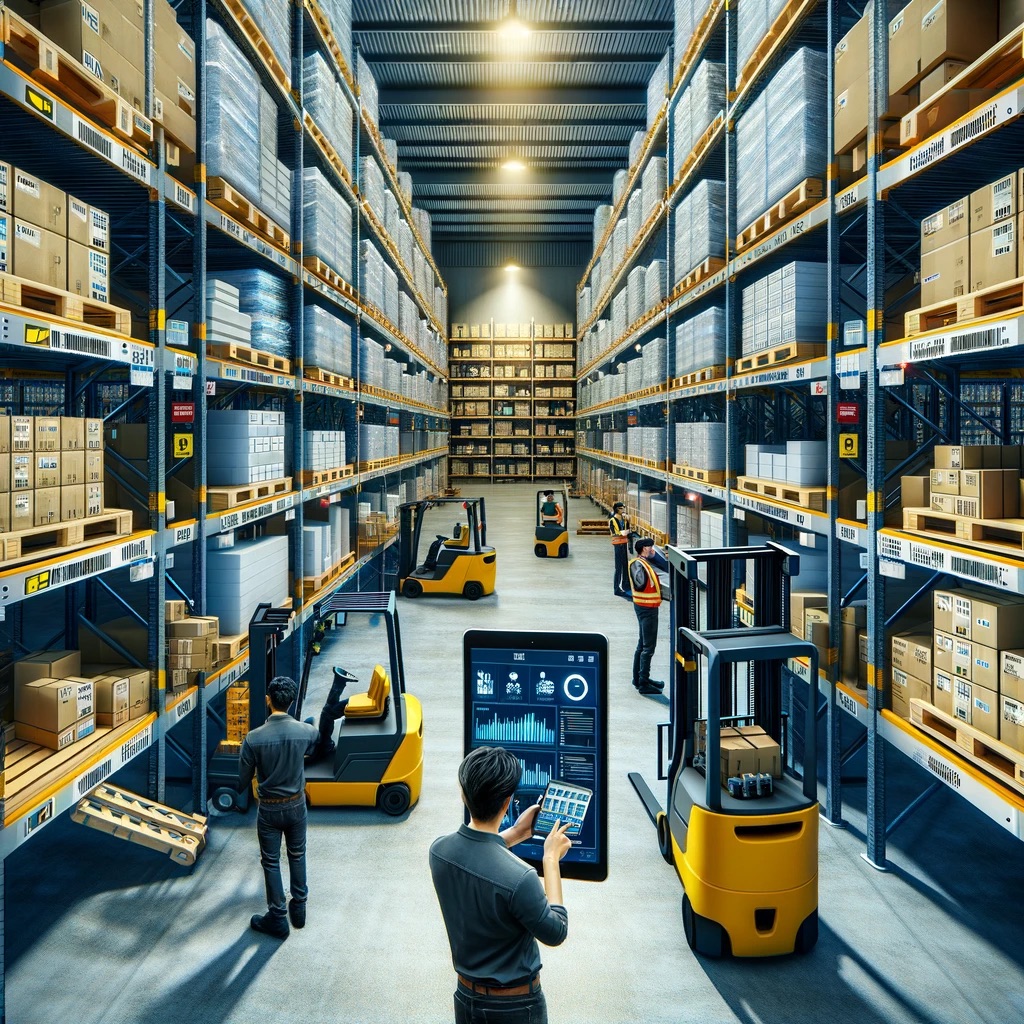
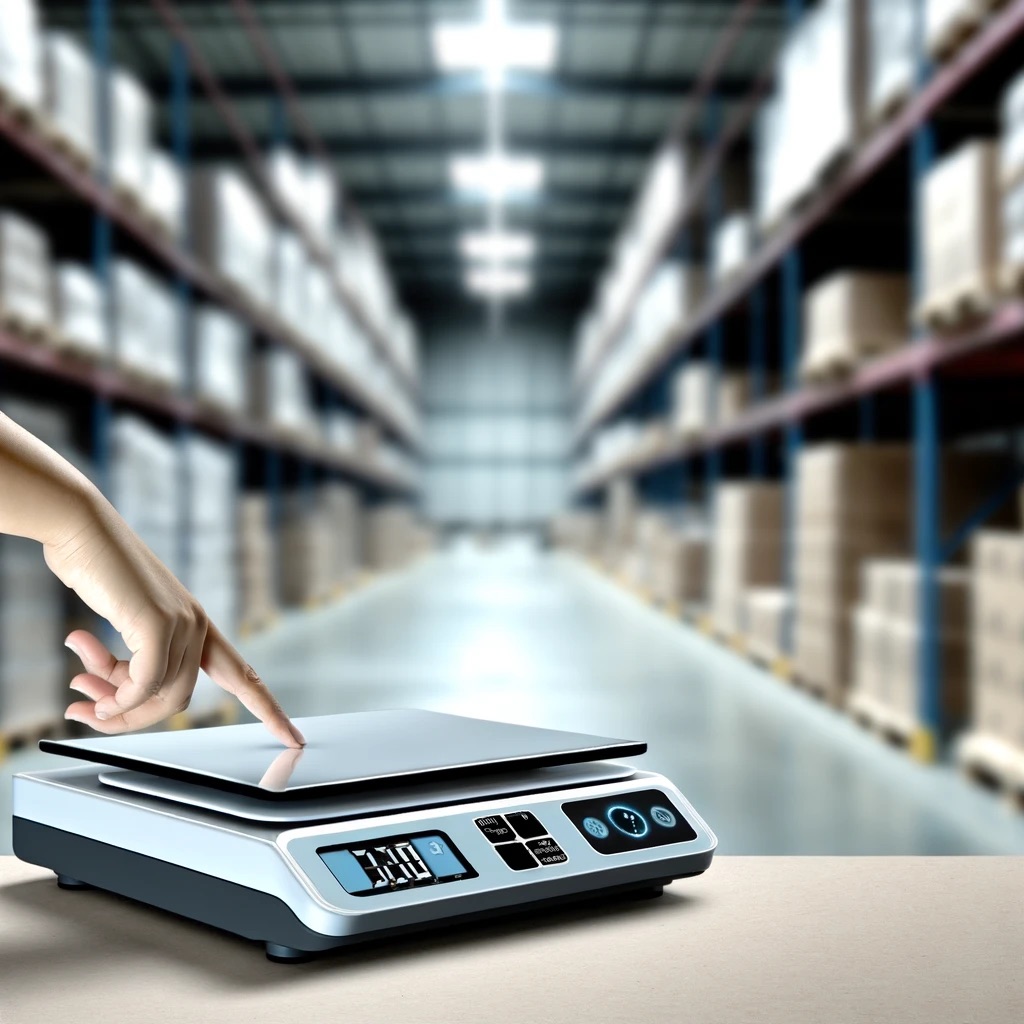
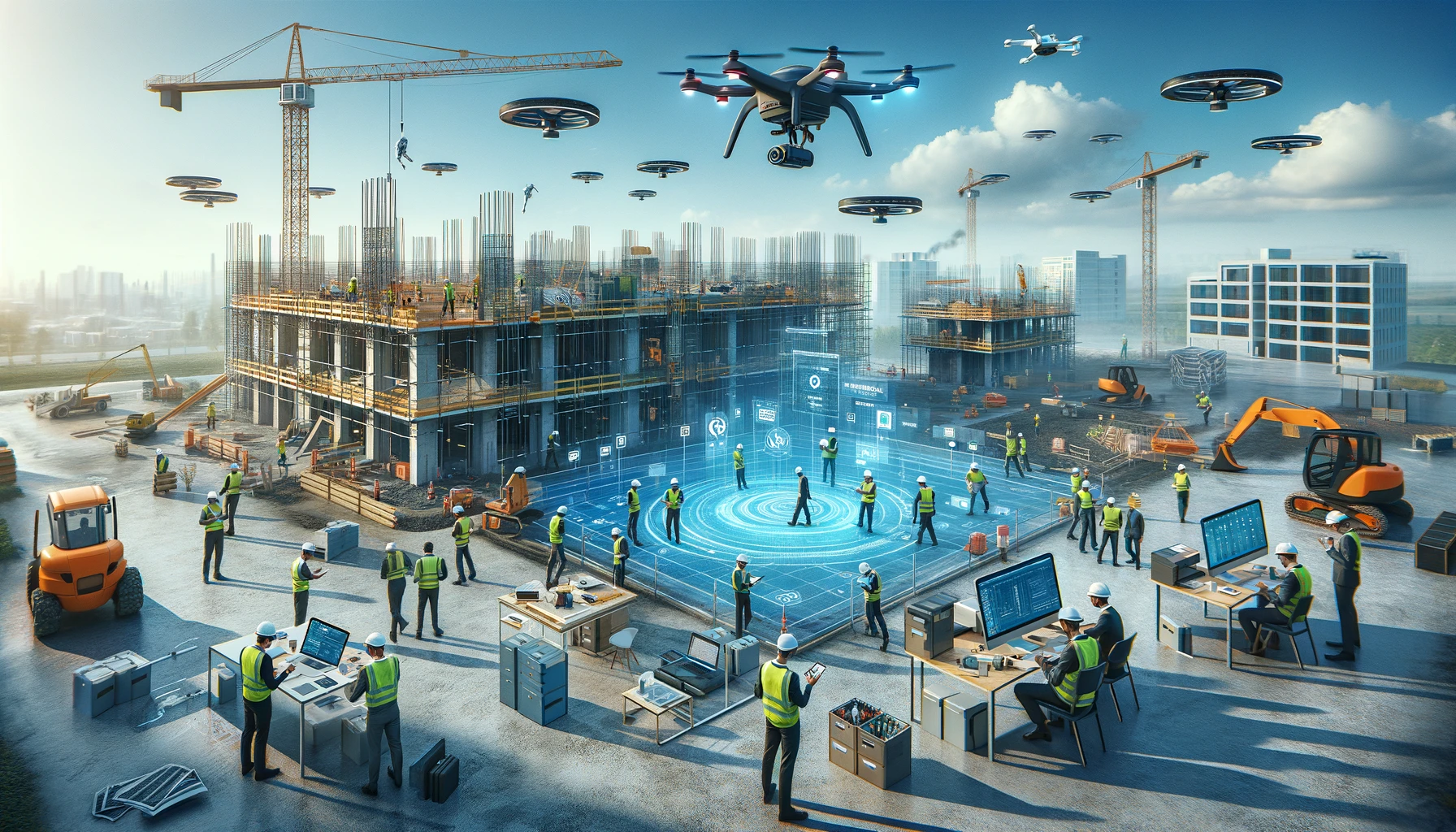
