現場帳票デジタル化で業務効率を2倍に改善- 電子部品製造業A社の成功事例
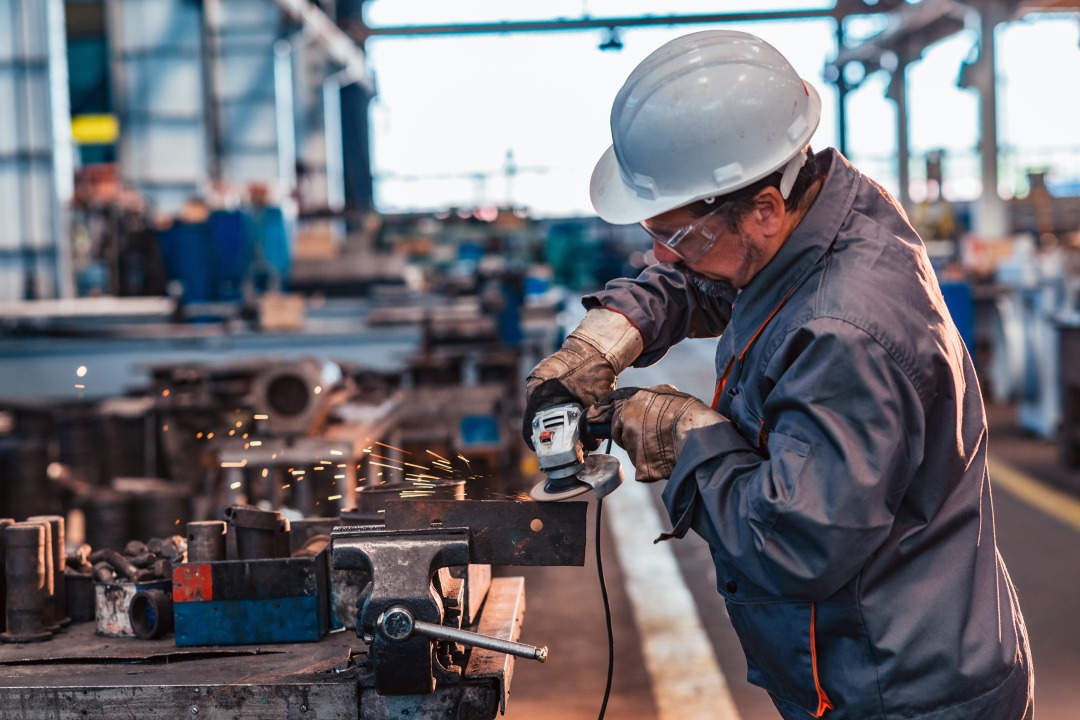
現場帳票をデジタル化する前の課題
電子部品製造業A社では、生産管理業務の中でも特に少量多品種製品の管理において、進捗管理をエクセルで行っていました。この方法では、進捗状況の確認やスケジュール変更が頻繁に発生し、その度に現地確認が必要となっていました。これにより、生産管理部門の業務負担が大きくなり、他の工場に比べて約2倍の人員を必要としていました。
実施したこと
1. 課題把握
- 現場の業務オペレーションの整理 :現場の作業内容やフローを詳細に整理し、現在の課題を明確化。
- ボトルネックと課題の特定 :生産プロセスのどこに問題があるのかを特定。
- 理想的なオペレーションの検討 :最適な業務フローを設計し、その実現に必要なデータを検討。
2. データ収集
- ツール選定 :データ取得のためのツールを選定し、現場での実装が可能か検証。
- 現場説明会の実施 :導入予定のツールについて現場で説明会を行い、要望を回収。
- 業務への実装 :選定したツールを現場に導入し、運用を開始。
3. 可視化・分析
- データの可視化 :設備や人の稼働状況をデータとして可視化し、どこにボトルネックがあるのかを把握。
- 改善案の検討・実施 :特定したボトルネックに対する改善策を検討・実施。
- 最適な人員配置の検討 :データを基に、最適な人員配置を検討。
4. 予期化