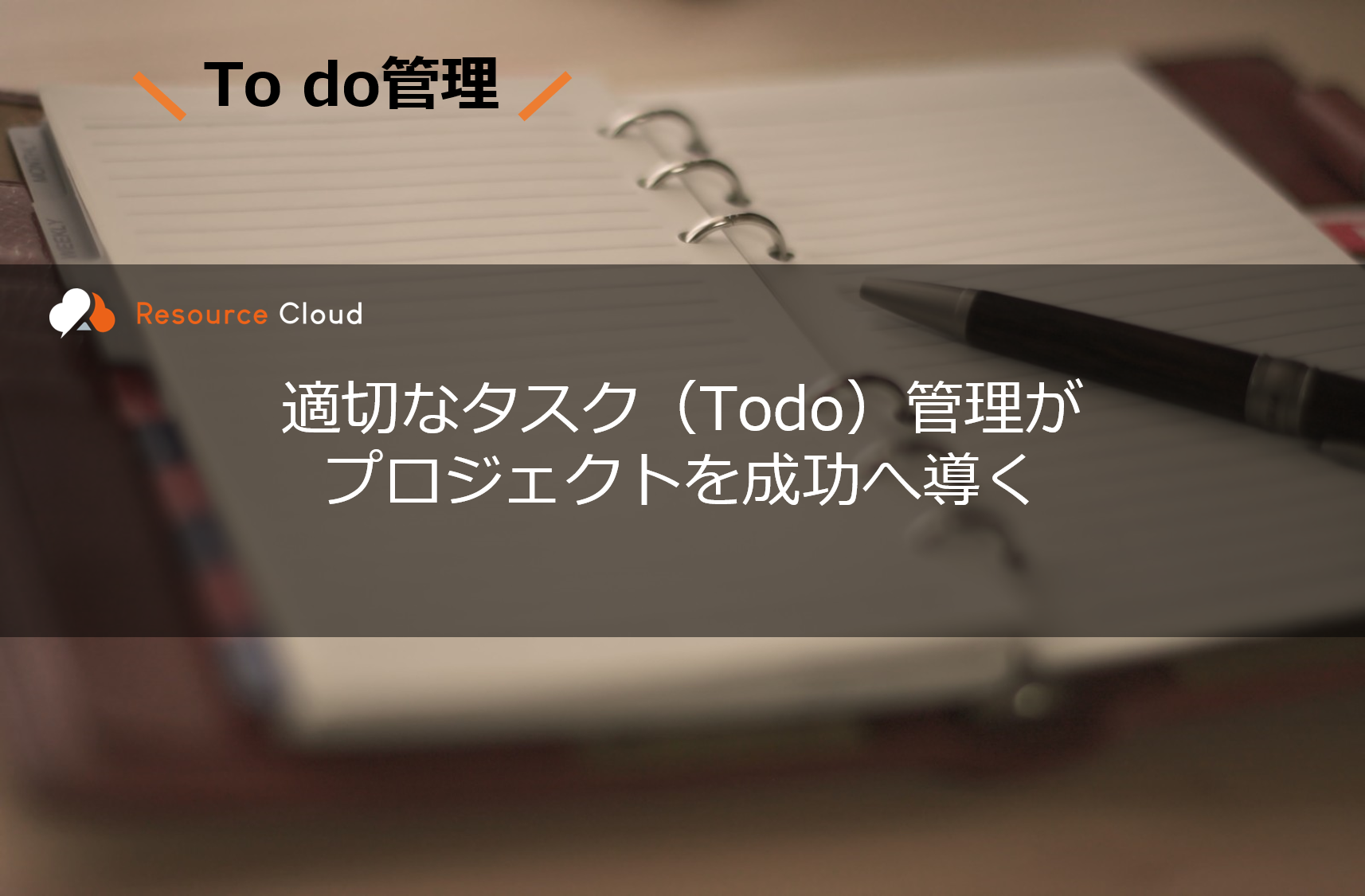

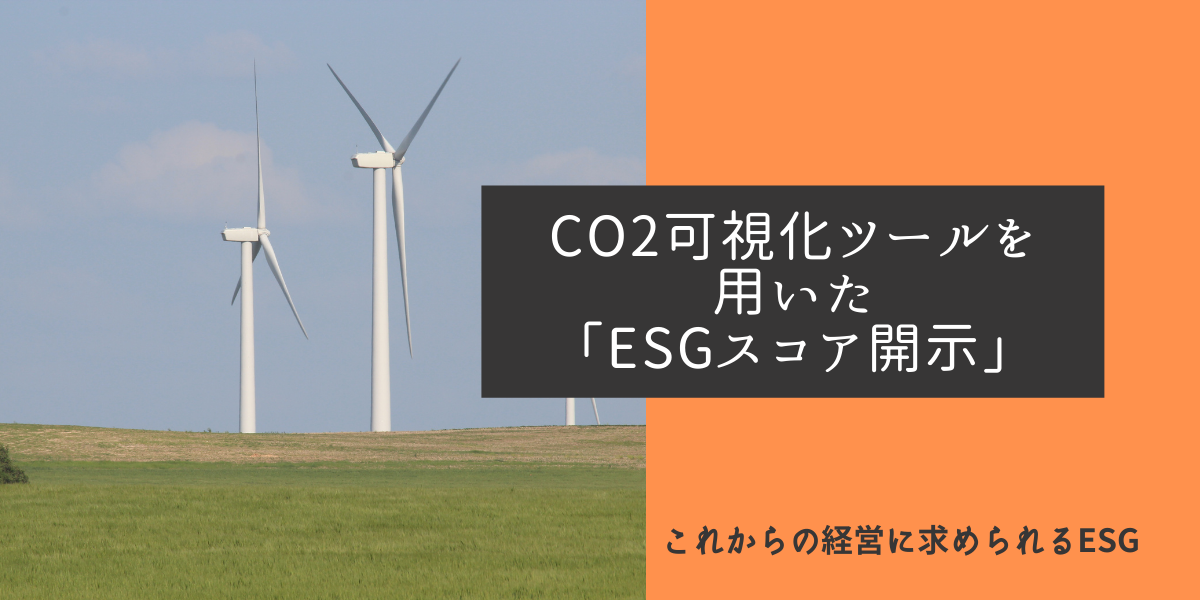
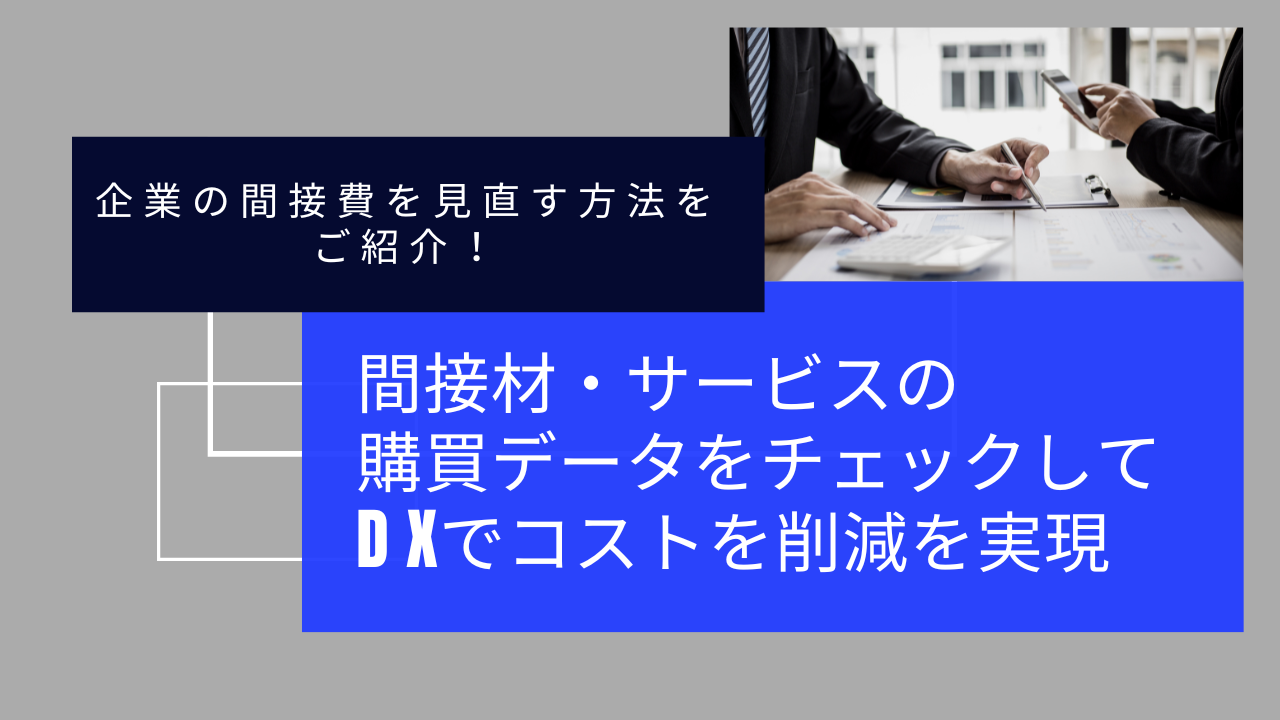
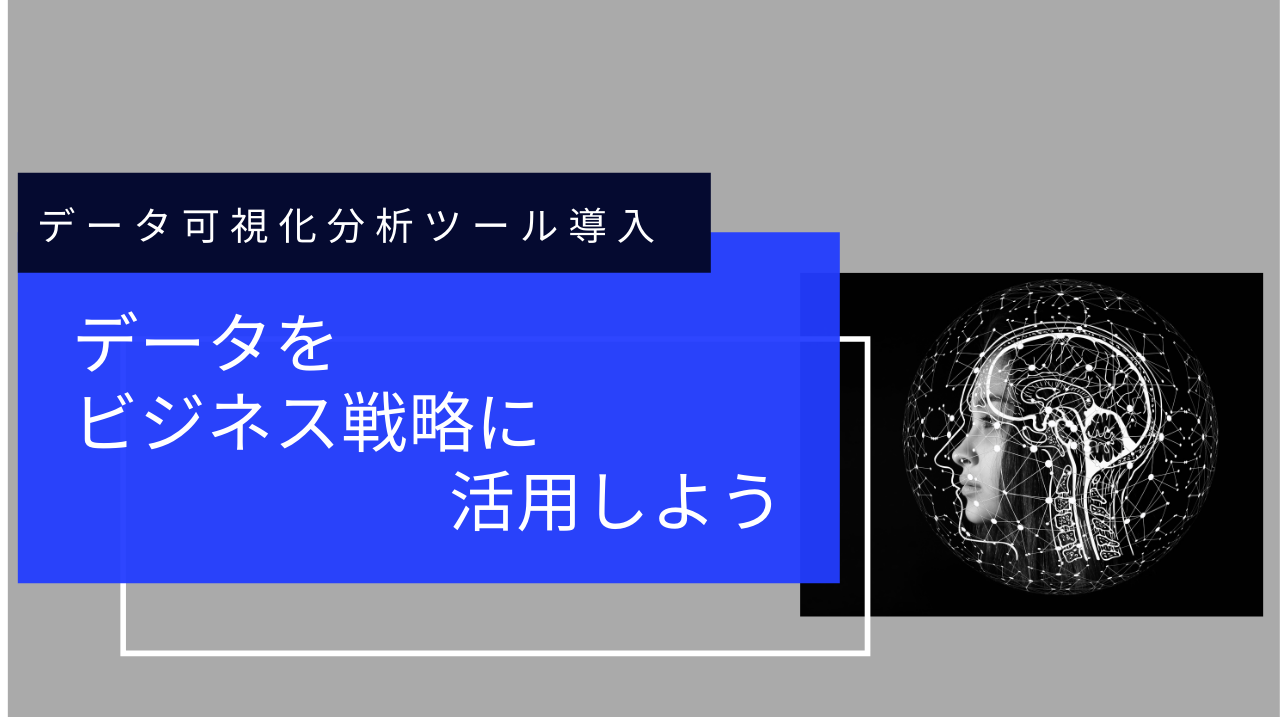
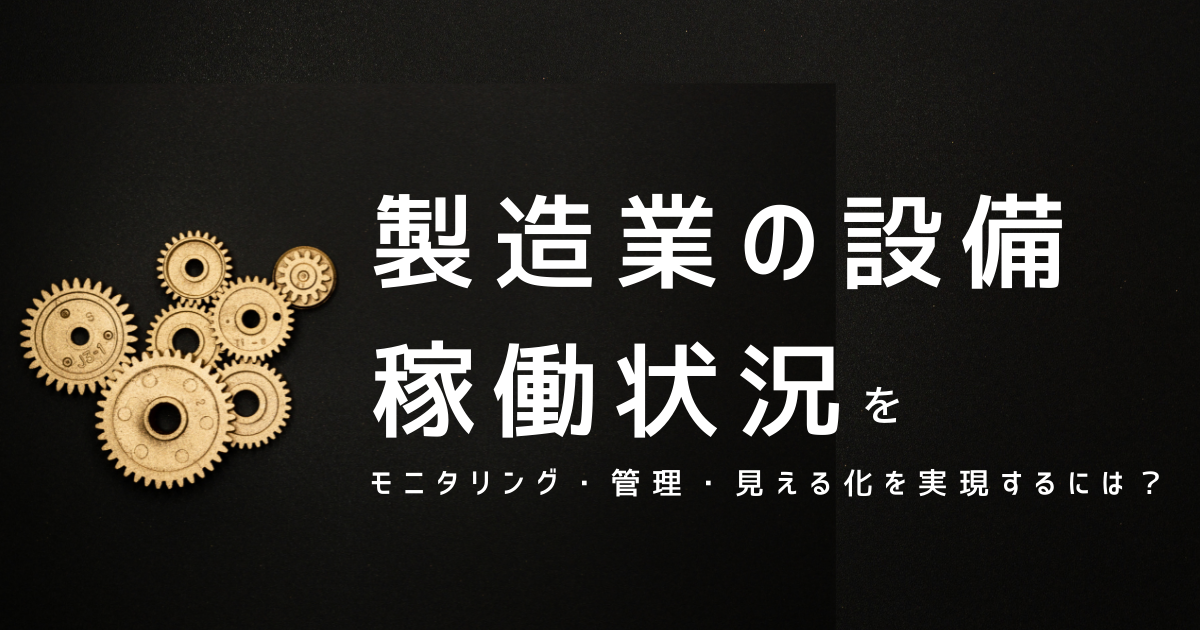
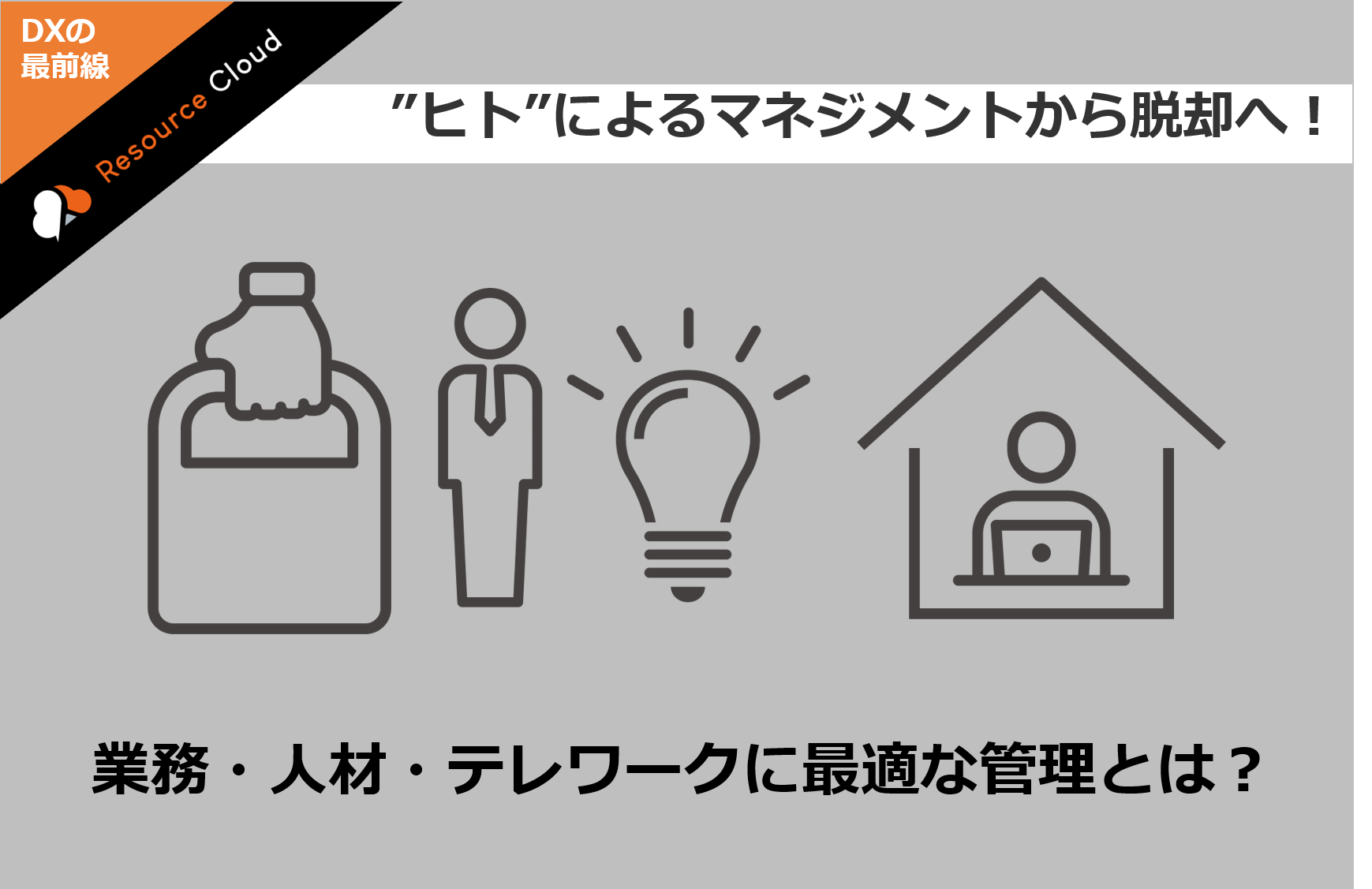
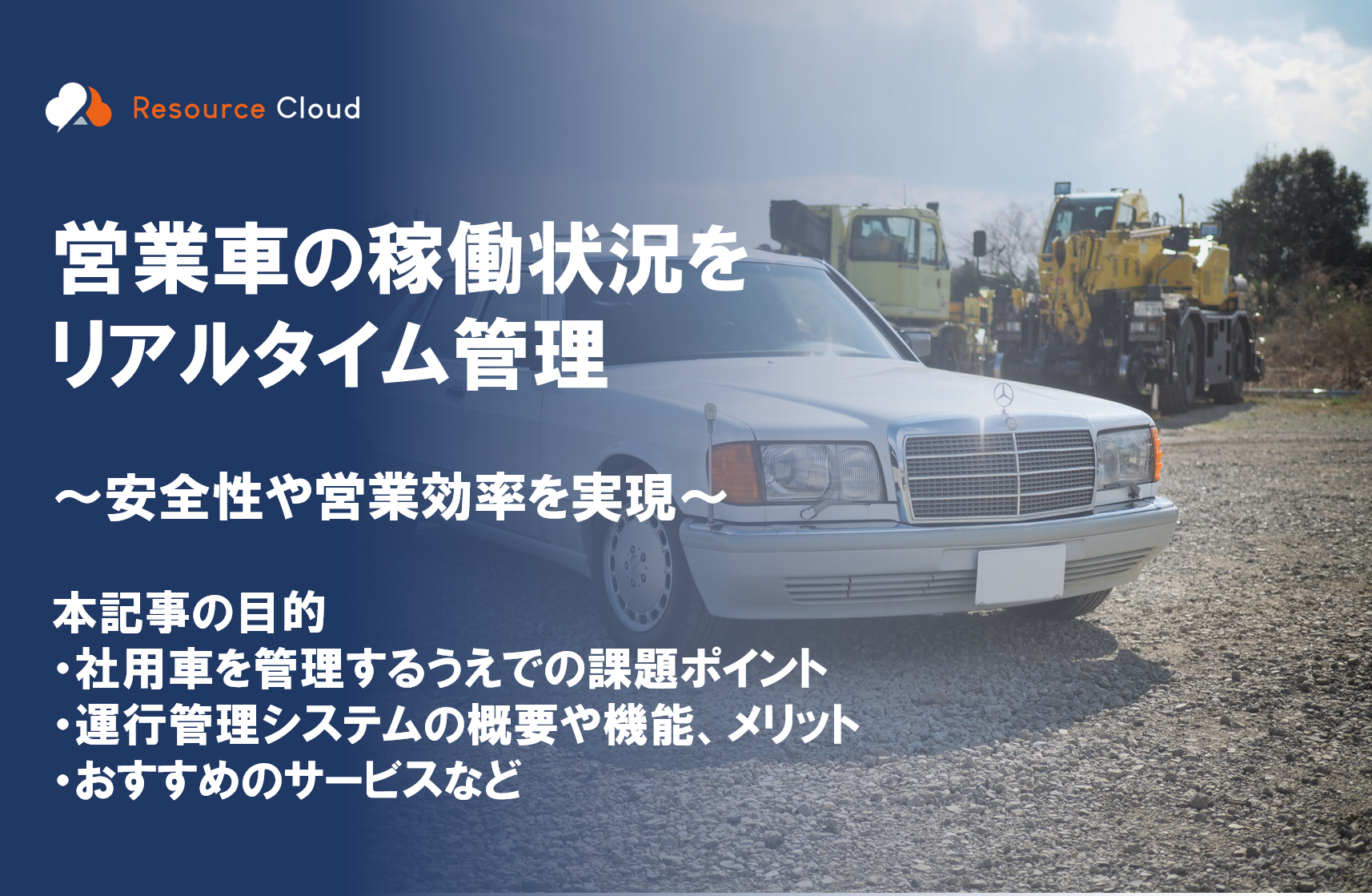