- 設備故障の予測 :データを活用して設備の故障を予測し、予防保全を実施。
- 調達の自動化 :必要な資材の調達を自動化し、効率化を図った。
- 生産計画予測 :繁忙期を考慮した生産計画を立て、需給を最適化。
得られた効果
エクセルでの管理を排除し、工程管理ツールを導入することで次のような効果が得られました。
- 業務効率化 :生産管理部門による頻繁な現場確認やスケジュール変更業務が削減。
- リアルタイム更新 :作業対応者が工程管理ツール上で進捗を更新することで、最新の作業計画を自動的に反映。
- 進捗の見える化 :生産進捗がシステム上で確認できるため、前後の工程の進捗も現場を見に行くことなく把握することが可能に。
これにより、生産管理業務の効率化が実現し、現場での負担が大幅に軽減されました。さらに、工程管理システムを自社の工程にカスタマイズするのではなく、既存ツールの特性に合わせてオペレーションを変更することで、無理のない投資で現場課題を解決できました。
ポイント
A社は既存のツールを活用し、必要な変更を最小限に抑えることで、効果的かつ効率的なデジタル化を実現しました。このアプローチにより、多大な投資を避けつつ、現場課題を解決し、業務の最適化を達成しました。
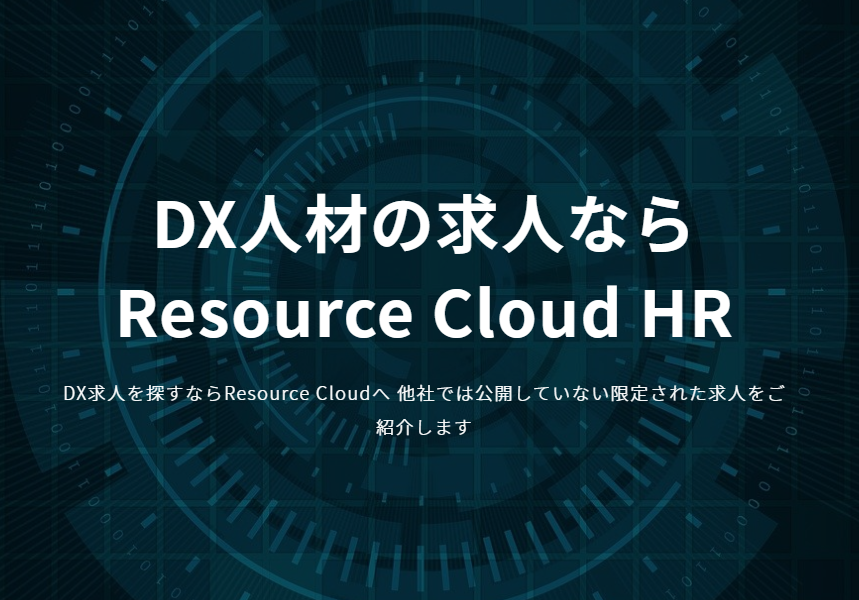
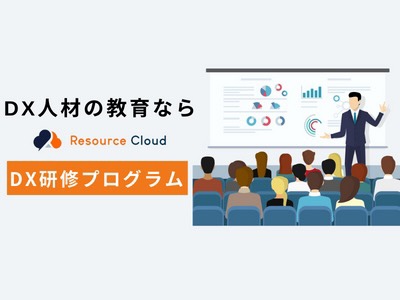
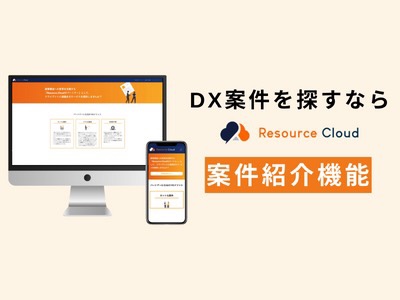