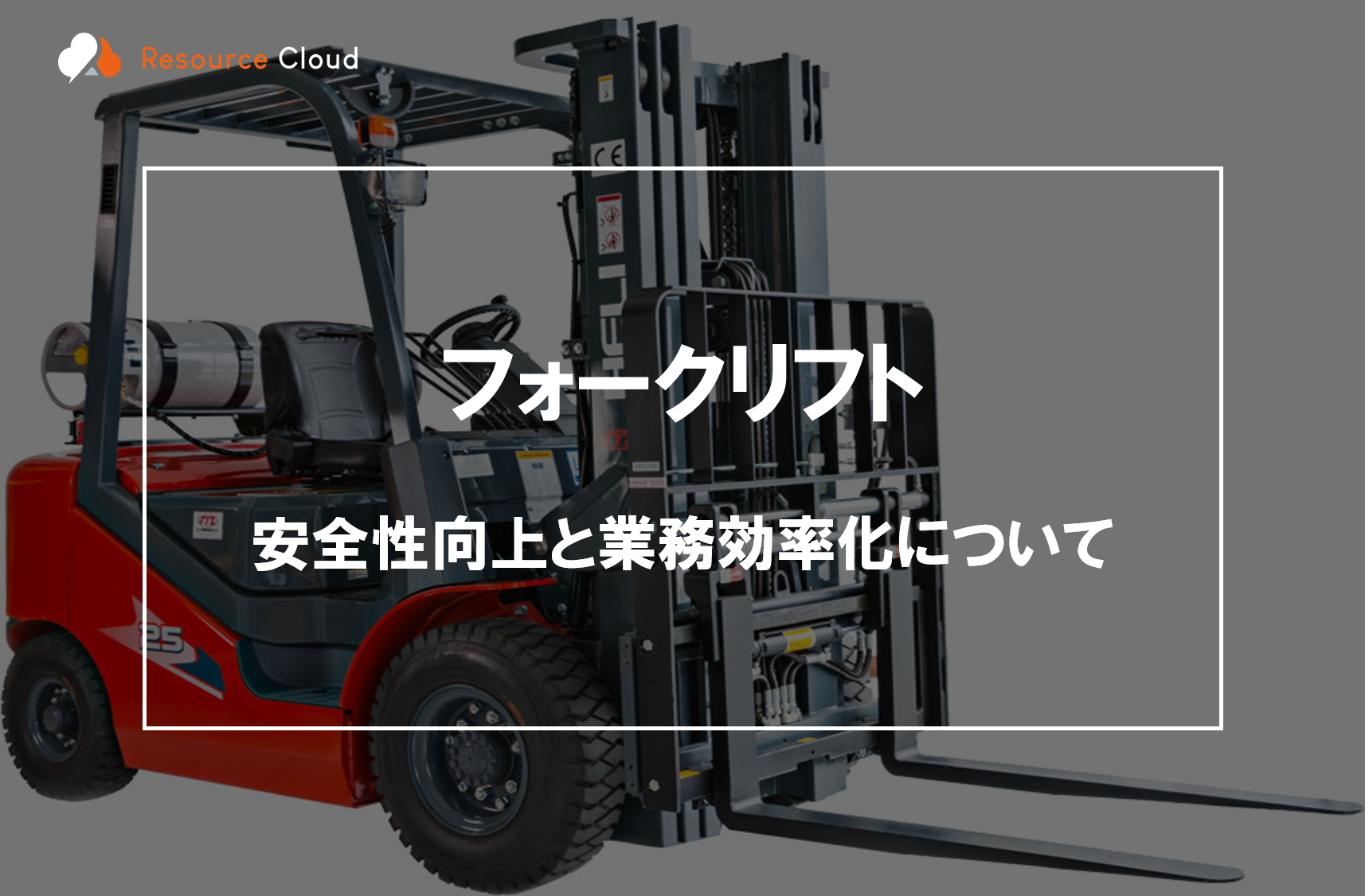
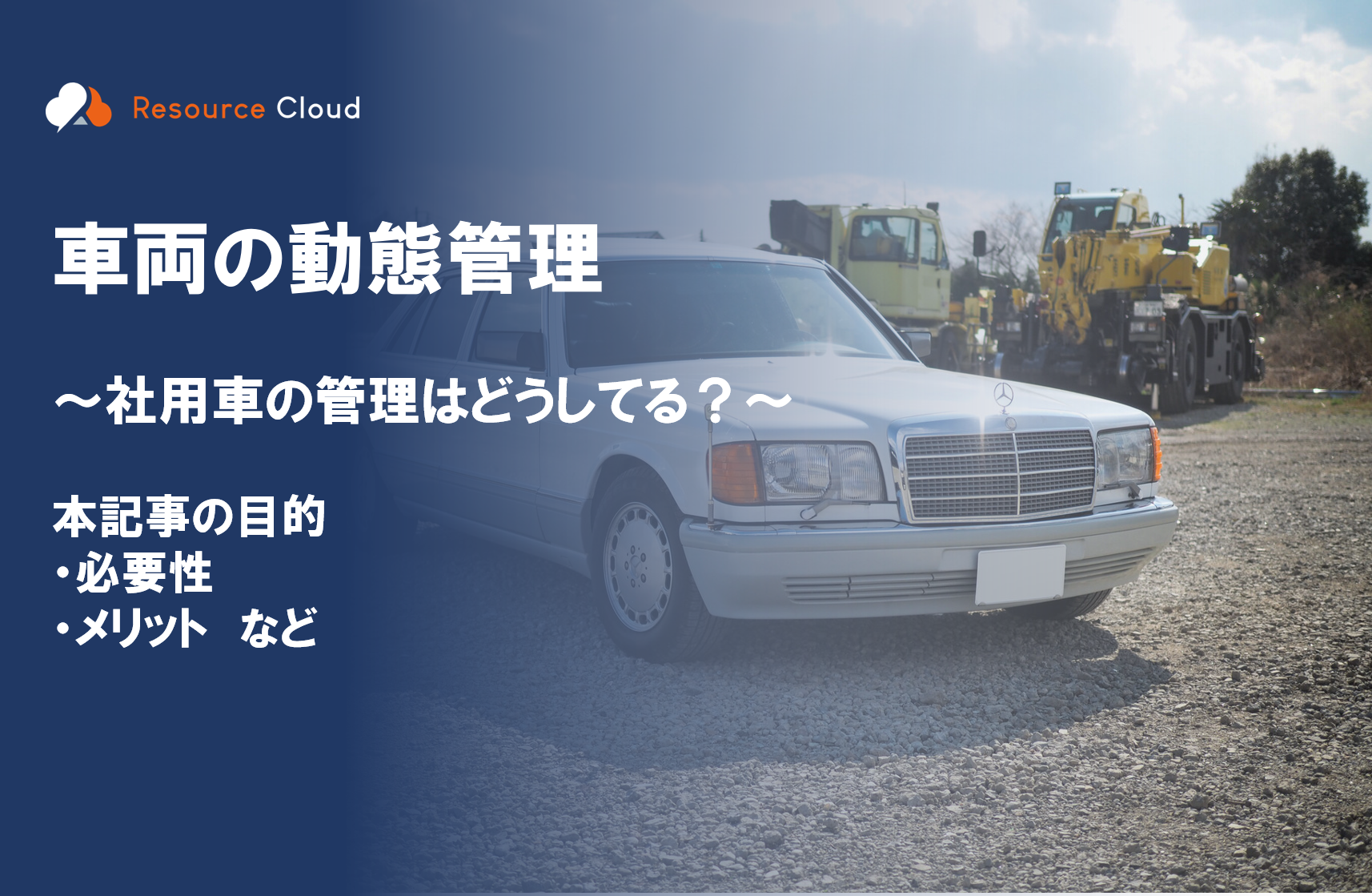
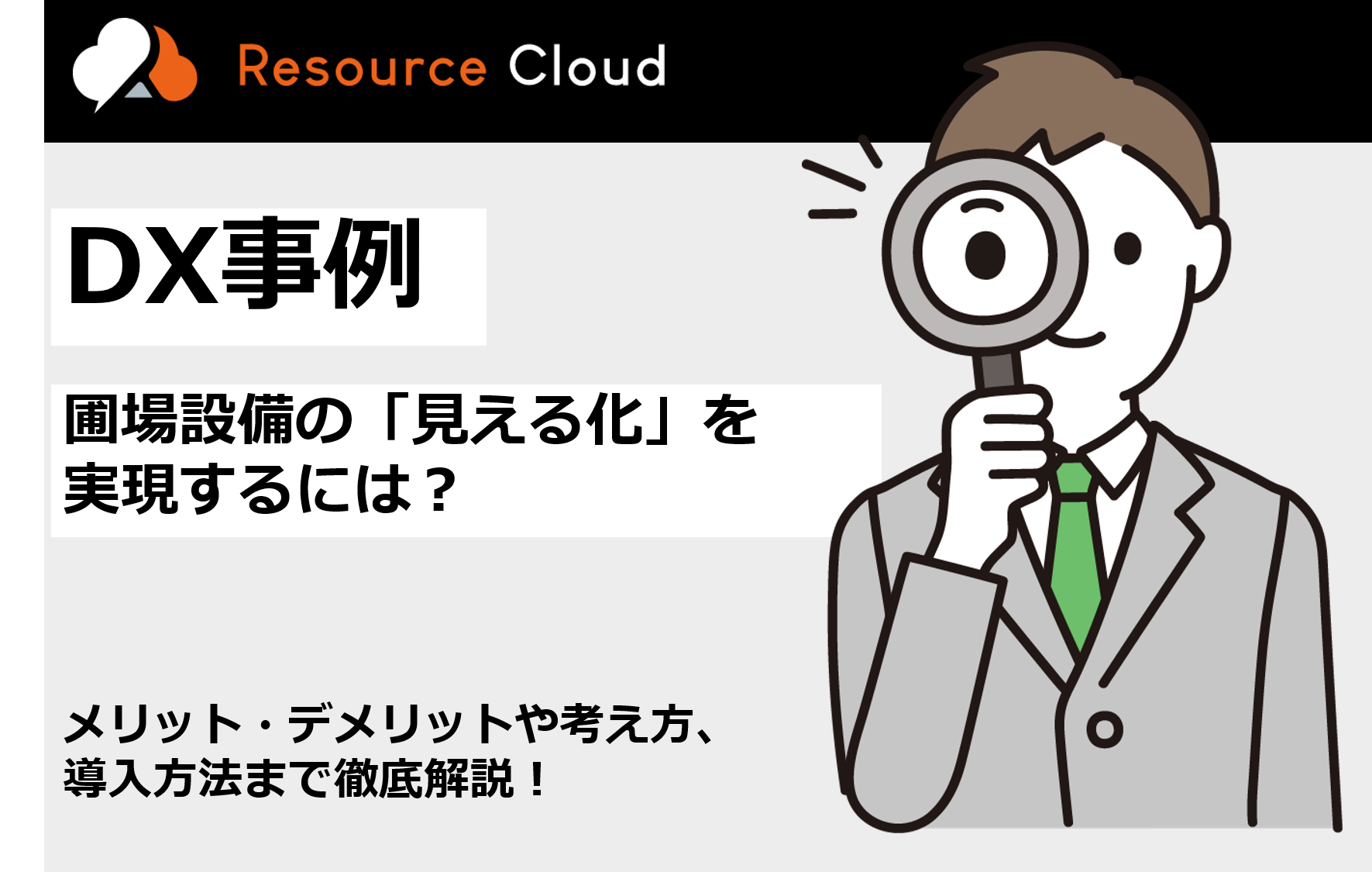
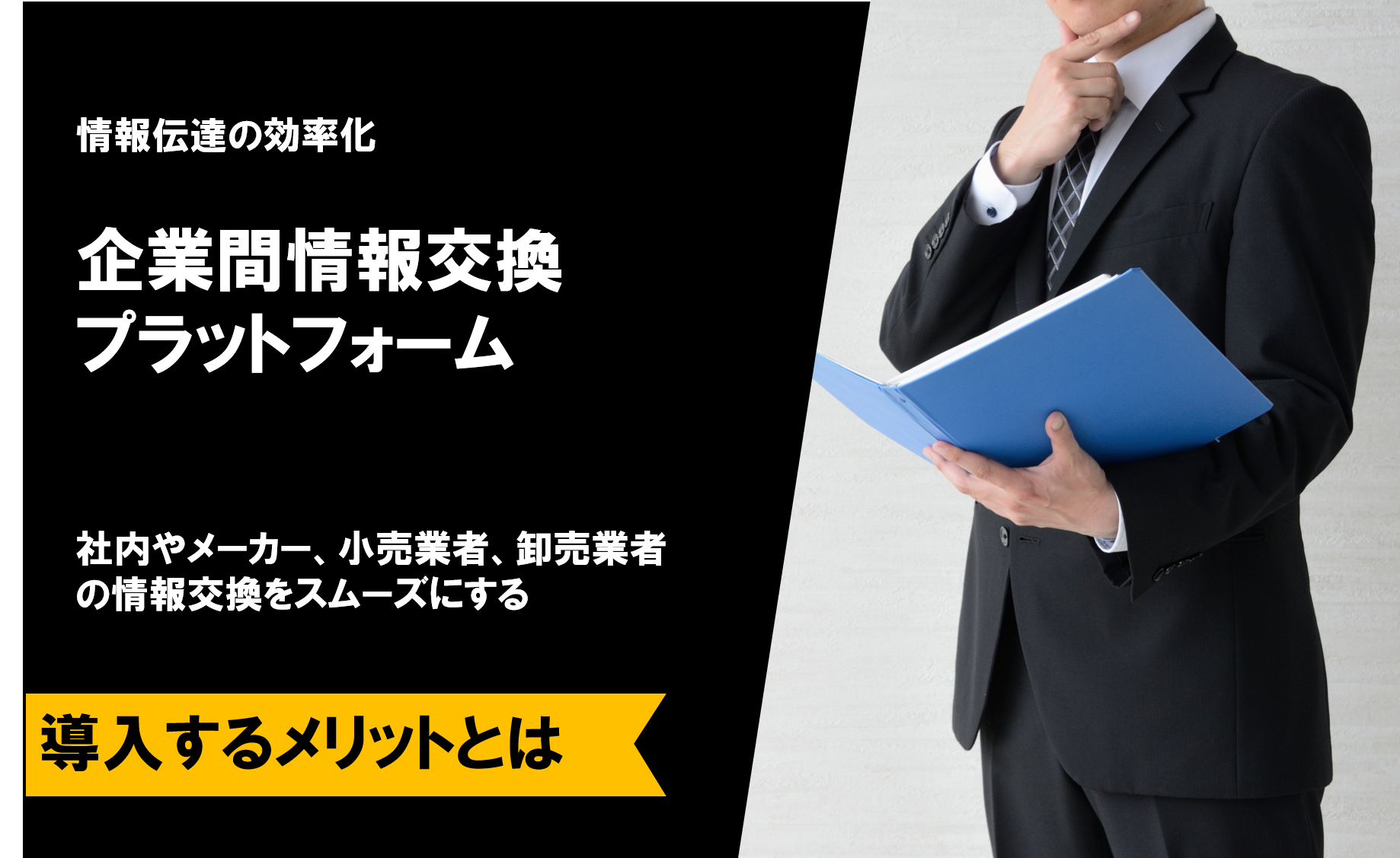
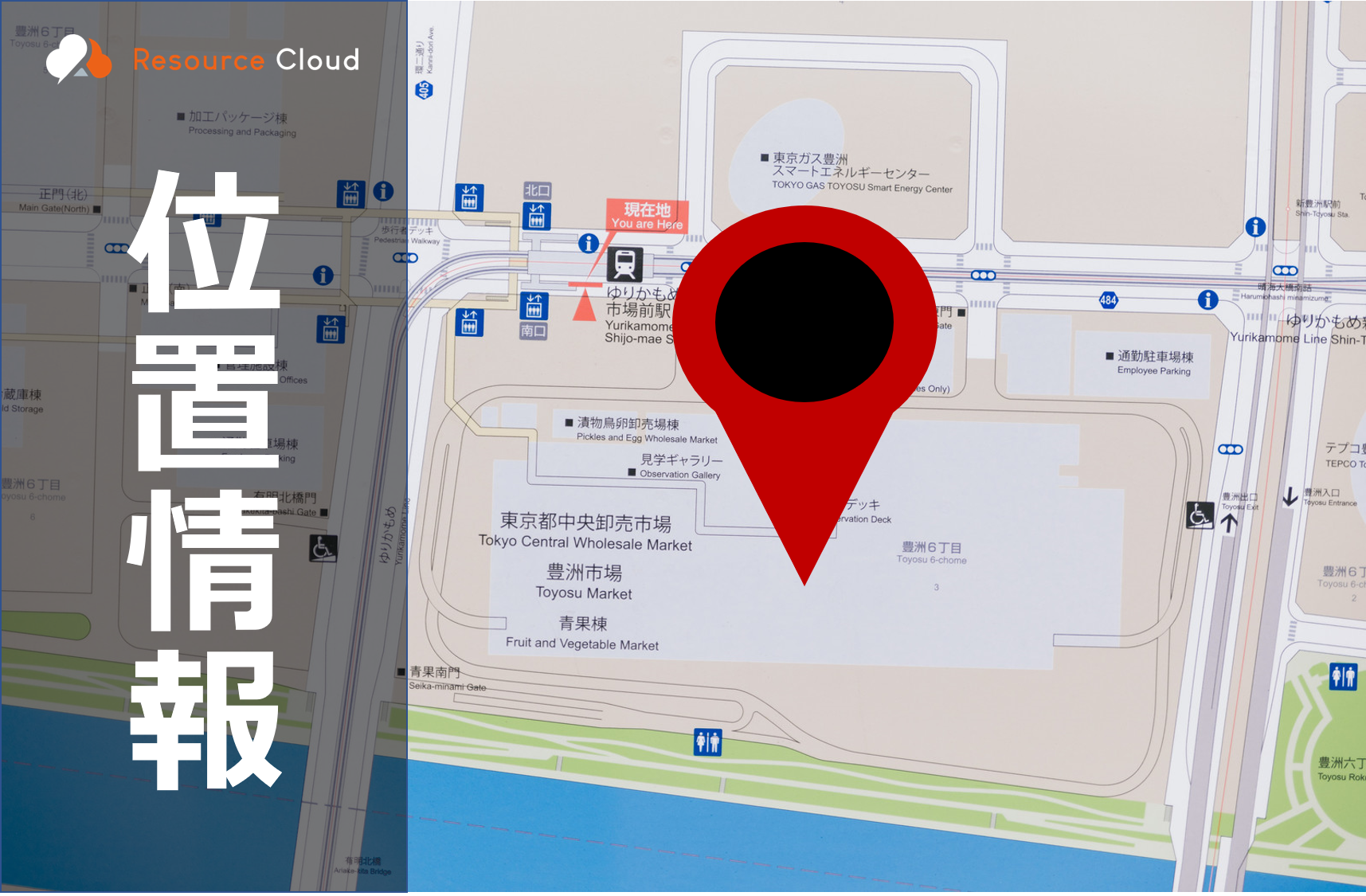
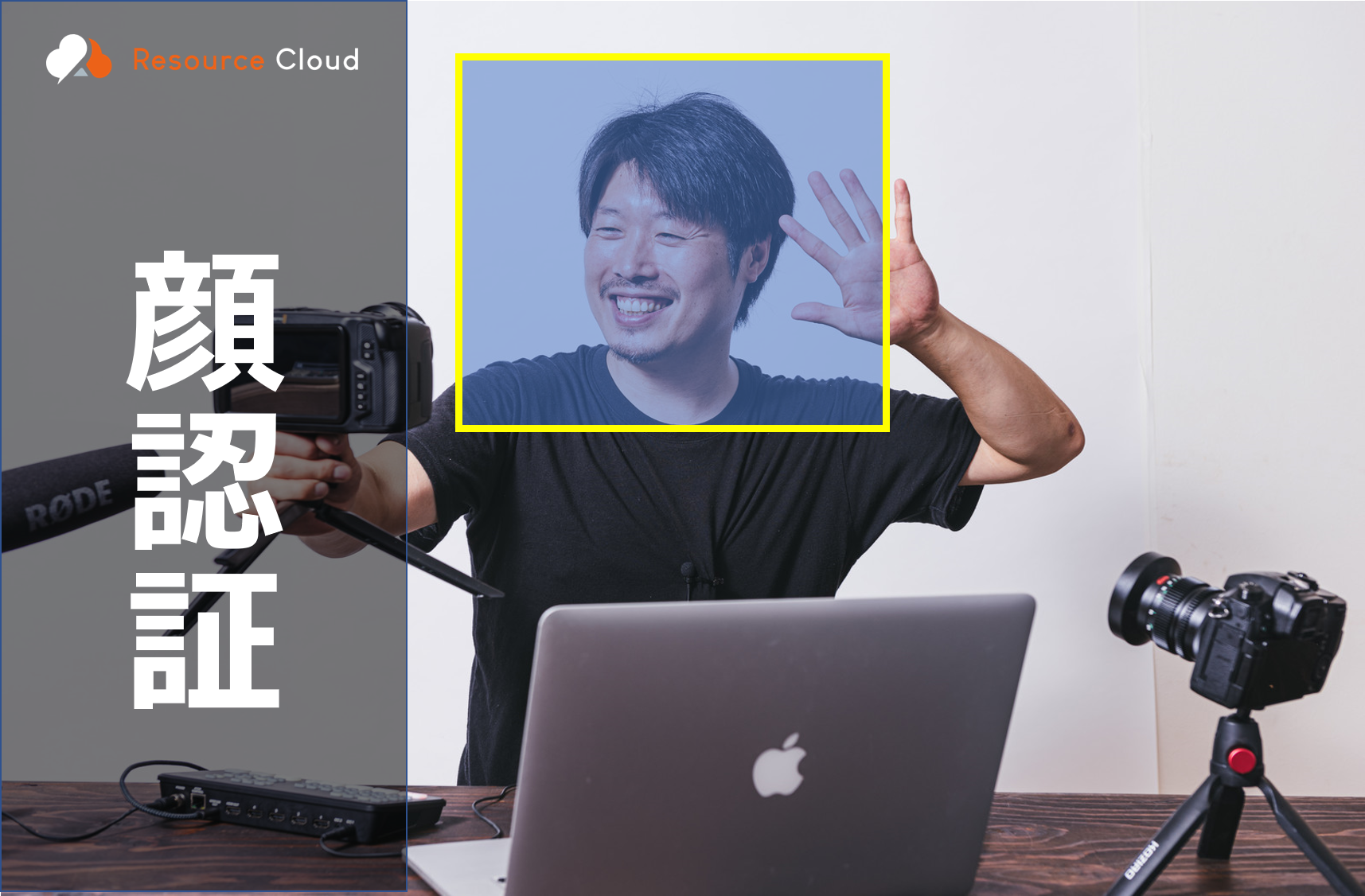
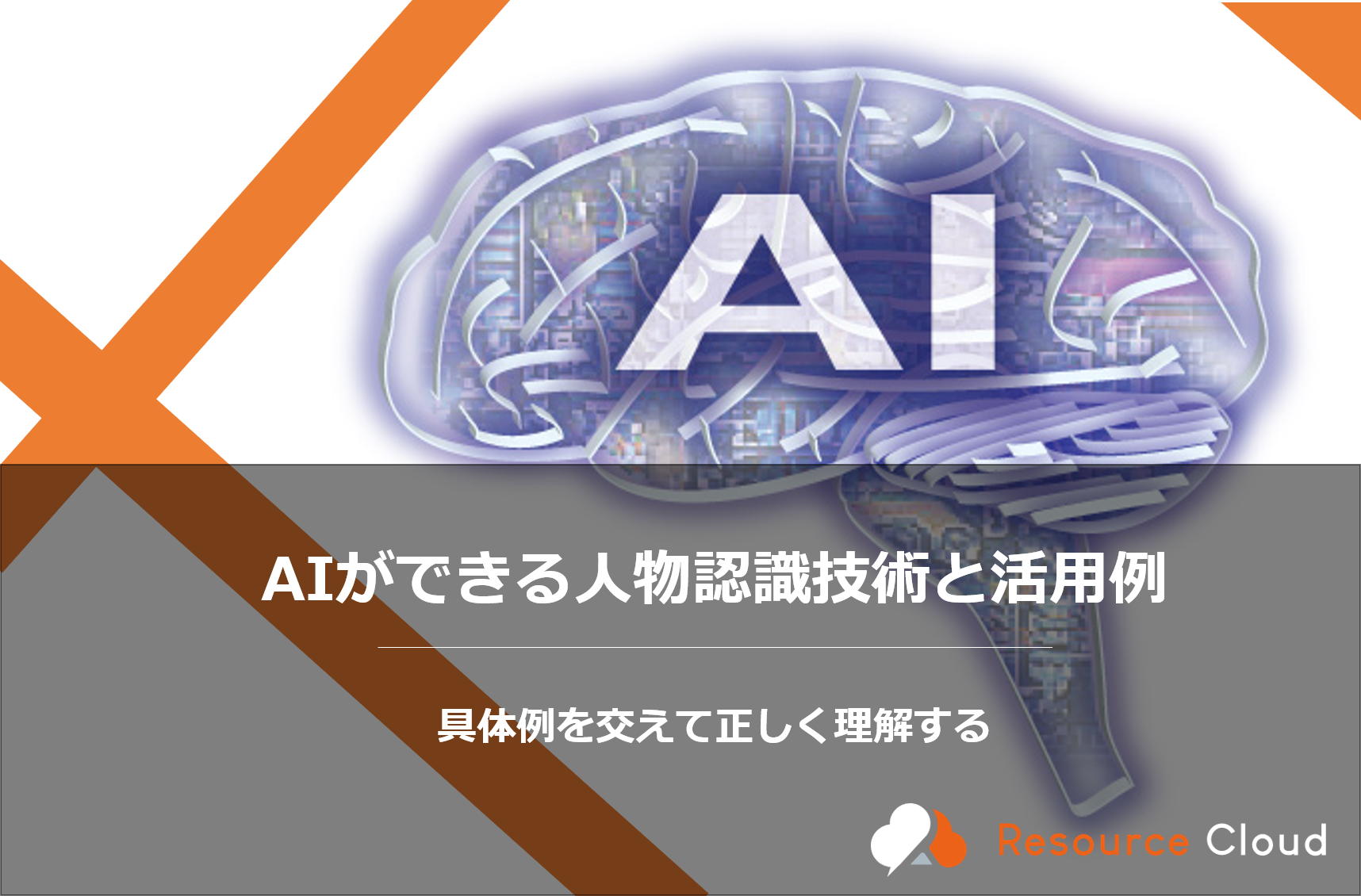
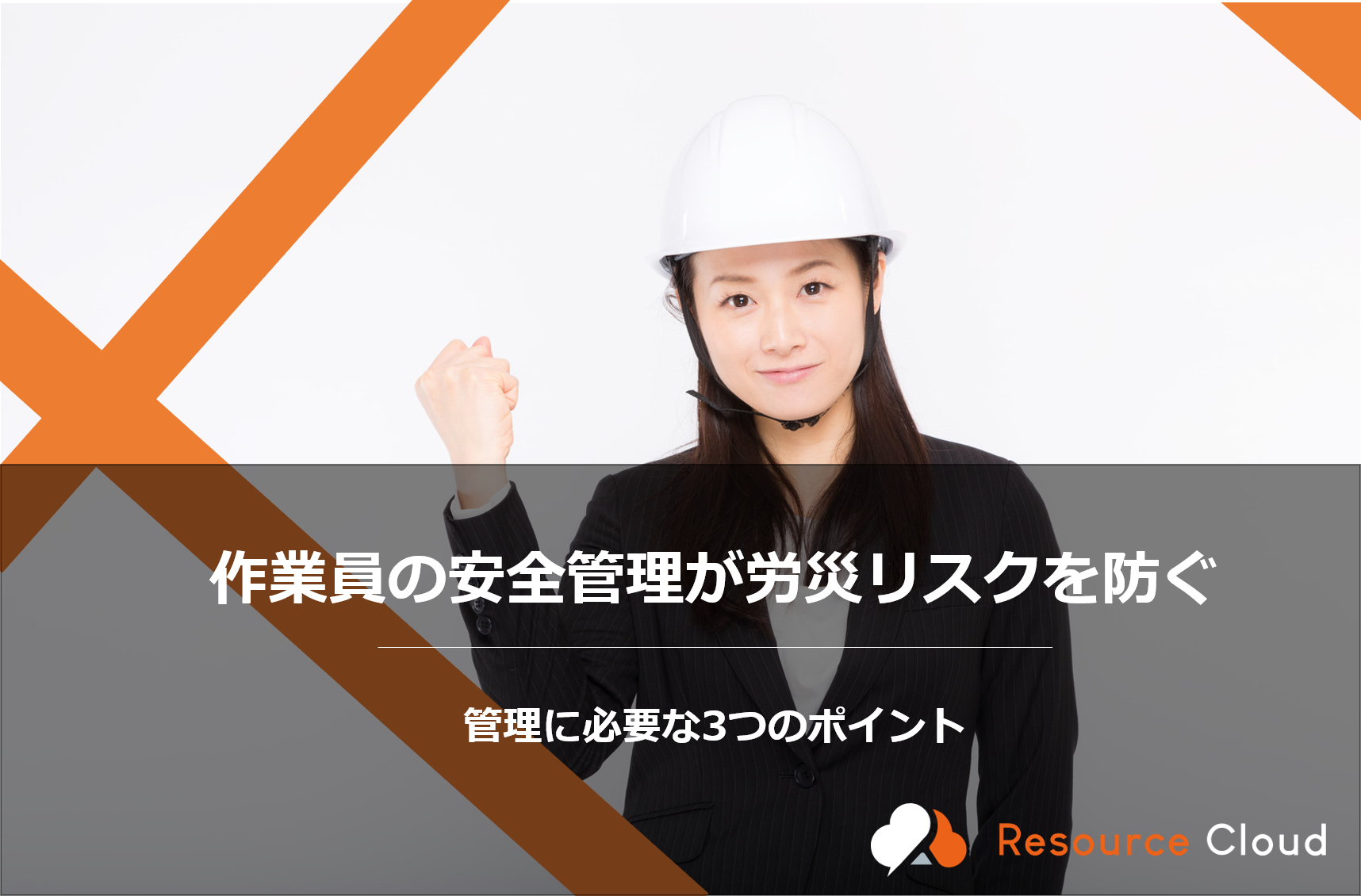
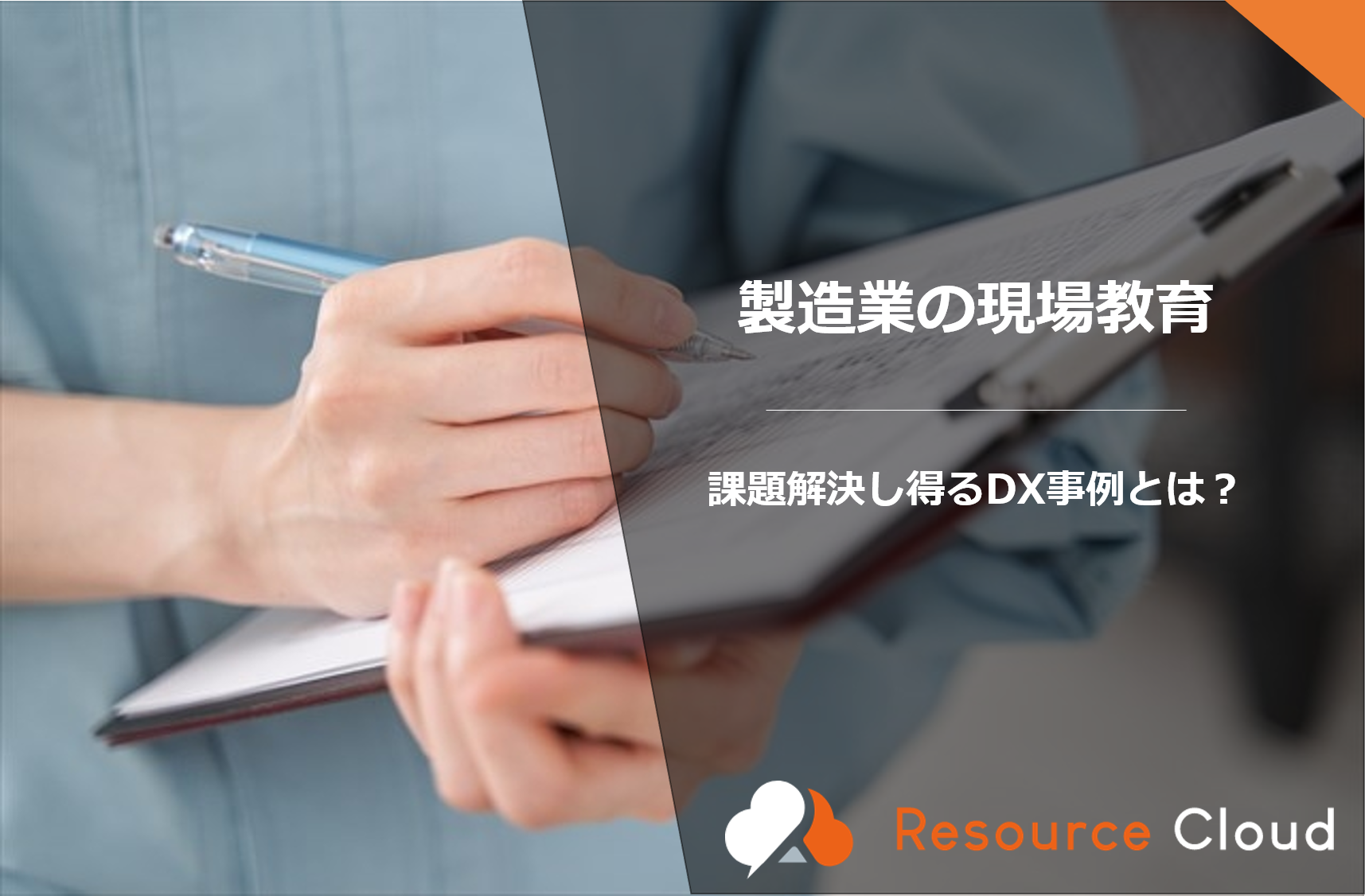
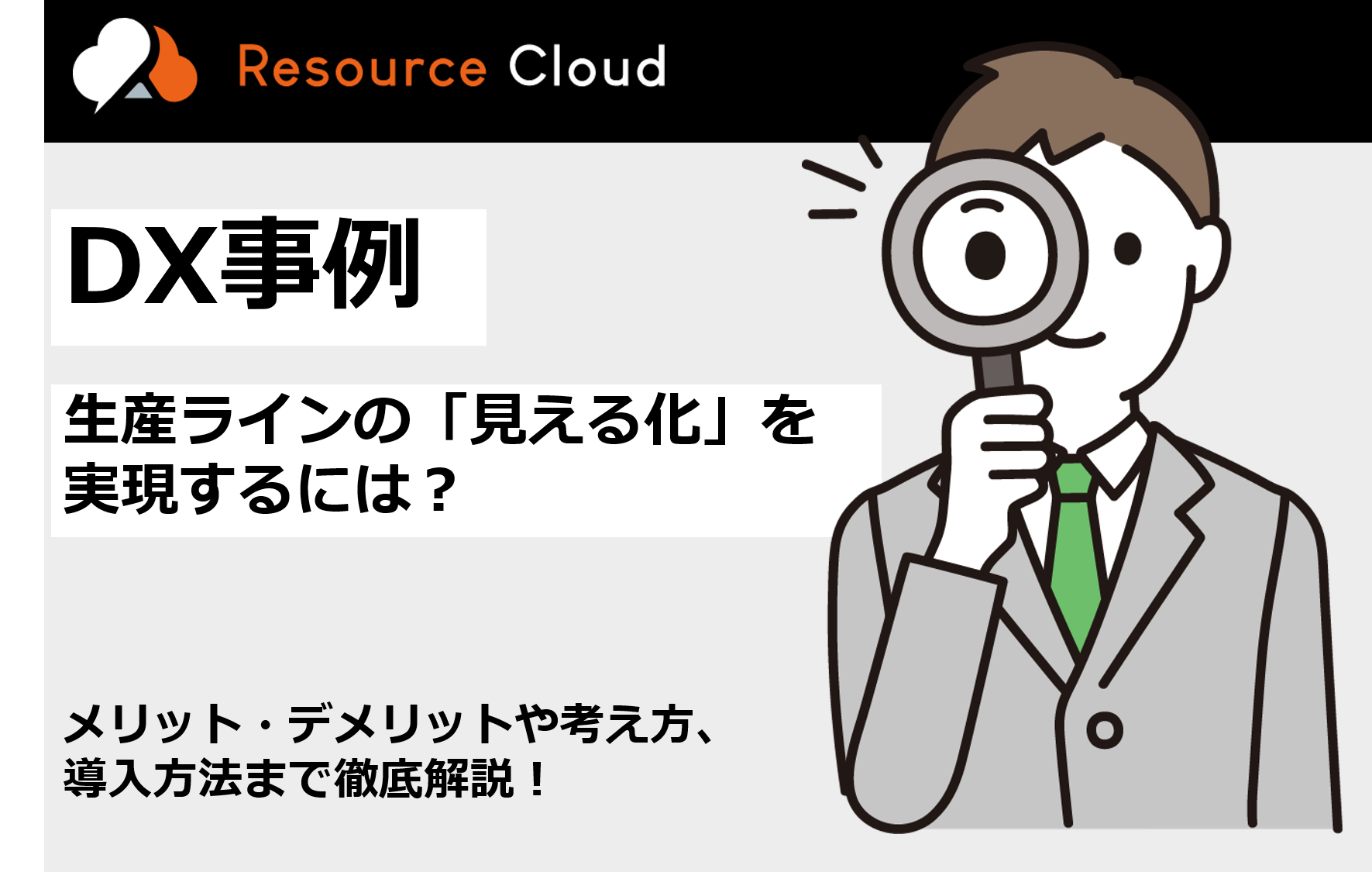
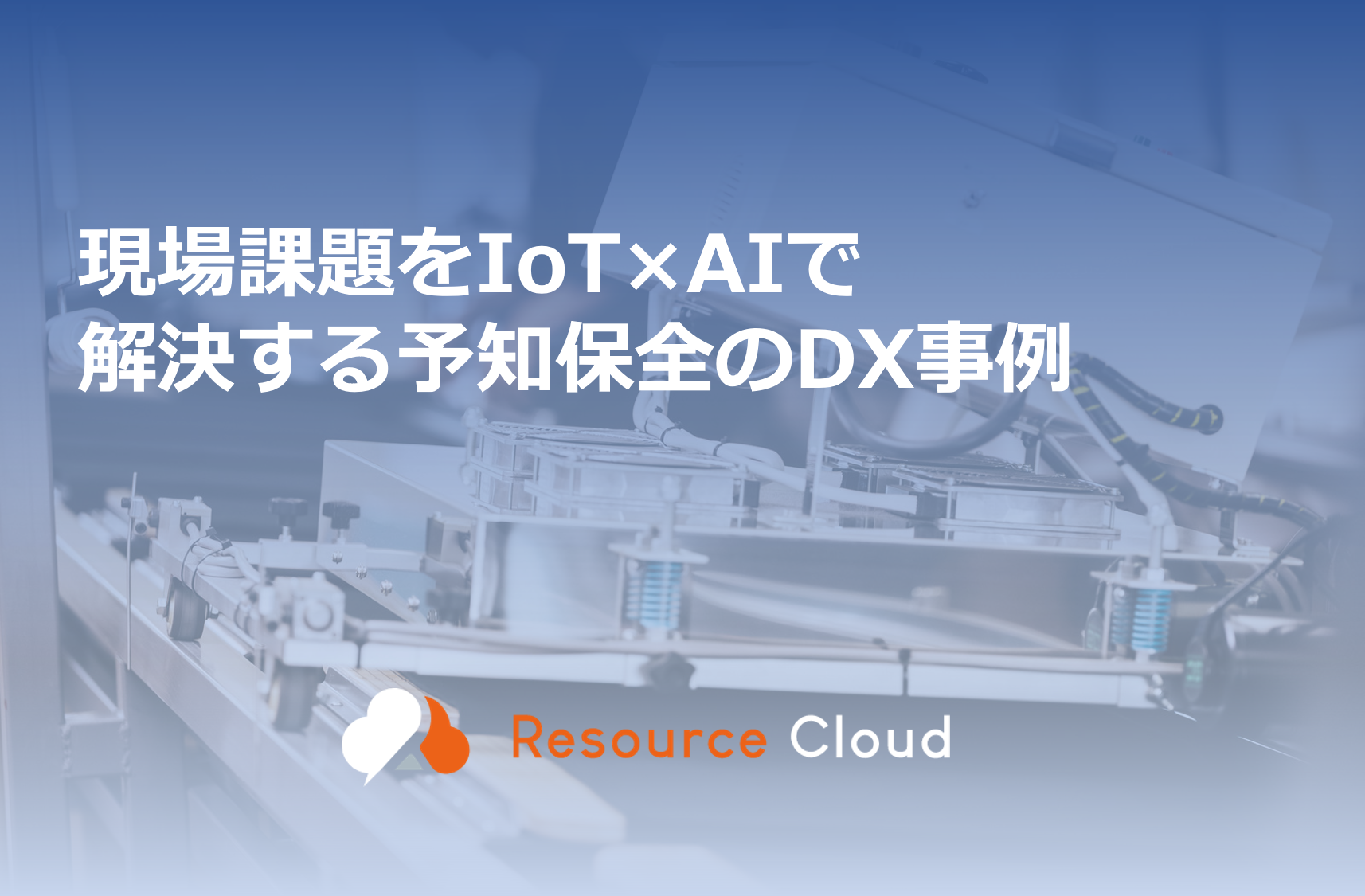
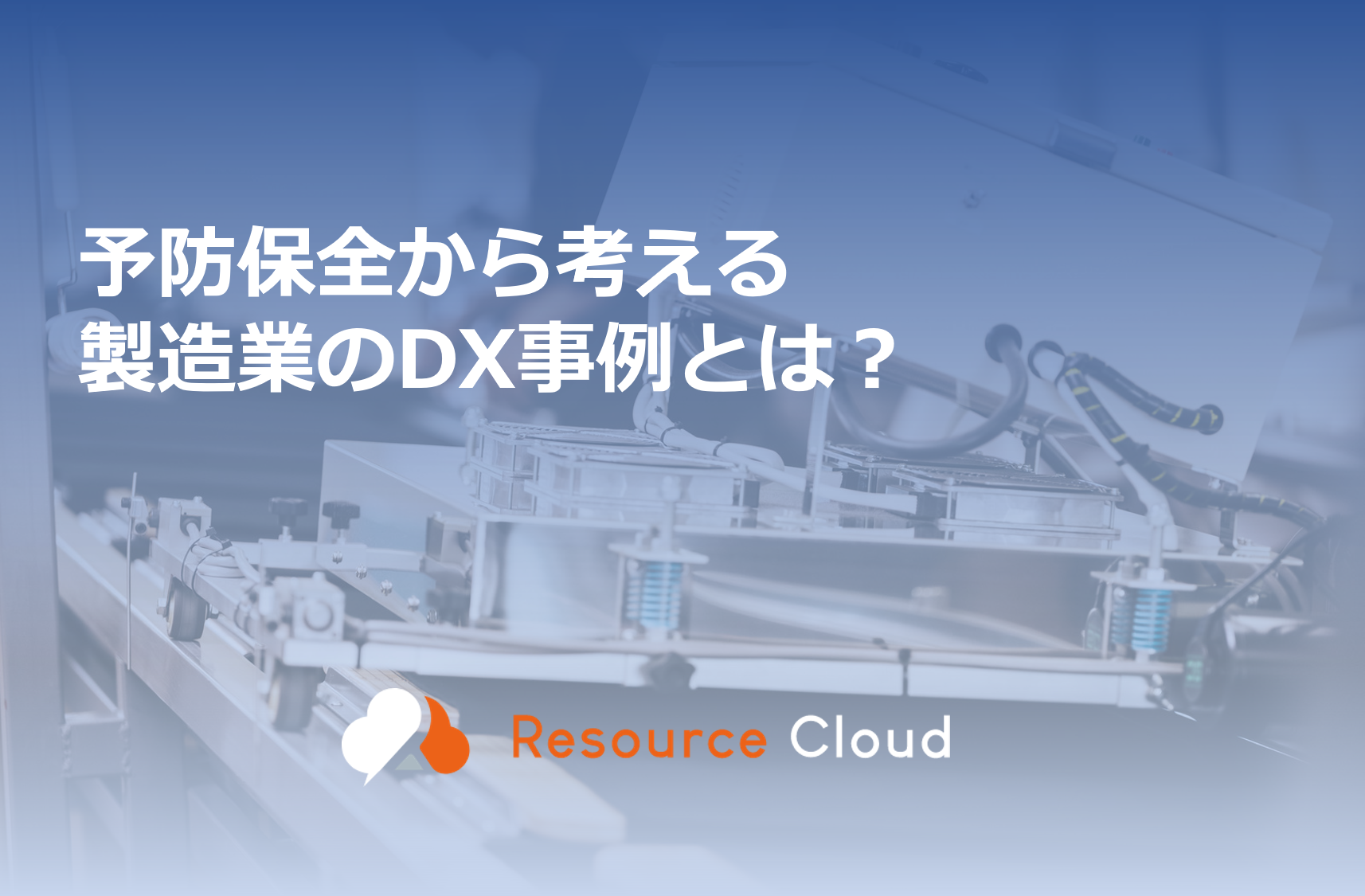
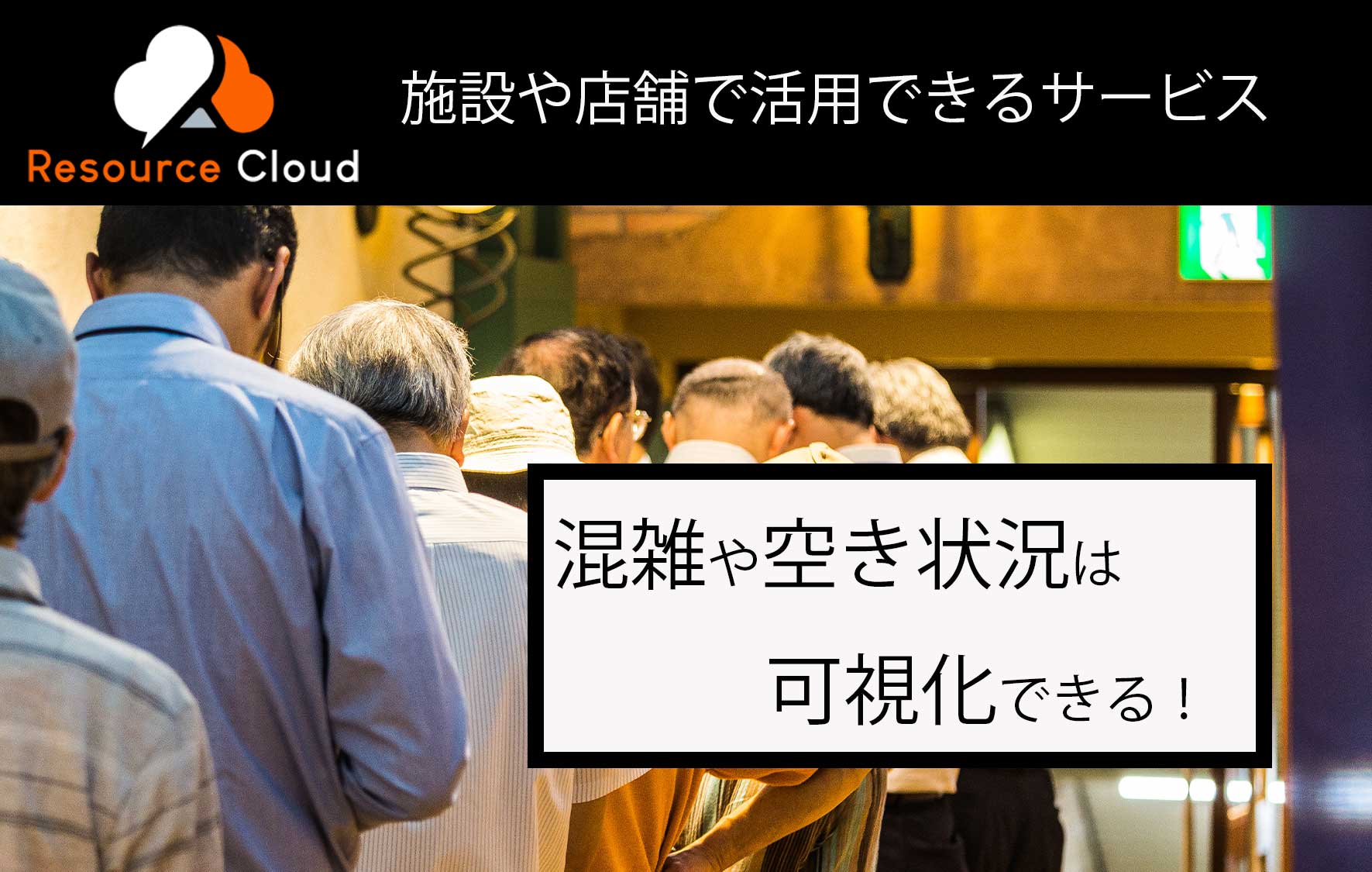
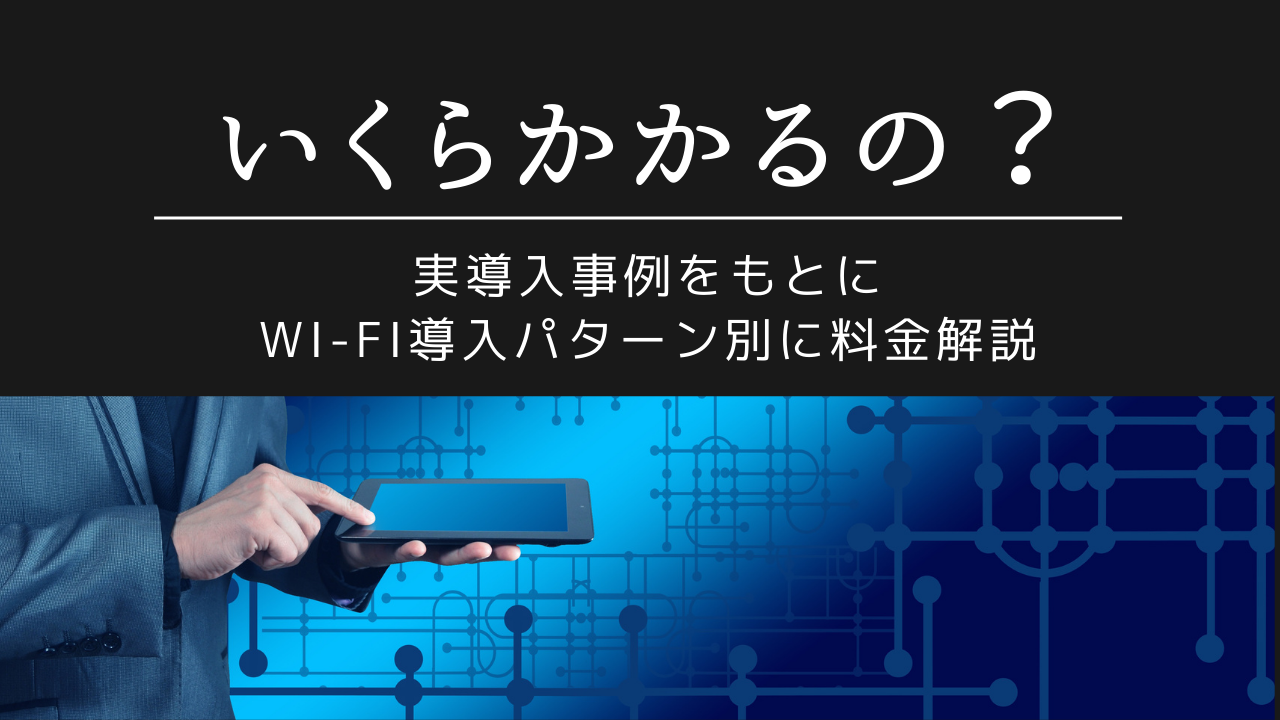
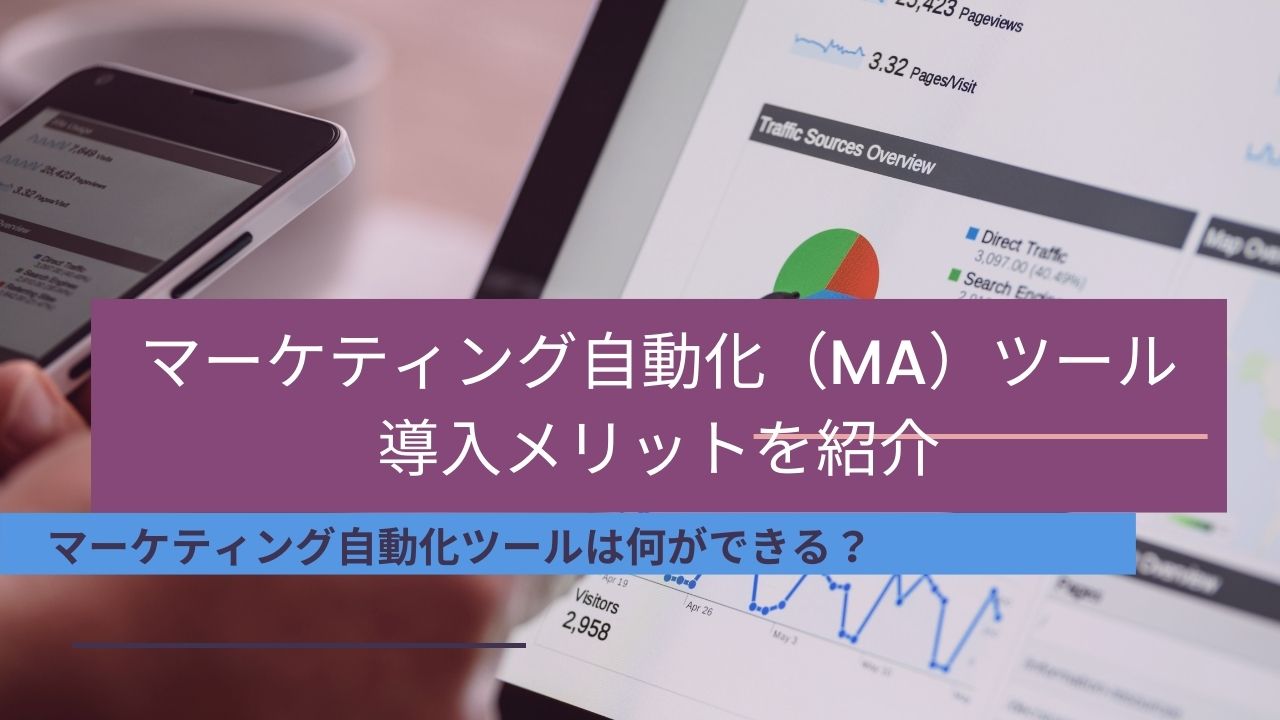
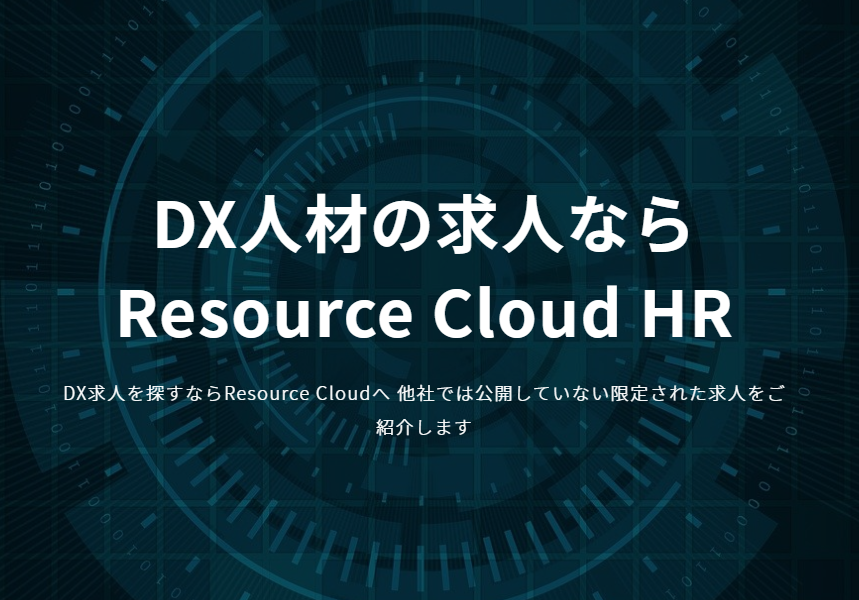
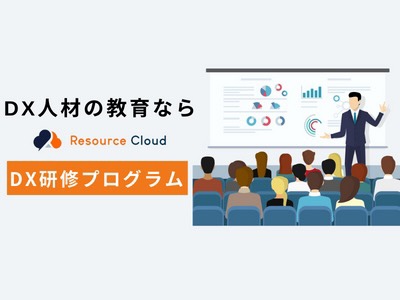
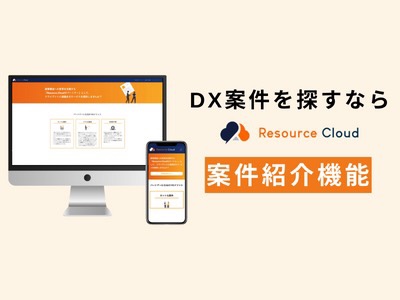